Caco3 filler masterbatch is a concentrated mixture containing calcium carbonate particles, which is mixed with a carrier and then cut into granules. The granules are white with a whiteness of over 98%. It is mainly composed of calcium carbonate filler, coupling agent, dispersant, and carrier resin. Among them, calcium carbonate mainly plays a role in modification and cost reduction; Coupling agents improve the adhesion between fillers and resins; Dispersants can effectively disperse calcium carbonate powder in the carrier resin; The carrier resin has good compatibility with the resin to be filled and has certain mechanical properties.
Types
Classified by particle size of calcium carbonate
Ordinary Caco3 filler masterbatch: Calcium carbonate with larger particle size, generally above 10 microns, is usually used. This type of masterbatch has a lower production cost and is mainly used in products that do not require high filler particle size and pursue low cost, such as some ordinary plastic products, rubber products, etc. It can increase product weight and reduce costs.
Micro Caco3 filler masterbatch: The particle size of calcium carbonate is between 1-10 microns. Compared with ordinary Caco3 filler masterbatch, the products filled with fine Caco3 filler masterbatch have certain improvements in mechanical properties, such as tensile strength, impact strength, etc. At the same time, it can improve the surface smoothness of the products and can be used in plastics, rubber, coatings and other products with certain performance requirements.
Nano Caco3 filler masterbatch: The particle size of calcium carbonate is less than 100 nanometers. Nano calcium carbonate has a huge specific surface area and special surface properties. Adding it to the matrix material can significantly improve the material’s performance, such as enhancing the rigidity, toughness, heat resistance, etc. of plastics, improving the vulcanization and wear resistance of rubber, etc. It has a wide range of applications in high-end plastic products, rubber products, coatings, inks, and other fields.
Classified by surface treatment condition
Untreated Caco3 filler masterbatch: The surface of calcium carbonate is not treated and is directly mixed with carrier resin to form masterbatch. This type of masterbatch has poor compatibility with the matrix material and is prone to agglomeration during the filling process, resulting in a decrease in product performance. It is generally only used in products with low performance requirements.
Surface treatment of Caco3 filler masterbatch:
Fatty acid treated Caco3 filler masterbatch: Fatty acids such as stearic acid are commonly used for surface treatment of calcium carbonate. One end of the fatty acid molecule undergoes a chemical reaction with the hydroxyl group on the surface of calcium carbonate, while the other end is a non-polar group that can be better compatible with organic matrix materials, thereby improving the dispersibility of calcium carbonate in the matrix and enhancing the mechanical and processing properties of the product. It is widely used in industries such as plastics and rubber.
Coupling agent treatment of Caco3 filler masterbatch: Silane coupling agent, titanate coupling agent, etc. are used to treat the surface of calcium carbonate. Coupling agent molecules have two different functional groups that can undergo chemical reactions with the surface of calcium carbonate and the matrix material, respectively. They can form chemical bonds between calcium carbonate and the matrix material, greatly improving their bonding strength and significantly improving the performance of the product. They are particularly used in high-performance composite materials.
Composite treatment of Caco3 filler masterbatch: Multiple surface treatment agents are used to composite treat calcium carbonate, combining the advantages of different treatment agents to further improve the compatibility between calcium carbonate and matrix materials and the performance of products. It is suitable for high-end products with high performance requirements.
Classified by carrier resin
Polyethylene (PE) carrier Caco3 filler masterbatch: Using polyethylene as the carrier resin, it has good processing performance and flexibility, and is compatible with polyethylene plastic matrix. It is mainly used for filling and modifying polyethylene plastic products, such as polyethylene films, pipes, injection molded products, etc., which can reduce costs and improve certain properties of the products.
Polypropylene (PP) carrier Caco3 filler masterbatch: Using polypropylene as the carrier resin, it has good compatibility with polypropylene plastic and can be uniformly dispersed in polypropylene products. Suitable for polypropylene injection molded products, fibers, films, and other fields, it can improve the rigidity, hardness, and heat resistance of products.
