PPO masterbatch is a type of plastic masterbatch made from polyphenylene oxide (PPO) as the base material, which has various excellent properties and is widely used in multiple fields. PPO masterbatch can be mixed with other plastics such as ABS HDPE、PPS、PA、HIPS、 Glass fiber and other materials are blended and modified to further improve their performance or reduce costs.
Types
There are mainly the following types of PPO masterbatch:
Flame retardant PPO masterbatch
Introduction: It is made by adding phosphorus based, bromine based and other flame retardants or their compound systems mixed with PPO resin. If environmentally friendly bromine and antimony flame retardants are used, they are organically combined, modified, and synergistically treated with various flame retardant components, and then produced through strict mixing, extrusion, and other processes.
Characteristics: It has excellent flame retardant properties, can effectively prevent material combustion, and can make PPO products reach different flame retardant levels, such as UL94-V0 level, while maintaining some of the original characteristics of PPO. It has excellent dispersibility, good compatibility with PPO resin, high mechanical properties and thermal stability.
Usage: Widely used in fields that require flame retardancy, such as electronic appliances, home appliance casings, wires and cables, such as charger casings, power converters, printer accessories, etc.
Conductive PPO masterbatch
Introduction: It is made by mixing PPO raw materials with conductive fillers such as carbon fiber, carbon black, metal fiber, metal powder, and carbon nanotubes. For example, PPO L1501 is a highly conductive plastic masterbatch prepared by adding 15wt% multi walled carbon nanotubes to PPO as the substrate.
Features: It has good conductivity and can achieve functions such as anti-static, static dissipation, conductivity, and electromagnetic interference (EMI), while retaining the high mechanical strength, dimensional stability, low shrinkage rate, creep resistance, heat resistance, water resistance, acid and alkali resistance, and washing resistance of PPO.
Usage: Suitable for electronic and electrical components, automotive parts, packaging boxes, trays, containers, and other fields that require conductivity and anti-static properties.
Enhanced PPO masterbatch
Introduction: It is usually made by adding reinforcing materials such as glass fiber and carbon fiber to PPO. Products such as SABIC’s GFN1 and GFN2 series are reinforcing materials made of PPO and glass fibers with different contents.
Features: It can significantly improve the mechanical strength, rigidity, heat resistance, and dimensional stability of PPO, making it suitable for applications with high material performance requirements.
Usage: Commonly used in the fields of automotive parts, mechanical parts, electronic and electrical casings, etc., it can be used to manufacture new energy lithium battery trays, water filters and instrument components, pump casings/impellers, etc.
Alloy type PPO masterbatch
Introduction: PPO is blended and modified with other polymers such as polystyrene (PS), polyamide (PA), polypropylene (PP), thermoplastic elastomer (TPE), etc. For example, PPO/HIPS series, PPO/PA series, PPO/PP series, PPO/TPE series, etc.
Characteristics: Through alloying, the advantages of various polymers can be integrated to improve the processing performance, toughness, chemical resistance, and cost reduction of PPO. For example, the PPO/PP series alloys combine the fluidity and chemical resistance of PP with the high-temperature performance, surface hardness, and rigidity of PPO.
Usage: According to different alloy combinations, it can be applied in multiple fields such as electronic appliances, automobiles, packaging, daily necessities, etc. PPO/TPE series can be used for insulation and sheathing in the wire and cable industry.
Color masterbatch type PPO masterbatch
Introduction: It is a coloring masterbatch made by adding high concentration pigments or dyes to PPO resin. Common colors include black, white, yellow, etc., such as the carrier free black KO5500, which is suitable for various plastics such as PPO.
Features: It has good dispersibility, which can make PPO products achieve uniform color, and can customize various colors according to customer needs. Meanwhile, the addition of color masterbatch has little effect on other properties of PPO.
Usage: Mainly used for coloring PPO plastic products, widely applied in the fields of home appliance casings, electronic components, daily necessities, etc., to meet the different user requirements for product appearance color.
