Fiberglass masterbatch is a thermoplastic reinforced resin masterbatch processed from glass fibers and resin. The processing method of glass fiber masterbatch usually includes steps such as mixing glass fibers with resin, melting, extruding, and cutting. For example, a processing method for water-resistant alcoholysis PPE/glass fiber masterbatch includes plasticizing and melting PPE resin, then impregnating glass fibers with the melt of PPE resin, and finally cooling and solidifying and cutting into pellets.
Types
Classified by length
Long glass fiber: The fiber length is usually between 25-50 millimeters or even longer, which can maintain a long continuous length in the product and has good orientation. Long glass fibers can form a more effective load-bearing network in reinforced plastics, thus significantly improving the mechanical properties of materials such as tensile strength, bending strength, and impact strength. For example, polypropylene materials reinforced with long glass fibers have a tensile strength several times higher than ordinary polypropylene, and have good creep resistance, making them suitable for structural components that can withstand large loads.
Short fiberglass: The fiber length is generally around 3-10 millimeters and is distributed in a discontinuous short cut state in the matrix resin. Although short glass fibers can also improve the mechanical properties of plastics, due to their shorter length, the stress transmission efficiency between fibers and matrix is relatively low when subjected to loads, and the reinforcement effect is not as significant as that of long glass fibers. However, short fiberglass can improve the rigidity and hardness of the material to a certain extent, making the product have good dimensional stability.
Classified by matrix resin
Polyolefin fiberglass masterbatch
Made from polyolefin resins such as polyethylene (PE) and polypropylene (PP) as the matrix, with a certain amount of glass fiber and other additives added. It has good chemical corrosion resistance, water resistance, and processing performance, and is widely used in fields such as plastic pipes, sheets, injection molded products, etc. It can improve the strength, rigidity, and heat resistance of products.
Engineering plastic fiberglass masterbatch
Based on engineering plastics such as nylon (PA), polybutylene terephthalate (PBT), polycarbonate (PC), etc. This type of masterbatch can endow products with excellent mechanical properties, heat resistance, and dimensional stability, and is commonly used in fields with high performance requirements such as automotive parts, electronic and electrical casings, and precision mechanical parts. For example, nylon fiberglass masterbatch can be used to manufacture components around automotive engines, such as intake manifolds, oil pans, etc., which can maintain good performance in high temperature and high mechanical stress environments.
Thermoplastic elastomer fiberglass masterbatch
The matrix is a thermoplastic elastomer (TPE), such as styrene thermoplastic elastomers (SBS, SEBS), polyolefin thermoplastic elastomers (TPO), etc. Combining the flexibility and elasticity of thermoplastic elastomers with the reinforcing effect of glass fibers, it can be used to manufacture products that require both strength and good elasticity and flexibility, such as wire and cable sheaths, elastic components in automotive interior parts, etc.
Classified by glass fiber content
Low glass fiber content masterbatch
The glass fiber content is usually between 5% and 15%. Mainly used in situations where there is no high demand for product performance improvement or high demand for processing fluidity. Adding low glass fiber content masterbatch can improve the strength and rigidity of plastic products to a certain extent, while having a relatively small impact on processing performance and maintaining good molding processability.
Medium glass fiber content masterbatch
The glass fiber content is generally between 15% and 30%. This type of masterbatch has a significant effect on improving the performance of products, which can significantly enhance the mechanical strength, rigidity, and heat resistance of products, while still maintaining good comprehensive performance and processing performance. It is a widely used type of fiberglass masterbatch, suitable for modifying various plastic products.
High fiberglass content masterbatch
The glass fiber content is usually between 30% and 50% or even higher. Mainly used in applications that require extremely high product performance, such as aerospace, high-end electronic equipment, high-performance automotive components, and other fields. High glass fiber content masterbatch can provide products with ultra-high strength, rigidity, and dimensional stability. However, as the glass fiber content increases, the processing difficulty of the product will also increase accordingly, and the requirements for processing equipment and technology will be more stringent.
