ABS masterbatch is a granular product made by mixing ultrafine composite inorganic powder particles or functional additives with carrier resin, and extruding and granulating them through a twin-screw extruder. When manufacturing ABS masterbatch, the raw material is usually heated to a plastic state, then cast into a mold, cooled and solidified to form the masterbatch. This process requires precise control to ensure the quality and performance of the masterbatch.
Types
ABS masterbatch can be mainly divided into the following types based on its composition and performance characteristics:
Universal ABS masterbatch
This is the most common type of ABS masterbatch with balanced physical properties. Its mechanical properties, processing performance, and appearance quality are relatively balanced, which can meet the production requirements of general plastic products and is widely used in fields such as home appliance casings, toys, stationery, etc. For example, many common TV casings, plastic toy cars, etc. are produced using universal ABS masterbatch.
High impact resistant ABS masterbatch
By adding an appropriate amount of rubber phase components such as butadiene rubber to ABS resin, the impact strength of the material has been significantly improved. This type of ABS masterbatch is suitable for applications that require high impact resistance, such as automotive parts, helmets, sports equipment, etc. Like the bumper of a car, in order to effectively absorb energy and reduce damage to the vehicle and personnel in the event of a collision, high impact ABS masterbatch is often used for manufacturing.
Heat resistant ABS masterbatch
Special heat-resistant agents were added to ABS resin or monomers with good heat resistance were used for polymerization, resulting in high thermal deformation temperature of the masterbatch. Generally, it can maintain good dimensional stability and mechanical properties in higher temperature environments, and is commonly used in the production of plastic products that need to be used in high-temperature environments, such as high-temperature components in electronic appliances, kitchen utensils, etc. For example, some oven liners and microwave turntable brackets use heat-resistant ABS masterbatch to ensure that deformation or performance degradation does not occur under high temperature working conditions.
Flame retardant ABS masterbatch
By adding flame retardants, ABS masterbatch has good flame retardant properties, which can prevent or delay the combustion process of plastics and reduce the risk of fire. Depending on the type and amount of flame retardant added, different flame retardant levels can be achieved, such as UL94 V-0, V-1, V-2, etc. Commonly used in fields with high requirements for fire safety, such as electronic and electrical enclosures, insulation layers for wires and cables, and building decoration materials. For example, the use of flame-retardant ABS masterbatch for computer host casings, socket casings, etc. can delay the spread of fire in the event of electrical failure, and buy time for personnel evacuation and firefighting rescue.
Electroplated ABS masterbatch
Its surface has good conductivity and smoothness, which can effectively adsorb electroplating layers and achieve high-quality electroplating effects. This type of ABS masterbatch is mainly used for plastic products that require electroplating treatment, such as car decorations, electronic product casings, bathroom hardware, etc., to enhance the appearance texture and corrosion resistance of the products. For example, chrome plated decorative strips on cars and metal textured decorative parts on mobile phone casings are usually manufactured using electroplated ABS masterbatch and then processed through electroplating technology.
Transparent ABS masterbatch
Through special formulas and processing techniques, ABS masterbatch has high transparency while maintaining some basic properties of ABS resin. Can be used to produce plastic products that require transparency, such as transparent toys, transparent stationery, cosmetic packaging, etc. Compared with traditional transparent plastics such as polymethyl methacrylate (PMMA), transparent ABS masterbatch has better toughness and processability, and has certain advantages in some application scenarios.
