PPSU masterbatch, also known as polyphenylsulfone masterbatch, is a granular concentrate made from polyphenylsulfone (PPSU) resin as the substrate, with the addition of specific functional additives and fillers. PPSU, as a high-performance thermoplastic, has excellent heat resistance, chemical corrosion resistance, and mechanical properties. Therefore, PPSU masterbatch has a wide range of applications in multiple fields.
Characteristic
1. Excellent heat resistance: PPSU masterbatch has a high glass transition temperature and thermal deformation temperature, and can be used for a long time in high temperature environments. In general, its thermal deformation temperature can reach 207 ℃, and it can still maintain good mechanical properties at 180 ℃. It can withstand multiple high-temperature disinfections and is suitable for products that require high-temperature processing or use in high-temperature environments.
2. Good mechanical performance: It has excellent strength and rigidity, with outstanding tensile strength, bending strength, and impact strength. Even under high temperature or long-term use conditions, it can maintain stable mechanical properties, is not easily deformed or brittle, and can be used to manufacture components that can withstand large external forces and pressures.
3. Outstanding chemical corrosion resistance: PPSU masterbatch has good resistance to most acids, bases, salts, and organic solvents. It can maintain stable performance in harsh chemical environments and is not easily corroded or dissolved by chemical substances. It is suitable for applications that come into contact with various chemical substances, such as chemical pipelines, reactor liners, etc.
4. High insulation performance: It has excellent electrical insulation performance, with stable dielectric constant and dielectric loss tangent over a wide temperature and frequency range, and high volume resistivity. It can be used to manufacture insulation components in the electronic and electrical fields, ensuring the safe and reliable operation of equipment.
5. Good flame retardancy: PPSU masterbatch has certain flame retardant properties and can achieve a high flame retardant level, such as UL94 V-0, without the need to add a large amount of flame retardants. It can effectively prevent the spread of fire and improve the safety of use in the event of a fire.
6. Hygiene and Non toxicity: PPSU masterbatch meets the relevant standards for food contact materials, is non-toxic, odorless, and does not release harmful substances. It can be used to manufacture products that come into direct contact with the human body, such as food packaging and medical devices, to ensure human health and safety.
7. Good processing performance: Although PPSU has a high melting point, it has good fluidity and formability during the processing, and can be made into various shapes of products through various processing methods such as injection molding, extrusion, blow molding, etc., which can meet the production needs of different products.
8. Hydrolysis resistance: PPSU masterbatch still has good hydrolysis resistance in high temperature and high humidity environments, is not easily hydrolyzed or degraded, and has stable product performance. It can be used for products that come into long-term contact with water or are used in humid environments, such as hot water pipes, bathroom products, etc.
Types
PPSU masterbatch can have multiple types according to different classification criteria. The following are some common classification methods and corresponding types:
Classified by purpose
Universal type: It has the basic performance of PPSU and is suitable for general purposes that do not require particularly strict performance requirements, such as some ordinary plastic products, electronic and electrical casings, etc.
Enhanced type: By adding reinforcing materials such as glass fiber and carbon fiber, the strength, rigidity, and heat resistance of PPSU masterbatch are improved. It is commonly used in the manufacturing of components with high mechanical performance requirements, such as automotive engine parts, aerospace structural components, etc.
Flame retardant type: After special flame retardant treatment, it has good flame retardant performance and can meet the strict requirements for material flame retardancy in electronic and electrical, construction and other fields. It can be used to manufacture products such as wire and cable insulation layers, electrical enclosures, etc. that are prone to fire hazards.
Thermal conductivity type: Added thermal conductivity filler to give PPSU masterbatch good thermal conductivity, mainly used for electronic device components that require heat dissipation, such as computer CPU heat sinks, power amplifier housings, etc., which can effectively dissipate heat and ensure the normal operation of the equipment.
Food contact type: meets food hygiene and safety standards, is non-toxic and odorless, and can be used to manufacture products that come into direct contact with food, such as food packaging containers, tableware, and food processing equipment components.
Medical grade: With higher purity and biocompatibility, it meets the strict requirements of the medical industry for materials and can be used to manufacture medical devices such as syringes, infusion sets, medical catheters, artificial organs, etc.
According to the classification of additives
Filler type: Various fillers such as calcium carbonate, talc powder, mica powder, etc. are added to reduce costs, improve processing performance, or enhance certain specific properties such as hardness and dimensional stability.
Toughened type: Added toughening agent to improve the toughness and impact resistance of PPSU masterbatch, making it less likely to break when subjected to external impact, suitable for occasions with high requirements for product toughness.
