MDPE masterbatch is composed of excess chemical additives, carrier resins (such as MDPE), and dispersants. It usually contains components such as flame retardants, resins, and additives to endow plastic products with specific properties. MDPE masterbatch is widely used in injection molding, extrusion, blown film, drawing, foaming, coating and other process products. For example, it can be used to manufacture pipes, films, hollow containers, etc. It is also commonly used for high-speed molding of various bottles, high-speed automatic packaging films, various injection molded products, rotary molded products, wire and cable cladding, waterproof materials, water pipes, gas pipes, etc.
Types
MDPE (medium density polyethylene) masterbatch can be classified into the following types based on their functions and uses:
Ordinary MDPE masterbatch: It has the general characteristics of medium density polyethylene, such as good flexibility, low temperature resistance, and chemical stability. Mainly used for producing various plastic products, such as films, pipes, injection molded products, etc., to meet basic usage requirements.
Filling masterbatch: A large amount of fillers such as calcium carbonate, talc powder, etc. are added to MDPE masterbatch. The main function of filling masterbatch is to reduce production costs, while also improving certain properties of the product, such as increasing hardness, rigidity, and dimensional stability. Commonly used in the production of cost sensitive plastic products, such as garbage bags, shopping bags, plastic buckets, etc.
Flame retardant masterbatch: made by adding flame retardants, MDPE has good flame retardant properties. Flame retardant masterbatch can be used to produce various plastic products that require fire safety performance, such as wire and cable sheaths, building plastic sheets, electrical enclosures, etc., to improve the fire rating of these products and reduce fire hazards.
Anti aging masterbatch: additives such as antioxidant and ultraviolet absorber are added to improve the anti-aging performance of MDPE products, making them not prone to degradation, discoloration and embrittlement under long-term exposure to sunlight, oxygen, high temperature and other environmental conditions. Commonly used for producing plastic products for outdoor use, such as agricultural films, shade nets, plastic pipes, etc., to extend their service life.
Toughened masterbatch: Adding toughening agents can significantly improve the toughness and impact resistance of MDPE. Toughened masterbatch is suitable for producing plastic products that require high toughness, such as turnover boxes, plastic pallets, automotive parts, etc., so that they are not easily broken when subjected to external impact.
Conductive masterbatch: Conductive materials such as carbon black and metal fibers are added to endow MDPE masterbatch with conductivity. Conductive masterbatch is mainly used in the production of plastic products with anti-static or conductive functions, such as electronic equipment packaging materials, anti-static pipes, wire and cable shielding layers, etc., to prevent the hazards caused by static electricity accumulation or meet specific electrical performance requirements.
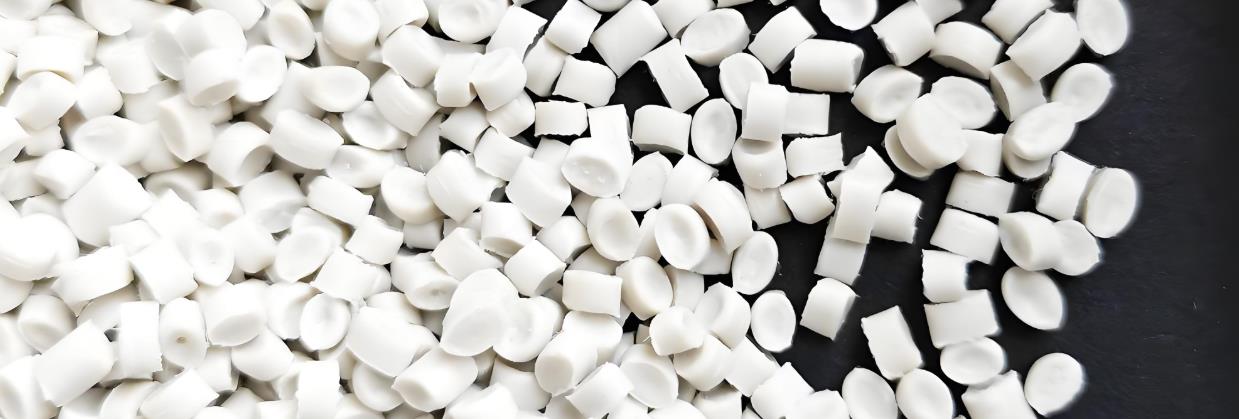
Formula ratio
The following are the approximate formula ratios for different types of MDPE masterbatch. In actual production, adjustments will be made based on specific product requirements, production processes, and raw material characteristics
Ordinary MDPE masterbatch: MDPE resin usually accounts for 90% -100%, and a small amount of antioxidants, lubricants, and other additives may be added as needed, usually around 0% -10%. For example, in order to improve processing performance and product aging resistance, 0.1% -1% antioxidants and 0.5% -2% lubricants may be added.