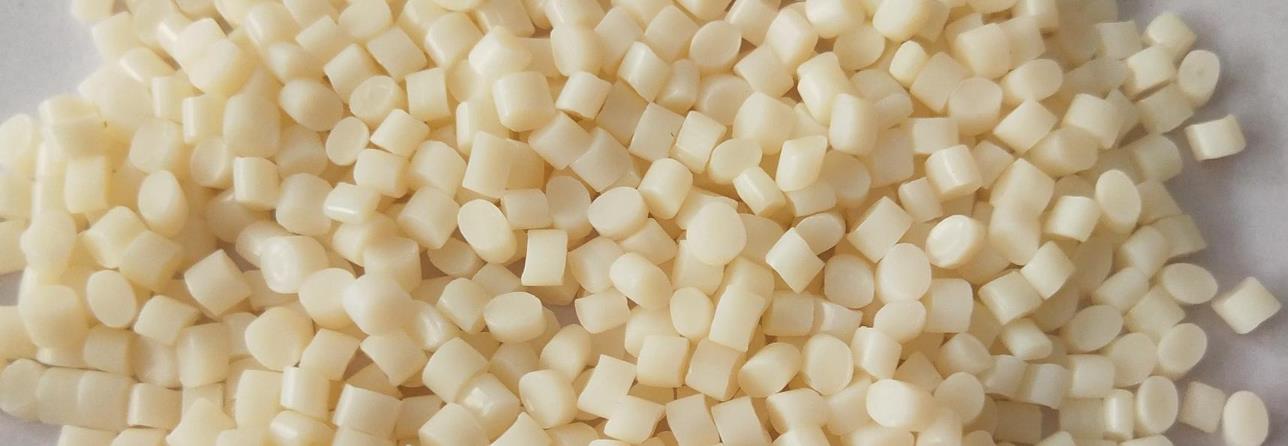
Formula ratio
Different types of ABS masterbatch may have different ratios. The following are the approximate ratio ranges and related explanations for some common types of ABS masterbatch:
Universal ABS masterbatch
Main components and ratios: Typically, acrylonitrile butadiene styrene copolymer (ABS) resin accounts for about 90% -95%, while additives (such as lubricants, antioxidants, etc.) account for about 5% -10%.
Explanation: This ratio enables universal ABS masterbatch to have balanced mechanical properties, processing performance, and appearance quality, which can meet the production needs of most daily plastic products.
High impact resistant ABS masterbatch
Main components and ratios: The content of butadiene rubber in ABS resin is relatively high, generally around 20% -30%, while the copolymer content of acrylonitrile and styrene is about 70% -80%. At the same time, some auxiliary components such as compatibilizers may be added to improve the compatibility between the rubber phase and the resin phase, with an addition amount usually around 2% -5%.
Explanation: The higher content of butadiene rubber endows the masterbatch with good flexibility and impact resistance, making it suitable for products that require high impact strength.
Heat resistant ABS masterbatch
Main components and ratios: On the basis of ABS resin, 10% -20% heat-resistant agents such as glass fiber, mica powder and other inorganic fillers are added, or monomers with good heat resistance are polymerized to adjust the proportion of acrylonitrile, butadiene and styrene, thereby improving the heat resistance performance. For example, the acrylonitrile content may be appropriately increased to 25% -30% to increase the rigidity and heat resistance of the molecular chain.
Explanation: By using this ratio, the thermal deformation temperature of the masterbatch can be increased, allowing it to maintain good dimensional stability and mechanical properties in high-temperature environments.
Flame retardant ABS masterbatch
Main components and ratios: Generally, 15% -30% of flame retardants, such as bromine based flame retardants, phosphorus based flame retardants, or inorganic flame retardants, are added to ABS resin. At the same time, in order to improve the compatibility and processing performance of flame retardants and resins, some synergists and lubricants may be added, usually at a dosage of around 3% -5%.
Explanation: Appropriate flame retardant ratios can achieve different flame retardant levels for ABS masterbatch, meeting the requirements for fire safety in different application scenarios.
Electroplated ABS masterbatch
Main components and ratios: The ratio of ABS resin itself is different from that of the general type, and the content and distribution of butadiene rubber are usually adjusted to around 0.5% -1.5% to obtain a finer surface structure, which is conducive to the adhesion of the electroplating layer. At the same time, some surfactants and conductive agents may be added in an amount of about 3% -8% to improve surface conductivity and smoothness.
Explanation: This ratio helps to achieve high-quality electroplating effect on the surface of plastic products, improving the appearance texture and corrosion resistance of the product.
Transparent ABS masterbatch
Main components and ratios: Through special polymerization processes and formula adjustments, the molecular structure of ABS resin is made more regular, reducing the crystallinity of molecular chains. Generally, the content of butadiene rubber is reduced to 5% -10%, and some transparent modifiers such as methyl methacrylate styrene copolymer (MMA St) are added at a dosage of about 10% -20% to improve transparency.
Explanation: This ratio enables ABS masterbatch to have high transparency while maintaining a certain level of toughness and processability.
It should be noted that the above ratio is only a rough range. In actual production, different manufacturers may make appropriate adjustments based on their own production processes, product quality requirements, and costs.