Polyvinyl chloride (PVC) carrier Caco3 filler masterbatch: Using PVC as the carrier resin, it has good compatibility with PVC resin and can be used in PVC pipes, profiles, films, artificial leather and other products, reducing production costs while improving the processing performance and certain physical properties of PVC products.
Other carrier Caco3 filler masterbatch: There are also Caco3 filler masterbatch using polystyrene (PS), polyester (PET, PBT, etc.), nylon (PA) and other carrier resins, which are suitable for corresponding resin based composite materials to meet the performance requirements and processing characteristics of different materials.
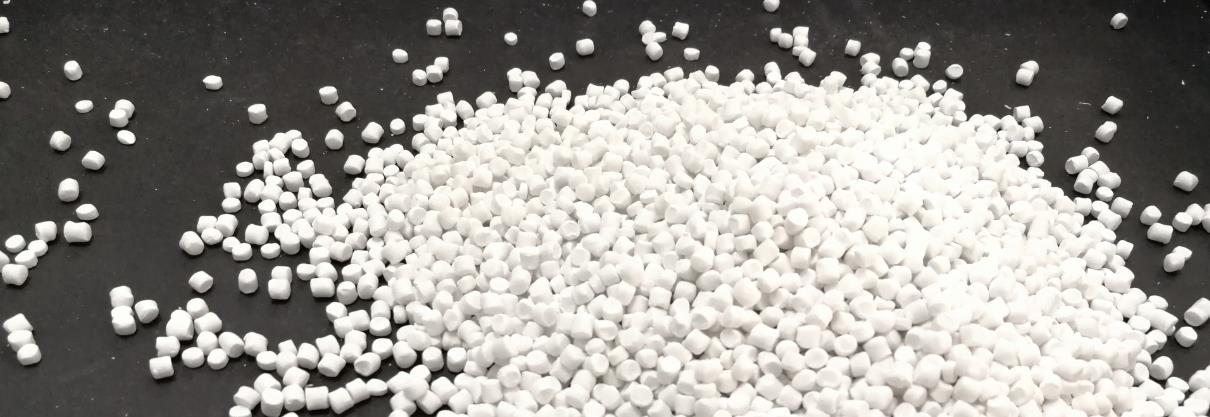
Formula ratio
The formula ratio of Caco3 filler masterbatch may vary depending on factors such as application field, performance requirements, and carrier resin type. The following are some common formula ratio examples:
Calcium carbonate filler master batch for plastic film: 84-90 parts of calcium carbonate, 1.5-5 parts of low-density polyethylene, 3-8 parts of linear low-density polyethylene, 0.5-2 parts of stearate, 1-2.8 parts of polyvinyl acetate lotion, and 1-3 parts of polyethylene wax. Among them, calcium carbonate is preferred to be 800-1250 mesh, linear low-density polyethylene grades are preferred to be 7144, 8916, 7050, 8332 or 3224, etc., and polyethylene wax molecular weight is preferred to be 1500-4500. The masterbatch produced by this formula can be applied to plastic films, which can achieve lower density and higher foaming rate, while improving rigidity.
Caco3 filler masterbatch for polymer waterproofing membranes: based on weight parts, 50-90 parts calcium carbonate, 5-30 parts resin, 2-10 parts titanium dioxide, 0.5-3 parts first lubricant, 0.5-3 parts second lubricant, and 0.5-3 parts third lubricant. The particle size of calcium carbonate is 800-2000 mesh. This formula uses multiple lubricants to treat the surface of calcium carbonate, improving the interface compatibility between resin and calcium carbonate. It can prepare high filling content calcium carbonate masterbatch, which can be applied to polymer waterproofing membranes to enhance their performance.
Biodegradable Caco3 filler masterbatch: 70-85 parts calcium carbonate, 15-28 parts PBAT, 0.3-1 part monoglyceride, 0.3-1 part amide modified aliphatic hyperbranched polyester. The moisture content of calcium carbonate is below 0.1wt%, and the particle size is above 1250 mesh, preferably 1250-3000 mesh. Monostearic acid glycerol ester is coated on the surface of calcium carbonate, and amide modified aliphatic hyperbranched polyester is coated on the surface of monostearic acid glycerol ester, which can improve the addition amount of calcium carbonate in the biodegradable material PBAT and the mechanical properties of the resulting composite material.