Functional type: Added additives with specific functions, such as anti-static agents, UV absorbers, lubricants, etc., to make PPSU masterbatch have special functions such as anti-static, UV aging resistance, and good processing flowability.
Formula ratio
The following are common formula ratios for different types of PPSU masterbatch, which will be adjusted according to specific product requirements and production processes in actual production.
Enhanced PPSU masterbatch
PPSU resin: 60-80 parts, used as the base material to provide the basic properties of PPSU.
Reinforcing materials (such as glass fiber, carbon fiber, etc.): 20-40 parts, to improve the mechanical properties such as strength, rigidity, and heat resistance of the masterbatch.
Coupling agent: 0.5-2 parts, used to improve the bonding force between the reinforcing material and PPSU resin, and enhance the performance of the composite material.
Lubricant: 0.5-1 part, helps improve processing performance, reduce friction, and make materials flow more easily during the processing.
Flame retardant PPSU masterbatch
PPSU resin: 70-90 parts, providing basic properties and structural support for the masterbatch.
Flame retardant: 10-30 parts, choose the appropriate flame retardant and dosage according to the required flame retardant level, such as bromine flame retardant, phosphorus flame retardant, magnesium hydroxide, aluminum hydroxide, etc. For example, if a compound system of bromine based flame retardants and antimony trioxide is used, the ratio of the two is usually around 3:1-4:1.
Synergistic agent: 0-5 parts, such as antimony trioxide, used in combination with flame retardants to enhance the flame retardant effect.
Antioxidant: 0.5-1 part, to prevent PPSU resin from aging and degradation due to heat, oxidation and other factors during processing and use, and to improve the stability and service life of the product.
Thermal conductive PPSU masterbatch
PPSU resin: 50-70 parts, used as the matrix material.
Thermal conductive fillers (such as alumina, boron nitride, silicon carbide, etc.): 30-50 parts, the amount added depends on the required thermal conductivity. These fillers can improve the thermal conductivity of the masterbatch and enable rapid heat conduction.
Dispersant: 0.5-2 parts, to help evenly disperse the thermal conductive filler in PPSU resin, avoid agglomeration, and improve the consistency of thermal conductivity.
Coupling agent: 0.5-2 parts, improves the interface bonding between the thermal conductive filler and PPSU resin, and enhances the overall performance of the composite material.
Food contact PPSU masterbatch
PPSU resin: 95-100 parts, requiring the use of high-purity PPSU resin that meets food hygiene and safety standards.
Additives (such as antioxidants, lubricants, etc.): 0-5 parts, must use food grade additives, and the amount added must be strictly controlled to ensure that the product complies with relevant regulations and standards for food contact materials.
Medical grade PPSU masterbatch
PPSU resin: 90-99 parts, using high-purity and highly biocompatible PPSU resin to meet the strict requirements for material safety and reliability in the medical field.
Additives: 1-10 portions, including antioxidants, lubricants, antibacterial agents, etc. Medical grade additives should also be selected to ensure the stability, hygiene, and safety of the product in medical environments. For example, adding an appropriate amount of antibacterial agents can prevent bacterial growth and improve the hygiene performance of products.
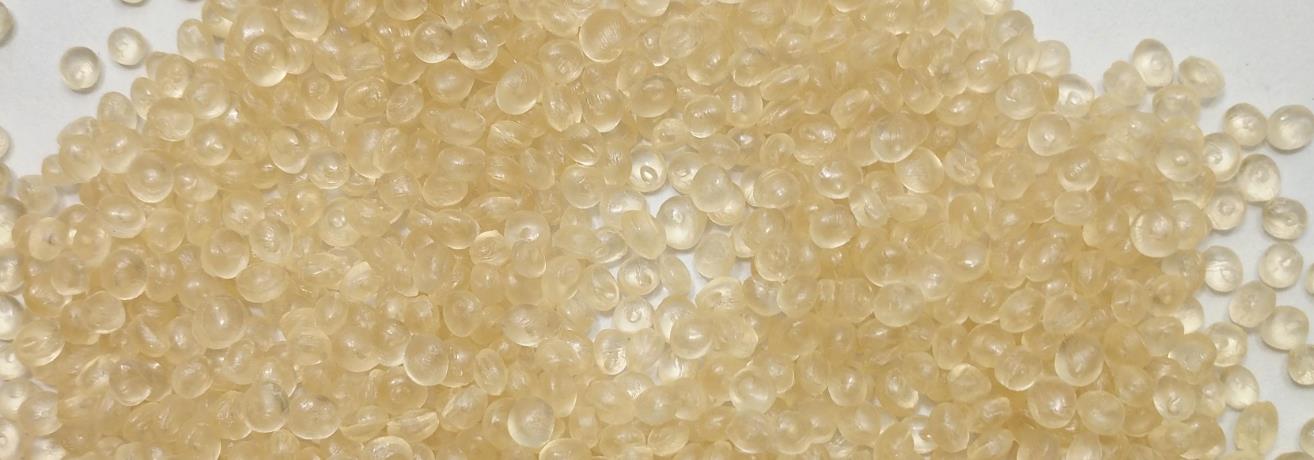
Production process
The production process of PPSU masterbatch usually includes multiple steps such as raw material preparation, mixing, melt extrusion, granulation, etc. The following is a detailed introduction to its production process:
1. Raw material preparation
PPSU resin: Select appropriate models and specifications of PPSU resin particles based on product performance requirements to ensure their purity, molecular weight distribution, and other indicators meet production requirements. PPSU resin generally needs to be dried before use to remove moisture and prevent problems such as bubbles or hydrolysis during processing, which can affect product quality. The drying conditions are usually at a temperature of 120-150 ℃ and for 3-6 hours.
