POM masterbatch is a masterbatch made from polyoxymethylene (POM) as the base material. Polyoxymethylene is a highly crystalline thermoplastic engineering plastic, known as “super steel” or “Sai steel”, widely used in multiple fields due to its excellent mechanical properties.
Types
POM (polyoxymethylene) masterbatch can be classified into the following types based on its function and characteristics:
Universal POM masterbatch
This is the most common type of POM masterbatch, which has the basic properties of POM resin, such as high hardness, high rigidity, good wear resistance, fatigue resistance, and excellent dimensional stability.
Suitable for general industrial products that do not have particularly demanding material performance requirements, such as ordinary mechanical parts, gears, bearings, toys, stationery, etc.
Enhanced POM masterbatch
Made by adding reinforcing materials such as glass fiber and carbon fiber to POM resin. After adding glass fiber, the mechanical strength, rigidity, and heat resistance of POM can be significantly improved, enabling it to withstand higher loads and working temperatures.
Commonly used in manufacturing automotive components, such as various parts under the hood, car door locks, seat adjustment mechanisms, etc; In the field of electronic appliances, it can be used to manufacture components such as connectors, sockets, switches, etc. that require high strength and heat resistance.
Toughened POM masterbatch
To improve the toughness and impact resistance of POM, various toughening agents such as rubber elastomers and thermoplastic elastomers have been added to POM masterbatch. The toughened POM masterbatch has better impact resistance and cracking resistance while maintaining a certain degree of rigidity.
Suitable for occasions that are prone to impact or require a certain degree of flexibility, such as sports equipment, tool handles, household appliance casings, etc.
Wear resistant POM masterbatch
Solid lubricants or wear-resistant additives such as molybdenum disulfide, graphite, and polytetrafluoroethylene (PTFE) were added to POM masterbatch, further improving the wear resistance and self-lubricating properties of POM.
Commonly used in manufacturing components that require long-term frictional motion, such as guides, sliders, chains, gears, etc., it can reduce the coefficient of friction, minimize wear, and improve the service life and operational efficiency of the components.
Conductive POM masterbatch
By adding conductive materials such as carbon black, carbon fiber, and metal fiber, POM masterbatch can have good conductivity or anti-static properties.
Mainly used in fields with high requirements for electrostatic protection such as electronics, semiconductors, and chemicals, it can be used to manufacture electronic equipment casings, trays, turnover boxes, etc., to prevent static electricity accumulation from causing damage to electronic components.
Flame retardant POM masterbatch
By adding flame retardants such as bromine, phosphorus, and nitrogen, POM masterbatch has excellent flame retardant properties and can meet different fire safety standards.
Commonly used in fields with high fire safety requirements such as electronic appliances, construction, and automobiles, such as insulation layers for wires and cables, electrical enclosures, and automotive interior parts, to improve product safety.
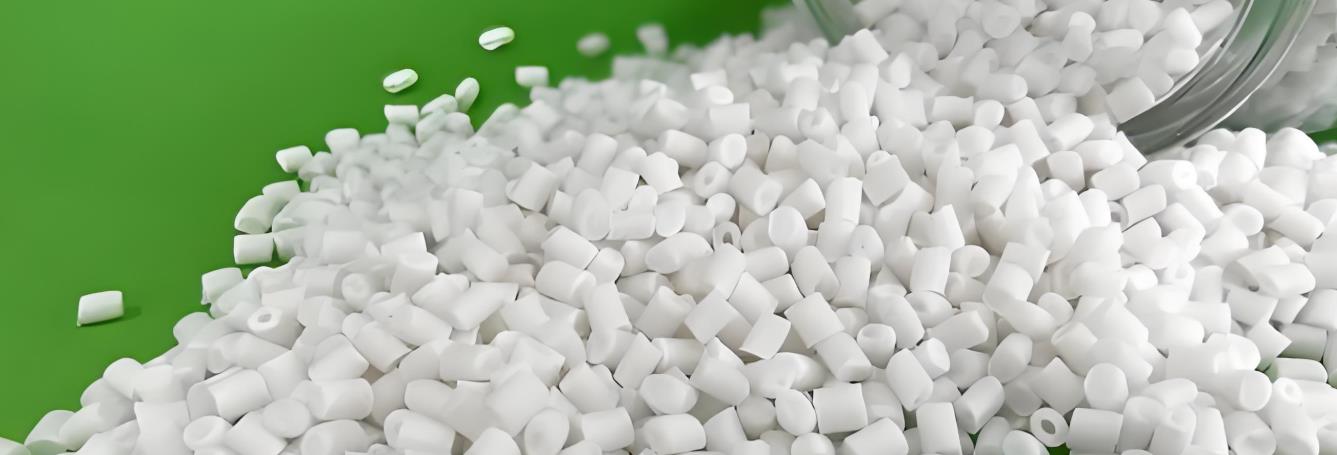
Formula ratio
The formula ratio of POM masterbatch may vary depending on different types and performance requirements. The following are approximate formula ratios for some common types of POM masterbatch:
Reinforced POM masterbatch: Typically, POM resin accounts for 70% -90%, while reinforcing materials such as glass fiber or carbon fiber account for 10% -30%. For example, in some reinforced POM masterbatch used in automotive components, POM resin may account for 80% and glass fiber for 20% to achieve high mechanical strength and rigidity.