Classification by function
Ordinary reinforced fiberglass masterbatch
The main purpose is to improve the mechanical properties of plastic products, such as tensile strength, bending strength, impact strength, etc. By uniformly dispersing glass fibers in the matrix resin to form a reinforced skeleton, the strength and rigidity of the product can be effectively improved, meeting the performance requirements of general industrial products.
Heat resistant fiberglass masterbatch
On the basis of ordinary glass fiber masterbatch, some heat-resistant additives or special treatments are added to the glass fiber to make it have better heat resistance performance. It can maintain good mechanical properties and dimensional stability of the product at high temperatures, and is suitable for plastic products that need to be used in high-temperature environments, such as heating components in household appliances and parts in car engine compartments.
Flame retardant fiberglass masterbatch
Added flame retardant to give the product good flame retardant properties. In the event of a fire, it can delay or prevent the combustion of plastic, reduce the production of smoke and toxic gases, and improve the safety of plastic products. Commonly used in fields with high requirements for fire safety, such as electronic and electrical enclosures, wires and cables.
Weather resistant fiberglass masterbatch
In response to the aging problem faced by plastic products during outdoor use, additives such as anti UV agents and antioxidants have been added. It can effectively improve the weather resistance of products, allowing them to maintain good performance and appearance even when exposed to natural environments such as sunlight, wind and rain for a long time, reducing the occurrence of fading, cracking, brittleness and other phenomena. It is suitable for outdoor building materials, automotive exterior parts and other fields.
Formula ratio
Low dielectric constant glass fiber reinforced polypropylene masterbatch
Polypropylene: 60-80 parts
Maleic anhydride grafted polypropylene: 3-4 parts
Fiberglass: 20-40 parts
Coupling agent: 0.5-1.5 parts
Antioxidant: 1-1.6 parts
Doped silica: 0.5-0.8 parts
Light stabilizer: 0.1-0.5 parts
Glass fiber reinforced polypropylene masterbatch with high scratch resistance and stress whitening
Polypropylene: 70-90 parts
Polyolefin elastomer: 1-10 parts
High density polyethylene: 1-10 parts
Compatibility agent: 1-5 parts
Scratch resistant additive: 0.1-0.5 parts
Antioxidant masterbatch: 1-5 parts
Stabilizer: 0.2-1 part
High performance fiberglass: 5-20 parts
Color powder (zinc sulfide): 0.5-2.0 parts (including 0.2-1.0 parts of zinc sulfide)
Fiberglass reinforced nylon masterbatch
Nylon (PA6/PA66): 70-90 parts
Fiberglass: 10-30 parts
In actual production, appropriate amounts of coupling agents, antioxidants, lubricants, flame retardants, and other additives can be added according to specific product requirements. For example, adding 1-3 parts of coupling agent to improve the interfacial bonding between fiberglass and nylon; 0.1-0.5 parts antioxidant to improve the antioxidant performance of the material; 0.5-1.5 parts of lubricant to improve processing performance; If flame retardant performance is required, an appropriate amount of flame retardant can be added.
Fiberglass reinforced polyethylene masterbatch
Polyethylene (PE): 75-85 parts
Fiberglass: 15-25 parts
Similarly, 0.5-2 parts of coupling agent, 0.1-0.5 parts of antioxidant, 0.5-1.5 parts of lubricant and other additives can be added as needed to meet different performance requirements.
The above formula ratios are for reference only. The actual formula needs to be adjusted and optimized based on specific application scenarios, product performance requirements, and the characteristics of raw materials.
Production process
Fiberglass masterbatch mainly includes long fiberglass masterbatch, short fiberglass masterbatch, functional fiberglass masterbatch, and other types. Its production process generally includes steps such as raw material preparation, mixing, and processing molding, but the specific process may vary depending on different types of fiberglass masterbatch. The following is a detailed introduction:
Production process of long glass fiber masterbatch
1. Raw material preparation: Select a suitable matrix resin, such as polypropylene, nylon, etc., and dry it to remove moisture and prevent defects such as bubbles during processing. At the same time, prepare long glass fibers with a length of 25-50 millimeters and perform surface treatment, such as coating with coupling agents, to improve the bonding strength between the glass fibers and the matrix resin.
