PMMA masterbatch is a kind of plastic masterbatch made of polymethyl methacrylate (PMMA) as the basic material. At present, there are many suppliers in the market providing PMMA masterbatch products, such as anti blue light masterbatch, anti-aging masterbatch, etc. These products come in different specifications, performance, and prices to meet the needs of different customers. With the advancement of technology and the expansion of the market, the application fields of PMMA masterbatch will become increasingly wide, and the market demand will continue to grow.
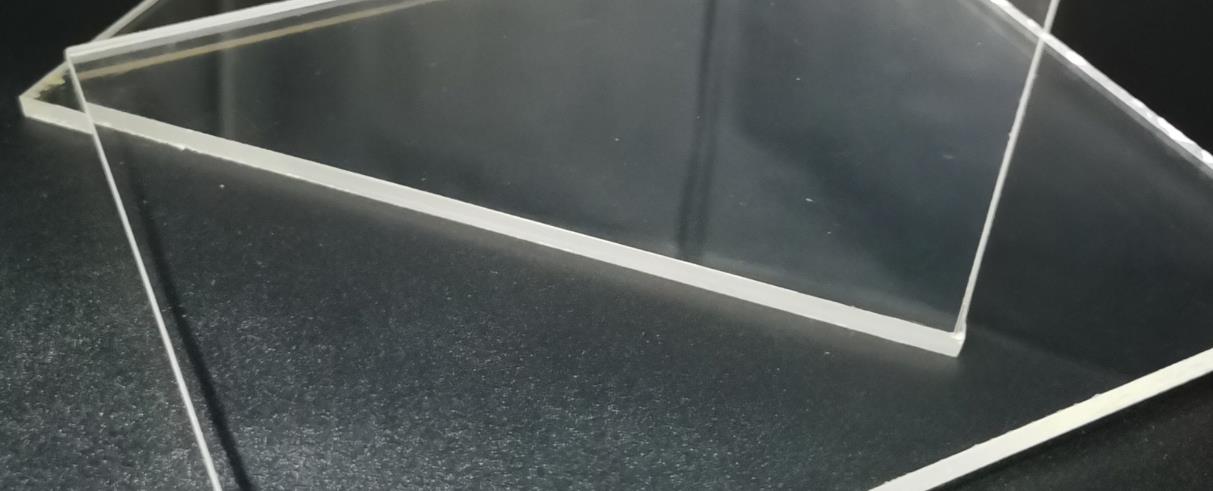
Type
There are various types of PMMA masterbatch, and the following are some common classifications:
Classified by functional characteristics:
Anti static PMMA masterbatch: such as PEBAX 30R51SA01-PMMA transparent anti-static masterbatch, produced by French company Arkema, extracted from bio based castor seeds and polymerized with polyether, can make PMMA products have anti-static properties and can be applied in industries such as food packaging, achieving transparency in PMMA.
Flame retardant PMMA masterbatch: such as OM-D-LR-3 type PMMA halogen-free flame retardant masterbatch, with an effective substance content of 67%, has the characteristics of low smoke emission, non-volatile, and no harmful gas production during combustion. It can be used in injection molding, extrusion, blown film, wire drawing and other processes to endow PMMA products with flame retardancy.
Weather resistant PMMA masterbatch: Added with weather resistant additives, it can improve the ability of PMMA products to resist UV rays, temperature changes, rainwater and other factors in outdoor environments, reduce yellowing, aging and performance degradation, and extend the service life of products. It is commonly used in outdoor billboards, car light housings and other products that require high weather resistance.
High transparency PMMA masterbatch: With excellent optical properties, it can maintain high transparency of PMMA products, approaching or reaching the transparency level of optical grade PMMA. It is commonly used in the manufacturing of optical lenses, display screen protective covers, transparent containers and other products with strict transparency requirements.
Classified by color:
Black PMMA masterbatch: It has good black uniformity and blackening effect, which can effectively improve the quality of plastic products. It is widely used in the automotive industry, home appliance industry, medical equipment and other fields, such as automotive interior parts, exterior parts, TV housings, air conditioning panels, medical equipment, etc., to achieve a uniform black appearance.
Colored PMMA masterbatch: Various colors can be customized according to customer needs, such as red, blue, green, yellow, etc., for the production of PMMA products with different color requirements, such as toys, decorations, stationery, etc.
White PMMA masterbatch: It can make PMMA products appear white, with good coverage and whiteness. It is commonly used in some products that require a white appearance, such as white household appliance shells, building decoration materials, etc.