Filling masterbatch: Fillers such as calcium carbonate and talc powder have a high content, usually accounting for 50% -80% of the masterbatch’s mass. MDPE resin is used as a carrier, accounting for 20% -50%. In addition, a small amount of coupling agents, dispersants and other additives will be added to improve the compatibility and dispersibility of fillers and resins, generally around 0.5% -3%. For example, in calcium carbonate filled masterbatch, the calcium carbonate content may be 60%, MDPE resin may be 38%, and coupling agents and dispersants together account for 2%.
Flame retardant masterbatch: Flame retardant is a key component, with a content usually between 20% and 60%. MDPE resin accounts for 40% -80%. According to the type and performance requirements of flame retardants, some synergists may be added, such as antimony trioxide, with a content of about 1% -10%. For example, an MDPE flame retardant masterbatch containing a bromine based flame retardant, with a flame retardant content of 40%, MDPE resin of 55%, and antimony trioxide synergist of 5%.
Anti aging masterbatch: anti-aging additives such as antioxidants and UV absorbers are the main components, generally accounting for 5% -20% of the masterbatch mass. MDPE resin accounts for 80% -95%. In order to improve the dispersibility and stability of the additive, a small amount of dispersant may be added, usually around 0.5% -2%. For example, the total content of antioxidant 1010 and UV absorber UV-531 is 10%, MDPE resin is 90%, and dispersant is 0.5%.
Toughening masterbatch: The toughening agent content is generally between 10% -50%, and MDPE resin accounts for 50% -90%. In order to improve the compatibility between toughening agents and MDPE, some compatibilizers may be added, with a content of about 1% -5%. For example, the content of POE toughening agent is 30%, MDPE resin is 68%, and compatibilizer is 2%.
Conductive masterbatch: The content of conductive materials such as conductive carbon black, metal fibers, etc. is about 10% -50%, and MDPE resin accounts for 50% -90%. In order to improve the dispersibility and conductivity of conductive materials, some dispersants and surface treatment agents may be added, usually around 0.5% -5%. For example, the conductive carbon black content is 20%, MDPE resin is 78%, and the dispersant and surface treatment agent together account for 2%.
Production process
The production process of MDPE masterbatch generally includes steps such as raw material preparation, mixing, melt extrusion, cooling granulation, packaging, etc. The following is a specific introduction:
1. Raw material preparation
Accurately select MDPE resin and various additives based on the type of masterbatch, such as preparing fillers such as calcium carbonate and talc powder for the production of filling masterbatch, and preparing flame retardants for the production of flame retardant masterbatch. Ensure that the quality and performance of raw materials meet production requirements, and dry the raw materials, especially for MDPE resins and certain additives that are prone to moisture absorption, to remove moisture and prevent the formation of bubbles or affect product quality during processing.
2. Mixing
Add MDPE resin and additives into the high-speed mixer according to the designed formula ratio. It is crucial to ensure the consistency of the properties of the masterbatch by thoroughly mixing the materials at high speed to ensure even distribution of additives in MDPE resin. Some masterbatch production may require the addition of auxiliary agents such as coupling agents, dispersants, etc., which are also added and mixed evenly at this stage.
3. Melt extrusion
The mixed material enters the extruder barrel and is gradually heated to a molten state by the heating of the extruder and the rotation of the screw. The temperature setting of the extruder needs to be adjusted according to the characteristics of MDPE resin and additives. Generally, the temperature in the front section of the barrel is lower and the temperature in the back section is higher to ensure that the material is fully melted and does not undergo overheating decomposition. During the melting process, the rotational speed and shear force of the screw can also affect the mixing effect and plasticization quality of the material, which needs to be optimized according to the actual situation.
4. Cooling granulation
The molten material extruded from the extruder is formed into specific shaped strips or filaments through a mold, and then enters a cooling water tank or is cooled and solidified by air cooling. The cooled material is cut into uniform particles by a granulator, and the size and shape of the particles can be controlled by adjusting the parameters of the granulator. For some masterbatch with special requirements, surface treatment or lubricant addition may be necessary to improve the flowability and surface properties of the particles.
5. Packaging
The MDPE masterbatch after granulation is usually packaged in plastic woven bags or composite packaging bags to prevent moisture and contamination of the masterbatch. Label the product name, specifications, production date, shelf life, and other information on the packaging for storage, transportation, and use.
There may be slight differences in the production process of different types of MDPE masterbatch. For example, in the production of conductive masterbatch, in order to ensure the stability of conductivity, special dispersion processes may be required during the mixing process, or special control of the distribution of conductive materials may be required during the extrusion process. When producing anti-aging masterbatch, attention should be paid to the addition method and mixing uniformity of anti-aging additives to ensure that they can play the best anti-aging effect in MDPE resin.
