PSU masterbatch, also known as polysulfone masterbatch, is a granular concentrate made from polysulfone (PSU) resin as the substrate, with the addition of specific functional additives and fillers. It belongs to a type of functional masterbatch aimed at enhancing the processing performance of PSU materials or endowing them with special functions. PSU masterbatch has a wide range of applications, thanks to the excellent properties of PSU materials themselves, such as high temperature resistance, chemical corrosion resistance, good mechanical properties, and biocompatibility.
Characteristic
1. Excellent heat resistance: PSU masterbatch has a high glass transition temperature and thermal deformation temperature, and can be used for a long time in the temperature range of -100 ℃ to 150 ℃, with a short-term use temperature of up to 180 ℃. In high temperature environments, its mechanical properties, dimensional stability, etc. can be maintained at a good level, and it is not prone to deformation, softening, and other problems.
2. Good mechanical properties: Products made from PSU masterbatch have high strength, stiffness, and toughness, excellent mechanical indicators such as tensile strength and bending strength, as well as good creep resistance. They can maintain stable shape and performance even under long-term load, making them suitable for manufacturing structural components that can withstand large external forces.
3. Excellent electrical insulation performance: PSU has good electrical insulation performance, and its electrical insulation performance is relatively stable under different temperature and humidity conditions, which can effectively prevent current leakage and can be used to manufacture insulation components, circuit boards, etc. in electronic and electrical equipment.
4. Outstanding chemical corrosion resistance: It has good resistance to various chemical substances such as acids, bases, and salts. In conventional chemical environments, its performance will not significantly decrease due to chemical corrosion, and it can be used to manufacture containers, pipelines, valves, and other components that come into contact with chemical media.
5. Good hydrolysis resistance: PSU masterbatch has good stability in humid environments or in contact with water, and is not prone to hydrolysis reactions that can cause performance degradation. It can be used to manufacture products for use in humid or water environments.
6. Flame retardancy: PSU itself has a certain degree of flame retardancy, with low smoke emission during combustion and no toxic or harmful gases produced. It meets relevant fire safety standards and is suitable for occasions with high fire prevention requirements.
7. Transparency: Some PSU masterbatch can be made into transparent or semi transparent products with good optical properties, which can be used to manufacture components that require transparency, such as optical lenses, transparent covers, etc.
8. Good processing performance: PSU masterbatch can be molded through various processing methods such as injection molding, extrusion, blow molding, etc., and can be made into products of various shapes and sizes to meet different application needs. During the processing, it has good fluidity, is easy to fill the mold, and the formed product has high dimensional accuracy and good surface quality.
Types
Classified by molecular structure
Ordinary bisphenol A-type PSU masterbatch: The main chain of the molecule contains isopropyl, ether, sulfone, and phenylene groups. It has excellent antioxidant properties, thermal stability, toughness, and mechanical strength, and is the most common type of PSU.
Polyphenylsulfone (PPSU) masterbatch: The main chain contains a benzene ring, which gives it higher heat resistance and mechanical properties. At the same time, the introduction of ether bonds provides excellent fluidity and processing performance.
Polyether sulfone (PESU) masterbatch: The molecule contains ether and sulfone groups, which have flexibility, high fluidity, and heat resistance. The presence of phenylene provides rigidity.
Classified by functional characteristics
Conductive PSU masterbatch: such as PSU carbon nanotube conductive masterbatch, by adding conductive fillers such as carbon nanotubes, PSU masterbatch has good conductivity and can be used to manufacture products that require anti-static or conductive properties, such as electronic device casings, circuit boards, etc.
Color PSU masterbatch: Made by adding organic or inorganic pigments to PSU masterbatch, different color requirements are achieved by adding different color masterbatch or pigments to meet the appearance requirements of different products.