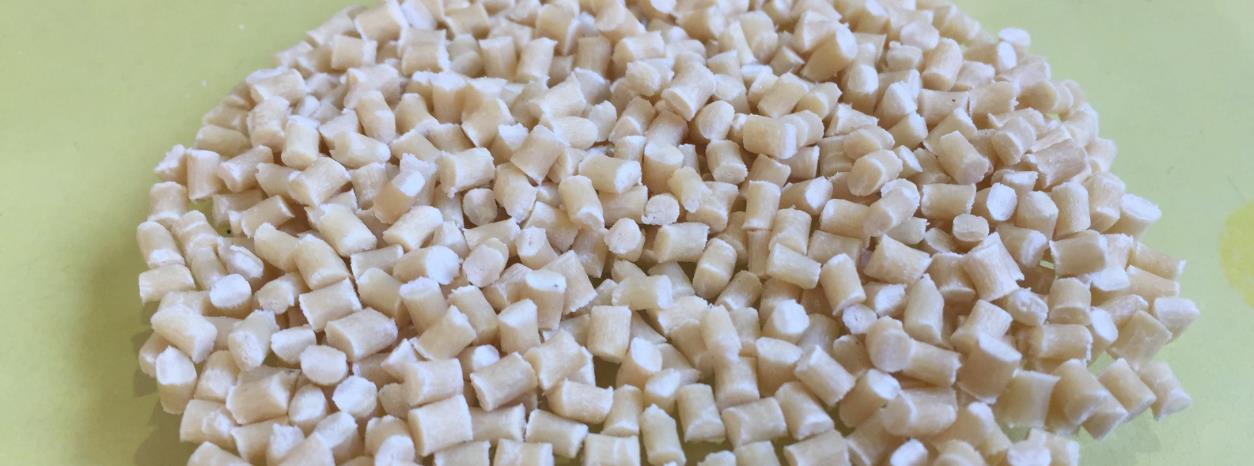
Formula ratio
The formula ratio of PPO masterbatch varies depending on the type. The following are the approximate formula ratios of some common PPO masterbatch, which may be adjusted according to specific needs and processes in actual production:
Flame retardant PPO masterbatch
PPO resin: 50% -70%
Flame retardants: 20% -40%, such as bromine based flame retardants (decabromodiphenyl ether, etc.), phosphorus based flame retardants (ammonium polyphosphate, etc.), and their compound systems.
Synergistic agent: 5% -10%, such as antimony trioxide, used in combination with flame retardants to improve flame retardancy.
Other additives: 0.5% -5%, including antioxidants, lubricants, etc., used to improve processing performance and enhance product stability.
Conductive PPO masterbatch
PPO resin: 70% -90%
Conductive fillers: 10% -30%, such as carbon nanotubes, carbon black, carbon fiber, metal powder, etc. Taking carbon nanotubes as an example, the addition amount of 1% -5% can significantly improve conductivity; The amount of carbon black added is usually around 10% -20%; The amount of carbon fiber added may be between 15% and 30%.
Dispersant: 0.5% -5%, helps to evenly disperse conductive fillers in PPO resin.
Coupling agent: 0.5% -3%, improves the bonding strength between the filler and the resin.
Enhanced PPO masterbatch
PPO resin: 60% -85%
Reinforcement material: 15% -40%, such as glass fiber, carbon fiber, etc. The length and diameter of glass fiber will affect the reinforcement effect, and the general addition amount is between 20% and 40%; The amount of carbon fiber added is usually between 10% and 30%.
Surface treatment agent: 0.5% -3%, used to treat the surface of reinforced materials and improve compatibility with PPO resin.
Other additives: 0.5% -5%, including antioxidants, light stabilizers, etc., to improve the weather resistance and stability of the product.