Production equipment
In the production process of MDPE masterbatch, different production stages require the use of different equipment. The following are the main production equipment and their functions:
1. Ingredient equipment
Electronic scale: used to accurately weigh the weight of MDPE resin, various additives and other raw materials, ensuring accurate ingredients according to the formula to ensure the stability of product quality.
High speed mixer: Mix the weighed raw materials thoroughly and evenly, and use high-speed rotating stirring blades to achieve good mixing effect between MDPE resin and additives in a short period of time, laying the foundation for subsequent processing.
2. Extrusion equipment
Single screw extruder or twin-screw extruder: The single screw extruder has a simple structure and low cost, and is suitable for the production of ordinary MDPE masterbatch with low mixing requirements. The twin-screw extruder has better mixing performance, self-cleaning ability, and conveying ability, which can more evenly disperse additives and is suitable for producing high-performance and high demand MDPE masterbatch, such as flame retardant masterbatch, conductive masterbatch, etc. The extruder gradually melts the raw materials in the barrel through heating and rotation of the screw, and extrudes them into continuous strip or filamentous materials.
Extrusion mold: Installed at the discharge port of the extruder, it determines the shape and size of the extruded material. According to production needs, different types of molds can be selected, such as circular, flat, etc., to meet the requirements of subsequent granulation.
3. Cooling equipment
Cooling water tank: used for water-cooled cooling of extruded hot materials to quickly solidify and shape them. The parameters such as water temperature and flow rate in the sink need to be adjusted according to the characteristics of the material and production speed to ensure uniform and consistent cooling effect.
Air cooling system: For situations where water cooling is not suitable or rapid surface drying is required, an air cooling system will be used. Blow cold air towards the extruded material through a fan, allowing it to cool naturally in the air. Air cooling systems usually include components such as fans and air ducts, which can be arranged reasonably according to production site and process requirements.
4. Granulation equipment
Granulator: Cut the cooled material into uniform granules. There are two common types of pelletizers: hot pelletizers and cold pelletizers. Hot cutting machine is used to cut materials in a thermoplastic state, with a fast cutting speed, but requires subsequent drying treatment of the cut particles; The cold granulator cuts the material after it has completely cooled, resulting in better particle quality but relatively lower production efficiency.
5. Packaging equipment
Automatic packaging machine: used for quantitatively packaging MDPE masterbatch after granulation. Automatic packaging machines can achieve functions such as automatic measurement, filling, and sealing of materials, improve packaging efficiency and quality, and reduce manual operation errors. According to packaging specifications and material characteristics, different types of automatic packaging machines can be selected, such as granule packaging machines, powder packaging machines, etc.
Sealing machine: Seal the packaged products to ensure good sealing of the packaging bag and prevent moisture and contamination of the masterbatch. There are various sealing methods for sealing machines, such as heat sealing, pressure sealing, etc., which can be selected according to the material and requirements of the packaging bag.
In addition to the main equipment mentioned above, some auxiliary equipment may also be required during the production process, such as raw material drying equipment, conveying equipment, storage equipment, etc., to ensure the smooth progress of the entire production process.
MDPE masterbatch extruder
Kerke’s masterbatch extruder can be used to produce MDPE masterbatch. Our MDPE masterbatch extruder has multiple models to choose from, which can meet different production requirements.
-
Laboratory Twin Screw Extruder
When will you need a lab twin screw extruder? If you want to make trials and tests of…
-
Parallel Twin Screw Extruder
Our Parallel Co-rotating twin screw extruder is designed for compounding and masterbatch making with an output capacity from…
-
Triple (3 screws) Extruder
3 Screws extruder is a new technology that has many advantages. The triple screw extruder is mainly used…
-
Double-Stage Extrusion System
Mother-baby extrusion system is designed for special materials which can not process on one stage extruder, the first…
-
Banbury Kneader Compounding Line
Our kneader + extruder is designed for making special applications with an output capacity from 30kg/h to 1000kg/h.…
-
Cutting System / Pelletizing System
Different material needs different cutting system, Kerke provides all kinds of cutting system, here is the explanation of…
Related requirements
The extruder is crucial in the production of MDPE masterbatch, and the following are the requirements for its performance, quality, control system, and other aspects:
Performance Requirement
Plasticization ability: It is necessary to have good plasticization performance, which can enable MDPE resin and various additives to melt and plasticize quickly and uniformly at a certain temperature and pressure, ensuring good flowability of materials and meeting the production needs of different formula masterbatch. For example, for filling masterbatch, a large amount of filler needs to be thoroughly mixed and plasticized with MDPE resin.