Enhanced PSU masterbatch: PSU masterbatch with added reinforcing materials such as glass fiber and carbon fiber, such as RTP 905 Z from the United States, which is a 30% glass fiber reinforced PSU masterbatch, and UItrason from BASF in Germany ® S 2010 G6 is also a 30% glass fiber reinforced PSU masterbatch, which can improve the mechanical strength, hardness, and dimensional stability of PSU, and is suitable for applications with high mechanical performance requirements.
Formula ratio
The formula ratios of PSU masterbatch may vary depending on the type. The following are general formula ratios for ordinary bisphenol A PSU, PPSU, PESU, and conductive PSU masterbatch:
Ordinary Bisphenol A-type PSU masterbatch
Polysulfone resin: usually accounting for about 90% -99%, it is the main component of the masterbatch and provides basic properties such as heat resistance, mechanical properties, electrical insulation, etc.
Additives: including antioxidants, lubricants, etc., accounting for approximately 1% -10% of the total. Antioxidants can prevent resin oxidation and degradation during processing and use, improve product stability and service life, and are generally added at a dosage of about 0.1% -1%; Lubricants help improve processing performance, reduce melt viscosity, and make materials flow more easily during processing. The amount added is usually around 0.5% -5%.
Polyphenylsulfone (PPSU) masterbatch
Polyphenylsulfone resin: The content is generally around 85% -95%, and it is a key component that determines the properties of the masterbatch, endowing it with high heat resistance, good mechanical properties, and processability.
Reinforcement materials: such as glass fiber, carbon fiber, etc., with an addition amount of about 5% -15%. Adding glass fiber can improve the strength, stiffness, and dimensional stability of the masterbatch; Carbon fiber can improve the conductivity and other properties of the masterbatch while enhancing its strength.
Other additives: anti-aging agent, coupling agent, etc., accounting for about 1% -5%. The anti-aging agent can enhance the anti-aging performance of master batch during long-term use; Coupling agents can enhance the bonding strength between resins and reinforcing materials, thereby better exerting the reinforcing effect.
Polyether sulfone (PESU) masterbatch
Polyether sulfone resin: usually accounting for about 90% -98%, it is the main component of the masterbatch, providing excellent heat resistance, mechanical properties, and electrical insulation for the masterbatch.
Fillers: such as calcium carbonate, talc powder, etc., with an addition amount of about 2% -10%. Adding fillers can reduce costs and improve the hardness, dimensional stability, and processing performance of the masterbatch to a certain extent. For example, calcium carbonate can improve the hardness and rigidity of the masterbatch, while talc powder helps to enhance the size stability and surface smoothness of the masterbatch.
Additives: including heat stabilizers, light stabilizers, etc., accounting for about 1% -5% of the total. Heat stabilizers can prevent resin from decomposing due to heat during processing and use, while light stabilizers can improve the light aging resistance of masterbatch in outdoor environments.
Conductive PSU masterbatch
PSU resin: generally accounts for about 60% -90%, serving as the matrix material for the masterbatch, providing basic mechanical and processing properties.
Conductive fillers: such as carbon nanotubes, graphene, carbon black, etc., with an addition amount of about 10% -40%. These conductive fillers form a conductive network in PSU resin, thereby endowing the masterbatch with conductive properties. Among them, carbon nanotubes and graphene have excellent conductivity and mechanical properties, and the addition amount is relatively low, generally around 1% -10%, which can significantly improve the conductivity of the mother particles; Carbon black has a relatively low price and is usually added in an amount of around 10% -40%.
Dispersant: accounting for about 1-5%. The function of dispersants is to evenly disperse conductive fillers in the resin, improve the stability and consistency of conductivity, and enhance the processing performance of the masterbatch.
It should be noted that the above formula ratios are for general reference only. In actual production, different manufacturers may adjust them based on specific performance requirements, processing technology, and cost factors of the product.
