PEI masterbatch, also known as polyetherimide masterbatch, is a high-performance engineering plastic masterbatch mainly composed of polyetherimide (PEI). PEI is a super engineering plastic made from amorphous polyetherimide, which appears amber in color and has excellent mechanical, thermal, chemical, and electrical properties.
Basic characteristics
Physical property
Appearance and Form: PEI masterbatch typically appears as light yellow to amber transparent or semi transparent granules with a density ranging from 1.28 to 1.42 g/cm³.
Dimensional stability: It has excellent dimensional stability and can maintain stable dimensions under various environmental conditions.
Coefficient of thermal expansion: The coefficient of thermal expansion is small and uniform, which helps to maintain the dimensional accuracy of the component during temperature changes.
Mechanical property
Strength and modulus: It has excellent strength and modulus, with a yield tensile strength of up to 15000 pounds per square inch, and remains at 6000 pounds per square inch at 190 degrees Celsius.
Resilience: With a high elongation at break (60-80%), it exhibits extraordinary toughness and provides design freedom for the hook and loop structure of the component.
Creep resistance and fatigue resistance: Under long-term constant low stress loads, the change in apparent modulus can be ignored, and its creep behavior only needs to be considered under high temperature and stress.
Thermal performance
Long term use temperature: The long-term use temperature range of PEI masterbatch is between 150 ° C and 170 ° C, depending on product specifications and additives.
Short term heat resistance: The short-term heat resistance is even more outstanding, able to withstand temperatures up to 180 ° C to 200 ° C without damage.
Thermal stability: able to maintain high strength, rigidity, and wear resistance at high temperatures.
Chemical stability
Chemical resistance: It has good corrosion resistance to various chemical substances, including most hydrocarbons, alcohols, and all halogenated solvents, as well as resistance to inorganic acids and short-term weak bases.
Hydrolysis resistance: After soaking in boiling water for 10000 hours, the tensile strength remains above 85%.
Electrical performance
Electrical performance: It has stable dielectric constant, dielectric loss, and extremely high dielectric strength over a wide frequency and temperature range, making it the preferred material in the electronics and electrical industry.
Flame retardancy
It has excellent natural flame retardancy, inherent flame retardancy and low smoke without adding any additives, with an oxygen index of 47% and a combustion rating of UL94-V-0.
Processability
Molding processability: It can be processed using most thermoplastic molding methods such as injection molding, extrusion, blow molding, etc., but pre drying is required before processing to remove absorbed moisture.
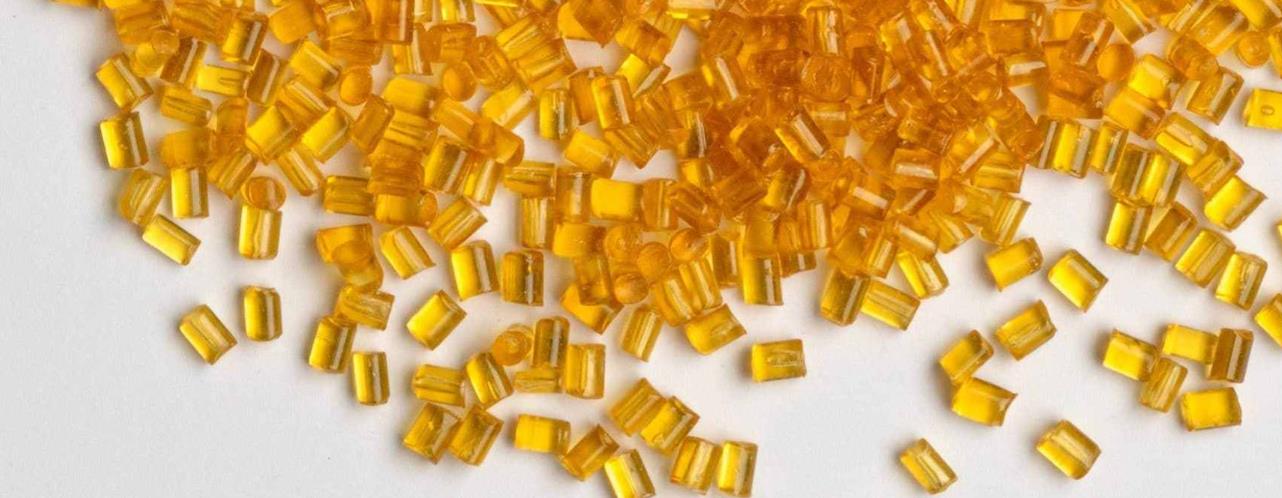
Types
Classified by reinforcement material
Fiberglass reinforced PEI masterbatch: Adding glass fibers to PEI resin can significantly improve the strength, rigidity, and thermal stability of the material. For example, RTP 2103Z in the United States is suitable for injection molded products such as automotive parts and electronic and electrical casings that require high mechanical performance.
