TPU masterbatch is a new polymer material composed of a high proportion of pigments and thermoplastic polyurethane elastomers (TPU) that are well dispersed, extruded, and pelletized. The resin selected for TPU masterbatch has good wetting and dispersing effects on coloring agents, and has good compatibility with the colored material. TPU itself has excellent characteristics of high tension, high tensile strength, toughness, and aging resistance, making it a mature environmentally friendly material.
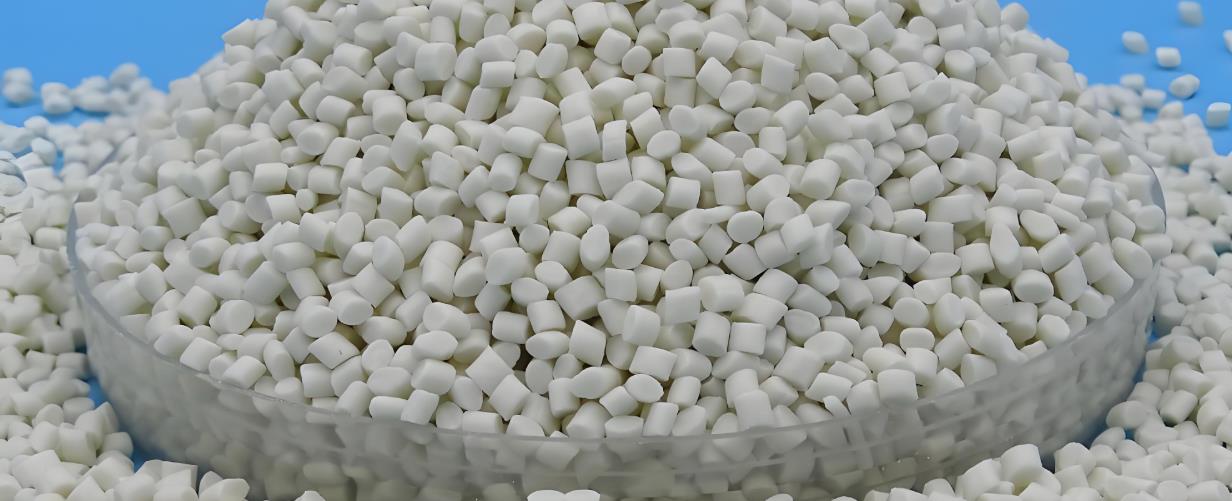
Classification
TPU masterbatch, also known as thermoplastic polyurethane elastomer masterbatch, can be classified into various types according to different classification standards. The following are some common classification methods and specific types:
Classified by soft segment structure
Polyester TPU masterbatch: The soft segment is composed of polyester polyols. It has high strength, wear resistance, and oil resistance, as well as good hydrolysis resistance and low-temperature performance, making it suitable for manufacturing products that require high strength and wear resistance, such as shoe soles, automotive interior parts, etc.
Polyether TPU masterbatch: The soft segment is composed of polyether polyols. Its outstanding features are excellent hydrolysis resistance, flexibility, and low-temperature performance, which can maintain good performance stability in humid environments. It is commonly used in the manufacture of waterproof and breathable films, wire and cable sheaths, and other products.
Polycaprolactone type TPU masterbatch: The soft segment is based on polycaprolactone polyol. It has good comprehensive performance, good biocompatibility, low-temperature flexibility, and processing performance, and can be applied in the medical field, such as medical catheters, artificial organs, etc. It can also be used in products that require environmental friendliness.
Classified by hardness
Low hardness TPU masterbatch: The hardness is usually below Shore A 60. Featuring softness and good elasticity, with a comfortable touch, it is suitable for manufacturing products that require a soft touch, such as phone cases, yoga mats, etc.
Medium hardness TPU masterbatch: hardness between Shore A 60-90. This type of TPU masterbatch has a relatively balanced comprehensive performance, with certain strength and wear resistance, as well as good elasticity and flexibility. It has a wide range of applications and can be used to manufacture sports shoe soles, automotive seals, etc.
