PES masterbatch, also known as polyethersulfone masterbatch, is a high-performance engineering plastic masterbatch mainly composed of polyethersulfone (PES). PES is an amorphous high-performance thermoplastic polymer with excellent heat resistance, mechanical properties, chemical stability, and electrical properties. Therefore, PES masterbatch has a wide range of applications in multiple high-end manufacturing fields.
Basic characteristics
Physical property
Appearance and Form: PES masterbatch is usually in granular form, and the color can be customized according to needs, such as black, natural color, or transparent.
Dimensional stability: It has excellent dimensional stability and can maintain stable dimensions in high temperatures and harsh environments.
Coefficient of thermal expansion: A small coefficient of thermal expansion helps maintain the dimensional accuracy of the component during temperature changes.
Mechanical property
Strength and modulus: PES masterbatch has high strength and modulus, and can withstand large loads.
Resilience: Exhibiting good resilience, suitable for application scenarios that require withstanding impact and vibration.
Thermal performance
Long term use temperature: The long-term use temperature of PES masterbatch can reach 180-200 ℃, with better short-term heat resistance and the ability to withstand higher temperatures.
Thermal stability: It can maintain stable performance at high temperatures and is not easily deformed or decomposed.
Chemical stability
Corrosion resistance: It has corrosion resistance to various chemical substances, including acids, bases, and organic solvents.
Hydrolysis resistance: It can maintain stable performance even in humid environments.
Electrical performance
Electrical insulation: It can maintain stable electrical insulation performance in high temperature and high humidity environments.
Dielectric constant and dielectric loss: It has stable dielectric constant and dielectric loss, suitable for the field of electronics and electrical engineering.
Flame retardancy
Some PES masterbatch have flame retardant properties and can meet specific safety standards, such as UL94-V0 level.
Processability
Processing technology: It can be processed into various products through various processes such as injection molding, extrusion, blow molding, etc.
Pre drying requirements: Pre drying is required before processing to remove absorbed moisture and ensure processing quality.
Types
PES (Polyether Sulfone) masterbatch can have multiple types according to different classification standards, and the following are some common classifications:
Classification by function
Ordinary PES masterbatch: It has the basic properties of PES resin, such as good heat resistance, mechanical properties, and electrical insulation, and is mainly used in the production of general plastic products to improve the comprehensive performance of the products.
Enhanced PES masterbatch: usually added with reinforcing materials such as glass fiber and carbon fiber, which can significantly improve the mechanical strength, rigidity, and dimensional stability of PES products. It is suitable for engineering plastic components with high strength requirements, such as automotive parts, electronic equipment casings, etc.
Flame retardant PES masterbatch: By adding flame retardants for modification, PES masterbatch has good flame retardant properties, which can meet the strict requirements for material flame retardancy in fields such as electronics and aerospace, and reduce the risk of fire.
Wear resistant PES masterbatch: with the addition of wear-resistant fillers or surface treatment, the wear resistance and friction resistance of PES material are improved. It is commonly used in the manufacturing of components that require long-term friction resistance, such as gears, bearings, conveyor belts, etc.
Conductive PES masterbatch: By adding conductive media such as carbon black and carbon fiber, PES masterbatch is endowed with conductivity and can be used to manufacture plastic products with anti-static and electromagnetic shielding functions. It has important applications in electronics, communication, and other fields.
Classified by additives
Inorganic additive type PES masterbatch: Adding inorganic fillers such as calcium carbonate, talc powder, titanium dioxide, etc. can improve the processing performance of PES, reduce costs, and to some extent enhance the rigidity, heat resistance, and dimensional stability of the product.
Organic additive PES masterbatch: Organic additives such as plasticizers, antioxidants, UV absorbers, etc. are added to improve the flexibility, aging resistance, and weather resistance of PES, extending the service life of the product.
Composite additive PES masterbatch: Multiple types of additives are added simultaneously to achieve comprehensive performance improvement and meet complex application requirements. For example, by simultaneously adding glass fiber and flame retardant, PES masterbatch can have both high strength and good flame retardancy.