Production process
The production process of ABS masterbatch generally includes steps such as raw material preparation, mixing, extrusion, granulation, packaging, etc. The following is a specific introduction:
1. Raw material preparation
Select appropriate ABS resin particles as the basic raw material, and choose corresponding additives according to the requirements of different types of ABS masterbatch, such as flame retardants, toughening agents, heat-resistant agents, color masterbatch, etc. Ensure that the quality and performance of raw materials meet production standards, dry the raw materials to remove moisture, and prevent issues such as bubbles or degradation during processing.
2. Mixing
Add the dried ABS resin particles and various additives in a certain proportion to the high-speed mixer for thorough mixing. During the mixing process, the additive is uniformly dispersed in the ABS resin particles through high-speed stirring, ensuring the uniformity of material mixing and laying the foundation for subsequent processing. Some special types of ABS masterbatch, such as high impact type, may require pre mixing rubber toughening agents with some ABS resin to improve the toughening effect.
3. Extrusion
The mixed materials are fed into the extruder. The extruder melts and plasticizes the material inside the barrel through heating, pressure, and other methods, and moves forward under the push of the screw. During the extrusion process, it is necessary to precisely control parameters such as temperature, pressure, and screw speed of the extruder. The extrusion process parameters of different types of ABS masterbatch vary. For example, heat-resistant ABS masterbatch may require higher processing temperatures and greater shear forces due to the addition of heat-resistant agents to ensure uniform dispersion of the heat-resistant agents in the resin matrix.
4. Granulation
The molten material extruded from the extruder is formed into continuous strips or filaments through the die head, and then enters the granulation equipment. The common granulation methods include hot cutting and cold cutting. Hot cutting pellets are immediately cut into granules using a rotating tool after the material extruder head, with regular particle shapes and uniform sizes. Cold cutting is the process of cooling the extruded material to a solid state before cutting it into pellets. This method is suitable for situations where particle shape and size requirements are not particularly strict. For some ABS masterbatch with special requirements, such as transparent type, attention should be paid to avoiding scratches or damage on the surface of the particles during the granulation process to avoid affecting transparency.
5. Packaging
After granulation, ABS masterbatch is screened, graded, and unqualified particles are removed before packaging. During the packaging process, attention should be paid to preventing particles from getting damp or contaminated. Generally, sealed bags or plastic woven bags are used for packaging, and the product model, specifications, production date, and other information should be indicated on the packaging.
Quality control is crucial throughout the entire production process. Strict performance testing is required for each batch of products, including testing of mechanical properties, thermal properties, flame retardancy, appearance quality, etc., to ensure that the products meet the corresponding quality standards and customer requirements.
Production equipment
The ABS masterbatch production equipment mainly includes the following types:
1. High speed mixer
Function: Used to thoroughly mix ABS resin particles with various additives. By using a high-speed rotating stirring blade, the material can achieve good mixing effect in a short period of time, ensuring that the additives are evenly dispersed in the resin.
Selection points: Choose the appropriate volume according to the production scale. Generally, enterprises with larger production scales can choose high-speed mixers with a capacity of 500-1000L; At the same time, the material and shape of the mixing blade should be considered to ensure the mixing effect and durability of the equipment.
2. Twin screw extruder
Function: Heat, melt and plasticize the mixed materials, and transport them forward under the push of the screw. At the same time, through the shearing and mixing effects of the screw, the additives are fully integrated with the ABS resin to achieve uniform dispersion.
Selection criteria: Select parameters such as screw diameter and aspect ratio based on production capacity and product requirements. Generally speaking, a twin-screw extruder with a screw diameter of 65-90mm and an aspect ratio of 30-40 can be used to produce universal ABS masterbatch; For the production of ABS masterbatch with high filling or special performance requirements, it is necessary to choose extruders with larger diameters and aspect ratios to provide stronger shear and mixing capabilities.
3. Mold
Function: Installed at the head of the extruder, it determines the shape and size of the extruded material. Common molds include circular, square, and other shapes of mouth molds, which are used to produce ABS masterbatch of different shapes.
Selection points: Choose the appropriate mold structure and size according to the specifications and shape requirements of the product. For example, ABS masterbatch with conventional circular particles can be produced using a mold with a circular mouth diameter of 2-4mm; For some special shaped particles, such as sheet-like or columnar particles, customized molds of corresponding shapes are required. At the same time, the material and processing accuracy of the mold should be considered to ensure the surface quality and dimensional accuracy of the extruded material.
