XLPE masterbatch is a plastic processing aid, fully known as cross-linked polyethylene masterbatch. It is composed of excessive chemical additives, carrier resins, and dispersants, and is commonly used to improve the performance of cross-linked polyethylene (XLPE). XLPE is the abbreviation for cross-linked polyethylene, which uses cross-linking technology to form chemical chain bridges between polyethylene molecules, thereby improving its comprehensive properties such as heat resistance, chemical resistance, and insulation.
Types
Cross linked polyethylene (XLPE) masterbatch can be classified into various types according to different classification standards. The following are common classifications and specific types:
Classified by crosslinking method
Chemical cross-linked XLPE masterbatch: usually contains crosslinking agents such as organic peroxides. Under the action of heating and pressure, the crosslinking agent decomposes to produce free radicals, triggering crosslinking reactions between polyethylene molecular chains and forming a three-dimensional network structure. This type of masterbatch has fast crosslinking speed, easy control of crosslinking degree, stable product performance, and is widely used in fields such as wires, cables, and pipes.
Radiation crosslinked XLPE masterbatch: This masterbatch does not contain crosslinking agents, but instead uses high-energy radiation (such as electron beams, gamma rays, etc.) to irradiate polyethylene, causing its molecular chains to generate free radicals and undergo crosslinking reactions. The production process of radiation cross-linked XLPE masterbatch does not use chemical cross-linking agents, so the product has high purity and no cross-linking agent residue, especially suitable for fields with high hygiene requirements, such as medical catheters, food packaging, etc.
Function
XLPE masterbatch for wires and cables: It has excellent electrical properties such as high insulation resistance, low dielectric loss, etc., which can effectively ensure the transmission performance and safety performance of wires and cables. At the same time, it also has good heat resistance and aging resistance, which can maintain stable performance during long-term use and is suitable for various power cables, communication cables, etc.
XLPE masterbatch for pipes: It has high mechanical strength and resistance to environmental stress cracking, and can withstand the pressure of fluids inside the pipeline and the influence of external environment. In addition, it also has good corrosion resistance and wear resistance, and can be widely used in fields such as water supply pipes, gas pipes, drainage pipes, etc.
XLPE masterbatch for film: The film produced has good transparency, flexibility, and mechanical properties. At the same time, it also has certain heat resistance and puncture resistance, and can be used in fields such as agricultural film and packaging film. Agricultural film can improve crop yield and quality, while packaging film can effectively protect goods.
Classified by additives
Flame retardant XLPE masterbatch: with the addition of flame retardants, it can prevent or delay the combustion of materials and improve their fire safety performance. Widely used in fields with high fire prevention requirements such as wires and cables, building materials, etc., it can effectively prevent the occurrence and spread of fires.
Anti aging XLPE master batch: anti-aging additives such as antioxidant and ultraviolet absorber are added, which can improve the ability of materials to resist oxidation, ultraviolet and other environmental factors during long-term use, extend the service life of materials, and are suitable for outdoor wire, cable, pipe, film and other products.
Filled XLPE masterbatch: Adding fillers such as calcium carbonate and talc powder can reduce material costs and improve certain properties of the material, such as increasing hardness, rigidity, and dimensional stability. Filled XLPE masterbatch is widely used in fields such as pipes and injection molded products.