2. Mixing: Add the dried matrix resin and processed long glass fibers in a certain proportion to a high-speed mixer for pre mixing, so that the two are initially evenly dispersed.
3. Extrusion: Add the pre mixed material into a twin-screw extruder for extrusion. During the extrusion process, parameters such as screw speed, temperature, and pressure need to be precisely controlled. Usually, the temperature of the extruder is set above the melting point of the matrix resin to fully melt the resin. At the same time, the long glass fibers are uniformly dispersed in the melted resin through the rotation and shear action of the screw. In order to ensure the length and orientation of long glass fibers, the aspect ratio of the extruder is generally large, and fiber breakage should be minimized as much as possible during the extrusion process.
4. Cooling granulation: The extruded material is cooled and shaped by water or air cooling, and then cut into particles of a certain length by a granulator to obtain long glass fiber masterbatch.
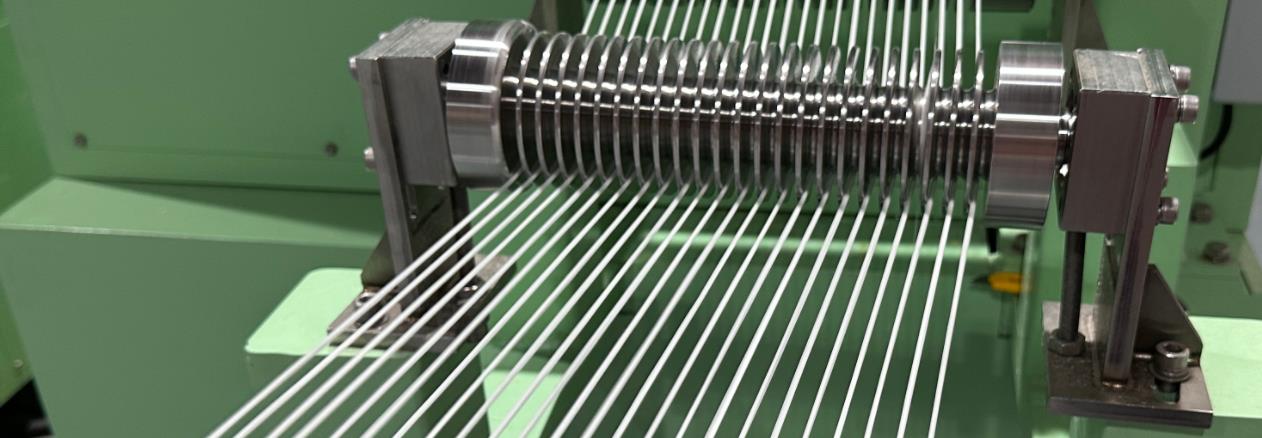
Production process of short glass fiber masterbatch
1. Raw material preparation: Select suitable matrix resins such as polyethylene, polybutylene terephthalate, etc., and dry them. Prepare short glass fibers with a length of 3-10 millimeters, which can also be surface treated.
2. Mixing: Add the matrix resin and short glass fibers into a high-speed mixer, while adding appropriate amounts of coupling agents, lubricants, and other additives for thorough mixing, so that the short glass fibers are evenly distributed in the resin.
3. Extrusion: Put the mixed materials into a single screw or twin-screw extruder for extrusion. Compared with the production of long glass fiber masterbatch, the extrusion process of short glass fiber masterbatch is relatively simple and requires lower aspect ratio of the extruder. During the extrusion process, the resin is melted and thoroughly mixed with short glass fibers by controlling the temperature and screw speed. Due to the good dispersibility of short glass fibers in the resin, the flowability of the material during extrusion is good, resulting in higher production efficiency.
4. Cooling granulation: After the extruded material is cooled, it is cut into granules by a granulator to obtain short glass fiber masterbatch.