High hardness TPU masterbatch: The hardness is above Shore A 90, and can even reach around Shore D 80. It has high rigidity, strength, and wear resistance, and can replace some engineering plastics. It is used to manufacture products that require extremely high hardness and wear resistance, such as gears, bearings, etc.
Classification by function
Flame retardant TPU masterbatch: Modified by adding flame retardants, it has good flame retardant properties and can meet different fire safety standards. It is commonly used in fields such as wires and cables, electronic device casings, etc. that require high fire resistance.
Anti static TPU masterbatch: Added with anti-static agent, the surface resistance is low, which can effectively prevent the accumulation of static electricity and avoid the harm caused by static electricity. It has important applications in electronic component packaging, dust-free workshop supplies, and other fields.
Weather resistant TPU masterbatch: After special formula design and additive modification, it has excellent UV resistance and aging resistance, and can maintain stable performance even after long-term outdoor use. It is suitable for manufacturing outdoor sunshades, automotive exterior parts and other products.
Biodegradable TPU masterbatch: On the basis of ordinary TPU, biodegradable components or structures are introduced to enable it to be decomposed by microorganisms in the natural environment, meeting environmental protection requirements. It can be used in some fields with high requirements for environmental friendliness, such as disposable packaging materials, agricultural films, etc.
Formula ratio
The ratio of different types of TPU masterbatch may vary due to specific performance requirements, application scenarios, and production processes. The following are the approximate ratio ranges and related explanations for some common types of TPU masterbatch:
Polyester TPU masterbatch
Raw material composition and ratio
Polyester polyol: 40% -60%, is the main component that provides soft segments, and its relative molecular weight and structure will affect the performance of TPU. Generally, the relative molecular weight is between 1000-3000.
Isocyanates: 15% -30%, commonly used include toluene diisocyanate (TDI), diphenylmethane diisocyanate (MDI), etc. They react with polyester polyols to form urethane bonds, which are key raw materials determining the structure and properties of TPU hard segments.
Chain extender: 10% -20%, such as ethylene glycol, propylene glycol, butanediol, etc., used to connect polyester polyols and isocyanates to form linear polymer chains, improving molecular weight and polymer strength.
Additives: 0.5% -5%, including antioxidants, light stabilizers, lubricants, etc., used to improve the processing performance, weather resistance, and stability of TPU.
Polyether TPU masterbatch
Raw material composition and ratio
Polyether polyols: 45% -65%, as the main component of the soft segment, the relative molecular weight of polyether polyols is usually between 2000-4000, giving TPU good flexibility, hydrolysis resistance, and low-temperature performance.
Isocyanate: 15% -30%, similar to polyester TPU, commonly used MDI or TDI, etc. Its dosage is determined based on the hydroxyl content of the polyether polyol and the required hard segment content.
Chain extenders: 10% -20%, can be amine extenders such as ethylenediamine, diethylenetriamine, or alcohol extenders, selected according to specific polyether structure and performance requirements.
Additives: 0.5% -5%, similar to polyester TPU, adding antioxidants, light stabilizers, etc. to improve product performance.
Flame retardant TPU masterbatch
Raw material composition and ratio
Basic TPU: 70% -90%, can be polyester or polyether TPU, providing basic mechanical and processing properties as a matrix.
Flame retardant: 10% -30%, choose suitable flame retardants according to different flame retardant requirements, such as phosphorus based flame retardants, halogen based flame retardants, nitrogen based flame retardants, etc., or use compound flame retardants to achieve better flame retardant effect and comprehensive performance.
Synergistic agent: 0-5%, such as antimony trioxide, when used in combination with flame retardants, can improve flame retardant efficiency, reduce the amount of flame retardants used, and improve certain properties of the material.
Anti static TPU masterbatch
Raw material composition and ratio
Basic TPU: 80% -95%, made of polyester or polyether TPU.
Antistatic agent: 5% -20%. Commonly used antistatic agents include quaternary ammonium salts, sulfonic acid salts, polyethers, etc. The amount added depends on the required antistatic grade and the performance of the basic TPU.
Weather resistant TPU masterbatch
Raw material composition and ratio
Basic TPU: 85% -95%, can be various types of TPU.