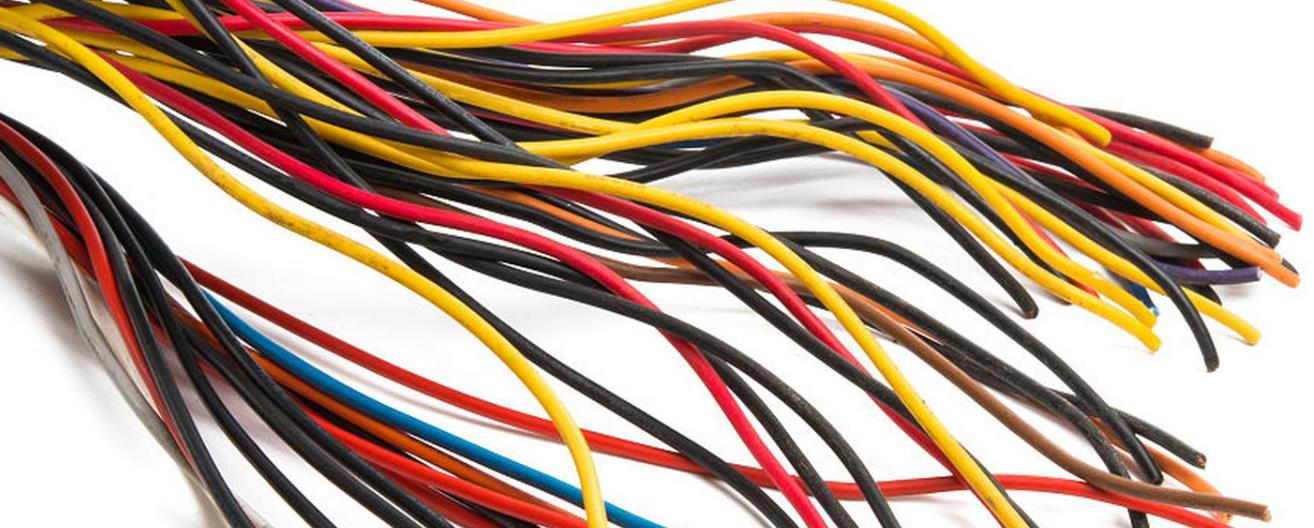
Fórmula
The formula ratio of XLPE masterbatch may vary depending on different uses, performance requirements, and production processes. Here are several typical formula ratio examples and their explanations:
Universal XLPE masterbatch formula
Low density polyethylene (LDPE): 60-70 parts
Provide good flexibility and processing performance, making the masterbatch easy to plasticize and shape during the processing.
Linear low-density polyethylene (LLDPE): 20-30 parts
Improve the strength and toughness of the masterbatch, enhance the tensile and tear resistance of the product.
Crosslinking agent (such as DCP peroxide): 0.8-1.2 parts
Under heating conditions, decomposition generates free radicals, triggering cross-linking reactions between polyethylene molecular chains to form a three-dimensional network structure, thereby improving the material’s heat resistance, mechanical properties, and chemical corrosion resistance.
Antioxidants (such as 1010, 168, etc.): 0.1-0.3 parts
Prevent oxidation reactions of polyethylene during processing and use, delay the aging rate of materials, and improve the service life of materials.
Crosslinking agent (such as triallyl isocyanurate TAIC): 0.2-0.5 parts
Synergistic effect with crosslinking agents enhances crosslinking efficiency, makes crosslinking reactions more uniform, improves crosslinking structure, and thus improves the overall performance of materials.
XLPE masterbatch formula for wires and cables
High density polyethylene (HDPE): 40-50 parts
It has high rigidity and mechanical strength, and can meet the mechanical performance requirements of wire and cable sheath materials.
Ethylene vinyl acetate copolymer (EVA): 10-20 parts
Improve the flexibility and low temperature resistance of the masterbatch, so that wires and cables can maintain good performance in low temperature environments.
Crosslinking agent (DCP): 1-1.5 parts
Initiate cross-linking reactions, improve the heat resistance and electrical insulation performance of materials, and ensure the safety and stability of wires and cables during long-term use.
Antioxidants (1076, 168, etc.): 0.2-0.5 parts
Prevent material performance degradation caused by oxidation during processing and use, and extend the service life of wires and cables.
Lubricant (such as zinc stearate): 0.1-0.3 parts
Reducing friction during processing, improving material flowability, making the extrusion process smoother for masterbatch, and also helping to improve the surface quality of the product.
Inorganic fillers (such as aluminum hydroxide, magnesium hydroxide): 20-30 parts
Plays a role in flame retardancy and cost reduction. During combustion, inorganic fillers will decompose and absorb heat, suppress material combustion, and improve the flame retardant performance of wires and cables.
XLPE masterbatch formula for pipes
HDPE: 50-60 copies
Endow the pipe with high rigidity, strength, and corrosion resistance, enabling it to withstand the pressure of the fluid inside the pipeline and the effects of the external environment.
LLDPE: 20-30 copies
Improve the flexibility and impact resistance of pipes, and reduce the risk of pipe breakage due to collisions during transportation and installation.