Carbon nano filled PEI masterbatch: Adding carbon nano materials can endow PEI masterbatch with excellent conductivity, anti-static properties, as well as good mechanical and thermal properties. Such as RTP 2199X89189C from the United States, it can be used in electronic device components that require electrostatic protection, aerospace, and other fields.
Aromatic polyamide fiber filled PEI masterbatch: Adding aromatic polyamide fiber can improve the wear resistance, impact resistance, and high temperature resistance of PEI masterbatch. Like RTP’s 2100AR15TFE15 in the United States, it is commonly used to manufacture high-performance mechanical parts, wear-resistant components, etc.
Classified by functional characteristics
Conductive PEI masterbatch: By adding conductive fillers, PEI masterbatch has good conductivity and can be used to produce products that require electrostatic discharge, electromagnetic shielding, and other functions, such as electronic device casings, circuit boards, etc.
Anti static PEI masterbatch: It can effectively prevent static electricity from forming on the surface of products, avoid problems such as electrostatic adsorption of dust and sparks, and is suitable for environments sensitive to static electricity, such as packaging of electronic components, clean room supplies, etc.
Flame retardant PEI masterbatch: Added flame retardant to make PEI masterbatch flame retardant, which can meet the requirements of different fields for material fire safety. It is commonly used in components with strict flame retardant performance requirements in industries such as construction, aerospace, and electronics.
Classified by processing method
Injection grade PEI masterbatch: With good fluidity and formability, it is suitable for injection molding processes and can produce various complex shaped products, such as plastic shells, components, etc. Common ones include the 2200R and 1110F of the Shaber Foundation (formerly GE) and the 2285A of the RTP in the United States.
Extrusion grade PEI masterbatch: With good melt strength and extrusion stability, it is suitable for extrusion molding processes and can be used to manufacture products such as pipes, sheets, and films.
Spinning grade PEI masterbatch: After special formulation and processing technology, it has properties suitable for spinning and can be used in the production of fibers for textile, filtration materials and other fields.
In addition, there are some special types of PEI masterbatch, such as reinforced PEI masterbatch with boron nitride nanotubes added, which can significantly improve the mechanical and thermal properties of the material, and are suitable for 3D printing to manufacture high-performance components and other fields.
Formula ratio
Easy to metalize long glass fiber reinforced PEI material for circuit boards
Components: 24.5-56.5 parts PEI resin, 20-40 parts continuous glass fiber, 5-10 parts inorganic filler masterbatch, 15-20 parts inorganic filler masterbatch, 2-3 parts compatibilizer, 1-1.5 parts antioxidant, 0.5-1 part lubricant.
Explanation: Inorganic filler masterbatch is one or a mixture of magnesium hydroxide, aluminum hydroxide, and calcium carbonate, with a particle size of 5-10 μ m; Inorganic filler masterbatch is one or a mixture of aluminum oxide, boron nitride, and silicon dioxide, with a particle size of 20-40 μ m. The compatibilizer is one or a mixture of POE-g-MAH, POE-g-GMA, and SEBS-g-MAH. The antioxidant is one or a mixture of antioxidant 1076, antioxidant 168, and antioxidant 1098. The lubricant is one or a mixture of erucamide, zinc stearate, and ethylene bistearate.
Carbon nano filled PEI masterbatch (for reference only)
Ingredients: 90-95 parts PEI resin, 5-10 parts carbon nanomaterials, 0.5-1 part antioxidant, 0.5-1 part dispersant.
