PLA masterbatch, also known as polylactic acid masterbatch, is a biodegradable plastic material mainly composed of polylactic acid (PLA). Polylactic acid is a polyester polymer mainly composed of lactic acid, and its production materials mainly come from renewable resources such as corn and cassava. Therefore, PLA masterbatch is known as a representative of “green plastics”.
Features
Biodegradability
Degradation conditions: Under composting conditions (suitable conditions such as temperature, humidity, microorganisms, etc.), PLA masterbatch products can be completely degraded into carbon dioxide and water within a certain period of time. The specific degradation time is affected by the thickness, shape, and environmental conditions of the product.
Environmental advantages: Compared with traditional petroleum based plastics, PLA masterbatch products will not cause white pollution after disposal, which is in line with the concept of sustainable development.
Physical property
Mechanical properties: PLA masterbatch has good tensile strength and rigidity, but high brittleness and relatively low impact strength. Therefore, toughening agents and other additives are often added during the processing to improve its performance.
Processing performance: PLA masterbatch has a low melting point (generally between 170-180 ℃), a wide processing temperature range, and is easy to process into various products through various processes such as blown film, injection molding, extrusion, etc.
Surface properties: PLA masterbatch products have a smooth surface, high glossiness, good printing adaptability, and decorative properties.
Biocompatibility
PLA masterbatch has good biocompatibility, is non-toxic and harmless, and can be widely used in medical, health and other fields.
Types
PLA (polylactic acid) masterbatch can be classified into various types according to different classification criteria. The following are some common classification methods and corresponding types:
Function
PLA masterbatch for packaging: It has good transparency, heat sealing properties, and mechanical properties, and is suitable for producing various packaging materials such as food packaging, shopping bags, cling film, etc.
Fiber grade PLA masterbatch: With high strength and flexibility, it can be used for the production of clothing fibers, home textile fibers, industrial fibers, etc.
PLA masterbatch for injection molding: with good fluidity and good formability, suitable for injection molding production of various plastic products, such as toys, stationery, tableware, etc.
PLA masterbatch for extrusion: It has good extrusion performance and can be used for extrusion production of pipes, sheets, profiles, etc.
Classified by additives
Toughened PLA masterbatch: Adding toughening agents improves the toughness and impact resistance of PLA, enabling it to maintain good performance even in low temperature environments.
Heat resistant PLA masterbatch: Added heat-resistant additives to increase the thermal deformation temperature of PLA, allowing it to be used at higher temperatures and expanding its application range.
Antibacterial PLA masterbatch: Added antibacterial agents to give PLA antibacterial properties, which can be used in the production of medical products, food packaging, and other products with high hygiene requirements.
Flame retardant PLA masterbatch: Added flame retardant to improve the flame retardant performance of PLA, making it comply with relevant fire safety standards, and can be used for the production of electronic and electrical casings, building materials, etc.
Classified by degradation performance
Fully biodegradable PLA masterbatch: It can be completely degraded into carbon dioxide and water in natural environments, without polluting the environment.
Controllable degradation of PLA masterbatch: By adjusting the formula and processing technology, the degradation rate and time of PLA can be controlled to meet the needs of different application scenarios.
Classified by molecular weight
Low molecular weight PLA masterbatch: With a relatively low molecular weight, it has good flowability and processability, making it suitable for applications that require high processability.
High molecular weight PLA masterbatch: With a high molecular weight, it has high strength, toughness, and heat resistance, but the processing difficulty is relatively high, making it suitable for fields that require high product performance.