Additives: Accurately weigh various additives according to the formula, such as reinforcing materials, flame retardants, thermal conductive fillers, coupling agents, lubricants, antioxidants, etc. Ensure that the quality and purity of additives meet the requirements, and carry out corresponding pretreatment according to their characteristics, such as surface treatment of reinforcement materials, coating treatment of flame retardants, etc., to improve the compatibility and dispersibility of additives with PPSU resin.
2. Mixing
Add the dried PPSU resin and pre treated additives to the feeding section of the high-speed mixer or twin-screw extruder. By high-speed stirring or screw conveying, PPSU resin and additives are thoroughly mixed evenly. The mixing time is generally 5-15 minutes, depending on the performance of the mixing equipment and the characteristics of the material. During the mixing process, an appropriate amount of dispersant or surface treatment agent can be added as needed to further improve the dispersion effect of the additive in PPSU resin.
3. Melt extrusion
The uniformly mixed material enters the twin-screw extruder for melt extrusion. Twin screw extruders have excellent mixing, shearing, and conveying capabilities, which can fully melt and mix materials at high temperatures and pressures. The temperature setting of the extruder is adjusted according to the melting point of PPSU resin and the characteristics of additives. It is generally divided into multiple temperature ranges, with the temperature gradually increasing from the feeding section to the head, usually between 300-380 ℃. During the melt extrusion process, parameters such as screw speed and material residence time also need to be precisely controlled to ensure sufficient melting and uniform mixing of the material, while avoiding overheating, decomposition, or degradation of the material.
For some PPSU masterbatch with special requirements, such as reinforced or thermally conductive masterbatch, special processes may be required during the extrusion process. For example, when adding long fiber reinforcement materials, a specialized fiber feeding device is needed to ensure that the fibers are evenly distributed in the PPSU resin matrix; For thermal conductive masterbatch, it is necessary to optimize the screw structure and process parameters to improve the dispersion uniformity of thermal conductive fillers in order to achieve good thermal conductivity.
4. Granulation
The material that has been melted and extruded from the machine head is usually pelletized using underwater or air-cooled cutting methods. Underwater granulation is the process of directly feeding extruded materials into water and cutting them into granules using a rotating cutter. The granules are rapidly cooled and shaped in the water. This method produces granules with regular shapes, smooth surfaces, and uniform particle sizes, making it suitable for applications that require high particle quality. Air cooling granulation is the process of cooling the extruded material through an air cooling device before granulation. The equipment is relatively simple, but the cooling effect and shape accuracy of the particles are not as good as underwater granulation.
After cutting, the PPSU masterbatch undergoes drying, screening, and other processes to remove surface moisture and unqualified particles, resulting in PPSU masterbatch products that meet the requirements. Finally, package the product and store it in a dry and ventilated environment to prevent moisture, oxidation, and other factors.
Throughout the entire production process, it is necessary to strictly control various process parameters and regularly maintain and upkeep production equipment to ensure stable quality and reliable performance of the produced PPSU masterbatch. At the same time, it is necessary to conduct strict quality inspections on the products, including appearance, particle size distribution, melt flow rate, mechanical properties, thermal properties, and other aspects, to meet the needs of different users.