Explanation: Carbon nanomaterials can be carbon nanotubes, graphene, etc. Antioxidants such as antioxidant 1010 and antioxidant 168 can be selected. Dispersants such as polyethylene wax and EBS can be used to evenly disperse carbon nanomaterials in PEI resin.
Flame retardant PEI masterbatch (for reference only)
Ingredients: 80-90 parts PEI resin, 10-20 parts flame retardant, 0.5-1 part antioxidant, 0.5-1 part lubricant.
Explanation: Flame retardants can be selected from decabromodiphenyl ether, aluminum hydroxide, magnesium hydroxide, etc. Antioxidants such as antioxidant 1076 and antioxidant 168 can be selected. Lubricants such as zinc stearate and ethylene bis stearate can be used to improve processing performance.
It should be noted that the formula ratios of different manufacturers may vary in actual production, and adjustments and optimizations will be made based on specific application requirements, product performance requirements, and production processes.
Production process
The production process of PEI masterbatch usually includes multiple steps such as raw material preparation, mixing, extrusion, granulation, etc. The following is an introduction to its general production process:
1. Raw material preparation
Resin selection: Based on product performance requirements, select the appropriate type of PEI resin particles to ensure their purity, molecular weight, and distribution meet production standards.
Additive preparation: Accurately weigh various additives according to the formula, such as reinforcing materials (glass fiber, carbon nanomaterials, etc.), flame retardants, antioxidants, lubricants, etc. The quality and amount of additives directly affect the performance of the masterbatch and need to be strictly controlled.
2. Mixing
High speed mixing: Add PEI resin and additives into a high-speed mixer for thorough mixing. By using a high-speed rotating stirring blade, the material can be uniformly dispersed in a short period of time. Generally, the stirring speed is 500-1500 revolutions per minute and the stirring time is 10-30 minutes.
Preprocessing: For some special additives or reinforcing materials, pretreatment may be necessary. For example, fiberglass needs to undergo surface coupling treatment to improve its adhesion with PEI resin; Carbon nanomaterials may require dispersion treatment to prevent agglomeration.
3. Extrusion
Feeding: Add the mixed materials into the hopper of the extruder and transport them to the heating zone of the extruder through the rotation of the screw.
Heating plasticization: The heating zone of an extruder is usually divided into multiple sections, and the material is gradually heated to a molten state at different temperatures through electric heating or other heating methods. The melting temperature of PEI resin is relatively high, generally between 300-380 ℃.
Shear mixing: Under the rotation of the screw, the material is subjected to strong shear and mixing effects, allowing the additive to fully blend with PEI resin and further disperse uniformly. The length to diameter ratio and groove depth of the screw have a significant impact on the mixing effect.
Extrusion molding: The material that has been plasticized and mixed is extruded from the head of the extruder under the push of the screw, forming a continuous strip or sheet like melt.
4. Granulation
Air cooling or water cooling: The extruded melt is cooled and shaped by air cooling or water cooling. The air cooling method uses air convection to take away heat, with a slower cooling rate but better surface quality of the product; The water cooling method is to directly immerse the melt in water, which has a fast cooling rate, but may cause water marks on the surface of the product.
Granulation: The cooled strip or sheet is cut by a granulator to produce particles of the desired size. The cutting speed and cutting method of the granulator determine the shape and size accuracy of the particles.
5. Post processing
Drying: The PEI masterbatch after granulation may contain some moisture and needs to be dried to remove moisture and prevent defects such as bubbles and silver wires during subsequent processing. The drying temperature is generally between 100-150 ℃, and the drying time is 2-4 hours.
Screening: By using vibrating screens or other screening equipment, the mother particles are screened to remove particles that are too large or too small, ensuring uniform particle size distribution of the product.
6. Packaging
Put the post processed PEI masterbatch into sealed bags or packaging bags to prevent moisture and contamination. For some products with high environmental requirements, desiccants may also need to be added to the packaging or vacuum packaging may be used.
Throughout the entire production process, it is necessary to strictly control the process parameters of each link, such as temperature, pressure, speed, time, etc., and monitor and analyze the performance of the product in real time through quality testing equipment to ensure that the quality of the PEI masterbatch produced is stable and meets the requirements.