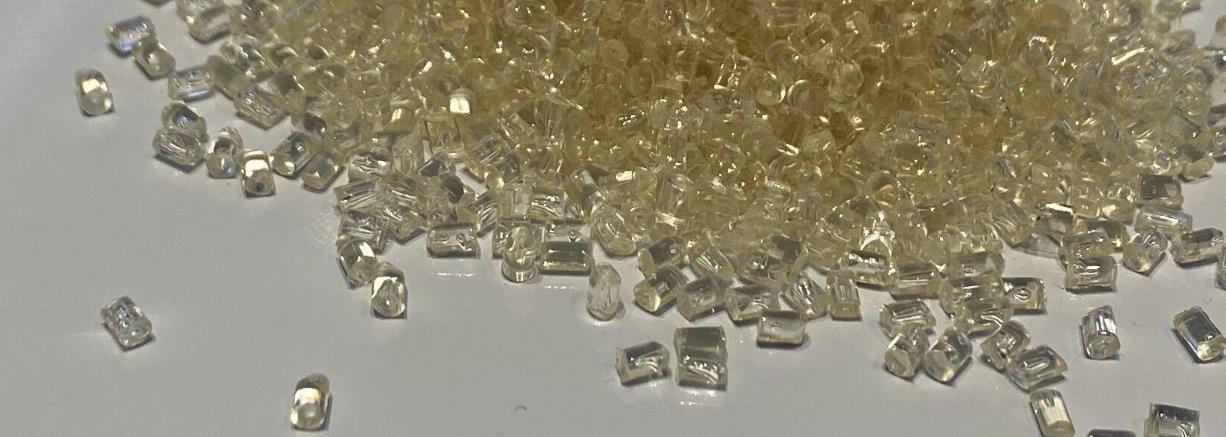
Production process
The production process of PSU masterbatch usually includes the following main steps:
Raw material preparation
Resin selection: Choose the appropriate polysulfone resin based on the type of PSU masterbatch required, such as bisphenol A PSU, PPSU, or PESU. Ensure that the quality of the resin meets production requirements, including molecular weight, molecular weight distribution, purity, and other indicators.
Additive preparation: Prepare various additives according to the formula requirements, such as antioxidants, lubricants, pigments, reinforcing materials, conductive fillers, etc. The quality and particle size distribution of additives need to meet the requirements of the production process.
Mixing of ingredients
Accurate measurement: Using high-precision measuring equipment, accurately weigh polysulfone resin and various additives according to the set formula ratio. For some trace additives, such as antioxidants, coupling agents, etc., special attention should be paid to the accuracy of measurement to ensure the stability of product performance.
Pre mixing: Add the weighed raw materials into a high-speed mixer for pre mixing. By high-speed stirring, the resin and additives are fully in contact and initially mixed evenly, preparing for the subsequent processing. The time and speed of pre mixing are adjusted according to the characteristics of the raw materials and the requirements of the formula.
Melt extrusion
Heating and melting: Add the pre mixed material into a twin-screw extruder. The barrel of the extruder is heated by electric heating or other heating methods to gradually melt the material under the push of the screw. The melting temperature of PSU resin is relatively high, generally around 300-350 ℃, and the specific temperature is adjusted according to the type and formula of the resin.
Screw extrusion: Under the rotation of the screw, the molten material is pushed forward, while the shearing effect of the screw further mixes the material evenly. The parameters such as screw speed and aspect ratio have a significant impact on the mixing effect and extrusion quality of materials. During the extrusion process, an appropriate amount of processing aids can be added as needed to improve the flowability and processing performance of the material.
Filtration and impurity removal: In order to ensure the quality of the product, a filter screen or filter device is usually installed at the head of the extruder to filter the molten materials, remove the impurities and gel particles that may exist in them, and improve the purity of the product.
Cooling pitching
Water or air cooling: The extruded masterbatch passes through the die head and enters the cooling device for cooling and shaping. There are two common cooling methods: water cooling and air cooling. Water cooling is the process of cooling the masterbatch through a water tank, with a fast cooling rate. However, it is important to control the water temperature to prevent the formation of bubbles or cracks on the surface of the masterbatch; Air cooling utilizes air convection for cooling, which is relatively slow but can achieve better surface quality.