Alloy type PPO masterbatch
PPO/PS alloy:
PPO resin: 30% -70%
Polystyrene (PS): 30% -70%, adjust the ratio of the two according to the requirements of product performance. For example, to improve processing fluidity, the proportion of PS can be appropriately increased.
Compatibility agent: 3% -10%, used to improve the compatibility between PPO and PS and enhance the performance of the alloy.
PPO/PA alloy:
PPO resin: 40% -60%
Polyamide (PA): 40% -60%, such as PA6, PA66, etc. The type and content of PA will affect the mechanical properties and water absorption of the alloy.
Compatibility agent: 5% -10%, usually using maleic anhydride grafted PPO or PA as a compatibility agent to improve the interfacial bonding strength between PPO and PA.
Other additives: 0.5% -5%, such as antioxidants, lubricants, etc., to improve processing performance and product quality.
Color masterbatch type PPO masterbatch
PPO resin: 80% -95%
Pigments or dyes: 5% -20%, depending on the required color depth and concentration to determine the specific dosage. For example, when preparing dark colored products, the amount of pigment used may be close to 20%; Light colored products have lower usage, possibly around 5%.
Dispersant: 0.5% -5%, helps to evenly disperse pigments in PPO resin, commonly used dispersants include zinc stearate, polyethylene wax, etc.
Other additives: 0-2%, such as antioxidants, light stabilizers, etc., to prevent color masterbatch from changing color during storage and use.
Production process
The production process of PPO masterbatch generally includes steps such as raw material preparation, mixing, extrusion, granulation, packaging, etc. The following is a specific introduction:
1. Raw material preparation
Choose the appropriate PPO resin: Based on the performance requirements of the masterbatch, choose different types and specifications of PPO resin, such as high fluidity, high heat resistance, or high toughness PPO resin.
Prepare additives: Accurately weigh various additives according to the formula, such as flame retardants, conductive fillers, reinforcing materials, pigments, dispersants, coupling agents, etc. Ensure that the quality and purity of the additives meet the requirements, and perform drying treatment to remove moisture and prevent the formation of bubbles or affecting product performance during processing.
2. Mixing
Pre mixing: Pre mix PPO resin with additives in a high-speed mixer or mixer to evenly disperse the additives in the PPO resin. For some additives that are difficult to disperse, such as carbon nanotubes, carbon fibers, etc., the method of first mixing the additive with a small amount of PPO resin to make a masterbatch, and then mixing it with a large amount of PPO resin can be used to improve the dispersion effect.
Add additives: As needed, add an appropriate amount of dispersants, coupling agents, and other additives during the mixing process to improve the compatibility and dispersibility between the additives and PPO resin. For example, the use of silane coupling agents can improve the bonding strength between glass fibers and PPO resin, and the use of dispersants such as zinc stearate can make pigments more evenly dispersed in PPO resin.
3. Extrusion
Choose an extruder: Select the appropriate extruder based on production scale and product requirements. Generally, twin-screw extruders are used, which have good mixing, plasticizing, and conveying capabilities, ensuring that materials are fully mixed and uniformly plasticized during the extrusion process.
Set process parameters: Based on the characteristics of PPO resin and additives, set the temperature, speed, pressure and other process parameters of the extruder. Usually, the temperature of the extruder is controlled between 230-280 ℃, depending on the type and formula of PPO resin. The speed is generally within the range of 100-500 revolutions per minute, and the pressure is adjusted according to the fluidity of the material and the structure of the extruder.
Extrusion operation: Add the mixed material into the hopper of the extruder, and the material gradually moves forward under the push of the extruder screw, while being heated, sheared, and mixed, and plasticized into a uniform melt. During the extrusion process, attention should be paid to observing the extrusion state of the material, such as the temperature, pressure, flow rate, etc. of the melt, and adjusting the process parameters in a timely manner to ensure the stability of the extrusion process and the consistency of product quality.