Classified by processing method
Injection grade PES masterbatch: has good fluidity and formability, suitable for injection molding processes, can quickly fill mold cavities, and produce high-precision, complex shaped plastic products, such as electronic component casings, toys, etc.
Extrusion grade PES masterbatch: With good melt strength and uniformity, it is suitable for extrusion molding processes and can produce plastic products such as pipes, sheets, films, etc. It is widely used in construction, packaging, medical and other fields.
Blow molding grade PES masterbatch: With high melt viscosity and elasticity, it can maintain good shape stability during the blow molding process and is used to manufacture various hollow plastic products, such as plastic bottles, containers, etc.
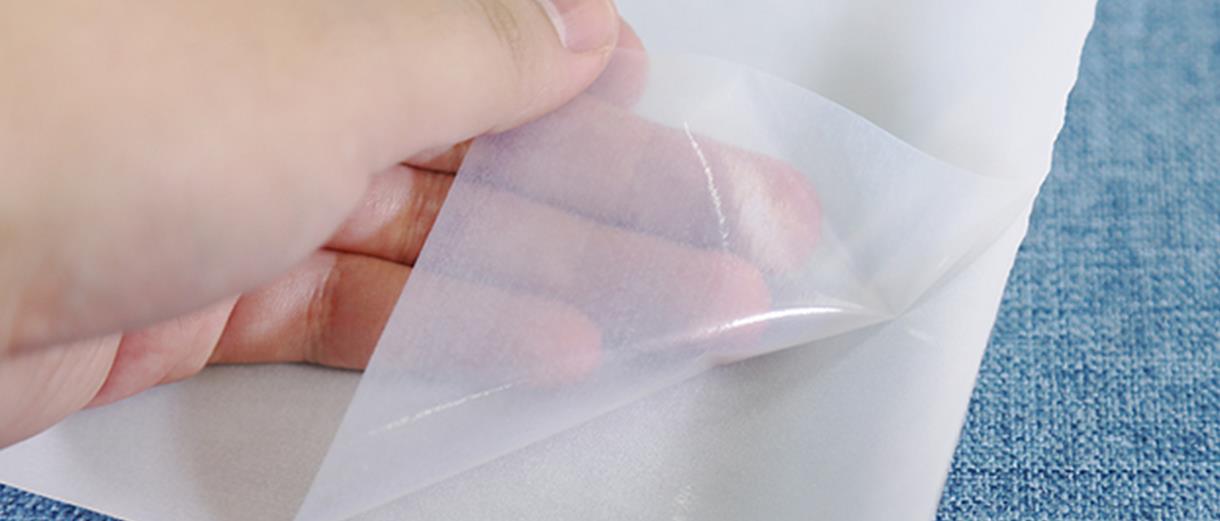
Formula ratio
The proportion of different types of PES masterbatch formulations may vary depending on specific performance requirements, production processes, and application scenarios. The following are some examples of the approximate formula proportion range for common types of PES masterbatch:
Enhanced PES masterbatch
PES resin: 60% -80%
Fiberglass: 20% -40%
Coupling agent: 0.5% -2%, used to improve the bonding strength between glass fiber and PES resin.
Flame retardant PES masterbatch
PES resin: 70% -90%
Flame retardant: 10% -30%, choose different flame retardants and their dosage according to the required flame retardant level, such as bromine based flame retardants, phosphorus based flame retardants, etc.
Synergistic agent: 0-5%, such as antimony trioxide, used in combination with flame retardants to enhance the flame retardant effect.
Wear resistant PES masterbatch
PES resin: 75% -90%
Wear resistant fillers: 10% -25%, such as molybdenum disulfide, graphite, silicon carbide, etc.
Lubricant: 0.5% -3%, helps improve processing performance and increase surface smoothness, reducing friction.
Conductive PES masterbatch
PES resin: 70% -90%
Conductive medium: 10% -30%, such as conductive carbon black, carbon fiber, etc.
Dispersant: 0.5% -3%, helps to evenly disperse the conductive medium in the resin.
Inorganic additive PES masterbatch
PES resin: 70% -90%
Inorganic fillers: 10% -30%, such as calcium carbonate, talc powder, titanium dioxide, etc.