Traction cutting: The cooled masterbatch is pulled by a traction device to maintain a certain speed and tension. Then, use a granulator to cut the mother granules into particles of a certain length, and adjust the length of the granules according to the requirements of the product, usually around 2-5mm.
Packaging and storage
Screening and packaging: The cut masterbatch is screened to remove any particles that may be too large or too small, ensuring the uniformity of the product’s particle size. Then, pack the qualified masterbatch into a sealed bag or packaging bag for packaging. During the packaging process, attention should be paid to preventing moisture and contamination of the masterbatch.
Quality inspection: Conduct quality inspection on packaged PSU masterbatch, including testing of appearance, particle size distribution, melt flow rate, mechanical properties, thermal properties, and other indicators. Only products that pass inspection can be stored in the warehouse or delivered to customers for use.
Throughout the entire production process, it is necessary to strictly control various process parameters, such as temperature, pressure, screw speed, cooling rate, etc., to ensure the quality stability and performance compliance of PSU masterbatch. At the same time, the cleanliness and humidity of the production environment can also affect product quality, and it is necessary to maintain a stable and clean production environment.
Production equipment
The production of PSU masterbatch requires various professional equipment, and the following are the main production equipment and their functions:
1. High speed mixer: used to pre mix polysulfone resin with various additives in precise formula ratios. By using high-speed rotating stirring blades, the material can achieve uniform mixing in a short period of time, providing a good raw material foundation for the subsequent melt extrusion process.
2. Twin screw extruder: It is one of the core equipment for PSU masterbatch production. It has two interlocking screws that rotate under the drive of a motor. After entering the extruder from the hopper, the material moves forward under the push of the screw, while being subjected to the shearing, squeezing, and heating effects of the screw, gradually melting and mixing the material evenly. The length to diameter ratio, screw configuration, heating and cooling system and other parameters of twin-screw extruder have a critical impact on the quality and performance of PSU masterbatch.
3. Extruder head and mold: Installed at the front end of the twin-screw extruder, its main function is to extrude the molten material through a specific shaped die hole, forming the desired masterbatch shape and size. The design and processing accuracy of the mold directly affect the appearance quality and dimensional accuracy of the masterbatch.
4. Cooling device: Common cooling devices include cooling water tanks and air cooling systems. The cooling water tank usually uses circulating water to rapidly cool the extruded masterbatch, allowing it to quickly solidify and improve production efficiency. The air-cooled system uses the airflow generated by the fan to cool the masterbatch. The cooling speed is relatively slow, but it can avoid surface defects that may be caused by water cooling, making it suitable for products with high surface quality requirements.
5. Traction device: located after the cooling device, it is used to pull the cooled masterbatch to maintain a certain tension and speed for subsequent cutting operations. The traction device usually consists of traction rollers and drive motors, which can adjust the traction speed according to production needs to ensure the uniformity of the length of the masterbatch.
6. Granulator: used to cut the mother granules pulled over into granules of a specified length. There are many types of pelletizers, commonly including hot cutting and cold cutting. The hot cutting granulator is used to cut while the masterbatch is in a molten state, with fast cutting speed and high production efficiency, but it requires high operational skills; The cold cutting granulator cuts after the mother granules have cooled and solidified, with good cutting quality and regular particle shape, but the production speed is relatively slow.
7. Screening equipment: Screen the cut masterbatch to separate out oversized or undersized particles that do not meet the particle size requirements, ensuring the uniformity of the product’s particle size. Common screening equipment includes vibrating screens, rotating screens, etc. Suitable equipment can be selected based on the particle size range and production scale of the mother particles.
8. Packaging equipment: used to package qualified masterbatch after screening. Packaging equipment includes automatic measuring devices, sealing machines, labeling machines, etc. The automatic measuring device can accurately weigh the weight of each bag of masterbatch. The sealing machine seals the packaging bag to ensure that the product is not affected by moisture or contamination during storage and transportation. The labeling machine attaches a product label to the packaging bag, indicating the product name, specifications, production date, and other information.