Classified by application field:
Universal PMMA masterbatch: It has general physical and processing properties and is suitable for the production of most ordinary PMMA products, such as daily necessities, stationery, toys, etc.
Optical grade PMMA masterbatch: It has strict requirements for optical properties, such as high transparency, low haze, and good refractive index uniformity. It is mainly used to manufacture optical products such as optical lenses, light guide plates, and optical fibers.
Medical grade PMMA masterbatch: meets the relevant standards and requirements for medical materials, has good biocompatibility, chemical stability, and hygiene performance, and can be used to manufacture medical devices and supplies such as syringes, infusion sets, dentures, artificial lenses, etc.
Food contact grade PMMA masterbatch: meets the requirements of relevant regulations on food contact, is non-toxic, odorless, chemically stable, and will not migrate harmful substances into food. It can be used to manufacture products that come into contact with food, such as food packaging containers, tableware, and food processing equipment components.
Formula ratio
The ratio of PMMA masterbatch in different applications may vary due to specific product requirements, production processes, and other additives added. Here are some common examples of ratios:
General PMMA products
PMMA masterbatch and pure PMMA resin can usually be mixed in a ratio of 1:9 to 3:7. If certain performance requirements for the product are not particularly high, the content of masterbatch can be relatively low, such as 10% -20%; If you want the product to better reflect the characteristics endowed by the masterbatch, such as color, anti-static, etc., the masterbatch content can be appropriately increased to about 30%. For example, in the production of ordinary PMMA plastic shells, if anti-static PMMA masterbatch is used, in order to achieve good anti-static effect while ensuring reasonable cost, it may be necessary to mix 20% -30% anti-static masterbatch with 70% -80% pure PMMA resin.
Optical grade PMMA products
PMMA masterbatch and optical grade PMMA raw materials: Generally, the amount of optical grade PMMA masterbatch added is relatively small, between 5% and 15%. Because optical grade products require extremely high optical properties such as transparency and refractive index, excessive addition of masterbatch may affect their optical performance. For example, when producing optical lenses, if high transparency PMMA masterbatch is used, in order to ensure the high transparency and precise optical performance of the lens, the amount of high transparency masterbatch added is usually controlled within 10% and mixed with more than 90% optical grade PMMA raw materials.
Medical grade PMMA products
PMMA masterbatch and medical grade PMMA base material: The ratio is usually between 1:9 and 2:8. Medical grade products have strict requirements for safety and performance stability, and the amount of masterbatch added needs to be precisely controlled. Taking the production of medical dentures as an example, if PMMA masterbatch with good biocompatibility is used, in order to ensure that the dentures meet medical standards, a mixture of 10% -20% masterbatch and 80% -90% medical grade PMMA base material may be used.
Food contact grade PMMA products
PMMA masterbatch and food contact grade PMMA resin: Generally, the amount of masterbatch added is around 10% -25%. It is necessary to ensure that the product has corresponding performance, such as good chemical resistance, hygiene, etc., while also ensuring compliance with relevant regulations on food contact. For example, when producing food packaging containers, if PMMA masterbatch with good weather resistance is used, in order to make the packaging container resistant to external environmental influences during storage and transportation, while ensuring food safety, a mixture of 15% -25% weather resistant PMMA masterbatch and 75% -85% food contact grade PMMA resin may be used.
The above ratio is only a rough range, and it needs to be adjusted and optimized according to specific product specifications, production equipment, process conditions, etc. in actual production to achieve the best product performance and quality requirements.
Production process
The production process of PMMA masterbatch usually includes steps such as raw material preparation, mixing, extrusion, granulation, etc. The following is a specific introduction:
1. Raw material preparation
Choose high-purity PMMA resin: Based on product performance requirements, select the appropriate model of polymethyl methacrylate (PMMA) resin as the base material. Its purity and molecular weight distribution will affect the final performance of the masterbatch.
Additive selection: Add corresponding additives based on the functional characteristics of the masterbatch, such as anti-static, flame retardant, weather resistance, etc. For example, anti-static masterbatch requires the addition of anti-static agents, flame retardant masterbatch requires the addition of flame retardants, and weather resistant masterbatch requires the addition of ultraviolet absorbers, hindered amine light stabilizers, and so on. The quality and amount of these additives need to be precisely controlled to ensure the stability of the masterbatch performance.