4. Granulation
Adopting appropriate granulation methods: The extruded melt is usually extruded into strips or filaments through a die, and then granulated using methods such as air cooling, water cooling, or hot cutting. Air cooled granulation is the process of cooling and solidifying extruded strips through an air cooling device, and then cutting them into pellets using a granulator; Water cooled granulation is the process of cooling the strip material through a water tank and then cutting it into pellets; Hot cutting granulation is the process of directly cutting the melt into pellets at the extrusion die, and then solidifying them through air or water cooling.
Control particle quality: During the granulation process, it is important to control the size, shape, and uniformity of the particles. Generally speaking, the particle size of PPO masterbatch is around 2-5 millimeters, and the particle shape should be regular and uniform in size to ensure fluidity and dispersion in subsequent processing. At the same time, attention should be paid to avoiding problems such as particle adhesion, breakage, or uneven surface.
5. Packaging
Drying treatment: The granulated PPO masterbatch usually contains a certain amount of moisture and needs to be dried to reduce the moisture content and prevent it from affecting product performance during storage and use. The drying temperature is generally between 80-120 ℃, and the drying time depends on the moisture content of the masterbatch and the efficiency of the drying equipment, usually 2-6 hours.
Packaging and storage: Dry PPO masterbatch should be placed in sealed bags or packaging bags, and the packaging should have good moisture, dust, and oxidation resistance to ensure that the quality of the masterbatch is not affected during storage and transportation. At the same time, the product name, model, specifications, production date, shelf life, and other information should be marked on the packaging bag, and stored according to the prescribed storage conditions. Generally, it should be stored in a dry, ventilated, and cool environment, avoiding direct sunlight and high temperature and humidity.
Production equipment
The PPO masterbatch production equipment mainly includes mixing equipment, extrusion equipment, granulation equipment, drying equipment, and packaging equipment. The following is a specific introduction:
1. Hybrid equipment
High speed mixer: used to preliminarily mix PPO resin with various additives, and achieve uniform mixing of materials in a short time through high-speed rotating stirring blades. Its advantages are high mixing efficiency, good mixing effect, and the ability to quickly mix different materials evenly.
Dual planetary mixer: It has two planetary agitator blades. During the mixing process, the agitator blades rotate around their own axis and revolve around the axis of the mixing container, achieving efficient mixing and dispersion of materials. For PPO masterbatch formulations that require precise mixing ratios and high uniformity, a dual planetary mixer is a better choice.
2. Extrusion equipment
Twin screw extruder: It is one of the core equipment for PPO masterbatch production. Its two screws mesh with each other, allowing for sufficient shearing, mixing, and plasticization of the material during rotation. Twin screw extruders have good material conveying and self-cleaning capabilities, and can adapt to materials with different viscosities and flowability. They can also precisely control the material processing process by adjusting parameters such as screw speed, temperature, and pressure.
Extruder supporting equipment: including hopper, feeding device, heating and cooling system, melt pump, etc. The hopper is used to store materials to be processed, and the feeding device can accurately control the feeding amount of materials to ensure the stability of the extrusion process. The heating and cooling system is used to regulate the temperature of each section of the extruder, so that the material can be plasticized and extruded within a suitable temperature range. The melt pump can further stabilize the pressure and flow rate of the melt, improving the quality and accuracy of the extruded product.
3. Granulation equipment
Air cooled die surface hot cutting granulator: At the extruder die head, the high-temperature melt is directly cut into particles, and then the particles are rapidly cooled and solidified through an air cooling system. This granulator has the advantages of high production efficiency, regular particle shape, and uniform size, and is suitable for producing PPO masterbatch of various specifications.
Water cooled strip granulator: First, the extruded melt is cooled into strips through a water tank, and then the strip material is cut into particles by a granulator. The equipment structure of the water-cooled strip granulator is relatively simple, and the cooling effect of the particles is good. However, the production efficiency is relatively low, and there may be some residual moisture on the surface of the particles, which requires subsequent drying treatment.