Toughened POM masterbatch: Generally, POM resin accounts for 75% -95%, and toughening agents such as rubber elastomers and thermoplastic elastomers account for 5% -25%. For toughening POM masterbatch used in sports equipment, POM resin may be used at 90% and thermoplastic elastomer at 10% to improve impact resistance and flexibility.
Wear resistant POM masterbatch: POM resin typically accounts for 85% -98%, while solid lubricants or wear-resistant additives such as molybdenum disulfide, graphite, and polytetrafluoroethylene (PTFE) account for 2% -15%. For example, in the production of wear-resistant POM masterbatch for guide rails and sliders, POM resin is 92% and polytetrafluoroethylene is 8%, which can reduce the friction coefficient and improve wear resistance.
Conductive POM masterbatch: POM resin accounts for 80% -95%, while conductive materials such as carbon black, carbon fiber, and metal fiber account for 5% -20%. In the conductive POM masterbatch used for electronic device casings, POM resin may account for 90% and conductive carbon black for 10% to achieve good conductivity or anti-static performance.
Flame retardant POM masterbatch: POM resin accounts for 80% -95%, and bromine, phosphorus, nitrogen and other flame retardants account for 5% -20%. For some flame-retardant POM masterbatch used in buildings, POM resin may be used at 85% and phosphorus based flame retardants at 15% to meet fire safety standards.
The above formula ratios are for reference only. In actual production, adjustments and optimizations need to be made based on specific product requirements, production processes, and costs.
Production process
The production process of POM masterbatch generally includes the following main steps:
Raw material preparation
POM resin: Select the appropriate model of POM resin based on product performance requirements, check its quality indicators such as molecular weight, melt flow rate, moisture content, etc., to ensure compliance with production requirements.
Additives: Accurately weigh various additives according to the formula, such as reinforcing materials (glass fiber, carbon fiber, etc.), toughening agents, wear-resistant additives, conductive materials, flame retardants, etc. For some additives that require special treatment, such as glass fiber, surface treatment is necessary to improve compatibility and adhesion with POM resin.
Mix
Add POM resin and additives to the high-speed mixer for thorough mixing. During the mixing process, it is necessary to control the mixing time, speed, and temperature to ensure that the additives are evenly dispersed in the POM resin. For some difficult to disperse additives, pre dispersion or batch addition can be used to improve the mixing effect.
Extrusion granulation
Heating plasticization: Add the mixed material into the hopper of the twin-screw extruder, and the material is gradually heated and plasticized inside the extruder barrel. The temperature of each section of the extruder needs to be accurately set according to the characteristics of POM resin and product requirements. Generally, the temperature gradually increases from the feeding section to the head to ensure that the material is fully plasticized.
Screw extrusion: Under the rotation and pushing of the screw, the plasticized material moves forward in the screw barrel and is subjected to the shearing and squeezing effects of the screw, further uniformly mixing and dispersing the additive and POM resin. Meanwhile, the rotational speed of the screw also affects the extrusion speed and mixing effect of the material, and needs to be adjusted according to the actual situation.
Head forming: When material is extruded from the extruder head, it is formed into continuous strips or granules through a specific head mold. The design and size of the mold should be selected according to the specifications of the product to ensure that the shape and size of the extruded masterbatch meet the standards.
Cooling granulation: The extruded strip material is cooled and shaped by a water tank or air cooling device, and then cut into particles of a certain length by a granulator to obtain POM masterbatch. The cutting tools of the granulator should be kept sharp to ensure the quality of the granules and avoid uneven particle size or uneven cutting edges.
Dry
Due to the moisture absorption of POM resin, which can affect the performance and processing quality of POM masterbatch, it is necessary to dry the granulated POM masterbatch. Generally, hot air drying or vacuum drying is used to reduce the moisture content in the masterbatch to a specified range, usually requiring a moisture content of less than 0.1%.
Package
The dried POM masterbatch is usually packaged in plastic woven bags or sealed plastic bags to prevent moisture absorption, contamination, or impurities during storage and transportation. For products with high quality requirements, desiccants can be added to the packaging to further ensure product quality.
Throughout the entire production process, it is necessary to strictly control various process parameters such as temperature, pressure, speed, mixing time, etc., and regularly conduct quality inspections on the products, including appearance, particle size, melt flow rate, mechanical properties, electrical properties, flame retardant properties, and other indicators, to ensure that the produced POM masterbatch meets quality standards and customer requirements.