Production process of functional fiberglass masterbatch
1. Raw material preparation: In addition to the matrix resin and glass fiber, corresponding functional additives need to be prepared according to functional requirements, such as flame retardants for improving flame retardancy and conductive fillers for improving conductivity. The processing of matrix resin and glass fiber is similar to the raw material preparation process of long or short glass fiber masterbatch mentioned above.
2. Mixing: Mix the matrix resin, glass fiber, and functional additives into a high-speed mixer according to specific formula ratios. To ensure the uniform dispersion of functional additives in the matrix resin, special mixing processes or the addition of dispersants may be necessary.
3. Extrusion: Send the mixed material into the extruder for extrusion. During the extrusion process, more precise control of process parameters is required to ensure the interaction between functional additives, matrix resin, and glass fibers, in order to achieve the expected functional performance. For example, in the production of flame-retardant fiberglass masterbatch, it is necessary to control the extrusion temperature and residence time to ensure that the flame retardant can fully exert its effect without affecting the performance of the matrix resin and fiberglass.
4. Cooling granulation: After extrusion, the material is cooled and shaped before granulation to obtain functional fiberglass masterbatch.
There are certain differences in the selection of raw materials, mixing methods, extrusion parameter control, and other aspects in the production process of different types of fiberglass masterbatch. The production process needs to be optimized and adjusted according to specific product requirements and raw material characteristics to ensure that product quality and performance meet the requirements.
(LFT-G) Long fiber reinforced thermoplastic composite material production line
Production equipment
The production equipment for fiberglass masterbatch varies depending on the production process and product type, mainly including the following:
Mixing equipment
High speed mixer: used for preliminary mixing of various raw materials such as matrix resin, glass fiber, coupling agent, lubricant, etc., to evenly disperse each component. It has the characteristics of fast mixing speed and good mixing effect, which can mix different properties of raw materials evenly in a short time, preparing for subsequent extrusion processing.
Dual planetary mixer: For the production of glass fiber masterbatch with high requirements for mixing uniformity, especially for formulas containing functional additives, dual planetary mixer is a commonly used equipment. It rotates in the mixing container through two planetary stirring blades, generating strong stirring and shearing effects, which can achieve finer and more uniform mixing effects, ensuring that functional additives are evenly distributed in the matrix resin.
Extrusion equipment
Twin screw extruder: It is the most commonly used extrusion equipment in the production of fiberglass masterbatch. It has strong conveying, mixing, and shearing capabilities, which can fully melt the matrix resin at high temperatures and mix it evenly with glass fibers. The screw structure is complex and can be designed and combined according to different production needs, such as changing the aspect ratio, groove depth, thread angle, etc. of the screw to adapt to the production of different types of fiberglass masterbatch. The production of long glass fiber masterbatch usually requires a twin-screw extruder with a large aspect ratio to ensure the uniform dispersion and good orientation of glass fibers in the resin.
Single screw extruder: widely used in the production of short glass fiber masterbatch. Its structure is relatively simple, the cost is low, and it is suitable for situations where the mixing requirements are not particularly high and the production scale is small. The single screw extruder pushes the material forward through the rotation of the screw, causing the resin to melt and mix with short glass fibers under heating and shearing. Although its mixing effect is not as good as that of twin-screw extruders, it can still meet the product quality requirements for the production of short glass fiber masterbatch under reasonable control of process parameters.
Granulation equipment
Water cooled strand cutting machine: First, the extruded fiberglass masterbatch material is cooled and shaped through a water cooling tank, and then the cutting machine cuts the material into particles of a certain length. This granulation method produces particles with regular shapes, smooth surfaces, and good quality. Suitable for the production of various types of fiberglass masterbatch, especially for products with high requirements for particle appearance quality.
Wind cooled granulator: Cut the molten material into particles directly at the extruder head, and then cool the particles through an air cooling system. Its advantages are high production efficiency, regular particle shape, and small equipment footprint. But for some high viscosity materials or situations that require high particle cooling, other cooling methods may need to be combined to ensure particle quality.