2. Mixing
Pre mixing: PMMA resin and additives are pre mixed in a high-speed mixer or kneading machine in a certain proportion to evenly disperse the additives on the surface of PMMA resin particles. This step helps to improve the uniformity of the material during the subsequent extrusion process.
Enhanced mixing: For some additives that are difficult to disperse, it may be necessary to use the feeding section of a twin-screw extruder for further enhanced mixing. Under the rotation of the screw, the material is subjected to strong shear and compression in the barrel, causing the additive to mix evenly with PMMA resin.
3. Extrusion
Heating plasticization: After the mixed material enters the extruder, it is gradually heated to the melting temperature of PMMA resin in the heating section of the extruder, usually between 180-230 ℃. At this temperature, PMMA resin transforms from a solid state to a viscous flow state, facilitating subsequent extrusion molding.
Screw extrusion: Under the push of the screw, the molten material moves forward in the extruder barrel. The design parameters of the screw, such as aspect ratio and compression ratio, will affect the extrusion effect and mixing uniformity of the material. Usually, in order to achieve better mixing and extrusion results, a twin-screw extruder with a larger aspect ratio is used.
Filtering: In the extrusion process, a filter screen or filtering device is usually installed at the head of the extruder to remove impurities and undissolved additive aggregates from the material. The filtration accuracy depends on the product requirements and is generally between 20-100 mesh.
4. Granulation
Hot cutting granulation: The extruded strip is cut into uniform particles by a hot cutting device under the action of a rotating tool. The advantages of hot cutting granulation are high production efficiency, regular particle shape, and uniform particle size.
Air cooling or water cooling: The PMMA masterbatch after granulation needs to be cooled to prevent particle adhesion and deformation. There are two common cooling methods: air cooling and water cooling. Air cooling removes heat from the surface of particles through high-speed air flow, while water cooling cools particles through a water tank. The cooling effect of water cooling is better, but attention should be paid to controlling the cooling rate to avoid internal stress in particles.
5. Packaging
Measurement packaging: PMMA masterbatch that has been cooled and screened is measured and packaged according to a certain weight specification. Packaging materials usually use moisture-proof and anti-static packaging bags or barrels to prevent the mother granules from absorbing moisture or being affected by static electricity during storage and transportation, ensuring product quality.
In the production process, it is necessary to strictly control various process parameters, such as temperature, pressure, screw speed, feeding speed, etc., to ensure the stable performance and reliable quality of PMMA masterbatch. At the same time, in order to improve production efficiency and product quality, online detection equipment such as melt flow rate testers, particle size analyzers, etc. can be used to perform real-time detection and monitoring of materials during the production process, adjust process parameters in a timely manner, and ensure the stability and consistency of the production process.
Production equipment
Mixing equipment
High speed mixer: used for preliminary mixing of PMMA resin with various additives. It achieves uniform mixing of materials in a short period of time through high-speed rotating stirring blades, with the advantages of high mixing efficiency and good mixing uniformity.
Kneading machine: suitable for occasions that require more thorough mixing and kneading, such as when it is difficult to mix additives with resins. Its stirring blade has a special shape, which can exert strong shear and extrusion effects on the material, making the additive better dispersed in PMMA resin.
Extrusion equipment
Twin screw extruder: It is a key equipment for the production of PMMA masterbatch. Has good material conveying, mixing, and plasticizing capabilities. The meshing structure of the twin-screw causes strong shear and rubbing effects on the material during extrusion, effectively promoting the uniform mixing of additives and PMMA resin. At the same time, the precise temperature control system ensures that the material is melted and extruded at the appropriate temperature. A twin-screw extruder with a larger aspect ratio is more conducive to improving the mixing uniformity of materials and product quality.
Granulation equipment
Hot cutting granulator: installed at the head of the extruder, when the extruded molten material flows out in a strip shape, the rotating tool of the hot cutting granulator cuts it into granules. This granulation method has high production efficiency, regular particle shape, and good uniformity of particle size.
Air cooling or water cooling system: used to cool the PMMA masterbatch after granulation. The air cooling system generates high-speed air flow through the fan, which takes away the heat on the surface of the particles; The water cooling system allows particles to be cooled through a water tank for better cooling effect, but attention should be paid to controlling the cooling rate to prevent particles from generating internal stress.
Auxiliary equipment
Feeding machine: responsible for conveying PMMA resin and additives to mixing equipment and extruders. Common types include spiral feeders and vacuum feeders, which can be selected according to the production site and material characteristics to achieve automated material transportation and improve production efficiency.
