PBT masterbatch is an aggregate made by uniformly loading super constant substances such as pigments and additives into resin. When in use, simply mix it with the corresponding resin to obtain the desired color product or achieve a certain functional requirement of the product. PBT masterbatch is widely used in fields such as toothbrush bristles, wigs, spinning, optical cables, modified plastics, household appliance accessories, automotive parts, etc. By adding different types of masterbatch, PBT plastic can be endowed with specific properties such as color, weather resistance, flame retardancy, and toughness.
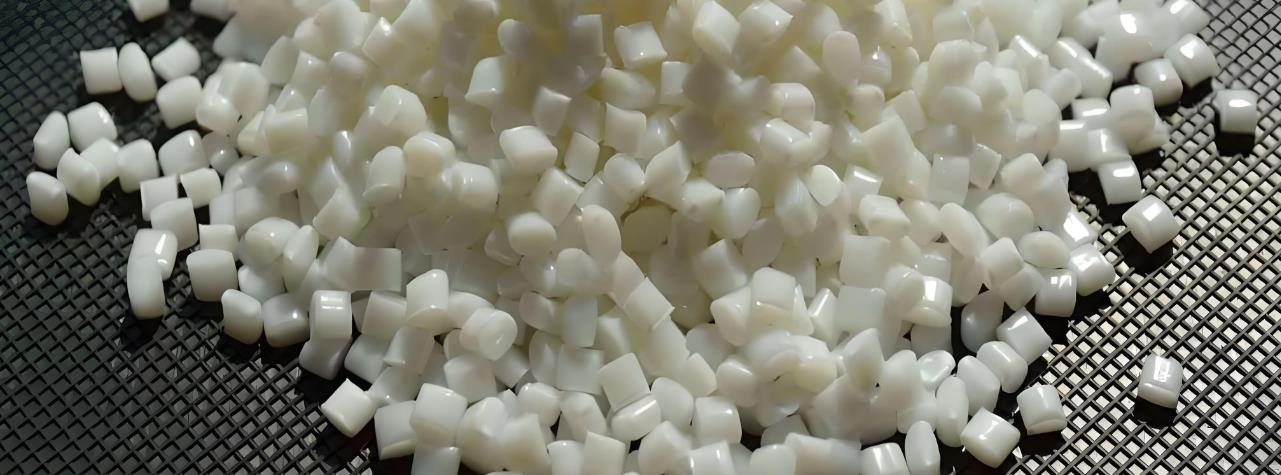
Production process
The production process of PBT masterbatch usually includes the following key steps:
Raw material preparation
PBT resin selection: Select the appropriate type of PBT resin based on product performance requirements, such as high viscosity, low viscosity, or specially modified PBT resin. At the same time, it is necessary to ensure the quality stability of the resin and that the moisture content meets the requirements. Generally, the moisture content should be controlled below 0.05% to avoid adverse reactions such as hydrolysis during the processing.
Additive preparation: Accurately weigh various additives according to the formula, such as flame retardants, toughening agents, antioxidants, pigments, etc. The quality and amount of additives directly affect the performance of PBT masterbatch. For example, the amount of flame retardant added needs to be precisely adjusted according to the required flame retardant level, generally between 5% and 30%.
Mixing of ingredients
Pre mixing: Pre mix PBT resin and additives in the feeding section of a high-speed mixer or twin-screw extruder, so that the additives can be initially uniformly dispersed in the PBT resin. The pre mixing time is usually 5-15 minutes, depending on the characteristics of the material and the performance of the mixing equipment.
High speed mixing: further mixing is carried out using a high-speed mixer, and the material is mixed more evenly in a short period of time through a high-speed rotating stirring blade. The mixing speed is generally between 500-1500 revolutions per minute, and the mixing time is 10-30 minutes.
Extrusion granulation
Melt extrusion: The mixed material is added to a twin-screw extruder and heated to the melting temperature of PBT through the extruder’s heating system, typically between 230-250 ℃. At the same time, the rotation of the screw causes the material to be subjected to shear and pressure inside the barrel, further mixing and plasticizing evenly. The screw speed of the extruder is usually between 100-500 revolutions per minute, adjusted according to the characteristics of the material and production efficiency.