9. Raw material storage and transportation equipment: including raw material storage tanks, feeding machines, etc. The raw material storage tank is used to store polysulfone resin and various additives, ensuring a stable supply of raw materials. The feeding machine is responsible for transporting raw materials from the storage tank to the hopper of the high-speed mixer or twin-screw extruder, achieving automated conveying of raw materials, improving production efficiency, and reducing manual operation errors.
10. Quality inspection equipment: such as melt flow rate meter, universal material testing machine, thermogravimetric analyzer, differential scanning calorimeter, etc. The melt flow rate meter is used to measure the melt flow properties of PSU masterbatch and reflect its processing performance; The universal material testing machine can test the mechanical properties of masterbatch, such as tensile strength, elongation at break, etc; Thermogravimetric analyzer and differential scanning calorimeter are used to analyze the thermal stability and thermal transformation behavior of the masterbatch, respectively, to help evaluate the quality and performance of the product.
PSU masterbatch extruder
Kerke’s masterbatch extruder can be used to produce PSU masterbatch. Our PSU masterbatch extruder has multiple models to choose from, which can meet different production requirements.
-
Лабораторный двухшнековый экструдер
When will you need a lab twin screw extruder? If you want to make trials and tests of…
-
Параллельный двухшнековый экструдер
Our Parallel Co-rotating twin screw extruder is designed for compounding and masterbatch making with an output capacity from…
-
Тройной (3 винта) Экструдер
3 Screws extruder is a new technology that has many advantages. The triple screw extruder is mainly used…
-
Двухступенчатая система экструзии
Mother-baby extrusion system is designed for special materials which can not process on one stage extruder, the first…
-
Линия для замешивания компаундов Banbury Kneader
Our kneader + extruder is designed for making special applications with an output capacity from 30kg/h to 1000kg/h.…
-
Система резки / Система гранулирования
Different material needs different cutting system, Kerke provides all kinds of cutting system, here is the explanation of…
Related requirements
In the production of PSU masterbatch, the extruder needs to meet the following requirements:
High temperature control accuracy: The melting temperature of PSU resin is relatively high, generally around 300-350 ℃, and it is sensitive to temperature changes. The extruder needs to be equipped with a high-precision heating and cooling system to ensure that the temperature of each section of the barrel can be accurately controlled within the set range, with a fluctuation range usually required to be within ± 1 ℃, in order to ensure the full melting and stable extrusion of PSU resin and avoid unstable product performance or quality defects caused by temperature fluctuations.
Strong shear mixing ability: In order to fully mix PSU resin with various additives evenly, the screw of the extruder needs to have strong shear and mixing ability. By designing the screw configuration reasonably, such as using special threaded elements, kneading blocks, etc., the shear force and friction force of materials during extrusion can be increased, promoting the mutual mixing and dispersion of materials, and enabling additives to be evenly distributed in the PSU resin matrix, thereby improving the consistency of product performance.
Good material conveying performance: PSU resin has high viscosity in the molten state, and the extruder needs to provide stable and uniform material conveying capacity to ensure the continuity of the production process. The design of the screw should be able to adapt to the transportation of high viscosity materials, avoiding situations such as material accumulation or unstable transportation. At the same time, the drive system of the extruder should have sufficient torque and power to overcome the resistance of the material during the extrusion process, ensuring that the material can be smoothly transported from the hopper to the head.
Wear resistance and corrosion resistance: During the production process of PSU masterbatch, the material is subjected to high temperature, high pressure, and strong shear in the extruder, resulting in significant wear on the screw and barrel. In addition, some additives may be corrosive, so the screw and barrel of the extruder need to be made of wear-resistant and corrosion-resistant alloy materials, such as nitride steel, bimetallic alloys, etc., to extend the service life of the equipment and reduce maintenance costs.