Production equipment
The PPSU masterbatch production equipment mainly includes related equipment for raw material processing, mixing, melt extrusion, granulation, and subsequent processing. The following is a specific introduction:
1. Drying equipment
Hot air circulating oven: used for drying PPSU resin raw materials to remove moisture. Its working principle is to achieve the drying effect of materials at a certain temperature and time by circulating hot air. The general temperature can be adjusted within the range of 120-150 ℃, suitable for small and medium-sized production.
Dehumidification dryer: For large-scale production or situations with high requirements for raw material drying, dehumidification dryer is often used. It removes moisture from the dry air through a dehumidification system, and then delivers the dried hot air to the hopper for drying the materials, which can more accurately control the drying temperature and humidity and achieve better drying effect.
2. Hybrid equipment
High speed mixer: Utilizing high-speed rotating stirring blades to thoroughly mix PPSU resin with additives. It has the characteristics of fast mixing speed and high mixing uniformity, and can quickly mix various materials into a uniform mixture, suitable for mixing multiple additives.
Dual planetary mixer: There are two planetary stirring blades rotating inside the mixing kettle, while revolving around the center of the kettle body. The mixing effect is good, which can effectively avoid the problems of material agglomeration and uneven mixing, especially suitable for high viscosity materials and situations that require precise mixing.
3. Extrusion equipment
Twin screw extruder: a key equipment for PPSU masterbatch production. Two interlocking screws rotate inside the barrel, pushing the material forward. At the same time, through the shearing, squeezing, and mixing effects of the screws, the material is fully melted and mixed uniformly at high temperatures. It has good material conveying capacity, mixing effect, and adaptability, and can meet different formula and process requirements by adjusting parameters such as screw combination, speed, and temperature.
Single screw extruder: With a relatively simple structure, it is suitable for the production of PPSU masterbatch with low mixing requirements and low output. Its working principle is to transport and extrude materials through the rotation of a single screw, but its mixing effect is not as good as that of a twin-screw extruder, usually requiring the addition of some auxiliary mixing devices in the feeding section.
4. Granulation equipment
Underwater granulator: The molten material extruded from the extruder head is directly introduced into water, and the material is cut into particles by a high-speed rotating cutter. The particles are quickly cooled and shaped in water. The particles produced have regular shapes, smooth surfaces, uniform particle sizes, high production efficiency, and are suitable for large-scale production of high-quality PPSU masterbatch.
Air cooled pellet cutter: The extruded material is first cooled by an air cooling device, and then cut into pellets by a cutting blade. The equipment has a simple structure and low investment cost, but the cooling effect and shape accuracy of the particles are relatively poor, making it suitable for situations where particle quality requirements are not high and production is small.
5. Auxiliary equipment
Feeding device: including weight loss feeders, volumetric feeders, etc., used to accurately control the feeding amount of various raw materials, ensure the accuracy of the formula and the stability of product quality.
Cooling system: provides cooling circulating water for extruders, pelletizers and other equipment, ensuring that the equipment operates within the normal temperature range, preventing equipment from overheating and damage, and also helping to cool and solidify materials.
Screening equipment: Screen the PPSU masterbatch after granulation to remove particles that are too large or too small, ensuring that the particle size of the product meets the requirements. Commonly used ones include vibrating screens, rotary vibrating screens, etc.
Packaging equipment: The qualified masterbatch after screening is packaged. If an automatic packaging machine is used, it can achieve automation of packaging processes such as measurement, filling, and sealing, improve packaging efficiency and quality, and ensure that the product is not affected by moisture or pollution during storage and transportation.
PPSU masterbatch extruder
Kerke’s masterbatch extruder can be used to produce PPSU masterbatch. Our PPSU masterbatch extruder has multiple models to choose from, which can meet different production requirements.
-
Laboratory Twin Screw Extruder
When will you need a lab twin screw extruder? If you want to make trials and tests of…
-
Parallel Twin Screw Extruder
Our Parallel Co-rotating twin screw extruder is designed for compounding and masterbatch making with an output capacity from…
-
Triple (3 screws) Extruder
3 Screws extruder is a new technology that has many advantages. The triple screw extruder is mainly used…
-
Double-Stage Extrusion System
Mother-baby extrusion system is designed for special materials which can not process on one stage extruder, the first…
-
Banbury Kneader Compounding Line
Our kneader + extruder is designed for making special applications with an output capacity from 30kg/h to 1000kg/h.…
-
Cutting System / Pelletizing System
Different material needs different cutting system, Kerke provides all kinds of cutting system, here is the explanation of…
Related requirements
The working parameters of a twin-screw extruder need to be adjusted according to the characteristics of PPSU resin, the type and amount of additives, and the quality requirements of the product. The following is the general range of working parameters:
Temperature parameters
Feeding section: The temperature is usually set at 200-250 ℃. This stage is mainly to transport the material into the extruder, and the temperature should not be too high to prevent premature melting of the material and affect the conveying effect.