4. Granulator
Function: Make the extruded molten material into granules. There are two common types of granulators: hot cutting granulators and cold cutting granulators. The hot cutting machine is suitable for producing high-precision and high-quality ABS masterbatch, which can achieve continuous production and high production efficiency; Cold granulators are suitable for situations where particle shape requirements are not particularly strict.
Selection points: If producing universal ABS masterbatch, the corresponding specifications of hot cutting granulator can be selected according to production capacity, such as equipment with a production capacity of 500-1000kg/h; For some ABS masterbatch with special requirements, such as transparent or products with high requirements for particle surface quality, high-precision hot cutting granulators should be preferred, and corresponding cooling and screening devices should be equipped to ensure the quality of the particles.
5. Drying equipment
Function: Dry ABS resin particles and additives before production to remove moisture, prevent defects such as bubbles and silver lines during processing, and improve product quality.
Selection criteria: Choose the appropriate type and specifications of drying equipment based on production scale and material characteristics. Common drying equipment includes ovens, boiling dryers, dehumidifiers, etc. For large-scale production, a dehumidifier dryer can be used, which has high drying efficiency and can accurately control the drying temperature and time. It is suitable for materials with strong moisture absorption such as ABS resin.
6. Cooling equipment
Function: Used for cooling and shaping extruded materials to quickly solidify them into granules. The cooling effect of cooling equipment directly affects the quality and performance of particles.
Key selection points: Choose appropriate cooling methods and equipment based on production capacity and process requirements. There are two common types of cooling equipment: air-cooled and water-cooled. Air cooled cooling equipment has a simple structure and easy operation, but its cooling efficiency is relatively low; Water cooled cooling equipment has high cooling efficiency, but requires corresponding water circulation systems. Generally speaking, for ABS masterbatch production lines with fast production speed and large output, water-cooled cooling equipment can be selected, combined with air-cooled auxiliary cooling, to achieve better cooling effect.
7. Screening equipment
Function: Screen and grade ABS masterbatch after granulation, remove oversized or undersized particles and impurities, and ensure the uniformity and quality of product particle size.
Selection key points: Select the appropriate screening equipment type and sieve specifications based on the particle size requirements of the product. Common screening equipment includes vibrating screens, rotary vibrating screens, etc. The general production of universal ABS masterbatch can use a vibrating screen, and the mesh size of the screen is selected according to the particle size requirements, such as 20-40 mesh. For some special products with high requirements for particle size, it is necessary to use higher precision rotary vibrating screens and equip them with different mesh sizes for multi-stage screening.
8. Packaging equipment
Function: Package the screened ABS masterbatch for storage and transportation. Packaging equipment can achieve automatic measurement, filling, sealing and other packaging processes, improving packaging efficiency and quality.
Selection criteria: Choose appropriate packaging equipment based on production scale and packaging specifications. For small packaging products, semi-automatic or fully automatic granule packaging machines can be used, with a packaging speed of generally 10-60 bags per minute; For large packaging products, such as ton bag packaging, corresponding auxiliary equipment such as ton bag packaging machines and forklifts need to be equipped to achieve efficient and convenient packaging operations.
ABS masterbatch extruder
Kerke’s masterbatch extruder can be used to produce ABS masterbatch. Our ABS masterbatch extruder has multiple models to choose from, which can meet different production requirements.
-
Лабораторный двухшнековый экструдер
When will you need a lab twin screw extruder? If you want to make trials and tests of…
-
Параллельный двухшнековый экструдер
Our Parallel Co-rotating twin screw extruder is designed for compounding and masterbatch making with an output capacity from…
-
Тройной (3 винта) Экструдер
3 Screws extruder is a new technology that has many advantages. The triple screw extruder is mainly used…
-
Двухступенчатая система экструзии
Mother-baby extrusion system is designed for special materials which can not process on one stage extruder, the first…
-
Линия для замешивания компаундов Banbury Kneader
Our kneader + extruder is designed for making special applications with an output capacity from 30kg/h to 1000kg/h.…
-
Система резки / Система гранулирования
Different material needs different cutting system, Kerke provides all kinds of cutting system, here is the explanation of…
Related requirements
In the production process of ABS masterbatch, the extruder needs to meet various requirements such as plasticization, mixing, and temperature control to ensure product quality and production efficiency. The following is a specific introduction:
Plasticizing capacity
Appropriate screw design: The melting characteristics of ABS resin require extruder screws to have good plasticizing ability. Usually, a gradient screw is used, and the depth of the screw groove gradually becomes shallower from the feeding section to the homogenization section, which can gradually compress and shear the ABS resin during the rotation of the screw, achieving good plasticization. Meanwhile, the aspect ratio of the screw is generally between 20-30 to provide sufficient plasticizing length and time, ensuring that the ABS resin is fully melted.