Production equipment
The POM masterbatch production equipment mainly includes the following types:
1. High speed mixer: used to thoroughly mix POM resin with various additives. By using high-speed rotating stirring blades, the material can achieve uniform mixing in a short period of time. It has the characteristics of high mixing efficiency and good mixing uniformity, and can adjust the mixing time and speed according to different formulas and production needs.
2. Twin screw extruder: It is the core equipment for POM masterbatch production. It consists of two interlocking screws and has multiple functions such as conveying, mixing, plasticizing, extrusion, etc. Under the action of the screw, the material is gradually heated, plasticized, and mixed evenly through different areas such as the feeding section, compression section, and homogenization section, and extruded from the machine head. The twin-screw extruder has strong shear force and conveying capacity, which can ensure sufficient mixing and stable extrusion of materials, and is suitable for processing high viscosity and difficult to mix materials.
3. Cooling water tank or air cooling device: used for cooling and shaping the extruded strip-shaped POM masterbatch. Cooling water tanks usually use circulating water for cooling, which can quickly reduce the temperature of the masterbatch, allowing it to solidify and form quickly, ensuring the shape and dimensional accuracy of the masterbatch. The air cooling device uses the cold air blown out by the fan to cool the masterbatch, which is suitable for the production of POM masterbatch that is sensitive to moisture and can avoid the influence of moisture on the performance of the masterbatch.
4. Granulator: Cut the cooled strip-shaped POM masterbatch into particles of a certain length. There are two common types of pelletizers: hot cutting and cold cutting. The hot cutting granulator is used to cut materials in a thermoplastic state, with fast cutting speed and regular particle shape, but requires specialized heating and cooling systems; The cold cutting granulator is used for cutting after the material has completely cooled down, with good cutting quality and suitable for cutting various shapes and sizes of masterbatch. It is widely used.
5. Drying equipment: such as hot air dryer or vacuum dryer, used to remove moisture from POM masterbatch. The hot air dryer heats and dries the masterbatch by circulating hot air, which is easy to operate and has high drying efficiency; A vacuum dryer is used to dry POM masterbatch in a vacuum environment, which can quickly remove moisture at lower temperatures and avoid oxidation or degradation of POM masterbatch during the drying process. It is suitable for occasions with high requirements for drying quality.
6. Packaging equipment: including automatic packaging machines, sealing machines, etc., used to package dried POM masterbatch. The automatic packaging machine can automatically measure and package according to the set weight or quantity, improving packaging efficiency and accuracy; The sealing machine is used to seal the packaged bags to prevent moisture absorption, dampness, or contamination of the masterbatch during storage and transportation.
7. Testing equipment: including melt flow rate meter, electronic universal testing machine, impact testing machine, thermogravimetric analyzer, differential scanning calorimeter, particle size analyzer, electrical performance tester, flame retardant performance tester, etc. These devices are used to detect and analyze various performance indicators of POM masterbatch to ensure product quality meets standards and customer requirements.
8. Feeding equipment: such as screw feeders, pneumatic conveying devices, etc., used to transport POM resin and additives from storage containers to the hopper of high-speed mixers or twin-screw extruders. The feeding equipment can achieve automated feeding, improve production efficiency, reduce manual labor intensity, and ensure the stability and accuracy of material transportation.
POM masterbatch extruder
Kerke’s masterbatch extruder can be used to produce POM masterbatch. Our POM masterbatch extruder has multiple models to choose from, which can meet different production requirements.
-
Лабораторный двухшнековый экструдер
When will you need a lab twin screw extruder? If you want to make trials and tests of…
-
Параллельный двухшнековый экструдер
Our Parallel Co-rotating twin screw extruder is designed for compounding and masterbatch making with an output capacity from…
-
Тройной (3 винта) Экструдер
3 Screws extruder is a new technology that has many advantages. The triple screw extruder is mainly used…
-
Двухступенчатая система экструзии
Mother-baby extrusion system is designed for special materials which can not process on one stage extruder, the first…
-
Линия для замешивания компаундов Banbury Kneader
Our kneader + extruder is designed for making special applications with an output capacity from 30kg/h to 1000kg/h.…
-
Система резки / Система гранулирования
Different material needs different cutting system, Kerke provides all kinds of cutting system, here is the explanation of…
Related requirements
The extruder plays a key role in the production of POM masterbatch, and the following are some requirements for the extruder:
Plasticizing capacity
POM resin has a high melting point, and its melt viscosity is sensitive to temperature and shear rate. Therefore, extruders need to have sufficient plasticizing ability to heat POM resin to the appropriate processing temperature and fully plasticize it in a short period of time, usually between 180-220 ℃.