In actual production, it is necessary to determine the optimal formula ratio through experiments and debugging based on specific product requirements, production processes, and cost factors.
Production process
The production process of Caco3 filler masterbatch usually includes the following main steps:
Raw material preparation
Calcium carbonate: Select appropriate particle size and purity of calcium carbonate powder according to product requirements, such as ordinary calcium carbonate, fine calcium carbonate, or nano calcium carbonate. Generally speaking, high-purity, uniformly sized, and well dispersed calcium carbonate helps to improve the quality of masterbatch.
Carrier resin: Common carrier resins include polyethylene (PE), polypropylene (PP), polyvinyl chloride (PVC), etc. According to the application field and performance requirements of Caco3 filler masterbatch, select the corresponding carrier resin and ensure its good flowability, thermal stability, and compatibility with calcium carbonate.
Surface treatment agent: In order to improve the adhesion and dispersibility between calcium carbonate and carrier resin, it is necessary to use surface treatment agents to treat the surface of calcium carbonate. Common surface treatment agents include fatty acids (such as stearic acid), coupling agents (such as silane coupling agents, titanate coupling agents), etc.
Other additives: Other additives such as lubricants, antioxidants, dispersants, etc. may be added as needed to improve the processing and usability of the masterbatch.
Calcium carbonate surface treatment
Add calcium carbonate powder into a high-speed mixer, heat it to a certain temperature (usually 80-120 ℃), and then slowly add an appropriate amount of surface treatment agent while stirring, so that the surface treatment agent evenly covers the surface of the calcium carbonate particles. The stirring time is generally 10-30 minutes, and the specific time and temperature depend on the type, particle size, and surface treatment agent of the calcium carbonate. For example, when using stearic acid to treat calcium carbonate, the stirring temperature can be controlled at 100-120 ℃ and the stirring time is 15-20 minutes to ensure that the stearic acid fully reacts with the surface of calcium carbonate and forms a uniform coating layer.
Mixing of ingredients
Add surface treated calcium carbonate, carrier resin, and other additives to the feeding hopper of the high-speed mixer or twin-screw extruder according to the set formula ratio. By stirring or rotating the screw, various raw materials are thoroughly mixed evenly. The mixing time is usually 5-15 minutes to ensure the uniformity of material mixing. During the mixing process, attention should be paid to controlling the mixing speed and temperature to avoid material performance degradation caused by excessive friction or high temperature.
Melt extrusion
The mixed material enters the twin-screw extruder and moves forward under the push of the screw. At the same time, the heating system of the extruder heats the material to a certain temperature, causing the carrier resin to melt. The twin-screw extruder has good mixing and shearing effects, which can evenly disperse calcium carbonate in the molten carrier resin. The extrusion temperature is generally set according to the type and characteristics of the carrier resin. For example, for polyethylene carrier resin, the extrusion temperature is usually between 160-200 ℃; For polypropylene carrier resin, the extrusion temperature is around 180-220 ℃. The residence time of materials in the extruder is generally 2-5 minutes to ensure sufficient mixing and uniform dispersion of calcium carbonate and carrier resin.
The molten material is extruded from the die of the extruder to form continuous strips or filaments. The extruded material is cooled and shaped by a cooling water tank or air cooling device to solidify into the desired shape.
Diced
The cooled strip or filamentous material is cut into particles of a certain length by a granulator to obtain Caco3 filler masterbatch. The size and shape of the pellets can be adjusted according to customer requirements. Generally speaking, the particle size of the masterbatch is usually around 2-5 millimeters, and its shape is cylindrical or spherical.
Package
The cut Caco3 filler masterbatch is usually packaged in plastic woven bags or sealed plastic bags to prevent moisture and contamination of the masterbatch. The packaged masterbatch is stored in a dry and ventilated warehouse, waiting for factory sales or further processing and use.