Mixing performance: It should have efficient mixing ability. Through the structural design and rotation of the screw, MDPE resin and additives should be fully mixed during the melting process, ensuring that the additives are evenly dispersed in the resin to obtain stable performance masterbatch products. When producing conductive masterbatch, it is necessary to evenly distribute the conductive material in MDPE resin.
Extrusion stability: able to maintain stable extrusion volume and pressure during long-term operation, ensuring consistency in product quality. This requires the screw, barrel, and other components of the extruder to have good wear resistance and rigidity to withstand high pressure and shear forces.
Quality requirement
Material selection: The barrel and screw are usually made of high-strength, corrosion-resistant alloy steel, such as 38CrMoAlA nitride steel, to resist the wear and corrosion of MDPE resin and additives under high temperature and pressure, and extend the service life of the equipment.
Processing accuracy: The processing accuracy of screws and barrels should be high, and the errors of parameters such as screw diameter, pitch, and thread shape should be controlled within a very small range to ensure the uniformity and stability of material flow in the barrel and improve extrusion quality.
Control system requirements
Temperature control: Equipped with a precise temperature control system, it can independently adjust and control the temperature of each section of the material barrel and the machine head, ensuring that the material is in a suitable temperature environment at different stages, avoiding problems such as material decomposition and poor plasticization caused by high or low temperature. The general temperature control accuracy needs to be within ± 1 ℃.
Speed control: The speed of the screw should be precisely adjustable, providing appropriate shear force and conveying speed according to different material characteristics and production process requirements to achieve the best plasticization and mixing effect. The speed control range is usually between 0-600rpm and can be adjusted in small increments.
Pressure control: equipped with pressure monitoring and control devices, real-time monitoring of pressure changes during the extrusion process, and by adjusting parameters such as screw speed and barrel temperature, the extrusion pressure is maintained within the set range, ensuring the dimensional accuracy and appearance quality of the product.
Application
MDPE (medium density polyethylene) masterbatch has good flexibility, corrosion resistance, and environmental stress cracking resistance, and is therefore widely used in multiple fields. The following are some of the main application aspects:
Plastic film
Agricultural film: MDPE masterbatch can be used to produce agricultural films, such as greenhouse films, mulching films, etc. It can endow the film with good transparency, thermal insulation, and weather resistance, which is helpful for the growth and development of crops, and can improve crop yield and quality. At the same time, the film produced by MDPE masterbatch also has certain strength and toughness, which can resist the erosion of natural environments such as wind, sun, and rain.
Packaging film: In the field of packaging, MDPE masterbatch is widely used in the production of various packaging films, such as food packaging film, daily necessities packaging film, etc. It can make the film have good flexibility, transparency, and heat sealing properties, which can effectively protect packaging items and facilitate consumer use. In addition, MDPE masterbatch can also be blended or compounded with other materials to produce packaging films with special properties, such as barrier films, puncture resistant films, etc.
Pipe
Water supply pipes: MDPE masterbatch is one of the important raw materials for producing water supply pipes. The water supply pipe made of MDPE masterbatch has the advantages of corrosion resistance, wear resistance, high pressure resistance, hygiene and non toxicity, which can ensure the safety and stability of water quality. It is widely used in urban water supply, rural drinking water safety engineering and other fields.
Drainage pipes: In drainage engineering, MDPE masterbatch produced pipes have good flexibility and impact resistance, which can adapt to different geological conditions and terrain changes, and are not easily broken or leaked. Meanwhile, MDPE drainage pipes also have the characteristics of light weight, easy installation, and long service life, which can reduce construction and maintenance costs.
Injection molding products
Plastic containers: MDPE masterbatch can be used to produce various plastic containers, such as plastic buckets, plastic pots, plastic boxes, etc. It can make plastic containers have good rigidity, toughness, and chemical corrosion resistance, able to withstand certain pressure and weight, while also having good appearance quality and processing performance.
Industrial parts: In the industrial field, injection molded products made from MDPE masterbatch can also be used to manufacture various industrial parts, such as automotive components, electronic and electrical components, etc. MDPE masterbatch has good insulation performance, wear resistance, and aging resistance, which can meet the requirements of industrial parts and improve the reliability and service life of products.
Wire and cable
Insulation layer: MDPE masterbatch has good insulation performance and low temperature resistance, and can be used for producing insulation layers for wires and cables. It can effectively prevent current leakage and short circuit, ensuring the safe operation of wires and cables. At the same time, MDPE insulation layer also has certain flexibility and wear resistance, which can adapt to different usage environments and installation requirements.
Sheath: MDPE masterbatch can also be used to produce sheaths for wires and cables. Sheath can protect the internal structure of wires and cables from external environmental factors such as moisture, dust, ultraviolet radiation, etc. MDPE sheath has good weather resistance, corrosion resistance, and mechanical strength, which can extend the service life of wires and cables.