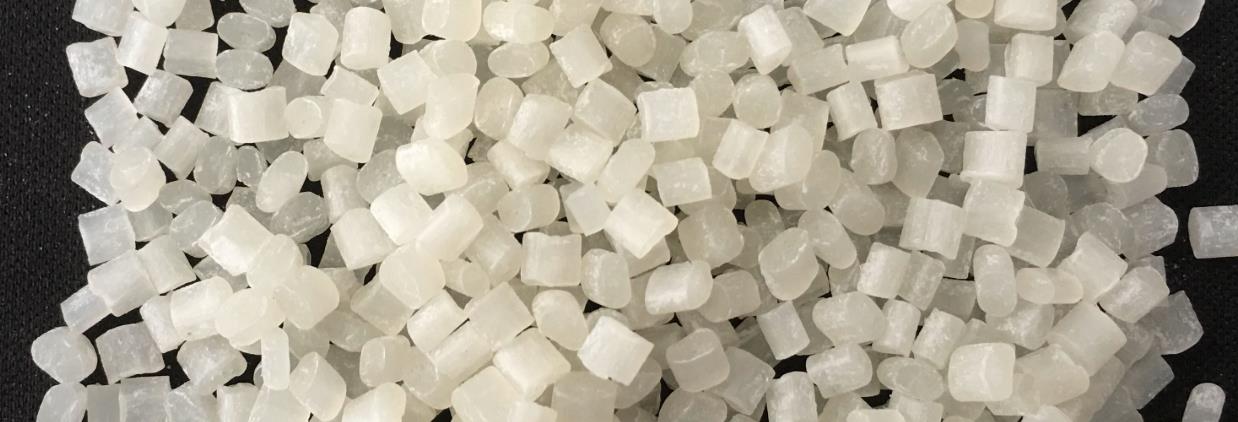
Formula ratio
Fully degradable PLA masterbatch: 60% -74% PLA particles, 10% -13% mixed pigments, 8% -18% dispersants, 6% -12% antioxidants, 2% -5% coupling agents.
Composite toughened polylactic acid degradable masterbatch: 20-60 parts of PLA resin, 10-50 parts of modified plant short fibers, 10-50 parts of modified CaCO Ⅲ particles, 0.5-1.0 parts of lubricant. Preferably, 30-50 parts of PLA resin, 20-40 parts of modified plant short fibers, 20-40 parts of modified CaCO3 particles, and 0.5-1.0 parts of lubricant are used; Further preference is given to 35-45 parts of PLA resin, 25-35 parts of modified plant short fibers, 25-35 parts of modified CaCO3 particles, and 0.6-0.9 parts of lubricant.
PLA soft masterbatch: obtained by melting and extruding PLA particles, fatty amide derivatives, and phosphites in a mass ratio of 73: (24-26): (1.9-2.1).
Antibacterial polylactic acid masterbatch: Mix pure PLA slices with silver loaded zirconium phosphate powder evenly and place them in a twin-screw extruder. The mass fractions of PLA slices and silver loaded zirconium phosphate powder are 80% and 20%, respectively, to make antibacterial masterbatch.
Production process
The production process of PLA masterbatch generally includes steps such as raw material preparation, ingredient mixing, melt extrusion, cooling and cutting, packaging, etc. The following is a specific introduction:
1. Raw material preparation
Select suitable polylactic acid (PLA) resin as the base material, and choose PLA particles with different molecular weights and intrinsic viscosities according to different product requirements. At the same time, prepare various additives such as plasticizers, antioxidants, lubricants, color masterbatch, etc. to improve the performance and appearance of PLA masterbatch.
2. Mixing of ingredients
Accurately weigh PLA resin and various additives according to the designed formula. Put the weighed raw materials into the high-speed mixer for thorough mixing. By stirring, the additive is evenly dispersed on the surface of PLA resin particles to form a premix.
3. Melt extrusion
Add the premix into the hopper of the twin-screw extruder. The twin-screw extruder heats the raw materials in the barrel to above the melting point of PLA through a heating device, gradually melting them. Under the rotation of the screw, the molten material is subjected to shear, compression, and mixing in the barrel, further homogenizing. At the same time, additive addition ports can be set at different positions of the extruder as needed, such as adding some additives that need to be fully effective at high temperatures in the middle of the extruder.