Filtering: In the extrusion process, in order to remove impurities and unmelted particles from the material, it is necessary to filter through a filter screen or filtering device. The mesh size of the filter is generally between 80-200 mesh, and should be selected according to the product quality requirements.
Granulation: The filtered molten material is extruded from the die of the extruder to form continuous strips or filaments, and then cooled and shaped by air or water cooling. The cooled strip-shaped or filamentous material is then cut into particles of the desired size by a granulator, namely PBT masterbatch. The speed of the granulator and the selection of the cutting tool will affect the particle size and shape of the masterbatch. Generally, the particle size of the masterbatch is between 2-5 millimeters.
Drying process
Moisture removal: Due to the possibility of PBT masterbatch absorbing a certain amount of moisture during production, drying treatment is required to ensure its performance and quality. The drying temperature is generally between 120-150 ℃, and the drying time is 2-4 hours to reduce the moisture content of the masterbatch to below 0.05%. Common drying equipment includes hot air circulation drying oven, boiling dryer, etc.
Packaging and storage
Packaging: The dried PBT masterbatch is packaged in plastic or paper bags and then placed in a sealed outer packaging box to prevent the masterbatch from absorbing moisture and being contaminated during storage and transportation. The packaging specifications are generally determined according to customer needs, commonly including 25kg/bag or ton bag packaging.
Storage: PBT masterbatch should be stored in a dry, ventilated environment, away from direct sunlight and moisture. It is best to control the storage temperature between 10-30 ℃ to prevent changes in the properties of the masterbatch.
Production equipment
The PBT masterbatch production equipment mainly includes reaction devices, material processing, and auxiliary equipment. The following is a specific introduction:
Reaction device
Esterification reactor: It is the core equipment for esterification reaction, usually made of stainless steel material, with good corrosion resistance and heat transfer performance. Usually equipped with a stirrer, terephthalic acid (PTA) or dimethyl terephthalate (DMT) is thoroughly mixed with 1,4-butanediol (BDO) and reacted. At the same time, there are heating and cooling systems that can accurately control the reaction temperature at around 180-250 ℃ to meet the conditions of esterification reaction.
Condensation reactor: used for condensation reaction after esterification reaction, which needs to be carried out at higher temperature and vacuum degree. The materials are mostly stainless steel or nickel based alloys, which can withstand high temperatures and high vacuum environments. Equipped with a stirrer and precise temperature control system, the reaction temperature is generally controlled at 230-260 ℃, and the vacuum degree needs to reach 10-100Pa to promote the growth of molecular chains and generate PBT resin.
Material handling equipment
Feeding system: including raw material storage tanks, measuring devices, and conveying pipelines. The raw material storage tank is used to store PTA, DMT, BDO and other raw materials. The measuring device can accurately control the feeding amount of raw materials to ensure that they enter the reaction kettle according to a certain ratio. The conveying pipeline uses corrosion-resistant pipes to transport raw materials from the storage tank to the reaction vessel.
Extruder: Common types include single screw extruder and twin-screw extruder. Twin screw extruder is more commonly used in PBT masterbatch production due to its good mixing effect and strong material conveying capacity. It can heat the reacted PBT resin to a molten state and push the material forward through the rotation of the screw, while achieving further mixing and plasticization of the material. The temperature of the extruder is controlled at around 200-250 ℃, and the screw speed and aspect ratio can be adjusted according to different product requirements.
Granulator: Installed at the outlet of the extruder, it cuts the extruded PBT resin strip into uniform particles. Common types include hot cutting granulators and cold cutting granulators. Hot cutting granulators cut materials while they are in a molten state, and then cool and shape the particles through air or water cooling; The cold granulator first cools the extruded resin strip to room temperature, and then cuts it to obtain particles with regular shapes and smooth surfaces.
Auxiliary equipment
Drying equipment: PBT masterbatch is prone to absorbing moisture during the production process, which affects product quality. Therefore, drying equipment is required for drying treatment. The commonly used ones are vacuum drying oven and hot air circulation drying oven. The vacuum drying oven reduces the pressure inside the oven to evaporate moisture at a lower temperature, resulting in good drying effect and effective removal of moisture from PBT masterbatch, preventing hydrolysis and other problems during subsequent processing; The hot air circulation drying oven uses hot air circulation to dry materials, with a temperature generally controlled at 120-150 ℃. The drying time depends on the moisture content of the material and the performance of the drying equipment, usually 2-8 hours.