Crosslinking agent (DCP): 0.8-1.2 parts
Cross link polyethylene molecules to improve the heat resistance and environmental stress cracking resistance of pipes, and extend the service life of pipes.
Antioxidants (such as hindered phenolic antioxidants): 0.1-0.3 parts
Prevent the aging of pipes due to oxidation during long-term use and maintain the stability of pipe performance.
Light stabilizer (such as UV absorber UV-531): 0.1-0.2 parts
Absorb ultraviolet rays to prevent degradation of pipes due to ultraviolet radiation during outdoor use, and improve the weather resistance of pipes.
Processing aids (such as ACR): 0.5-1 part
Improve the processing performance of masterbatch, increase the extrusion speed and surface quality of pipes, reduce processing temperature, and save energy.
The above formula ratios are for reference only. In actual production, adjustments and optimizations need to be made based on specific production equipment, process conditions, and product performance requirements.
Proceso de producción
The production process of XLPE masterbatch usually includes multiple steps such as raw material preparation, mixing, extrusion, cross-linking, granulation, etc. The following is a detailed introduction to its production process:
1. Preparación de la materia prima
Choose base resin: Based on product performance requirements, select suitable polyethylene resins such as low-density polyethylene (LDPE), linear low-density polyethylene (LLDPE), or high-density polyethylene (HDPE).
Preparation of additives: Accurately weigh crosslinking agents, antioxidants, crosslinking aids, lubricants, and other additives to ensure that the quality and purity of the additives meet the requirements.
2. Mezcla
Add the prepared polyethylene resin and various additives into the high-speed mixer for thorough mixing. By high-speed stirring, the additive is uniformly dispersed on the surface of polyethylene resin particles to form a premix.
3. Extrusión
Feeding: Add the premix into the hopper of the extruder and transport the material forward through the rotation of the screw.
Plasticization: In the heating zone of the extruder, the material is gradually heated to a molten state, while the shearing effect of the screw further mixes the material evenly, achieving a good plasticization effect.
4. Cross linking
Chemical crosslinking: If chemical crosslinking is used, during the extrusion process, the crosslinking agent decomposes under high temperature and screw shear to produce free radicals, triggering crosslinking reactions between polyethylene molecular chains. By controlling parameters such as temperature, screw speed, and residence time of the extruder, the cross-linking reaction is fully carried out inside the extruder, forming XLPE melt with a certain degree of cross-linking.
Radiation crosslinking: For radiation crosslinked XLPE masterbatch, extruded polyethylene pipes or films are irradiated with high-energy rays (such as electron beams, gamma rays) to generate free radicals in the polyethylene molecular chains, leading to crosslinking reactions. The radiation dose and exposure time are key factors affecting the radiation cross-linking effect, which need to be precisely controlled according to the performance requirements and thickness of the product.
5. Granulation
Underwater granulation: The cross-linked XLPE melt is extruded from the extruder die and directly enters the underwater granulation system. Underwater, a high-speed rotating cutter cuts the melt into uniform particles, which quickly cool and solidify in water. Then, they are dehydrated using equipment such as centrifugal dehydration or vibrating screens to obtain XLPE masterbatch.
Air cooling granulation: Another method is air cooling granulation. After the melt is extruded from the die, it is first cooled by an air cooling device before entering the granulator for granulation. The cut particles are collected and cooled by equipment such as conveyor belts or cyclone separators, and finally obtain XLPE masterbatch.
6. Packaging
The produced XLPE masterbatch is packaged using packaging materials such as plastic woven bags or ton bags to prevent moisture and contamination, and to facilitate storage and transportation.
Throughout the entire production process, it is necessary to strictly control the process parameters of each link, such as temperature, pressure, screw speed, crosslinking agent dosage, etc., to ensure the quality stability and performance compliance of XLPE masterbatch. At the same time, regular maintenance and upkeep of production equipment are necessary to ensure its normal operation, improve production efficiency and product quality.
Production equipment
The XLPE masterbatch production equipment mainly includes equipment used for raw material processing, mixing, extrusion, cross-linking, granulation, and packaging. The following is a specific introduction:
1. Equipo de ingredientes
Electronic scale: used for precise weighing of various raw materials, such as polyethylene resin, crosslinking agents, antioxidants, etc., to ensure the accuracy of ingredient ratios.