Auxiliary equipment
Drying equipment: such as ovens, dehumidifiers, etc., used for drying raw materials such as base resins to remove moisture and volatile substances. The dried raw materials can effectively avoid problems such as bubbles and hydrolysis during the extrusion process, improving product quality. Different resin materials have different requirements for drying conditions, and suitable drying equipment and drying processes need to be selected according to specific situations.
Measuring equipment: including electronic scales, weight loss scales, etc., used to accurately measure the input amount of various raw materials. Accurate measurement is the key to ensuring the accurate proportion of fiberglass masterbatch formula and stable product quality. Measurement equipment needs to have high accuracy and stability to meet the measurement requirements in the production process.
Cooling equipment: In addition to the water cooling tank in the water-cooled bar granulator and the air cooling system in the air-cooled granulator, specialized cooling circulation systems such as chillers and cooling towers are also required for some large production equipment or production in high-temperature environments to ensure the normal operation of the equipment and the cooling effect of the materials.
In addition, in the production of functional fiberglass masterbatch, special equipment may be used according to specific functional requirements, such as high-speed dispersers to further refine and disperse conductive fillers when adding them, and specialized flame retardant treatment equipment may be required when producing flame-retardant fiberglass masterbatch.
Fiberglass masterbatch extruder
Kerke’s masterbatch extruder can be used to produce Fiberglass masterbatch. Our Fiberglass masterbatch extruder has multiple models to choose from, which can meet different production requirements.
-
Лабораторный двухшнековый экструдер
When will you need a lab twin screw extruder? If you want to make trials and tests of…
-
Параллельный двухшнековый экструдер
Our Parallel Co-rotating twin screw extruder is designed for compounding and masterbatch making with an output capacity from…
-
Тройной (3 винта) Экструдер
3 Screws extruder is a new technology that has many advantages. The triple screw extruder is mainly used…
-
Двухступенчатая система экструзии
Mother-baby extrusion system is designed for special materials which can not process on one stage extruder, the first…
-
Линия для замешивания компаундов Banbury Kneader
Our kneader + extruder is designed for making special applications with an output capacity from 30kg/h to 1000kg/h.…
-
Система резки / Система гранулирования
Different material needs different cutting system, Kerke provides all kinds of cutting system, here is the explanation of…
Related requirements
The extruder is a key equipment for the production of fiberglass masterbatch. Different types of fiberglass masterbatch have different requirements for the extruder. Overall, there are the following requirements in terms of screw structure, aspect ratio, temperature control, etc.:
Screw structure
Conveyor section: The screw conveyor section is required to have good material conveying capacity, which can stably transport the mixed materials from the hopper to the heating and mixing area of the extruder. For the production of fiberglass masterbatch, especially for long fiberglass masterbatch, the presence of fiberglass increases the friction and flowability of the material. Therefore, the screw design of the conveying section needs to consider how to effectively push these mixed materials with different characteristics, avoiding material accumulation or unstable conveying.
Compression section: In the compression section, the screw needs to compress the material to gradually compact it and eliminate air and volatile substances. For fiberglass masterbatch, the design of the compression section should be able to adapt to the mixing characteristics of fiberglass and matrix resin, ensuring effective compression of the material while avoiding excessive compression that may cause excessive breakage or damage to the fiberglass and affect product performance.
Measurement section: The screw in the measurement section needs to precisely control the extrusion amount of the material to ensure the stability of product quality. In the production of fiberglass masterbatch, the content and distribution of fiberglass have a significant impact on product performance. Therefore, the screw design of the measuring section should be able to accurately extrude uniformly mixed materials at a stable flow rate, ensuring that the content and distribution of fiberglass in each batch of products are uniform and consistent.
Aspect ratio
Long glass fiber masterbatch: The production of long glass fiber masterbatch usually requires a large aspect ratio, generally between 30-40. A longer aspect ratio can provide sufficient space and time for glass fibers to be fully dispersed and oriented in the matrix resin. In extruders with a large aspect ratio, the material stays in the screw for a longer time. After multiple heating and shearing zones, it can better achieve resin melting, infiltration of glass fibers and resin, and uniform distribution of glass fibers, thereby improving the performance of long glass fiber masterbatch.