High torque drive: ABS resin has a high viscosity in the molten state and requires a large torque to push the material forward in the screw. Therefore, the extruder needs to be equipped with a high torque drive motor and gearbox to ensure that the screw can provide sufficient power at different production speeds, achieving stable plasticization and extrusion.
Mixed dispersion performance
Mixing elements: In order to evenly mix various components (such as ABS resin, additives, colorants, etc.) in ABS masterbatch, multiple mixing elements should be installed on the extruder screw. For example, components such as kneading blocks and toothed mixing discs are installed in the middle and front of the screw, which can generate strong shear and mixing effects, thoroughly mix materials of different components, and improve the quality stability of the masterbatch.
Dispersion ability: For some functional additives (such as flame retardants, toughening agents, etc.) added to ABS masterbatch, good dispersion effect is required to fully exert their effects. The extruder should have strong dispersion ability. Through the special design of the screw and appropriate process parameter adjustment, the additives can be evenly dispersed in the ABS resin matrix, avoiding agglomeration or local high concentration.
Temperature control accuracy
Multi stage temperature control: In the production process of ABS masterbatch, precise temperature control is required for materials at different stages. Extruders are usually equipped with multiple heating and cooling sections, generally divided into 5-8 sections. The temperature in the feeding section is lower to prevent premature melting of materials and affect transportation; As the material moves towards the machine head, the temperature gradually increases and reaches the highest temperature in the homogenization section, allowing the ABS resin to fully melt and mix; At the head of the machine, the temperature should be appropriately lowered to ensure that the extruded masterbatch has a good molding effect. The temperature control accuracy of each heating section should be within ± 2 ℃.
Quick response: Due to the sensitivity of ABS resin to temperature, high or low temperature can affect product quality, so the heating and cooling system of the extruder needs to have quick response capability. When the temperature of the material fluctuates, the heating and cooling system can quickly adjust to restore the temperature to the set value, ensuring the stability of the production process.
Pressure stability
Stable extrusion pressure: During the extrusion process of ABS masterbatch, stable pressure is the key to ensuring the dimensional accuracy and appearance quality of the product. The hydraulic system or mechanical transmission system of the extruder should be able to provide stable extrusion pressure, with pressure fluctuations generally controlled within ± 5%. Stable pressure can maintain a uniform flow rate of materials through the machine head and mold, thereby producing masterbatch with uniform size and smooth surface.
Pressure regulation capability: Different ABS masterbatch formulations and production processes may require different extrusion pressures, so extruders should have good pressure regulation capabilities. Operators can flexibly adjust the extrusion pressure according to the actual production situation by adjusting parameters such as screw speed and back pressure to meet the production requirements of different products.
Material conveying stability
Uniform feeding: In the production of ABS masterbatch, uniform feeding of materials is an important link to ensure production stability. The feeding device of the extruder should use high-precision feeders, such as weight loss feeders or volumetric feeders, which can accurately control the feeding amount of materials such as ABS resin and additives, ensuring that various materials enter the extruder uniformly according to the set proportion. At the same time, the feeder should have good sealing to prevent material leakage and air from entering the extruder.
Stable screw conveying: The design and processing accuracy of the screw have a significant impact on the stability of material conveying. The pitch and groove depth of the screw should be uniform and consistent to ensure that the material can be stably transported forward inside the screw. In addition, the gap between the screw and the barrel should also be reasonably controlled. If the gap is too large, it may cause material reflux and affect the conveying efficiency; If the gap is too small, it is easy to cause excessive shearing and wear of the material.