Light stabilizers: 0.5% -5%, such as hindered amine light stabilizers (HALS), UV absorbers, etc., can effectively absorb or quench UV radiation, preventing TPU molecular chains from degrading under light.
Antioxidant: 0.5% -5%, synergistically works with light stabilizers to improve the oxidation resistance of TPU and prevent it from aging due to oxidation during long-term use.
It should be noted that the above ratio is only a rough range, and in actual production, it needs to be optimized and adjusted according to specific product requirements, production equipment, and processes to obtain TPU masterbatch products with excellent performance.
Production process
The production process of TPU masterbatch mainly includes two methods: pre polymerization method and one-step method. The following are their specific introductions:
prepolymer process
1. Raw material preparation: Accurately weigh polyester polyols, polyether polyols, isocyanates, chain extenders, and various additives and other raw materials. The purity and quality of raw materials are crucial to product performance, and must be strictly selected and inspected according to formula requirements.
2. Prepolymerization reaction: Polyester polyols or polyether polyols are put into a reaction vessel and subjected to vacuum dehydration treatment at a certain temperature (usually 110-120 ℃) to remove moisture from the raw materials. Then isocyanate is added, and a pre polymerization reaction is carried out under stirring conditions. The reaction temperature is controlled at 80-100 ℃, and the reaction time depends on the type of raw material and product requirements, usually 2-4 hours, to generate a pre polymer containing terminal isocyanate groups.
3. Chain extension reaction: Transfer the prepolymer to another reaction vessel, add a chain extender, and perform a chain extension reaction at a certain temperature (such as 70-90 ℃) to further increase the molecular chain and form TPU polymer with certain molecular weight and properties. The reaction time for chain extension is usually 1-3 hours.
4. Post processing: After the reaction is complete, the TPU polymer is extruded into pellets through an extruder, and after water or air cooling, TPU masterbatch is obtained. During the granulation process, appropriate additives such as antioxidants and light stabilizers can be added as needed to improve the performance and stability of the product.
one-step method
1. Raw material mixing: Accurately weigh polyester polyols, polyether polyols, isocyanates, chain extenders, and additives according to the formula ratio, and put them into a high-speed mixer for thorough mixing.
2. Reactive extrusion: The mixed raw materials are directly added to a twin-screw extruder. Under the heating and shearing action of the extruder, chemical reactions occur between the raw materials, completing the synthesis and extrusion granulation process of the polymer. The temperature distribution of the extruder is crucial, generally increasing gradually from the feeding section to the head, and the temperature of each section is controlled between 150-220 ℃. During the extrusion process, by controlling parameters such as screw speed and raw material feed rate, the reaction is fully carried out to obtain TPU masterbatch with stable performance.
3. Cooling granulation: The extruded TPU melt is extruded into strips through a die, then cooled and shaped by a water or air cooling device, and then cut into particles of the desired size by a granulator to obtain TPU masterbatch.
Both processes have their own advantages and disadvantages. The pre polymerization production process is relatively easy to control, with stable product quality, and is suitable for producing high-performance, high value-added TPU products. However, the process flow is long and the equipment investment is large. The one-step process is simple, efficient, and cost-effective, but it requires high raw materials and is difficult to control the production process. It is suitable for producing TPU products with ordinary performance.
Production equipment
The equipment for producing TPU masterbatch mainly includes reaction vessels, extruders, mixers, etc. The following is a specific introduction:
Reaction equipment
Reactor: Used for pre polymerization and chain extension reactions in pre polymerization production. Usually equipped with stirring devices, heating and cooling systems, to ensure that the reaction takes place at the desired temperature and under uniform material mixing conditions. The material of the reaction kettle is generally stainless steel, which can withstand certain pressure and temperature, and has good corrosion resistance.
Vacuum system: matched with the reaction kettle, used to create a vacuum environment during the dehydration and reaction process of raw materials, remove moisture and small molecule by-products generated by the reaction, and improve product quality.
Mixing equipment
High speed mixer: used for mixing raw materials in one-step production, which can achieve uniform mixing of polyester polyols, isocyanates, chain extenders, additives and other raw materials in a short period of time. It has high-speed rotating stirring blades that achieve thorough mixing of materials through strong stirring.