4. Cooling and granulation
The molten material extruded from the extruder die is in a continuous strip shape and cooled through a water tank to rapidly solidify the material. The cooled strip enters the granulator, which cuts the strip into uniform particles according to the set particle size, thus obtaining PLA masterbatch.
5. Packaging
The PLA masterbatch produced is usually packaged in sealed packaging to prevent moisture absorption, oxidation, and other factors that may affect its performance. The packaged PLA masterbatch can be stored in the warehouse or transported to downstream customers for further processing and application.
In the production process, it is necessary to strictly control the process parameters of each link, such as temperature, screw speed, feeding speed, etc., to ensure the quality stability and performance compliance of PLA masterbatch. At the same time, in order to improve production efficiency and product quality, some advanced production equipment and technologies can also be adopted, such as the use of efficient mixing equipment, precision extruder control systems, etc.
Production equipment
1. High speed mixer: used to evenly mix PLA resin with various additives. It achieves sufficient mixing of materials in a short period of time through high-speed rotating stirring blades, ensuring uniform distribution of additives in PLA resin and laying the foundation for subsequent production.
2. Twin screw extruder: It is the core equipment for the production of PLA masterbatch. It has two interlocking screws that rotate under the drive of a motor. There are multiple heating zones on the barrel, which can accurately control the temperature, allowing PLA resin and additives to be fully mixed, plasticized, and homogenized through the shearing, extrusion, and conveying effects of the screw in the heated and melted state, and finally extruded from the mold head.
3. Sink: Usually made of stainless steel material, it is used to cool and solidify high-temperature strip materials extruded from the extruder die. The water temperature in the sink can be precisely controlled by a temperature control system to ensure that the material can cool quickly and achieve good appearance and performance.
4. Granulator: Common types include hot pelletizers and cold pelletizers. Hot cutting machine is used for cutting materials that are in a thermoplastic state and are suitable for temperature sensitive materials; The cold granulator cuts the material after it has cooled and solidified, resulting in particles with regular shapes and uniform sizes. The granulator can precisely control the particle size and shape of PLA masterbatch by adjusting the speed and cutting frequency of the cutting tool.
5. Packaging machine: used for packaging the produced PLA masterbatch. Automatic packaging machines can automate a series of packaging processes such as measurement, filling, and sealing, improving packaging efficiency and quality. Common types include weighing packaging machines and volumetric packaging machines, which can be selected according to the packaging requirements of the product.
In addition to the main equipment mentioned above, auxiliary equipment such as feeders, dehumidifiers, and mold filters may also be used in the production process to improve production efficiency and product quality.
PLA masterbatch extruder
Kerke’s masterbatch extruder can be used to produce PLA masterbatch. Our PLA masterbatch extruder has multiple models to choose from, which can meet different production requirements.
-
Лабораторный двухшнековый экструдер
When will you need a lab twin screw extruder? If you want to make trials and tests of…
-
Параллельный двухшнековый экструдер
Our Parallel Co-rotating twin screw extruder is designed for compounding and masterbatch making with an output capacity from…
-
Тройной (3 винта) Экструдер
3 Screws extruder is a new technology that has many advantages. The triple screw extruder is mainly used…
-
Двухступенчатая система экструзии
Mother-baby extrusion system is designed for special materials which can not process on one stage extruder, the first…
-
Линия для замешивания компаундов Banbury Kneader
Our kneader + extruder is designed for making special applications with an output capacity from 30kg/h to 1000kg/h.…
-
Система резки / Система гранулирования
Different material needs different cutting system, Kerke provides all kinds of cutting system, here is the explanation of…
Related requirements
Good plasticizing ability: PLA resin needs to be fully plasticized during the extrusion process to ensure product quality. Therefore, the extruder should have sufficient heating power and screw design to achieve uniform melting of PLA resin in a short period of time. For example, using a gradient screw with a longer compression section can gradually compress and shear the material during extrusion, achieving a good plasticizing effect.