Vacuum system: provides a high vacuum environment for condensation reaction, mainly composed of vacuum pump, vacuum pipeline, and vacuum valve. The pumping capacity of the vacuum pump needs to be selected according to the volume and process requirements of the reaction vessel. Generally, it is required to be able to pump the vacuum degree inside the reaction vessel to 10-100Pa. The vacuum pipeline is made of stainless steel material and tightly connected to ensure the sealing of the system.
Cooling system: used to cool equipment such as reaction vessels and extruders, ensuring that the equipment operates within the normal temperature range. The cooling system usually consists of cooling water pumps, cooling towers, cooling pipelines, etc., which take away the heat generated by the equipment through circulating cooling water. The cooling water temperature is generally controlled at 20-30 ℃ to ensure the cooling effect.
PBT Masterbatch Extruder
Kerke’s masterbatch extruder can be used to produce PBT masterbatch. Our PBT masterbatch extruder has multiple models to choose from, which can meet different production requirements.
-
Лабораторный двухшнековый экструдер
When will you need a lab twin screw extruder? If you want to make trials and tests of…
-
Параллельный двухшнековый экструдер
Our Parallel Co-rotating twin screw extruder is designed for compounding and masterbatch making with an output capacity from…
-
Тройной (3 винта) Экструдер
3 Screws extruder is a new technology that has many advantages. The triple screw extruder is mainly used…
-
Двухступенчатая система экструзии
Mother-baby extrusion system is designed for special materials which can not process on one stage extruder, the first…
-
Линия для замешивания компаундов Banbury Kneader
Our kneader + extruder is designed for making special applications with an output capacity from 30kg/h to 1000kg/h.…
-
Система резки / Система гранулирования
Different material needs different cutting system, Kerke provides all kinds of cutting system, here is the explanation of…
The production of PBT masterbatch requires the following specifications for the extruder:
Plasticizing capacity
High melting temperature: PBT has a high melting point, generally between 220-230 ℃, which requires the heating system of the extruder to provide sufficient heat to enable the PBT resin to reach a molten state in a short period of time, and the temperature control accuracy should be high, usually controlled within ± 1 ℃, to ensure the melting quality and stability of PBT.
Good plasticization uniformity: The screw design of the extruder needs to ensure that PBT resin can be fully and uniformly mixed and plasticized during the melting process, reduce temperature and viscosity differences of materials, avoid local overheating or poor plasticization, and thus ensure the quality stability of PBT masterbatch. For example, using a gradient screw, the depth of the screw groove gradually becomes shallower, causing the material to experience increasing shear and pressure during extrusion, achieving a good plasticizing effect.
Mixing performance
Efficient additive dispersion: When producing PBT masterbatch, various additives such as flame retardants, toughening agents, antioxidants, etc. are usually required to be added. The extruder needs to have good mixing performance to evenly disperse these additives in the PBT resin matrix. For example, using screws with mixing elements such as pin screws, static mixers, etc., can increase the mixing effect of materials during extrusion, fully mix additives with PBT resin, and ensure the consistency of masterbatch performance.
Accurate metering control: The amount of additives added needs to be precisely controlled to ensure that the performance of PBT masterbatch meets the requirements. The measuring system of the extruder should have high accuracy and be able to accurately transport various materials to the extruder according to the formula ratio. High precision metering pumps or weight loss feeders are generally used to precisely control the flow rate of materials, with errors controlled within ± 1%.
Extrusion stability
Stable pressure and flow rate: In the production process of PBT masterbatch, the extruder needs to maintain stable extrusion pressure and flow rate to ensure the dimensional accuracy and appearance quality of the masterbatch. Stable pressure can evenly extrude materials in the mold, avoiding problems such as uneven discharge, bubbles, and deformation. By using high-performance hydraulic systems or variable frequency speed control systems, the screw speed and back pressure of the extruder are precisely controlled, so that the fluctuations in extrusion pressure and flow rate are controlled within a small range.