Surface treatment agent: 0.5% -3%, used to improve the compatibility between inorganic fillers and PES resin.
Organic additive PES masterbatch
PES resin: 90% -98%
Plasticizer: 0-10%, added according to the requirements for flexibility.
Antioxidants: 0.1% -1%
UV absorber: 0.1% -1%, used to improve weather resistance.
The above formula ratios are for reference only. In actual production, adjustments and optimizations need to be made based on specific product requirements, raw material characteristics, and production equipment to achieve optimal performance and economic benefits. At the same time, there may be differences in the production formulas of different manufacturers.
Production process
The production process of PES masterbatch usually includes steps such as raw material preparation, mixing, extrusion, granulation, etc. The following is a specific introduction:
1. Raw material preparation
Select appropriate PES resin particles as the base material, prepare corresponding additives according to the type of masterbatch, such as reinforcing materials, flame retardants, wear-resistant fillers, conductive media, etc., and ensure that the purity and quality of the raw materials meet production requirements.
2. Mixing
Add PES resin and additives into the high-speed mixer according to the set formula ratio for thorough mixing. By high-speed stirring, the additive is uniformly dispersed on the surface of PES resin particles to form a premix. For some difficult to disperse additives, it may be necessary to add an appropriate amount of dispersant to improve the dispersion effect.
3. Extrusion
The premix is fed into the twin-screw extruder. Twin screw extruders have good mixing and conveying capabilities, which can fully melt and mix materials in the barrel. During the extrusion process, it is necessary to strictly control parameters such as temperature, speed, and pressure of the extruder.
Temperature control is particularly critical, and different heating temperatures should be set according to the characteristics of PES resin and the performance of additives. Generally, the heating temperature should gradually increase from the feeding section to the machine head to ensure that the material can melt evenly during the extrusion process, while avoiding material degradation or additive failure caused by high temperature.
The screw speed will affect the mixing effect and extrusion yield of the material, and needs to be adjusted according to the actual situation. Usually, higher rotational speeds are beneficial for improving mixing uniformity, but excessively high rotational speeds may cause material shear overheating.
The pressure of the extruder also needs to be kept stable to ensure smooth extrusion of materials and achieve good extrusion quality.
4. Granulation
The material extruded from the extruder head is in the form of strips or filaments, and is cooled and shaped by air or water cooling. The cooled material enters the granulator and is cut into particles of a certain length by a cutting tool, resulting in PES masterbatch.
During the granulation process, it is necessary to control the cutting speed and the sharpness of the cutting tool to ensure that the particle size of the mother granules is uniform and the surface is smooth. At the same time, the masterbatch can be screened as needed to remove particles that are too large or too small, ensuring consistency in product quality.
5. Packaging
The produced PES masterbatch is packaged in sealed bags or plastic drums to prevent moisture and contamination. The product model, specifications, production date, and other information should be indicated on the packaging for storage and management purposes.
Throughout the entire production process, in order to ensure the stability and consistency of product quality, it is necessary to regularly maintain and upkeep the production equipment, conduct quality inspections on raw materials and products, such as testing the particle size distribution of masterbatch, melt flow rate, mechanical properties, flame retardancy, and other indicators. Based on the inspection results, production process parameters should be adjusted in a timely manner.
Production equipment
The PES masterbatch production equipment mainly includes mixing equipment, extrusion equipment, granulation equipment, etc. The following is a specific introduction:
1. Hybrid equipment
High speed mixer: used to thoroughly mix PES resin with various additives. It achieves uniform mixing of materials in a short period of time through high-speed rotating stirring blades. Its characteristics are high mixing efficiency, good mixing uniformity, and the ability to adjust according to different formulas and production requirements.
Dual planetary mixer: suitable for occasions with high mixing requirements, especially when the content of additives is low or finer mixing is needed. It has two planetary stirring blades that rotate while revolving, generating strong shear and stirring effects to ensure uniform dispersion of additives in PES resin.