Measurement device: including electronic scales, flow meters, etc., used to accurately measure the amount of PMMA resin, additives, and other materials, ensuring that each component is mixed according to the set ratio, thereby ensuring the stability of product quality.
Screening equipment: After granulation, the masterbatch may have uneven particle size or a small amount of connected particles. Screening equipment such as vibrating screens can screen and grade the masterbatch, separating particles that do not meet the particle size requirements to ensure that the product’s particle size distribution meets the standards.
Packaging machine: used for packaging the produced PMMA masterbatch. Automatic packaging machines are usually used to automate packaging processes such as measurement, filling, and sealing, improving packaging efficiency and quality. At the same time, moisture-proof and anti-static packaging materials are selected to prevent the mother granules from absorbing moisture or being affected by static electricity during storage and transportation.
PMMA masterbatch extruder
Kerke’s masterbatch extruder can be used to produce PMMA masterbatch. Our PMMA masterbatch extruder has multiple models to choose from, which can meet different production requirements.
-
Лабораторный двухшнековый экструдер
When will you need a lab twin screw extruder? If you want to make trials and tests of…
-
Параллельный двухшнековый экструдер
Our Parallel Co-rotating twin screw extruder is designed for compounding and masterbatch making with an output capacity from…
-
Тройной (3 винта) Экструдер
3 Screws extruder is a new technology that has many advantages. The triple screw extruder is mainly used…
-
Двухступенчатая система экструзии
Mother-baby extrusion system is designed for special materials which can not process on one stage extruder, the first…
-
Линия для замешивания компаундов Banbury Kneader
Our kneader + extruder is designed for making special applications with an output capacity from 30kg/h to 1000kg/h.…
-
Система резки / Система гранулирования
Different material needs different cutting system, Kerke provides all kinds of cutting system, here is the explanation of…
Related requirements
The extruder plays a key role in the production of PMMA masterbatch, and the following are some requirements for the extruder:
Screw design
Length to diameter ratio: Generally, a length to diameter ratio between 20-40 is required. A longer aspect ratio helps the material to be fully mixed, plasticized, and homogenized in the extruder, enabling the PMMA resin and additives to be evenly dispersed and improving the quality stability of the masterbatch.
Compression ratio: The compression ratio is usually between 2-4. The appropriate compression ratio can subject the material to appropriate squeezing and shearing during the extrusion process, eliminate air in the material, and improve the compactness and plasticization effect of the material.
Mixed ability
Shear strength: The extruder should have strong shear ability to fully disperse additives in PMMA resin. Through the special design and combination of screws, such as the use of meshing twin-screw, high-strength shear force is generated during rotation, which disperses and evenly distributes the aggregated additive particles in the resin matrix.
Mixing uniformity: Ensuring uniform mixing of materials throughout the entire extrusion process is one of the key requirements. This requires the extruder to have good material conveying and distribution characteristics to avoid material retention or uneven local mixing. Some advanced extruders are equipped with mixing elements, such as static mixers or special screw configurations, which can further improve mixing uniformity.
Temperature control
Temperature control accuracy: During the extrusion process, temperature is crucial for the melting state of PMMA resin and the stability of additives. The temperature control system of the extruder should be able to accurately control the temperature of each heating section, and the temperature control accuracy is generally required to be within ± 1-2 ℃. This can ensure that the material is uniformly plasticized within the set temperature range, avoiding changes in material properties or additive failure caused by temperature fluctuations.
Heating and cooling efficiency: Rapid and effective heating and cooling capabilities are necessary. The heating system should be able to heat the material to the desired melting temperature in a short period of time, while the cooling system should be able to cool the various components of the extruder in a timely manner to prevent overheating. Usually, electric heating or thermal oil heating methods are used, and efficient air or water cooling devices are equipped to achieve precise temperature control.
Material conveying capacity
Stability: The extruder needs to transport materials stably to ensure the continuity of the production process and consistency of product quality. The speed and torque of the screw should be able to be accurately adjusted according to production needs, and remain stable during long-term operation to avoid fluctuations in material conveying volume or material breakage.
Adaptability: Able to adapt to materials with different viscosities and flowability. Due to differences in the types of PMMA resin and the content of additives, the characteristics of the material may vary. The extruder should have certain adaptability, by adjusting screw parameters or adopting special screw structures, to ensure good conveying and extrusion of various materials.