Long term continuous operation: In order to meet the needs of large-scale production, extruders need to have the ability to operate continuously and stably for a long time. This requires the key components of the extruder, such as screws, barrels, etc., to have good wear resistance and corrosion resistance, and to be able to operate stably for a long time in high temperature and high pressure working environments. At the same time, the lubrication system, cooling system, etc. of the extruder should also be reliable to ensure the normal operation of the equipment.
Adaptability
Processing of different formulas: PBT masterbatch has various formulas, and different types and proportions of additives may be added according to different application requirements. The extruder needs to be able to adapt to the processing requirements of different formulations, and achieve efficient production of PBT masterbatch for various formulations by adjusting screw combinations, process parameters, etc. For example, for PBT masterbatch with high filling amount of glass fibers, special screw design and processing technology are required to avoid excessive breakage of glass fibers and excessive shearing of materials.
Product specification adjustment: The product specifications of PBT masterbatch, such as particle size, shape, etc., may vary due to customer needs. The extruder needs to be easily adjustable to meet the production requirements of different specifications of products. For example, by replacing different molds and adjusting parameters such as traction speed, precise control of the particle size and shape of the mother particles can be achieved.
Type
There are various types of PBT masterbatch, and the following are common classifications:
Classified by additive type
Enhanced PBT masterbatch: Adding reinforcing materials such as glass fiber and carbon fiber can significantly improve the mechanical strength, rigidity, and heat resistance of PBT. For example, PBT masterbatch with 30% glass fiber added can achieve a tensile strength of over 100MPa and a heat deformation temperature of over 220 ℃. It is commonly used in the manufacturing of products with high strength and heat resistance requirements, such as automotive engine components and electronic and electrical casings.
Flame retardant PBT masterbatch: Added flame retardants such as bromine based flame retardants, phosphorus based flame retardants, etc., to give PBT good flame retardant properties. According to different flame retardant standards and requirements, its flame retardant rating can reach UL94 V-0 level, V-1 level, etc. This type of masterbatch is commonly used in electronic appliances, wires and cables, and other fields to improve product safety.
Toughened PBT masterbatch: By adding toughening agents such as elastomers, the toughness and impact resistance of PBT are improved. Even in low-temperature environments, it can maintain good flexibility and impact strength, and can be used to manufacture products such as automotive interior parts, wire and cable sheaths that require a certain degree of flexibility.
Classified by application field
PBT masterbatch for electronic appliances: It has excellent electrical insulation performance, heat resistance, and formability. It has high volume resistivity, low dielectric constant and dielectric loss tangent, which can meet the strict electrical performance requirements of electronic and electrical products. It is commonly used in the manufacturing of electronic and electrical components such as sockets, switches, and coil frames.
PBT masterbatch for automotive industry: It needs to have high strength, high heat resistance, weather resistance, and chemical corrosion resistance. For example, PBT masterbatch used to manufacture automotive radiator grilles should be able to maintain color stability and mechanical stability in long-term outdoor environments; PBT masterbatch used for manufacturing automotive engine peripheral components must be able to withstand high temperatures and erosion from engine oil.
PBT masterbatch for fibers: has good spinnability and dyeability. The fibers made from it are soft, elastic, and have low moisture absorption, and can be used for the production of clothing, home textiles, and industrial textiles. PBT fibers used in sportswear can provide good elasticity and wearing comfort.
Classified by aggregation process
Conventional PBT masterbatch: produced using traditional esterification and condensation processes, with mature production techniques and stable product performance, capable of meeting the needs of general application fields.
Modified PBT masterbatch: During the polymerization process, special modifiers are added or special polymerization techniques such as copolymerization and grafting are used to modify the molecular structure of PBT, in order to obtain PBT masterbatch with special properties such as high fluidity and high barrier properties.
Formula ratio
The formula ratio of PBT masterbatch may vary depending on different performance requirements and application scenarios. The following are the approximate formula ratios of some common types of PBT masterbatch:
Universal PBT masterbatch
PBT resin: 90% -95%
Antioxidants: 0.1% -0.5%, such as hindered phenolic antioxidant 1010, phosphite antioxidant 168, etc., can prevent PBT from oxidative degradation during processing and use.
Lubricant: 0.5% -1%, such as stearic acid, calcium stearate, etc., can improve the processing flowability of PBT and prevent materials from sticking to processing equipment.