In the production process, it is necessary to strictly control the process parameters of each link, such as temperature, speed, time, etc., to ensure the quality stability and performance of Caco3 filler masterbatch meet the requirements. At the same time, regular maintenance and upkeep of production equipment are necessary to ensure its normal operation and production efficiency.
Production equipment
The production equipment for Caco3 filler masterbatch mainly includes the following types:
Mixing equipment
High speed mixer: used to thoroughly mix calcium carbonate, carrier resin, surface treatment agents, and other additives. It uses high-speed rotating stirring blades to achieve uniform mixing of materials in a short period of time, while preheating the materials during the mixing process to prepare for subsequent extrusion processing.
Dual planetary mixer: It has two planetary stirring blades and one scraping blade, which can efficiently mix materials at different speeds. The special design of its stirring blade can generate complex motion trajectories of materials during the mixing process, thereby achieving a more uniform mixing effect, especially suitable for the production of Caco3 filler masterbatch with high requirements for mixing uniformity.
Surface treatment equipment
Reactor: If a more complex surface treatment process is used, such as surface modification with coupling agents, the reactor can provide a controllable reaction environment. Under certain temperature, pressure, and stirring conditions, fully react the coupling agent with the surface of calcium carbonate to improve the compatibility between calcium carbonate and the carrier resin.
Extrusion equipment
Twin screw extruder: It is a key equipment for producing Caco3 filler masterbatch. It has two interlocking screws that drive the material forward through the rotation of the screws. At the same time, heating and cooling devices are installed in different sections of the screws to ensure that the material undergoes multiple stages such as heating, melting, mixing, and shearing during the extrusion process, ensuring that calcium carbonate is evenly dispersed in the carrier resin. The length to diameter ratio, screw configuration, and other parameters of twin-screw extruders can be adjusted according to production needs to adapt to different material characteristics and product requirements.
Single screw extruder: In some situations where production accuracy is not high or output is small, single screw extruders are also used. It has a relatively simple structure and lower cost, but its mixing and dispersing effects are not as good as twin-screw extruders. The single screw extruder melts and extrudes materials through the rotation of the screw and the heating of the barrel, and is suitable for producing Caco3 filler masterbatch with relatively low production requirements.
Cooling equipment
Cooling water tank: The extruded masterbatch is cooled and shaped through a cooling water tank. The water in the sink can rapidly cool down the masterbatch, transforming it from a molten state to a solid state, thereby maintaining the shape and size stability of the masterbatch. The length and water temperature of the cooling water tank can be adjusted according to the characteristics of the masterbatch and production speed.
Air cooling device: For some masterbatch that is not suitable for contact with water or requires high cooling speed, an air cooling device can be used for cooling. The air cooling device blows cold air towards the extruded masterbatch through a fan, rapidly cooling it in the air. The air cooling method can avoid the problem of residual moisture caused by water cooling, while also improving production efficiency.
Granulation equipment
Hot cutting machine: When the masterbatch is in a thermoplastic state, it is cut into granules by a rotating tool. The advantages of the hot cutting machine are fast cutting speed, high production efficiency, regular particle shape, and smooth surface. But it causes significant wear on the cutting tools and requires regular tool replacement.
Cold cutting machine: First, cool the extruded masterbatch to room temperature, and then proceed with cutting. The cutting process of the cold granulator is relatively stable, with less wear on the cutting tool, and is suitable for cutting masterbatch of various hardness. However, the production efficiency of the cold granulator is relatively low, and the cut particles may have some burrs.
Packaging Equipment
Automatic packaging machine: capable of automatically measuring, filling, and sealing Caco3 filler masterbatch. It can accurately pack the masterbatch into the packaging bag according to the set packaging weight or quantity, and complete the sealing operation, improving packaging efficiency and quality. The automatic packaging machine can also be equipped with auxiliary equipment such as conveyor belts and sewing machines to achieve automation of the packaging production line.
Measuring equipment: such as electronic scales, used to accurately measure the packaging weight of masterbatch. During the packaging process, the electronic scale can monitor the weight of the material in real time. When the set packaging weight is reached, it automatically stops feeding to ensure that the weight of the masterbatch in each packaging bag meets the requirements.