Production equipment
The equipment for producing PEI masterbatch mainly includes the following types:
Mixing equipment
High speed mixer: used to thoroughly mix PEI resin with various additives. Its working principle is to generate strong convection and shear effects in the mixing drum through high-speed rotating stirring blades, thereby achieving uniform mixing of materials. It has the advantages of fast mixing speed and good mixing effect, and can achieve high mixing uniformity of materials in a short time.
Dual planetary mixer: suitable for occasions with high mixing requirements, especially when the additive content is low or special mixing effects are needed. It has two planetary agitator blades that revolve and rotate inside the mixing bucket, which can generate complex material flow patterns, further improving the uniformity and fineness of mixing, and effectively avoiding material agglomeration or local uneven mixing.
Extrusion equipment
Single screw extruder: The structure is relatively simple, consisting of a screw, a barrel, a heating device, a head, and a transmission system. The screw rotates inside the barrel, conveying the material from the hopper to the machine head, while gradually heating the material to a molten state through a heating device. Suitable for the production of PEI masterbatch with relatively simple product structure and low production requirements, it has the advantages of easy operation and low maintenance costs.
Twin screw extruder: With two interlocking screws, it can provide stronger conveying capacity, shear force, and mixing effect. The material is subjected to strong shear and rubbing in the meshing area between two screws, and the additive and PEI resin can be more fully mixed and dispersed, especially suitable for producing high-performance and high demand PEI masterbatch, such as masterbatch with added carbon nanomaterials, special flame retardants, etc. that require high dispersion. Its output is relatively high, and product quality can be precisely controlled by adjusting parameters such as screw speed and temperature distribution.
Granulation equipment
Air cooled die surface hot cutting granulator: After the extruded melt is extruded from the die head, it is immediately cut into particles by a rotating cutter, and the particles are cooled by an air cooling system. This granulator produces particles with regular shapes and smooth surfaces. The air cooling method can avoid the surface water mark problem that may be caused by water cooling, making it suitable for the production of PEI masterbatch with high requirements for particle appearance quality.
Underwater pelletizer: The extruded melt is directly immersed in water and pelletized underwater. Due to the good cooling effect of water and the fast cooling speed of particles, it can effectively prevent particle adhesion and achieve high production efficiency. But the equipment structure is relatively complex, requiring specialized water circulation systems and particle drying systems, suitable for large-scale production and situations with high requirements for particle cooling speed.
Drying equipment
Hot air circulation drying oven: The hot air is continuously circulated in the drying oven through a circulating fan, uniformly heating and drying the PEI masterbatch. It has the advantages of uniform drying temperature and simple operation. Different drying temperatures and times can be set according to the characteristics and drying requirements of the masterbatch.
Vacuum drying machine: Drying masterbatch in a vacuum environment can reduce the boiling point of water, accelerate the evaporation rate of water, and avoid the influence of high temperature on the performance of masterbatch. Suitable for PEI masterbatch with high drying requirements and easy oxidation or degradation at high temperatures. The dried masterbatch has lower moisture content and more stable quality.
Auxiliary equipment
Feeding machine: used to transport raw materials from storage containers to the hopper of mixing equipment or extruders, which can achieve automated feeding, improve production efficiency, and reduce manual labor intensity. Common types include screw feeders, pneumatic conveying feeders, etc.
Measuring equipment: including electronic scales, flow meters, etc., used to accurately measure the amount of various raw materials added, ensure the accuracy of the formula, and thus ensure the stability of product quality.
Testing equipment: such as melt flow rate tester, mechanical performance tester, thermal performance tester, etc., used for performance testing of raw materials, semi-finished products, and finished products in the production process, timely discovering problems and adjusting production processes to ensure that products meet quality standards.
PEI masterbatch extruder
Kerke’s masterbatch extruder can be used to produce PEI masterbatch. Our PEI masterbatch extruder has multiple models to choose from, which can meet different production requirements.