2. Extrusion equipment
Twin screw extruder: It is one of the core equipment for PES masterbatch production. It has two interlocking screws that can provide good material conveying, mixing, and plasticizing effects. Twin screw extruders can be designed with screw combinations based on different material characteristics and process requirements to achieve optimal extrusion results. It is also equipped with multiple heating and cooling sections, which can accurately control the temperature of the material during the extrusion process.
Single screw extruder: In some situations where mixing requirements are not high or production scale is small, single screw extruders are also used. It has a simple structure and easy operation, but compared to twin-screw extruders, its mixing and plasticizing ability is relatively weak. Single screw extruders are usually suitable for producing relatively simple PES masterbatch products.
3. Granulation equipment
Underwater granulator: It is one of the commonly used granulation equipment at present. It directly cuts the extruded hot melt material into particles underwater, and the cut particles quickly cool in water. It has the advantages of regular particle shape, uniform particle size, and smooth surface. The production efficiency of the underwater granulator is high, and it can adapt to different production scales. The particle size can be controlled by adjusting the speed and quantity of the cutter.
Air cooled granulator: The extruded material is cooled by air cooling before being pelletized. The structure of air-cooled granulators is relatively simple and cost-effective, but the cooling effect and shape accuracy of particles may not be as good as underwater granulators. It is suitable for situations where particle quality requirements are not particularly high.
4. Auxiliary equipment
Feeding system: including hopper, automatic feeding machine, etc., used to automatically transport raw materials to the mixer and extruder, achieve automated production, improve production efficiency, and reduce manual operation errors.
Cooling system: For extruders and granulators, corresponding cooling systems such as circulating water cooling devices, air cooling devices, etc. need to be equipped to control the temperature of equipment and materials, ensuring the stability of the production process and product quality.
Screening equipment: used to screen the PES masterbatch after granulation, remove oversized or undersized particles that do not meet the particle size requirements, and ensure the uniformity of the product’s particle size. Common screening equipment includes vibrating screens, rotating screens, etc.
Packaging equipment: including automatic packaging machines, sealing machines, etc., used to package the produced PES masterbatch, usually using sealed packaging to prevent moisture, oxidation, or contamination of the masterbatch.
In addition, in order to ensure quality control and testing in the production process, it is necessary to equip some testing equipment, such as melt flow rate testers, mechanical performance testing machines, thermogravimetric analyzers, particle size analyzers, etc., for the detection and analysis of various performance indicators of raw materials, semi-finished products, and finished products.
PES masterbatch extruder
Kerke’s masterbatch extruder can be used to produce PES masterbatch. Our PES masterbatch extruder has multiple models to choose from, which can meet different production requirements.
-
Laboratory Twin Screw Extruder
When will you need a lab twin screw extruder? If you want to make trials and tests of…
-
Parallel Twin Screw Extruder
Our Parallel Co-rotating twin screw extruder is designed for compounding and masterbatch making with an output capacity from…
-
Triple (3 screws) Extruder
3 Screws extruder is a new technology that has many advantages. The triple screw extruder is mainly used…
-
Double-Stage Extrusion System
Mother-baby extrusion system is designed for special materials which can not process on one stage extruder, the first…
-
Banbury Kneader Compounding Line
Our kneader + extruder is designed for making special applications with an output capacity from 30kg/h to 1000kg/h.…
-
Cutting System / Pelletizing System
Different material needs different cutting system, Kerke provides all kinds of cutting system, here is the explanation of…
Related requirements
In the production of PES masterbatch, extrusion equipment needs to meet various requirements such as plasticization, mixing, and temperature control to ensure product quality and production efficiency. The following is a specific introduction:
Good plasticizing ability
PES resin has a high melting point and viscosity, and extrusion equipment needs to have sufficient plasticizing ability to achieve complete melting of PES resin in a short period of time, ensuring good flowability of the material during the extrusion process to meet the requirements of the production process.
Efficient mixing performance
Due to the need to add various additives such as reinforcing materials, flame retardants, fillers, etc. in the production of PES masterbatch, the extrusion equipment should be able to fully mix PES resin and additives in a molten state to ensure the consistency and stability of masterbatch performance.