Static mixer: can be installed at the feed inlet or barrel of the extruder to further enhance the mixing effect of materials during the extrusion process, make the reaction more uniform, and improve product consistency.
Extrusion granulation equipment
Twin screw extruder: It is one of the key equipment for TPU masterbatch production, which needs to be used in both pre polymerization and one-step methods. It has two interlocking screws that can provide strong shear force and conveying capacity, allowing materials to be fully mixed, reacted, and plasticized during the extrusion process. By adjusting parameters such as screw speed, temperature distribution, and feeding rate, the quality and performance of the product can be controlled.
Granulator: Used in conjunction with an extruder, it cuts the extruded TPU strips into particles of the desired size. The common cutting methods include hot cutting and cold cutting. The hot cutting method is suitable for high viscosity TPU melt, while the cold cutting method is suitable for materials of various viscosities. The appropriate cutting machine can be selected according to product requirements and production processes.
Auxiliary equipment
Raw material storage tank: used to store polyester polyols, polyether polyols, isocyanates and other raw materials, usually with insulation, stirring and metering functions to ensure the stability and accurate supply of raw materials.
Measurement device: including electronic scales, flow meters, etc., used to accurately measure the input amount of various raw materials, ensuring the stability and consistency of product quality.
Cooling device: such as cooling water tank, air cooling device, etc., used to cool and shape the extruded TPU strip, allowing it to quickly solidify into particles. The cooling effect directly affects the appearance and performance of particles, and it needs to be designed reasonably according to production speed and product requirements.
Packaging equipment: used to package the produced TPU masterbatch, usually including automatic measuring packaging machines, sealing machines and other equipment, which can achieve quantitative packaging and sealed packaging of products, facilitating storage and transportation.
TPU masterbatch extruder
Kerke’s masterbatch extruder can be used to produce TPU masterbatch. Our TPU masterbatch extruder has multiple models to choose from, which can meet different production requirements.
-
Лабораторный двухшнековый экструдер
When will you need a lab twin screw extruder? If you want to make trials and tests of…
-
Параллельный двухшнековый экструдер
Our Parallel Co-rotating twin screw extruder is designed for compounding and masterbatch making with an output capacity from…
-
Тройной (3 винта) Экструдер
3 Screws extruder is a new technology that has many advantages. The triple screw extruder is mainly used…
-
Двухступенчатая система экструзии
Mother-baby extrusion system is designed for special materials which can not process on one stage extruder, the first…
-
Линия для замешивания компаундов Banbury Kneader
Our kneader + extruder is designed for making special applications with an output capacity from 30kg/h to 1000kg/h.…
-
Система резки / Система гранулирования
Different material needs different cutting system, Kerke provides all kinds of cutting system, here is the explanation of…
Related requirements
The production of TPU masterbatch (thermoplastic polyurethane elastomer masterbatch) has special requirements for the extruder in plasticization, mixing, temperature control, etc., as follows:
Plasticizing capacity
Screw design: TPU has high elasticity and viscosity, requiring the screw to provide good plasticizing effect. Usually, a gradient screw is used, which has a longer compression section and can evenly plasticize TPU materials under gradually increasing pressure and temperature. The aspect ratio of the screw is generally between 20-25 to ensure sufficient length for TPU to fully plasticize. In addition, the groove depth and helix angle of the screw also need to be optimized according to the characteristics of TPU. Generally, the groove depth is shallow and the helix angle is large to increase the shear and friction of the material and improve the plasticization efficiency.
Drive power: Due to the high energy consumption required for TPU plasticization, the extruder needs to be equipped with a suitable power drive motor. For extruders with an extrusion rate of 50-300 kilograms per hour, the driving power is usually around 15-55 kilowatts to ensure stable rotation of the screw, overcome material resistance, and achieve good plasticizing effect.
Mixed dispersion performance
Efficient mixing element: In order to evenly mix various additives (such as antioxidants, light stabilizers, colorants, etc.) in TPU masterbatch with TPU matrix, efficient mixing elements should be installed on the extruder screw. For example, using barrier type screws or screws with mixing pins can increase the turbulence level of materials and improve the mixing effect. At the same time, multiple kneading blocks are set on the screw, and the combination of kneading blocks at different angles and arrangements is used to achieve multiple shearing and mixing of the material, so that the additive can be uniformly dispersed in TPU.