4. Drying equipment
Hot air circulating oven: Drying PPO masterbatch by circulating hot air, causing the moisture in the masterbatch to evaporate and be discharged at a certain temperature. The hot air circulation oven has the advantages of uniform drying, high temperature control accuracy, and simple operation, and is suitable for small and medium-sized production.
Boiling dryer: uses hot air to make materials boil in the drying chamber, achieving rapid drying. The boiling dryer has high drying efficiency, which can reduce the moisture content of the masterbatch to a lower level in a short period of time, and the dried masterbatch has good fluidity and is not easy to clump.
5. Packaging equipment
Automatic weighing and packaging machine: capable of accurately weighing a certain weight of PPO masterbatch and putting it into packaging bags. The automatic weighing and packaging machine has the advantages of high weighing accuracy, fast packaging speed, and easy operation, and can be adjusted according to different packaging specifications.
Sealing machine: used to seal packaging bags containing PPO masterbatch, ensuring the sealing of the packaging bag and preventing the masterbatch from being damp, oxidized, etc. Common sealing machines include heat sealing machines, ultrasonic sealing machines, etc. Choose the appropriate sealing equipment according to the material and requirements of the packaging bag.
PPO masterbatch extruder
Kerke’s masterbatch extruder can be used to produce PPO masterbatch. Our PPO masterbatch extruder has multiple models to choose from, which can meet different production requirements.
-
Laboratory Twin Screw Extruder
When will you need a lab twin screw extruder? If you want to make trials and tests of…
-
Parallel Twin Screw Extruder
Our Parallel Co-rotating twin screw extruder is designed for compounding and masterbatch making with an output capacity from…
-
Triple (3 screws) Extruder
3 Screws extruder is a new technology that has many advantages. The triple screw extruder is mainly used…
-
Double-Stage Extrusion System
Mother-baby extrusion system is designed for special materials which can not process on one stage extruder, the first…
-
Banbury Kneader Compounding Line
Our kneader + extruder is designed for making special applications with an output capacity from 30kg/h to 1000kg/h.…
-
Cutting System / Pelletizing System
Different material needs different cutting system, Kerke provides all kinds of cutting system, here is the explanation of…
Related requirements
In the production of PPO masterbatch, the extruder plays a key role and has the following requirements:
1. Good plasticizing ability
PPO resin usually has a high melt viscosity and requires an extruder to provide sufficient heat and shear force to achieve good plasticization. The screw design of the extruder should be able to fully mix and melt the materials inside the barrel, ensuring that PPO resin and additives are evenly dispersed and form a uniformly textured melt.
Equipped with a stable temperature control system, it can accurately control the temperature of each heating section to meet the processing temperature requirements of PPO resin. Generally, the processing temperature is between 230-280 ℃.
2. Efficient mixing performance
Due to the need to add various additives such as flame retardants, reinforcement materials, pigments, etc. in the production of PPO masterbatch, the extruder needs to have efficient mixing performance to evenly distribute the additives in the PPO resin.
The combination design of the meshing block and screw of the twin-screw extruder should be reasonable. By using meshing blocks of different shapes and angles, strong shearing, stretching, and mixing effects can be generated, promoting the mutual diffusion and uniform mixing of materials.
3. Accurate measurement and conveying capacity
In order to ensure the quality stability of PPO masterbatch, the extruder needs to precisely control the extrusion amount and conveying speed of the material.
Equipped with high-precision measuring devices, such as weight loss measuring feeders, it can accurately feed PPO resin and additives into the extruder according to the formula ratio. At the same time, the screw speed of the extruder should be precisely adjustable to achieve stable material conveying and ensure consistent product quality.
4. Strong adaptability
The formula and performance requirements of PPO masterbatch may vary depending on different application fields, and the extruder should be able to adapt to changes in multiple formulas and processes.
The length to diameter ratio, compression ratio and other parameters of the screw should be flexibly adjustable to adapt to materials with different viscosities, flowability and filling amounts. For example, for high filling PPO masterbatch, a longer aspect ratio may be required to ensure sufficient mixing and plasticization of the material.