Corrosion Resistance
Corrosion resistant materials: In the production process of ABS masterbatch, certain additives (such as flame retardants, lubricants, etc.) may have a certain degree of corrosiveness, so the components in contact with the material such as the barrel and screw of the extruder need to use corrosion-resistant materials. For example, the barrel can be protected by lining it with stainless steel or spraying a corrosion-resistant coating, while the screw can be made of alloy steel material with good corrosion resistance and surface treated, such as nitriding, to improve its corrosion resistance and extend the service life of the equipment.
Automation control level
Parameter monitoring and recording: Advanced automation control systems can monitor various operating parameters of extruders in real time, such as temperature, pressure, screw speed, material flow rate, etc., and record and store these data. Operators can check the parameter changes during the production process at any time through the monitoring interface, detect abnormalities in a timely manner, and make adjustments. At the same time, recording historical data also helps to analyze and optimize production processes, improving the stability of product quality.
Remote control and fault diagnosis: Some high-end extruders also have remote control functions, allowing operators to operate and monitor the extruder remotely from the production site through the network, improving production flexibility and management efficiency. In addition, the automation control system should also have fault diagnosis function, which can automatically detect equipment faults and issue alarm signals in a timely manner to prompt operators to carry out maintenance. Some systems can also send fault information to device manufacturers or technical support personnel through remote communication technology to quickly obtain solutions.
Приложение
ABS masterbatch has a wide range of applications, including the following main areas:
Automotive industry
Interior parts: ABS masterbatch can be used to manufacture car dashboards, center consoles, door interior panels, etc. It has good impact resistance, heat resistance, and weather resistance, and can withstand various environmental conditions inside the car. At the same time, different additives can be added to achieve various colors and surface textures, meeting the aesthetic and comfort requirements of the car interior.
Exterior parts: In the field of automotive exterior, ABS masterbatch can be used to produce components such as rearview mirror housings, bumpers, grilles, etc. Its high glossiness and good formability make the exterior parts have excellent appearance quality, as well as certain scratch and corrosion resistance, which can enhance the overall quality and appearance attractiveness of the car.
Electronic appliances
Shell: ABS masterbatch is a commonly used material for the shell of electronic and electrical products, such as televisions, computer monitors, printers, copiers, etc. It has excellent electrical insulation performance, mechanical strength, and processing performance, which can protect internal electronic components from external environmental influences, while providing good appearance effects to meet consumers’ requirements for product appearance and quality.
Components: In electronic and electrical products, ABS masterbatch can also be used to manufacture various components, such as keyboard keys, mouse cases, phone cases, etc. Its good wear resistance and fatigue resistance can ensure that these components are not easily damaged during long-term use. At the same time, special additives can be added to achieve antibacterial, anti-static and other functions, meeting the special needs of different products.
Building materials industry
Pipe material: ABS masterbatch can be used to produce building pipes, such as water supply pipes, drainage pipes, etc. Compared with traditional metal pipes, ABS pipes have the advantages of light weight, corrosion resistance, wear resistance, and easy installation, and can be widely used in various building water supply and drainage systems.
Board: Board made of ABS masterbatch has good rigidity and toughness, and can be used in the field of architectural decoration, such as ceilings, wall panels, etc. These boards can achieve various decorative effects through surface treatment and printing processes, such as imitating wood grain, imitating stone, etc., to meet the decoration needs of different architectural styles.
Toys
Toy shell: ABS masterbatch is one of the ideal materials for toy shells, which has good safety, impact resistance, and processability. By adding different color masterbatch, various brightly colored and exquisite looking toy shells can be produced, and their non-toxic and odorless characteristics meet the safety standards of the toy industry, ensuring the safety of children’s use.
Toy components: In toy manufacturing, ABS masterbatch can also be used to produce various components, such as the body and wheels of toy cars, as well as joints and accessories of various plastic toys. Its good mechanical properties can ensure that toys are not easily damaged during play and extend their service life.
Other areas
Office supplies: such as folders, file boxes, staplers, calculators and other office supplies, many of which are also made of ABS masterbatch. It can provide good strength and durability, while meeting the aesthetic and practical requirements of office supplies through different surface treatments and color combinations.
Medical devices: In the field of medical devices, ABS masterbatch can be used to manufacture some non critical components, such as the casing and handle of medical devices. Its good biocompatibility and chemical corrosion resistance can meet the requirements of medical device use, and at the same time, it can achieve high precision and appearance quality required by medical devices through special processing technology.