-
Laboratory Twin Screw Extruder
When will you need a lab twin screw extruder? If you want to make trials and tests of…
-
Parallel Twin Screw Extruder
Our Parallel Co-rotating twin screw extruder is designed for compounding and masterbatch making with an output capacity from…
-
Triple (3 screws) Extruder
3 Screws extruder is a new technology that has many advantages. The triple screw extruder is mainly used…
-
Double-Stage Extrusion System
Mother-baby extrusion system is designed for special materials which can not process on one stage extruder, the first…
-
Banbury Kneader Compounding Line
Our kneader + extruder is designed for making special applications with an output capacity from 30kg/h to 1000kg/h.…
-
Cutting System / Pelletizing System
Different material needs different cutting system, Kerke provides all kinds of cutting system, here is the explanation of…
Related requirements
The extruder is one of the key equipment for producing PEI masterbatch. Due to the characteristics of PEI resin and production process requirements, the extruder has the following requirements:
Temperature control
High temperature capability: The melting temperature of PEI resin is relatively high, generally between 300-380 ℃, so the extruder needs to have the heating ability to reach and maintain this high temperature range stably. Efficient electric heating elements or other heating methods, such as thermal oil heating, are usually used to ensure that each section of the material barrel can be uniformly heated to the desired temperature.
Temperature uniformity: In order to ensure good plasticization of PEI resin and uniform dispersion of additives, the axial and radial temperatures of the extruder barrel need to be highly uniform. This requires the heating system to have precise temperature control devices that can adjust in real-time based on temperature feedback from different locations, while also ensuring good insulation performance of the material cylinder to reduce heat loss.
Quick response: During the production process, it may be necessary to quickly adjust the temperature according to different production situations or product requirements. For example, when changing product specifications or raw material batches, it is necessary to adjust the temperature in a timely manner to adapt to the new process parameters. Therefore, the temperature control system of the extruder should have fast response capability and be able to achieve precise temperature adjustment in a short period of time.
Screw design
High torque: PEI resin melt has a high viscosity and requires a large torque to push the material forward during extrusion. Therefore, the screw of the extruder needs to have sufficient strength and rigidity to withstand high torque loads, and the driving system should also provide corresponding high torque output to ensure stable rotation of the screw and smooth extrusion of materials.
Special thread structure: In order to achieve good mixing and dispersion effects, the thread structure of the screw usually requires special design. For example, using a gradient screw, the depth of the screw groove gradually becomes shallower from the feeding section to the homogenization section, which can enhance the shear and compression effects on the material during extrusion, which is beneficial for the plasticization of PEI resin and the uniform dispersion of additives; Alternatively, a mixing section can be installed on the screw, such as using pin screws, barrier screws, and other structures, to further improve the mixing effect of the material.
Length to diameter ratio: A longer length to diameter ratio is beneficial for the full plasticization, mixing, and homogenization of materials inside the screw. For the production of PEI masterbatch, it is generally required that the aspect ratio of the screw be between 25-40. A longer aspect ratio can provide more residence time and shear action, allowing additives to mix and react more thoroughly with PEI resin, thereby improving the quality and performance of the masterbatch.
Material selection
Wear resistance: Due to the strong wear effect of PEI resin and its additives on the screw and inner wall of the barrel during extrusion, especially when reinforced materials such as fiberglass and carbon nanomaterials are added, the wear is more severe. Therefore, screws and barrels are usually made of alloy steel materials with good wear resistance, such as 38CrMoAlA steel, and undergo nitriding treatment or hard chromium plating treatment to improve surface hardness and wear resistance, and extend the service life of the equipment.
Corrosion resistance: Some additives may have certain corrosiveness, such as flame retardants, lubricants, etc. In order to prevent equipment from being corroded, affecting product quality and equipment performance, the contact parts of the extruder need to have good corrosion resistance. Stainless steel material or corrosion-resistant coatings such as Teflon coating can be chosen on the metal surface to protect the equipment from corrosion damage.
Accuracy
Accurate feeding: The feeding system of the extruder needs to have high-precision metering capability to ensure accurate addition of various raw materials according to the formula. Whether using a weight loss feeder or a volumetric feeder, the feeding amount of raw materials should be accurately controlled, and the measurement accuracy is generally required to be within ± 1% to ensure the stability and consistency of the quality of the masterbatch products.