Accurate temperature control
PES resin is sensitive to temperature, and excessive temperature can easily lead to resin degradation and discoloration, affecting product performance; If the temperature is too low, it will cause poor plasticization of the material and make extrusion difficult. Therefore, the extrusion equipment needs to be equipped with a high-precision temperature control system, which can control the material temperature within the set range at different production stages. The temperature control accuracy usually needs to reach ± 1 ℃ or even higher.
Stable pressure control
Stable extrusion pressure is the key to ensuring product quality and production stability. The extrusion equipment should be able to maintain stable extrusion pressure at different production speeds and material characteristics, avoiding problems such as unstable product size and poor surface quality caused by pressure fluctuations.
Strong corrosion resistance
During the production process, certain additives may have certain corrosiveness, such as some halogenated flame retardants. Therefore, the components such as the barrel and screw of the extrusion equipment that come into contact with the material need to be made of corrosion-resistant materials, such as stainless steel, alloy steel, etc., to extend the service life of the equipment and ensure the continuity of production.
High production efficiency
To meet market demand and reduce production costs, extrusion equipment should have high production capacity and be able to extrude a certain amount of high-quality PES masterbatch per unit time. At the same time, the equipment should have a good degree of automation, be easy to operate and maintain, reduce manual intervention, and improve production efficiency.
Flexible screw combination design
Different types of PES masterbatch production require different screw combinations to achieve optimal extrusion results. Extrusion equipment should allow for flexible adjustment of parameters such as the length to diameter ratio, groove depth, and compression ratio of screws based on specific material characteristics, formulas, and production process requirements to meet diverse production needs.
Application
PES masterbatch has various excellent properties, such as high heat resistance, good mechanical properties, flame retardancy, etc., so it has a wide range of applications in multiple fields. The following are some of the main application areas:
Electronic and electrical field
Connector: PES masterbatch has high heat resistance and good electrical insulation performance, which can withstand the high temperature generated by electronic devices during operation while ensuring the stability of signal transmission. Therefore, it is widely used in the manufacture of various connectors.
Switch socket: Its excellent flame retardant performance can effectively prevent fires and ensure electrical safety, and is often used in the production of switch socket shells.
Coil skeleton: The coil skeleton made of PES masterbatch has good dimensional stability and mechanical strength, and can maintain its shape unchanged during long-term use, ensuring the normal operation of the coil.
Automotive industry field
Engine peripheral components such as engine hood, intake manifold, etc. PES masterbatch can maintain good mechanical properties in high temperature environments, withstand high temperatures and complex chemical environments in the engine compartment, while reducing vehicle weight and improving fuel economy.
Automotive electronic components: used for manufacturing automotive electronic control unit (ECU) housings, sensor housings, etc. Their high insulation and electromagnetic interference resistance can protect electronic components from external environmental influences, ensuring the stable operation of automotive electronic systems.
Aerospace field
Internal components of aircraft, such as seat frames, luggage racks, etc., PES masterbatch has the characteristics of high strength and lightweight, which can effectively reduce the weight of the aircraft, improve fuel efficiency, and lower operating costs while ensuring the structural strength of the aircraft.
Aviation electronic equipment: Its excellent radiation resistance and electrical performance make it an ideal material for manufacturing aviation electronic equipment casings and circuit boards. It can ensure the reliability and stability of equipment in complex electromagnetic environments and radiation conditions at high altitudes.
Fiber field
High performance fibers: PES masterbatch can be used to produce high-performance fibers, such as special industrial fabrics, filter materials, etc. These fibers have characteristics such as high strength, high temperature resistance, and chemical corrosion resistance, which can meet the requirements for use in harsh environments.
Medical fiber: Due to its good biocompatibility, PES masterbatch can be used to manufacture medical fiber materials such as sutures and artificial blood vessels, and has important applications in the medical field.
In addition, PES masterbatch has certain applications in the fields of optics, environmental protection, etc., such as manufacturing optical lenses, environmentally friendly plastic films, etc. With the continuous development of technology, the application fields of PES masterbatch will continue to expand and deepen.