Strengthening dispersion measures: For some additives that are difficult to disperse, such as nanoscale fillers, the extruder can be equipped with a static mixer. The static mixer is installed inside the barrel or in front of the head of the extruder, which can further enhance the mixing and dispersion effect during the material flow process, ensuring that the additive forms a stable and uniform system in the TPU masterbatch.
Temperature control accuracy
Accurate temperature control system: During the production process of TPU masterbatch, temperature has a significant impact on product quality. The extruder needs to be equipped with a high-precision temperature control system, generally using electric heating or thermal oil heating methods, and monitoring the temperature of each heating section in real time through temperature sensors such as thermocouples or thermal resistors. The temperature control accuracy should be within ± 1 ℃ to ensure that TPU is in a suitable temperature range during melting, mixing, and extrusion processes, and to avoid product performance degradation caused by temperature fluctuations, such as changes in hardness and decreased elasticity.
Cooling system: After TPU masterbatch extrusion, it is necessary to quickly reduce the temperature through a cooling device to prevent masterbatch adhesion and deformation. Extruders are usually equipped with air or water cooling systems to cool the head and extruded masterbatch. The air-cooled system uses a fan to force air flow to remove heat, while the water-cooled system uses circulating water for cooling. The cooling rate can be adjusted according to production speed and masterbatch specifications.
Pressure stability
Stable extrusion pressure: Stable extrusion pressure is a key factor in ensuring the uniformity of TPU masterbatch size and appearance quality. The hydraulic system or mechanical transmission system of the extruder should be able to provide stable pressure output, with pressure fluctuations generally controlled within ± 3%. Stable pressure can maintain a uniform flow rate of the material during extrusion, thereby producing TPU masterbatch with high precision in diameter and length.
Pressure regulating device: In order to adapt to different production processes and product requirements, extruders should have flexible pressure regulating devices. Operators can accurately adjust the extrusion pressure by adjusting the back pressure of the screw, changing the pressure parameters of the hydraulic system, or adjusting the throttle device of the machine head. For example, in the production of TPU masterbatch with different hardness or elasticity, by adjusting the extrusion pressure reasonably, the flowability and molding effect of the material can be optimized, and the quality and performance of the product can be improved.
Material conveying stability
Accurate feeding: The production of TPU masterbatch requires precise control of the amount of various materials added, so the feeding device of the extruder should use high-precision feeding equipment. Common weight loss feeders can accurately transport TPU raw materials, additives, and other materials to the extruder according to the set amount of material added. At the same time, the feeder should have good sealing and stability to prevent material leakage and uneven feeding, ensuring accurate proportioning of materials during the production process.
Screw conveying accuracy: The machining accuracy and assembly quality of screws have a significant impact on the stability of material conveying. The pitch and diameter tolerances of the screw should be controlled within a small range, generally with a pitch tolerance of no more than ± 0.05 millimeters and a diameter tolerance of no more than ± 0.03 millimeters, to ensure that the material can be stably conveyed forward in the screw groove and avoid material retention or fluctuation. In addition, the gap between the screw and the barrel should be uniform and consistent. If the gap is too large, it can easily cause material reflux and affect conveying efficiency; If the gap is too small, it may cause excessive material shearing and screw wear.
Corrosion resistance and wear resistance
Corrosion resistant materials: During the production process of TPU, some corrosive additives such as certain catalysts and additives may be used. Therefore, components such as the barrel and screw of the extruder that come into contact with the material need to be made of corrosion-resistant materials. The barrel is usually protected by lining with stainless steel or spraying a corrosion-resistant coating, while the screw can be made of alloy steel with good corrosion resistance and surface treated, such as hard chromium plating or electroless nickel plating, to improve its corrosion resistance and extend the service life of the equipment.