Short glass fiber masterbatch: The production of short glass fiber masterbatch has relatively low requirements for aspect ratio, generally between 20-30. Due to the relatively easy dispersion of short glass fibers in the resin, there is no need for excessively long screws to achieve uniform mixing. A shorter aspect ratio can improve production efficiency, reduce equipment costs and energy consumption while ensuring product quality.
Temperature control
Accuracy: The temperature control of the extruder needs to be very precise, as temperature has a significant impact on the melting state of the matrix resin, the bonding between glass fibers and resin, and the final performance of the product. Different matrix resins have different melting points and processing temperature ranges. For example, the processing temperature of nylon is generally between 250-280 ℃, and the processing temperature of polypropylene is between 180-220 ℃. When producing fiberglass masterbatch, it is necessary to control the temperature of each section of the extruder within the corresponding precise range according to the type of matrix resin used, to ensure that the resin can be fully melted and to avoid excessive temperature that may cause resin degradation or glass fiber performance degradation.
Uniformity: In addition to precise temperature control, the temperature distribution inside the extruder also needs to be maintained uniformly. Uneven temperature distribution can lead to uneven heating of materials during extrusion, thereby affecting the mixing effect of glass fibers and resins and the quality stability of products. For example, if the temperature of a certain section of the extruder is too high or too low, it may cause excessive or insufficient melting of the resin in that area, resulting in uneven dispersion of glass fibers in that area, ultimately affecting the mechanical properties and appearance quality of the product.
Shear strength
Moderate shear: In the production of fiberglass masterbatch, the extruder needs to provide moderate shear strength to achieve uniform dispersion and good bonding of fiberglass in the matrix resin. For long glass fiber masterbatch, appropriate shearing can better orient the long glass fibers in the resin and improve the mechanical properties of the product; For short glass fiber masterbatch, shear action helps to evenly distribute short glass fibers in the resin matrix, enhancing the overall performance of the product. But the shear strength cannot be too high, otherwise it will cause excessive breakage of glass fibers and reduce the reinforcement effect of glass fibers; The shear strength should not be too low, otherwise it will be impossible to achieve sufficient mixing and good bonding between glass fiber and resin.
Adjustable: The shear strength of the extruder should have good adjustability to adapt to the production of different types and formulations of fiberglass masterbatch. By adjusting parameters such as screw speed, groove depth, and thread shape, the shear strength of the extruder can be changed. For example, in the production of masterbatch containing high filling amount of glass fibers, it may be necessary to appropriately increase the shear strength to ensure the uniform dispersion of glass fibers in the resin; When producing long glass fiber masterbatch with high requirements for retaining the length of glass fibers, it is necessary to reduce the shear strength to avoid excessive breakage of glass fibers.
Corrosion Resistance
Contact with corrosive substances: In the production process of fiberglass masterbatch, the material may contain some substances that are corrosive to the equipment, such as certain coupling agents, additives, or acidic gases generated at high temperatures. These corrosive substances will come into contact with the screws, barrels, and other components of the extruder. If the corrosion resistance of the equipment is poor, it can cause surface corrosion and wear of the components, affecting the normal operation and service life of the equipment. At the same time, it may also contaminate the product and affect its quality.
Material selection: In order to improve the corrosion resistance of the extruder, materials with good corrosion resistance are usually chosen to manufacture the screw and barrel. For example, using stainless steel material or anti-corrosion treatment on metal surfaces, such as hard chrome plating, spraying corrosion-resistant coatings, etc. In addition, when designing the extruder, the rationality of the structure will also be considered to avoid the accumulation and retention of materials in the equipment, and reduce the erosion of corrosive substances on the equipment.