Vacuum feeding machine: It can transport raw materials from storage containers to mixing equipment or extruder hoppers, achieving automated feeding and avoiding moisture and pollution of raw materials.
2. Hybrid equipment
High speed mixer: It can evenly mix polyethylene resin and additives in a short period of time. Through high-speed rotating stirring blades, the material forms strong convection and shear in the container, ensuring that the additives are evenly dispersed in the resin.
3. Extrusion equipment
Single screw extruder or twin-screw extruder: Single screw extruder has a simple structure and low cost, suitable for production with low mixing requirements; Twin screw extruders have better mixing, plasticizing, and conveying capabilities, and can more accurately control the residence time and temperature distribution of materials, making them suitable for producing high-performance XLPE masterbatch.
Extruder auxiliary equipment: including feeding device, heating and cooling system, transmission system, etc. The feeding device ensures that the material enters the extruder uniformly and stably; The heating and cooling system is used to control the temperature of each section of the extruder, ensuring that the material is plasticized and crosslinked at the appropriate temperature; The transmission system provides power to the screw, ensuring stable rotational speed of the screw.
4. Cross linking equipment
Chemical crosslinking: The chemical crosslinking process is generally completed inside an extruder, by precisely controlling parameters such as temperature, screw speed, and residence time of the extruder, to fully decompose the crosslinking agent and initiate crosslinking reactions.
Radiation crosslinking: Radiation crosslinking requires specialized radiation devices such as electron accelerators or cobalt-60 radiation sources. The high-energy electron beam generated by an electron accelerator has the advantages of high energy, uniform dose distribution, and high production efficiency; The cobalt-60 radiation source has the characteristics of stable radiation intensity and simple equipment maintenance.
5. Granulation equipment
Underwater granulator: It is a commonly used granulation equipment in the production of XLPE masterbatch, with advantages such as uniform granulation, smooth particle surface, and high production efficiency. It consists of a cutting chamber, a water circulation system, a cutter drive system, and other parts, which can directly cut the extruded XLPE melt into particles underwater.
Air cooled pellet cutter: The extruded strip is cooled by an air cooling device and then cut into pellets by a cutting blade. Suitable for situations where particle shape and size requirements are not particularly strict, the equipment structure is relatively simple and the maintenance cost is low.
6. Packaging equipment
Automatic packaging machine: capable of automatically measuring, filling, and sealing XLPE masterbatch, improving packaging efficiency and quality. According to different packaging specifications and requirements, there are different types of automatic packaging machines to choose from, such as granule packaging machines, ton bag packaging machines, etc.
Metal detection machine: used to detect whether metal impurities are mixed in XLPE masterbatch before packaging, to prevent damage to downstream processing equipment caused by metal impurities, while also ensuring product quality and safety.
In addition to the main equipment mentioned above, the production workshop may also be equipped with auxiliary equipment such as air compressors, dehumidifiers, and cooling towers to provide compressed air, control workshop humidity, and circulate cooling water, ensuring the smooth progress of the production process.
XLPE masterbatch extruder
Kerke’s masterbatch extruder can be used to produce XLPE masterbatch. Our XLPE masterbatch extruder has multiple models to choose from, which can meet different production requirements.
-
Extrusora de doble husillo para laboratorio
¿Cuándo necesitará una extrusora de doble husillo de laboratorio? Si desea realizar ensayos y pruebas de...
-
Extrusora de doble husillo paralelo
Nuestra extrusora de doble husillo paralelo corrotante está diseñada para la fabricación de compuestos y...
-
Extrusor triple (3 tornillos)
La extrusora de 3 tornillos es una nueva tecnología que tiene muchas ventajas. La extrusora de triple tornillo se utiliza principalmente...
-
Sistema de extrusión de doble etapa
El sistema de extrusión madre-bebé está diseñado para materiales especiales que no pueden procesarse en una extrusora de una etapa,...
-
Línea de amasado Banbury
Nuestra amasadora + extrusora está diseñada para realizar aplicaciones especiales con una capacidad de producción de 30kg/h a 1000kg/h....