Compression section: The temperature gradually increases to 280-320 ℃. In the compression stage, the material is subjected to the compression and shear action of the screw, and gradually melts. The increase in temperature helps with the plasticization of the material.
Measurement section: The temperature is generally maintained at 300-350 ℃. At this stage, it is necessary to ensure that the material is fully melted and has good fluidity for precise measurement and extrusion.
Head: Temperature controlled between 320-380 ℃. The head temperature directly affects the performance and appearance quality of the extruded material, and an appropriate temperature can ensure smooth extrusion and good formability of the material.
Screw speed
Generally within the range of 100-500 revolutions per minute. Lower rotational speed is suitable for high viscosity materials or situations where high shear requirements are not high, which can avoid material overheating and degradation; A higher rotational speed can improve production efficiency and material mixing effect, but excessively high rotational speed may result in short material residence time, uneven mixing, or excessive shear heat generation.
Pressure parameters
Extrusion pressure: usually between 5-20MPa. The extrusion pressure is related to factors such as the viscosity of the material, screw speed, and die size. Appropriate extrusion pressure helps ensure the stability and uniformity of the material during the extrusion process, as well as the compactness and dimensional accuracy of the product.
Back pressure: The back pressure is generally controlled between 1-5 MPa. The function of back pressure is to increase the mixing effect and plasticization quality of materials. By adjusting back pressure, the residence time and flow state of materials in the extruder can be controlled.
Material retention time
Usually it takes 2-10 minutes. The residence time of materials refers to the time it takes for materials to enter the extruder and reach the extruder head, which has a significant impact on the degree of melting, mixing, and reaction of the materials. The appropriate residence time needs to be determined based on the specific formula and process requirements to ensure that the material is fully plasticized, the additives are evenly dispersed, and the expected product performance is achieved.
In actual production, it is necessary to conduct multiple experiments and adjustments to find the most suitable combination of working parameters for specific production situations, in order to produce PPSU masterbatch products with stable quality and excellent performance.
Application
PPSU masterbatch has excellent heat resistance, water resistance, chemical corrosion resistance, mechanical properties, and electrical properties, and therefore has a wide range of applications in multiple fields. The following are some of the main application areas:
Electronic and electrical field
Connector: The connector made of PPSU masterbatch has good high temperature resistance and electrical insulation performance, and can work stably in high temperature environments to ensure the accuracy and stability of signal transmission.
Socket and switch: Its high insulation and flame retardancy make PPSU masterbatch an ideal material for manufacturing sockets and switches, which can effectively prevent electrical accidents from occurring.
Coil skeleton: PPSU masterbatch has good formability and dimensional stability, and can be made into various complex shaped coil skeletons to meet the requirements of miniaturization and high performance of electronic devices.
Automotive industry field
Automotive components: such as components around the engine, such as the intake manifold, oil pan, water pump impeller, etc. PPSU masterbatch can withstand high temperatures and complex chemical environments in the engine compartment, with good oil and corrosion resistance, effectively improving the service life and reliability of automotive components.
Automotive electronic equipment: PPSU masterbatch is used to manufacture casings and insulation components in electronic control systems, sensors, and other parts of automobiles. It can provide good electrical insulation and anti-interference performance, ensuring the normal operation of automotive electronic equipment in harsh working environments.
Medical field
Medical devices: PPSU masterbatch has good biocompatibility and chemical corrosion resistance, and can be used to manufacture various medical devices such as syringes, infusion sets, blood dialyzers, etc. It has good transparency, making it easy to observe the flow of internal liquids, while also being able to withstand high-temperature and high-pressure sterilization treatment, ensuring the safety and hygiene of medical devices.
Medical packaging: Packaging materials made from PPSU masterbatch have good barrier properties, which can effectively protect drugs and medical devices from external environmental influences, while also having good heat and water resistance, and can adapt to various sterilization methods.
Food packaging field
Food containers: PPSU masterbatch has the characteristics of non toxicity, odorlessness, high temperature resistance, and cooking resistance, and can be used to manufacture various food containers, such as milk bottles, water bottles, preservation boxes, etc. Its good water resistance and chemical corrosion resistance can ensure that food containers will not release harmful substances during long-term use, providing good protection for food.
Food packaging film: The packaging film made of PPSU masterbatch has good flexibility, transparency, and barrier properties, which can effectively prevent food from getting damp, oxidized, and spoiled, and extend the shelf life of food.