Appropriate aspect ratio: The aspect ratio refers to the ratio of the effective length of a screw to its diameter. For the production of PSU masterbatch, it is usually necessary to choose an extruder with a large aspect ratio, usually between 30-40. A larger aspect ratio can provide longer material retention time and better mixing effect, allowing PSU resin and additives to fully mix and react, which is beneficial for improving product quality and performance. However, a large aspect ratio can also increase the cost and energy consumption of the equipment, so it is necessary to make reasonable choices based on specific production and process requirements.
High degree of automation control: In order to improve production efficiency and product quality stability, extruders should have a high degree of automation control. Equipped with an advanced control system, it can achieve real-time monitoring and automatic adjustment of parameters such as temperature, pressure, screw speed, and feeding amount of the extruder. At the same time, it can also be linked and controlled with other production equipment to achieve automated operation of the entire production process, reduce manual intervention, and improve production reliability and consistency.
Приложение
PSU (polysulfone) masterbatch has excellent characteristics such as high strength, high temperature resistance, chemical corrosion resistance, and good insulation performance, so it has a wide range of applications in multiple fields. The following are some of the main application areas:
Electronic and electrical field
Connector: The connector made of PSU masterbatch has good dimensional stability and insulation performance, which can maintain stable electrical performance in high temperature environments, ensuring the accuracy and reliability of signal transmission.
Integrated circuit packaging: When used for integrated circuit packaging, PSU masterbatch can protect the chip from external environmental influences and has good heat dissipation performance, which helps improve the efficiency and stability of the chip.
Switches and sockets: PSU masterbatch has high flame retardancy and electrical insulation performance, which can meet the safety requirements of electrical accessories such as switches and sockets. At the same time, its high strength and wear resistance can also ensure the service life of the product.
Automotive industry field
Automotive engine components, such as the intake manifold and valve cover of an automotive engine, are made using PSU masterbatch to withstand high temperatures and harsh chemical environments inside the engine compartment, while reducing component weight and improving fuel economy.
Automotive electronic equipment: In the electronic control system of automobiles, PSU masterbatch can be used to manufacture sensor housings, electronic control unit (ECU) housings, etc. It can provide good electromagnetic shielding performance and mechanical protection, ensuring that automotive electronic equipment works normally in complex electromagnetic environments and harsh driving conditions.
Aerospace field
Aircraft interior parts: PSU masterbatch has the characteristics of light weight, high strength, flame retardancy, etc., and can be used to manufacture interior parts such as seat armrests, luggage racks, cabin decorative panels, etc. It can not only reduce the weight of the aircraft, but also improve the aesthetics and safety of the interior.
Aviation electronic equipment: In aviation electronic systems, PSU masterbatch can be used to manufacture the casing and components of electronic equipment, which can meet the high-performance requirements of materials in the aerospace field, such as radiation resistance, fatigue resistance, high temperature resistance, etc., ensuring the reliability and stability of aviation electronic equipment under extreme conditions.
Medical field
Medical devices: PSU masterbatch has good biocompatibility and chemical stability, and can be used to manufacture various medical devices such as syringes, infusion sets, blood dialyzers, etc. It can meet the strict requirements of medical devices for safety and hygiene.
Medical equipment casing: The medical equipment casing made of PSU masterbatch has the characteristics of high strength, wear resistance, and easy cleaning, which can protect the precision components inside the equipment and meet the requirements of medical environment for equipment appearance and hygiene.
Food packaging field
Food containers: PSU masterbatch has the characteristics of non toxicity, odorlessness, and chemical corrosion resistance, and can be used to manufacture food packaging containers, such as food preservation boxes, beverage bottles, etc., which can ensure the quality and safety of food. At the same time, its good transparency and aesthetics can also enhance the market competitiveness of products.
Food packaging film: Packaging film made from PSU masterbatch has good barrier properties, which can prevent substances such as oxygen and water vapor from affecting food and extend the shelf life of food.