In addition, when producing functional fiberglass masterbatch, extruders may also need to have some special functions or requirements to meet the needs of adding and mixing functional additives. For example, in the case of adding nanoscale functional fillers, the extruder may need to be equipped with high-precision metering and mixing devices to ensure the uniform dispersion of the nano fillers in the resin.
Приложение
Fiberglass masterbatch is a granular product made by special processing of glass fibers and resin materials, which has a wide range of applications in various fields. The following are some of the main application aspects:
Reinforced plastic
Automotive components: Fiberglass masterbatch can be used to manufacture engine hoods, bumpers, instrument panels, door interior panels, and other components of automobiles. Adding fiberglass masterbatch can improve the strength, stiffness, and heat resistance of plastics, making automotive components more durable and sturdy. At the same time, it can also reduce component weight and help improve the fuel economy of automobiles.
Electronic and electrical casing: In the field of electronic and electrical appliances, fiberglass masterbatch is commonly used in the production of computer cases, TV casings, mobile phone casings, etc. It can enhance the mechanical properties of plastic shells, improve their impact resistance and wear resistance, protect internal electronic components from external environmental influences, and also improve the dimensional stability of the shell, preventing deformation due to heat or force during use.
Industrial products: In the industrial field, fiberglass masterbatch can be used to manufacture various mechanical parts, pipe fittings, sheets, etc. For example, fiberglass reinforced engineering plastics can be used to manufacture gears, bearings, conveyor belts, etc., which can withstand large loads and pressures, improve the operational efficiency and service life of industrial equipment.
Improve plastic properties
Improving heat resistance: Many plastics are prone to deformation or performance degradation in high temperature environments, and adding fiberglass masterbatch can significantly improve the heat resistance of plastics. For example, adding an appropriate amount of fiberglass masterbatch to polypropylene (PP) plastic can increase its thermal deformation temperature from about 100 ℃ to over 150 ℃, thereby expanding the temperature range of plastic use and making it suitable for applications that require high heat resistance.
Increasing dimensional stability: Fiberglass masterbatch can effectively improve the shrinkage rate of plastics and enhance their dimensional stability. During the molding process of plastic products, the shrinkage of plastic may lead to insufficient dimensional accuracy or deformation of the product. After adding fiberglass masterbatch, fiberglass can form a skeleton structure in the plastic, restricting the movement of plastic molecules and reducing the shrinkage rate of the plastic, allowing the product to maintain more accurate size and shape.
Improving mechanical performance: Fiberglass masterbatch can significantly enhance the mechanical properties of plastics, such as tensile strength, bending strength, and impact resistance. Glass fiber has high strength and modulus, and when combined with plastic matrix, it can bear some external forces, thereby improving the mechanical properties of the entire composite material. For example, adding about 30% glass fiber masterbatch to polyamide (PA) plastic can increase its tensile strength by more than twice, and its bending strength and impact resistance will also be significantly improved.
Other applications
Wire and cable: Fiberglass masterbatch can be used in the insulation layer and sheath material of wire and cable. It can improve the mechanical properties and heat resistance of materials, enhance the tensile, abrasion and aging resistance of wires and cables, and extend their service life. At the same time, fiberglass masterbatch also has certain flame retardant properties, which can improve the fire safety of wires and cables.
Building materials: In the field of construction, fiberglass masterbatch can be used to produce various building plastic products, such as plastic pipes, panels, door and window profiles, etc. Adding fiberglass masterbatch can improve the strength, stiffness, and weather resistance of these building materials, making them more durable and able to resist the erosion of natural environments such as wind, sun, and rain.
Fiber reinforced thermoplastic composites: Fiberglass masterbatch is an important raw material for preparing fiber-reinforced thermoplastic composites (FRTP). FRTP has advantages such as high specific strength, high specific modulus, fatigue resistance, and corrosion resistance, and has a wide range of applications in aerospace, rail transportation, sports equipment, and other fields. For example, in the aerospace field, FRTP can be used to manufacture aircraft wings, fuselage structural components, etc., which can reduce the weight of the aircraft while ensuring the strength and reliability of the structure.