5. High production efficiency
In industrial production, extruders need to have high production efficiency to meet market demand.
The extruder should have a large extrusion volume and a fast screw speed, while maintaining a stable operating state, reducing downtime and failure rates. In addition, a reasonable die design can also help improve production efficiency, allowing the melt to be evenly extruded and formed into the desired shape.
6. Reliable quality stability
The key components of the extruder, such as the screw and barrel, should have good wear resistance and corrosion resistance to ensure stable operation during long-term production without affecting product quality.
Equipped with advanced automation control system, it can monitor and adjust parameters such as temperature, pressure, and speed during the extrusion process in real time, timely discover and solve problems in production, and ensure the stability and consistency of product quality.
7. Good environmental performance
During the production process, the extruder should minimize the emission of noise, exhaust gas, and dust to meet environmental protection requirements.
Adopting efficient cooling systems and ventilation devices to reduce energy consumption and heat emissions during the production process. At the same time, effective collection and treatment of exhaust gas and dust are carried out to reduce environmental pollution.
Application
PPO masterbatch has excellent electrical insulation properties, mechanical properties, heat resistance, and flame retardancy, and is widely used in various fields such as electronics, automotive, aerospace, and construction. The following is a specific introduction:
Electronic and electrical field
Connector: PPO masterbatch has good electrical insulation performance and mechanical strength, which can maintain stable performance in different working environments, ensuring reliable connection of connectors. It is widely used in the manufacturing of connectors for electronic devices such as computers, mobile phones, and tablets.
Coil skeleton: Its low dielectric constant and low dielectric loss characteristics enable the coil to maintain good performance at high frequencies, reduce energy loss and distortion in signal transmission, and withstand high temperatures, meeting the heat dissipation requirements of the coil during operation.
Switch housing: The switch housing made of PPO masterbatch has good flame retardancy and mechanical properties, which can effectively prevent fire accidents and ensure that the switch is not easily damaged during frequent use, thereby extending its service life.
Automotive field
Automotive components: such as components around the engine, such as the intake manifold and throttle body, PPO masterbatch has high heat resistance and mechanical strength, and can withstand high temperatures and complex mechanical stresses in the engine compartment, ensuring the normal operation of the components.
Automotive electrical system: PPO masterbatch can be used to manufacture various electrical connectors, sockets, etc. in the automotive electrical system. Its good electrical performance and weather resistance can ensure the stable operation of the automotive electrical system under different climatic conditions.
Aerospace field
Aviation interior parts: PPO masterbatch has the advantages of light weight, high strength, good flame retardancy, and chemical corrosion resistance. It can be used to manufacture interior parts such as seat armrests and luggage racks for aircraft, reducing the weight of the aircraft while ensuring the safety and durability of the interior parts.
Aviation electronic equipment: Due to the excellent electrical insulation and electromagnetic interference resistance of PPO masterbatch, it can be used to manufacture the shell and circuit board substrate of aviation electronic equipment, ensuring stable operation of electronic equipment in complex electromagnetic environments and improving the reliability of aviation electronic systems.
Construction field
Wire and cable: PPO masterbatch has good insulation and flame retardant properties, and can be used as an insulation layer material for wire and cable, effectively preventing short circuits and fire accidents, and improving the safety of building electrical systems.
Building panels: Building panels with added PPO masterbatch have good thermal insulation performance and mechanical strength, and can be used for external wall insulation, roof insulation, and other parts of buildings, improving the energy-saving effect and structural stability of buildings.
Other areas
Medical devices: PPO masterbatch has good biocompatibility and chemical stability, and can be used to manufacture some medical device components, such as medical catheters, surgical instrument handles, etc.
Office supplies, such as photocopiers and printers, utilize the wear-resistant, heat-resistant, and excellent mechanical properties of PPO masterbatch to ensure the stability and reliability of office supplies during long-term use.