Wear resistant design: Due to the elasticity and hardness of TPU, it will cause significant wear on the screw and barrel during the extrusion process. In order to improve the wear resistance of the equipment, the surface of the screw and barrel should have high hardness and wear resistance. In addition to selecting suitable materials, special heat treatments such as quenching and tempering can also be applied to the screw and barrel to improve their surface hardness. In addition, wear-resistant liners can be installed in the feeding section and easily worn parts of the barrel for regular replacement and to reduce equipment maintenance costs.
Automated Control and Monitoring
Advanced control system: Modern TPU masterbatch production extruders are typically equipped with advanced automation control systems, such as PLC (Programmable Logic Controller) or DCS (Distributed Control System). These systems can achieve real-time monitoring and precise control of parameters such as temperature, pressure, screw speed, and material flow rate of the extruder. Operators can easily set and adjust production parameters through the human-machine interface (HMI), monitor and manage the production process, and improve production efficiency and product quality stability.
Fault diagnosis and warning: The automation control system should also have fault diagnosis and warning functions. The system can monitor the operating status of equipment in real time. When abnormal situations occur, such as high temperature, abnormal pressure, motor overload, etc., it can promptly issue alarm signals and automatically take corresponding protective measures, such as stopping the machine or reducing production speed. At the same time, the system can also record fault information to help maintenance personnel quickly locate and troubleshoot faults, reduce equipment downtime, and improve production continuity and reliability.
Приложения
TPU masterbatch has good wear resistance, oil resistance, elasticity, and low-temperature performance, so it has a wide range of applications in multiple fields. The following are some of the main application areas:
Shoe material
Sole: TPU masterbatch can be used to produce soles, giving them good elasticity, wear resistance, and tear resistance, providing a comfortable foot feel and a long service life. At the same time, it can also be compounded with other materials such as EVA, rubber, etc. to manufacture shoe soles with different performance characteristics.
Shoe material accessories: used to make shoe heels, buckles, shoelaces and other accessories, utilizing their high strength and good flexibility to increase the durability and aesthetics of shoe materials.
Automotive industry
Automotive Interior: TPU masterbatch can be used to make the skin material for interior parts such as car seat armrests, headrests, instrument panels, etc. It has a soft touch, good scratch resistance, and chemical resistance, which can enhance the comfort and luxury of the car interior.
Automotive exterior: used to manufacture exterior components such as car bumpers, mudguards, and window seals. Due to its excellent weather resistance and impact resistance, it can withstand different weather conditions and external impacts, protect the body of the vehicle, and maintain the integrity of the vehicle’s appearance.
Automotive hoses: TPU masterbatch produced hoses have good oil resistance, corrosion resistance, and flexibility, and can be used for fuel pipes, cooling water pipes, brake oil pipes, etc. in automobiles to ensure the safe and stable operation of automotive piping systems.
Wire and cable
Insulation sheath: TPU masterbatch has good electrical insulation performance, wear resistance, and low temperature resistance, and can be used as an insulation sheath material for wires and cables, protecting the conductors inside the wires and cables from external environmental influences, and improving the service life and safety of wires and cables.
Special cables: In some fields such as robot cables, new energy vehicle charging cables, etc., TPU masterbatch can meet the strict requirements of cables for flexibility, bending resistance, and weather resistance due to its excellent performance.
Thin films and sheets
Packaging film: The film made of TPU masterbatch has good flexibility, transparency, and puncture resistance, and can be used for packaging food, medicine, daily necessities, etc. It can protect products and provide good display effects.
Waterproof and breathable film: TPU film has unique waterproof and breathable properties, which can be used to make waterproof and breathable layers for sportswear, outdoor equipment, etc., allowing clothing to maintain waterproof performance while allowing sweat vapor generated by the human body to be discharged, maintaining comfort.
Sheet: TPU sheet can be used to manufacture various industrial components, gaskets, seals, etc., utilizing its good mechanical properties and chemical resistance to meet the application needs of different industrial fields.
Medical field
Medical tubing: TPU masterbatch has biocompatibility and good flexibility, and can be used to manufacture various medical tubing such as catheters, endotracheal tubes, vascular catheters, etc., ensuring the safe use of medical devices in the human body.
Medical supplies accessories: Used for producing accessories such as casings, handles, buttons, and some components of rehabilitation devices such as prosthetics and orthotics, providing a comfortable user experience and good durability.