Melt measurement: During the extrusion process, it is necessary to accurately measure and control the flow rate of the melt to ensure uniform quality and stable size of the extruded masterbatch. Usually, equipment such as melt pumps are used to accurately measure and control the melt flow rate. By adjusting the speed of the melt pump, the extrusion amount can be precisely controlled, and the measurement accuracy can reach within ± 0.5%.
Automated control
Process parameter monitoring: The extruder should be equipped with a comprehensive automation control system that can monitor and display various process parameters in real time, such as temperature, pressure, screw speed, melt flow rate, etc. Operators can intuitively understand the changes in various parameters during the production process through the control system and make adjustments as needed to ensure the stability of the production process and product quality.
Fault diagnosis and alarm: The automation control system should have fault diagnosis function, which can timely detect abnormal situations during equipment operation, such as high temperature, abnormal pressure, motor overload, etc., and issue alarm signals. At the same time, the system should also be able to automatically record fault information, helping maintenance personnel quickly locate and troubleshoot faults, reducing equipment downtime, and improving production efficiency.
Remote control and data management: In order to achieve intelligent management of the production process, modern extruders usually also support remote control and data management functions. Through network connection, operators can remotely operate and monitor the extruder, achieving centralized management of the production process. At the same time, the system can also store, analyze, and statistically analyze production data, providing a basis for production optimization and quality improvement.
Application
PEI masterbatch has various excellent properties, such as high temperature stability, high mechanical strength, good flame retardancy, and excellent electrical insulation. Therefore, it has a wide range of applications in multiple fields. The following are some of the main application areas:
Electronic and electrical field
Connector: PEI masterbatch has good electrical insulation performance, high temperature stability, and mechanical strength, which can meet the requirements of electronic connectors in various complex environments, ensuring the stability and reliability of signal transmission.
Socket and switch: Its high flame retardancy makes PEI masterbatch an ideal material for manufacturing electrical components such as sockets and switches, which can effectively prevent fire accidents. At the same time, its good mechanical properties can ensure the service life of the product.
Coil skeleton: PEI masterbatch can maintain good shape and performance in high temperature environments, withstand the heat generated by the coil during operation, and ensure the normal operation of electronic devices.
Automotive industry field
Engine peripheral components: such as engine hood, intake pipe, radiator grille, etc. PEI masterbatch can withstand the high temperature environment inside the engine compartment, while also having good chemical corrosion resistance and mechanical properties, which can reduce the weight of cars and improve fuel economy.
Automotive electrical system: used to manufacture electrical connectors, fuse boxes, and other components for automobiles. The electrical insulation and flame retardant properties of PEI masterbatch can ensure the safe and reliable operation of automotive electrical systems, reducing the risk of electrical failures.
Aerospace field
Aircraft interior parts: such as seat armrests, luggage racks, cabin decorative panels, etc. PEI masterbatch has excellent flame retardant properties, lightweight characteristics, and good mechanical properties, which can meet the strict requirements of materials in the aerospace industry and improve flight safety and comfort.
Aircraft engine components: Some non critical structural and auxiliary components that can be used to manufacture engines, such as fan covers, guide vanes, etc. The stability and good mechanical properties of PEI masterbatch at high temperatures enable it to withstand the high temperature and high pressure environment during engine operation.
Medical field
Medical devices: such as surgical instrument handles, medical syringes, infusion sets, etc. PEI masterbatch has good biocompatibility, chemical corrosion resistance, and high strength, which can meet the requirements of medical device use. At the same time, it is easy to process and shape, and can be made into various complex shaped medical device components.
Medical equipment casing: PEI masterbatch has good appearance quality and weather resistance, which can protect the electronic components and mechanical parts inside medical equipment. At the same time, its flame retardant performance also improves the safety of medical equipment during use.
Other areas
In the field of optics, PEI masterbatch has excellent optical properties and can be used to manufacture optical components such as optical lenses and fiber connectors, meeting the high-precision requirements of materials in the optical field.
In the industrial field, it can be used to manufacture various industrial components such as gears, bearings, seals, etc. The high strength, wear resistance, and chemical corrosion resistance of PEI masterbatch enable it to work stably for a long time in harsh industrial environments.