Caco3 Filler masterbatch extruder
Kerke’s masterbatch extruder can be used to produce Caco3 filler masterbatch. Our Caco3 filler masterbatch extruder has multiple models to choose from, which can meet different production requirements.
-
Лабораторный двухшнековый экструдер
When will you need a lab twin screw extruder? If you want to make trials and tests of…
-
Параллельный двухшнековый экструдер
Our Parallel Co-rotating twin screw extruder is designed for compounding and masterbatch making with an output capacity from…
-
Тройной (3 винта) Экструдер
3 Screws extruder is a new technology that has many advantages. The triple screw extruder is mainly used…
-
Двухступенчатая система экструзии
Mother-baby extrusion system is designed for special materials which can not process on one stage extruder, the first…
-
Линия для замешивания компаундов Banbury Kneader
Our kneader + extruder is designed for making special applications with an output capacity from 30kg/h to 1000kg/h.…
-
Система резки / Система гранулирования
Different material needs different cutting system, Kerke provides all kinds of cutting system, here is the explanation of…
Related requirements
The production of caco3 filler masterbatch has many requirements for extruders, mainly reflected in the following aspects:
Mixing and dispersing ability
Screw design: Special designed screws are required, such as those with multiple kneading blocks and reverse threaded segments. Kneading blocks can generate strong shear and mixing effects, evenly dispersing caco3 particles in the carrier resin; The reverse threaded section can cause reverse flow of the material, further improving the mixing effect.
High shear capacity: The extruder should have sufficient shear force to overcome the interfacial tension between caco3 and resin, allowing caco3 to be evenly distributed in the resin matrix. A higher shear rate can also better coat the resin on the surface of caco3 particles, improving the performance of the masterbatch.
Transportation capacity
Stable material transportation: It can ensure the stable and continuous transportation of materials such as caco3, resin, and various additives inside the screw, avoiding material accumulation or breakage, to ensure the stability of the production process and consistency of product quality.
Adapt to high filling volume: Due to the high content of caco3 in the caco3 filler masterbatch, the extruder needs to be able to adapt to the transportation of materials with high filling volume. This requires the reasonable design of parameters such as groove depth and pitch of the screw to increase the material conveying capacity and avoid screw overload caused by excessive material.
Heating and cooling system
Accurate temperature control: During the extrusion process, precise temperature control of the material is required. Different resins and caco3 have different processing temperature ranges, and the heating system of the extruder should be able to quickly heat the material to the desired processing temperature while maintaining temperature stability and controlling deviations within a small range. The cooling system should be able to timely cool and shape the extruded masterbatch to prevent deformation or performance changes during the cooling process.
Multi stage temperature control: In order to meet the temperature requirements of materials at different processing stages, extruders usually need to set up multiple heating and cooling zones. For example, in the feeding section, the temperature should not be too high to prevent premature melting of materials and affect transportation; In the compression and metering sections, the temperature should gradually increase to ensure that the material is fully melted and mixed; At the head of the machine, the temperature should be appropriately lowered to ensure that the extruded masterbatch has a good molding effect.
Voltage endurance capability
Enduring high pressure: In the production process of caco3 filler masterbatch, due to the high viscosity of the material and the significant wear of the caco3 particles on the screw and barrel, the extruder needs to withstand high pressure. Therefore, the barrel and screw of the extruder need to be made of high-strength and wear-resistant materials, such as nitride steel, bimetallic alloys, etc., to ensure that the equipment can maintain good performance and accuracy under long-term high-pressure operation.
Pressure stability: The hydraulic or mechanical transmission system of the extruder should be able to provide stable pressure and avoid excessive pressure fluctuations. The instability of pressure can lead to fluctuations in extrusion volume, which in turn affects the quality and yield of masterbatch.
Automated control
Parameter monitoring and adjustment: Equipped with advanced automation control system, it can monitor and adjust various parameters of the extruder in real time, such as temperature, pressure, screw speed, material flow rate, etc. Through the cooperation of sensors and controllers, parameters can be automatically adjusted according to the actual situation in the production process, ensuring the stability of the production process and product quality.