Accurate temperature control: PLA is sensitive to temperature, and excessive temperature can easily lead to its degradation, affecting its performance; If the temperature is too low, it will cause poor plasticization. The material barrel of the extruder should be equipped with multiple heating zones and a precise temperature control system, which can independently control the temperature of each heating zone to meet the processing temperature requirements of PLA at different stages. Generally speaking, the processing temperature range of PLA is between 160-220 ℃, and the specific temperature needs to be adjusted according to the model and formula of PLA.
Stable extrusion pressure and flow rate: In order to ensure the quality stability of PLA masterbatch, the extruder needs to provide stable extrusion pressure and flow rate. This requires the screw design of the extruder to be reasonable, the transmission system to be stable, and the ability to maintain consistency in extrusion pressure and flow rate at different production speeds. For example, adopting a new type of screw head design can improve the flow uniformity of materials during extrusion and reduce pressure fluctuations.
Strong mixing and dispersing ability: Due to the addition of various additives such as plasticizers, antioxidants, color masterbatch, etc. during the production of PLA masterbatch, extruders need to have strong mixing and dispersing ability to evenly disperse the additives in PLA resin. Special mixing elements such as toothed discs, kneading blocks, etc. can be installed on the screw to increase the shear and mixing effect of the material and improve the dispersion uniformity of the additive.
Corrosion resistance: During the production process of PLA masterbatch, certain additives may have certain corrosiveness, so the components in contact with the material such as the extruder barrel and screw should have good corrosion resistance. These components are typically manufactured using stainless steel or materials that have undergone special surface treatments to extend the lifespan of the extruder.
Приложение
PLA masterbatch has good biodegradability, thermal stability, and processability, so it has a wide range of applications in multiple fields. The following are some of the main application areas:
Packaging field
Disposable tableware: PLA masterbatch can be made into various shapes of tableware, such as plates, boxes, spoons, etc. It can gradually degrade in the natural environment after use, reducing white pollution and complying with environmental protection concepts.
Food packaging: Due to the excellent barrier properties and hygiene performance of PLA masterbatch, it can be used in the production of food packaging bags, boxes, etc. It can effectively maintain the freshness and quality of food, while being biodegradable after disposal, without causing long-term harm to the environment.
Shopping bag: A shopping bag made from PLA masterbatch, which has high strength and can withstand certain weight of items. Moreover, its biodegradable properties make it an ideal alternative to traditional plastic bags, helping to reduce the generation of plastic waste.
Textile field
Clothing: PLA masterbatch can be spun into fibers for making clothing. PLA fiber has a soft hand feel, good moisture absorption and UV resistance, making it comfortable to wear. At the same time, it also has natural wrinkle resistance, which keeps clothes in good appearance.
Home textiles: In home textile products such as bedding and curtains, fibers made from PLA masterbatch are becoming increasingly popular. It not only provides a comfortable user experience, but also adds environmentally friendly elements to the home environment.
Medical field
Suture: PLA masterbatch has good biocompatibility and degradability, and can be used to make sutures. After the wound heals, the suture can gradually degrade and be absorbed by the human body without the need for suture removal, reducing the patient’s pain and risk of infection.
Tissue engineering scaffold: PLA masterbatch can be used to prepare tissue engineering scaffolds, providing support for cell growth and tissue repair. Its biodegradability allows the stent to gradually disappear after tissue repair, avoiding the hassle of secondary surgical removal.
Drug sustained-release carrier: Encapsulating drugs in microspheres or nanoparticles made of PLA masterbatch can achieve slow drug release, prolong drug action time, and improve drug efficacy.
Agriculture
Agricultural film: Agricultural film made from PLA masterbatch has good insulation, moisture retention, and transparency properties, which can promote the growth of crops. Moreover, after use, the agricultural film can naturally degrade in the soil and will not remain in the soil like traditional agricultural films, affecting soil structure and crop growth.
Seedling bowl: A seedling bowl made of PLA masterbatch, which can be directly buried in the soil during seedling transplantation without the need to remove it, reducing damage to the seedling roots and avoiding the problem of recycling and disposal of seedling bowls.