To ensure the quality of plasticization, the screw barrel of the extruder should have good heating uniformity, and the temperature control accuracy is generally required to be within ± 2 ℃.
Mixing performance
Due to the need to add various additives such as reinforcing materials, toughening agents, flame retardants, etc. in the production of POM masterbatch, the extruder needs to have strong mixing performance to ensure that these additives can be evenly dispersed in the POM resin matrix.
Usually, the mixing effect is improved by optimizing the structure of the screw, such as using special mixing elements and increasing the aspect ratio of the screw. Generally, a length to diameter ratio between 25-40 is more suitable.
Transportation stability
The extruder needs to ensure stable material transportation within the screw barrel to achieve continuous and stable production. This requires high design and machining accuracy of the screw to avoid phenomena such as material slippage, stagnation, or backflow.
At the same time, the drive system of the extruder should have good stability and speed regulation performance, and be able to accurately adjust the screw speed according to production needs, with a general speed range of 50-500 revolutions per minute.
Voltage endurance capability
In the production process of POM masterbatch, the material will be subjected to high pressure inside the extruder, especially at the head. Therefore, the screw barrel and head of the extruder need to have sufficient pressure resistance to prevent problems such as leakage or equipment damage.
Generally, it is required that the extruder can withstand a pressure of 10-30 MPa.
Corrosion Resistance
Some additives may have a certain degree of corrosiveness, such as flame retardants, so the components in contact with the material, such as the extruder barrel and screw, need to have good corrosion resistance to extend the service life of the equipment.
Usually, stainless steel or materials with special surface treatments are used to manufacture these components.
Cleaning and maintenance convenience
In order to ensure product quality and production efficiency, the extruder needs to be cleaned and maintained regularly. Therefore, the structural design of the extruder should be easy to disassemble, clean, and replace vulnerable components.
For example, the use of a quick opening machine head structure and easily detachable screws makes it convenient for operators to clean and maintain the equipment.
Приложение
POM masterbatch has excellent comprehensive performance and is widely used in multiple fields. The following are some of the main application aspects:
Automotive industry
Power system: POM masterbatch can be used to manufacture various components in automotive engines, such as gears, bearings, shaft sleeves, etc. Its excellent wear resistance, self-lubricating properties, and mechanical strength can ensure stable operation of these components under high-speed and high load working conditions, reduce wear and friction, and improve the efficiency and reliability of the engine.
Interior parts: In terms of automotive interiors, POM masterbatch can be used to produce seat adjustment devices, door and window lifters, dashboard frames, etc. It can be made into various complex shapes through injection molding technology, meeting the requirements of precision, strength, and appearance quality for automotive interior parts. At the same time, POM masterbatch also has good chemical corrosion resistance and weather resistance, which can resist various chemicals and UV erosion in the automotive interior environment, maintaining the performance and appearance of components.
Electronic appliances
Connector: POM masterbatch has excellent electrical insulation performance, mechanical strength, and dimensional stability, making it an ideal material for manufacturing electronic and electrical connectors. It can ensure that the connector maintains good electrical connection performance during long-term use, preventing signal transmission failures or electrical fires caused by poor contact.
Switch components: POM masterbatch can be used to manufacture buttons, sliders, brackets, and other components for switches. Its excellent wear resistance and elastic recovery performance can ensure that the switch still has a sensitive touch and stable performance under frequent operation, extending the service life of the switch.
Machinery manufacturing
Transmission parts: In the field of mechanical transmission, POM masterbatch is commonly used to manufacture transmission parts such as gears, racks, sprockets, etc. Compared with metal transmission parts, POM material transmission parts have the advantages of light weight, low noise, and no need for lubrication, which can reduce the operating costs and maintenance workload of mechanical systems. Meanwhile, the high strength and wear resistance of POM masterbatch can also meet the working requirements of most mechanical transmissions.
Precision parts: Due to the excellent dimensional accuracy and stability of POM masterbatch, it can be used to manufacture various precision mechanical parts, such as clock movement parts, camera shutter components, copier gears, etc. These parts require extremely high dimensional accuracy and performance consistency, and POM masterbatch can meet these requirements through precision injection molding processes, ensuring product quality and reliability.
Daily Necessities
Zipper: POM masterbatch is one of the commonly used materials for manufacturing zippers. It has good wear resistance, corrosion resistance, and flexibility, which can maintain smooth opening and closing performance of the zipper during long-term use, and is not prone to problems such as jamming and breakage. Meanwhile, POM masterbatch can also be made into zippers of various colors by adding different pigments to meet the needs of different consumers.
Toys: In toy manufacturing, POM masterbatch can be used to produce components such as gears, joints, and shells for toys. Its characteristics of safety, non toxicity, bright colors, and good formability can provide good quality and appearance effects for toys, while also ensuring the safety and durability of toys during use.