Fault diagnosis and alarm: The automation control system should also have fault diagnosis function, which can timely detect faults during equipment operation and issue alarm signals. At the same time, the system can also record fault information to help maintenance personnel quickly locate and troubleshoot faults, reduce equipment downtime, and improve production efficiency.
Приложение
Caco3 filler masterbatch has a wide range of applications in multiple fields, and the following are some of the main application aspects:
Plastic industry
Improving performance: Adding Caco3 filler masterbatch in plastic processing can enhance the hardness, rigidity, dimensional stability, and heat resistance of plastic products. For example, adding an appropriate amount of Caco3 filler masterbatch to polypropylene (PP) plastic can increase the rigidity of PP products, making them less prone to deformation under pressure, while also increasing their thermal deformation temperature and expanding their application range in high-temperature environments.
Reducing costs: The price of calcium carbonate is relatively low. Adding Caco3 filler masterbatch to plastics can reduce the amount of plastic used without affecting the basic properties of plastic products, thereby reducing production costs. For example, in the production of polyethylene (PE) film, adding a certain proportion of Caco3 filler masterbatch can not only maintain the strength and toughness of the film, but also reduce the amount of PE resin used and lower production costs.
Improving processing performance: Caco3 filler masterbatch can improve the processing flowability of plastics, making them easier to form during extrusion, injection molding, and other processing processes, improving processing efficiency and surface quality of products. For example, in the production of polyvinyl chloride (PVC) pipes, adding Caco3 filler masterbatch can reduce the viscosity of PVC melt, making it smoother during extrusion, reducing extrusion pressure, and improving the surface smoothness of the pipe.
Rubber industry
Enhanced filling: Caco3 filler masterbatch is one of the commonly used fillers in the rubber industry, which can increase the volume of rubber products and reduce production costs. At the same time, it can also improve the hardness, tensile strength, wear resistance, and aging resistance of rubber. For example, in tire production, adding Caco3 filler masterbatch can improve the hardness and wear resistance of the tire tread, and extend the service life of the tire.
Improving processing performance: During rubber processing, Caco3 filler masterbatch can improve the mixing and molding properties of rubber, making it easier to mix with other additives evenly and increasing production efficiency. For example, in the molding process of rubber products, adding Caco3 filler masterbatch can reduce the viscosity of rubber, making it easier to flow and form in the mold, and reducing product defects.
Coating industry
Improving coverage and whiteness: Caco3 filler masterbatch has high whiteness and coverage. Adding Caco3 filler masterbatch to coatings can improve the coverage of coatings, making the surface of the coated object more uniform and flat. At the same time, it can also increase the whiteness of coatings and enhance their decorative properties. For example, in white latex paint, Caco3 filler masterbatch is an important substitute for white pigments, which can reduce the production cost of the coating while ensuring its coverage and whiteness.
Improving coating performance: Caco3 filler masterbatch can enhance the water resistance, weather resistance, and wear resistance of coatings. Adding an appropriate amount of Caco3 filler masterbatch to coatings can improve their stability in humid environments, reduce fading and powdering during long-term use, and extend their service life. For example, in outdoor architectural coatings, adding Caco3 filler masterbatch can improve the weather resistance of the coating, enabling it to better resist the erosion of natural factors such as ultraviolet radiation and rainwater.
Paper industry
Improving paper performance: In the paper industry, Caco3 filler masterbatch can be used as a filler and coating pigment for paper. Adding Caco3 filler masterbatch can improve the whiteness, opacity, smoothness, and printability of paper. For example, adding Caco3 filler masterbatch to writing and printing paper can make the surface of the paper smoother, improve the ink absorption and printing clarity of the paper, and also reduce the cost of the paper.
Improving paper strength: An appropriate amount of Caco3 filler masterbatch can improve the strength of paper to a certain extent, such as tensile strength, tear strength, etc. This is because calcium carbonate particles can be filled between the fibers of the paper, increasing the bonding force between the fibers and thus improving the overall strength of the paper. For example, adding Caco3 filler masterbatch to packaging paper and cardboard can improve the compressive strength and tear resistance of the paper, enabling it to better protect packaging items.