Voltage endurance capability
Head pressure: During the extrusion process, a certain pressure is generated at the head to ensure that the material can be smoothly extruded and formed. The extruder needs to have sufficient pressure resistance ability to withstand the head pressure during normal production process. Generally, the required pressure resistance strength is between 10-30MPa, and the specific value depends on the production process and product requirements.
Sealing performance: Good sealing performance is the key to ensuring the pressure resistance of the extruder. The connection between the barrel, screw, and head of the extruder should adopt a reliable sealing structure to prevent material leakage and prevent external air from entering the extrusion system, which may affect product quality.
Automated control
Parameter monitoring: Equipped with a comprehensive automation control system, it can monitor and record key parameters during the extrusion process in real time, such as temperature, pressure, screw speed, material flow rate, etc. By feeding back these parameters to the control system through sensors and instruments, operators can adjust the parameters in a timely manner according to the actual situation, ensuring that the production process is in the best state.
Fault diagnosis and alarm: The system should have fault diagnosis function, which can automatically detect abnormal situations during equipment operation and issue alarm signals in a timely manner. At the same time, it can accurately determine the type and location of faults, provide quick and effective maintenance guidance for maintenance personnel, reduce equipment downtime, and improve production efficiency.
Приложение
PMMA masterbatch has excellent optical properties, weather resistance, and processability, making it widely used in various fields. The following are some of the main application aspects:
Lighting field
LED lighting: PMMA masterbatch can be used to manufacture LED lampshades, light guide plates, etc. Its high transmittance can effectively improve the light output efficiency of LED, making the light more uniform and soft. At the same time, its good weather resistance ensures that it will not turn yellow or brittle due to lighting and environmental factors during long-term use, extending the service life of LED lighting products.
Home lighting: In home lighting fixtures such as chandeliers and ceiling lights, lampshades made of PMMA masterbatch not only provide good transparency, but also achieve various color and texture effects by adding different additives, meeting the needs of different home decoration styles.
Automotive field
Automotive lighting fixtures: PMMA masterbatch is an important material for manufacturing automotive headlights, taillights, turn signals, and other lighting fixtures. It has excellent optical performance, can accurately control the direction and intensity of light propagation, and has good impact resistance and weather resistance, which can adapt to various complex outdoor environments.
Automotive Interior: PMMA masterbatch can be used to manufacture decorative strips for instrument panels, center consoles, and interior lighting covers in automotive interiors. Its excellent processing performance can achieve various complex shapes and exquisite exterior designs, enhancing the quality and aesthetics of car interiors.
Construction field
Skylight panel: Skylight panels made of PMMA masterbatch have the advantages of high light transmittance, lightweight, and corrosion resistance. They are widely used in roof and wall lighting systems of industrial plants, sports halls, exhibition halls, and other buildings, which can effectively save energy and provide a natural and comfortable lighting environment.
Decorative materials: In architectural decoration, PMMA masterbatch can be used to manufacture various decorative panels, decorative lines, artistic shapes, etc. By adding different pigments and additives, a variety of colors and surface effects can be achieved, such as imitation marble, imitation wood, etc., to meet the needs of different architectural decoration styles.
Electronic and electrical field
Display screen: PMMA masterbatch is an important material for manufacturing optical films and light guide plates for displays such as liquid crystal displays (LCDs) and organic light-emitting diode displays (OLEDs). Its high transmittance and low haze characteristics can improve the brightness and contrast of the display screen, providing users with clear and bright visual effects.
Electrical casing: Some small electrical casings, such as phone cases, tablet cases, headphone cases, etc., are also made using PMMA masterbatch. It has good glossiness and texture, which can enhance the appearance quality of the product, while also possessing certain wear resistance and chemical resistance, protecting internal electronic components.
Medical field
Medical devices: PMMA masterbatch can be used to manufacture the shells or components of medical devices such as syringes, infusion sets, blood bags, etc. Its non-toxic, odorless, and biocompatible characteristics ensure that it will not cause harm to the human body during medical use, and its good transparency facilitates medical staff to observe the internal situation.
Dentures and dental materials: In the field of dentistry, PMMA masterbatch is a commonly used raw material for making dental restoration materials such as dentures and braces. It has good biocompatibility and mechanical properties, can closely adhere to oral tissues, is comfortable and durable, and can be dyed and processed to resemble the color and appearance of natural teeth, achieving a beautiful restoration effect.