Enhanced PBT masterbatch
PBT resin: 60% -70%
Glass fiber: 30% -40%, usually alkali free glass fiber is used, and its length and diameter are selected according to specific product requirements, which can effectively improve the mechanical strength and rigidity of PBT.
Coupling agent: 0.5% -1%, such as silane coupling agent, used to improve the bonding force between glass fiber and PBT resin, and enhance the performance of composite materials.
Antioxidants and lubricants: Similar to the addition amount of universal PBT masterbatch, they are 0.1% -0.5% and 0.5% -1%, respectively.
Flame retardant PBT masterbatch
PBT resin: 70% -80%
Flame retardants: 15% -25%, bromine based flame retardants such as decabromodiphenyl ether, tetrabromobisphenol A, etc., phosphorus based flame retardants such as ammonium polyphosphate, phosphate esters, etc., can be selected for single or compound use according to different flame retardant requirements.
Synergistic agent: 0.5% -2%, such as antimony trioxide, can be used in combination with flame retardants to improve flame retardancy.
Antioxidants and lubricants: The addition amount is generally 0.1% -0.5% and 0.5% -1%.
Toughened PBT masterbatch
PBT resin: 75% -85%
Toughening agent: 10-20%, such as ethylene octene copolymer (POE), styrene butadiene styrene block copolymer (SBS) and other elastomers, can effectively improve the toughness and impact resistance of PBT.
Compatibilizer: 0.5% -2%, used to improve the compatibility between toughening agent and PBT resin, so as to better combine the two and enhance the toughening effect.
Antioxidants and lubricants: Add 0.1% -0.5% and 0.5% -1% respectively.
The above formula ratios are for reference only. In actual production, adjustments and optimizations need to be made based on specific product performance requirements, production processes, and costs.
Приложение
PBT masterbatch has excellent comprehensive properties and is widely used in multiple fields. The following are some of the main application aspects:
Electronic and electrical field
Connector: PBT masterbatch has good electrical insulation performance, formability, and dimensional stability, which can meet the high-precision dimensional requirements of connectors and maintain stable electrical performance during long-term use, ensuring stable and reliable signal transmission.
Switch socket: It has high flame retardancy and heat resistance, which can effectively prevent fire hazards caused by current overload and other reasons, ensure safe use, and can be made in various shapes and colors to meet different appearance design requirements.
Coil skeleton: The low dielectric constant and low dielectric loss tangent value of PBT masterbatch can reduce electromagnetic interference, improve the performance and efficiency of the coil, and its mechanical strength can ensure that the skeleton does not deform during winding and use.
Automotive industry field
Peripheral components of the engine, such as the engine hood and intake pipe, PBT masterbatch has good heat resistance and chemical corrosion resistance, and can withstand the high temperature and erosion of various oils generated during engine operation. It is not easy to age and deform after long-term use.
Automotive interior parts, such as seat adjustment handles, interior panels, etc., PBT masterbatch can achieve various performance requirements by adding different additives, such as toughening to improve impact resistance, adding lubricants to improve surface smoothness, making it have good mechanical properties while providing comfortable touch and beautiful appearance.
Automotive lighting fixtures: The lamp housing made of PBT masterbatch has good heat resistance and weather resistance, and can maintain stable performance in various harsh outdoor environments, protecting the optical and electrical components inside the lamp. At the same time, its good formability can achieve complex lamp shape design.
Fiber field
Clothing: PBT fiber has a soft touch, good elasticity, and moisture wicking properties. Clothing made from it is comfortable to wear, has good fit and wrinkle resistance, and is commonly used in sports clothing, underwear, and other fields.
Home textile: In home textile products such as bedding, curtains, etc., PBT fiber can provide a soft texture and good durability, while its anti fouling performance makes it easy to clean and maintain.
Industrial textiles: In some industrial textiles such as geotextiles, filter materials, etc., PBT fibers have high strength and chemical corrosion resistance, which can meet the requirements of different environments.
Other areas
Medical devices: PBT masterbatch has good biocompatibility and chemical resistance, and can be used to manufacture some medical device components, such as syringe casings, medical equipment casings, etc.
Packaging field: PBT masterbatch can be made into packaging materials with high barrier properties, used for packaging products such as food and medicine that require high barrier properties. It can effectively prevent the invasion of substances such as oxygen and water vapor, and extend the shelf life of products.