-
Sistema de corte / Sistema de granulación
Diferentes materiales necesitan diferentes sistemas de corte, Kerke ofrece todo tipo de sistemas de corte, aquí está la explicación de...
Related requirements
The extruder is a key equipment for producing XLPE masterbatch, and it has the following requirements:
Screw design
Length to diameter ratio: Generally, a larger length to diameter ratio is required, usually between 25-35. Longer screws can provide longer material conveying and plasticizing distances, allowing polyethylene resin to be fully mixed with additives, plasticizing evenly, and facilitating cross-linking reactions.
Screw structure: Adopting gradient or mutation type screws. Gradient screw is suitable for processing various types of polyethylene resins, and can smoothly transform materials from solid to molten state; The mutant screw has a shorter compression section and can generate higher shear rates, making it more suitable for processing highly crystalline polyethylene resins. It can quickly compress and heat the material to a molten state.
Mixing and dispersing ability
Powerful shear mixing function: The extruder needs to have good mixing and dispersion ability. Through the special design and combination of screws, such as setting up mixing sections, kneading blocks, etc., the material is subjected to strong shear and stretching effects during the extrusion process, ensuring that crosslinking agents, antioxidants and other additives are evenly dispersed in the polyethylene resin, avoiding situations where the concentration of local additives is too high or too low, thereby ensuring the consistency of XLPE masterbatch performance.
Temperature control accuracy
Multi stage precise temperature control: The extruder barrel is usually divided into multiple heating and cooling sections, requiring high temperature control accuracy, generally within ± 1 ℃. Accurate temperature control is crucial for the plasticization of polyethylene resin, the decomposition of crosslinking agents, and the progress of crosslinking reactions. Different processing stages require different temperature conditions, for example, the feeding section has a lower temperature to prevent premature melting of materials; The temperature of the compression and metering sections gradually increases to fully plasticize and homogenize the material; In the crosslinking reaction zone, it is necessary to strictly control the temperature within the optimal decomposition temperature range of the crosslinking agent to ensure the smooth progress of the crosslinking reaction and the stability of the crosslinking degree.
Pressure stability
Stable extrusion pressure: During the extrusion process, it is necessary to maintain a stable pressure to ensure uniform and continuous extrusion of the material. Excessive pressure fluctuations can lead to unstable extrusion volume, affecting the uniformity of particle size and product quality. Therefore, the hydraulic system or mechanical transmission system of the extruder should have good stability and be able to maintain the fluctuation of extrusion pressure within a small range under different production speeds and material characteristics. Generally, the pressure fluctuation should not exceed ± 5%.
Output and production efficiency
Meet production scale requirements: Based on the production scale of the manufacturer and market demand, the extruder should have a suitable output range. Generally speaking, extruders used for XLPE masterbatch production can produce between tens and hundreds of kilograms per hour. At the same time, the extruder should have high production efficiency and be able to achieve continuous and stable production while ensuring product quality, reducing equipment downtime and maintenance costs.
Corrosion Resistance
Chemical corrosion resistance: Due to the possible presence of corrosive additives such as crosslinking agents and antioxidants in the material during the production of XLPE masterbatch, components such as the extruder barrel and screws that come into contact with the material need to be made of corrosion-resistant materials, such as stainless steel, nickel based alloys, etc., to prevent equipment from being corroded and affecting its service life and product quality.
Degree of automation control
Advanced control system: Modern XLPE masterbatch production requires extruders to have a high degree of automation control, which can achieve automatic monitoring and adjustment of parameters such as temperature, pressure, screw speed, and feeding amount. By equipping advanced programmable logic controllers (PLCs) and human-machine interfaces (HMIs), operators can easily set and modify process parameters, monitor various data in real-time during the production process, and perform fault diagnosis and alarm prompts, improving production safety and reliability, reducing manual operation errors and labor intensity.
Aplicación
XLPE (cross-linked polyethylene) masterbatch has a wide range of applications in the fields of wires and cables, pipes, films, rubber products, etc. The following is a specific introduction:
Wire and cable industry
Insulation layer: XLPE masterbatch has excellent electrical insulation, temperature resistance, and mechanical properties, making it an ideal material for wire and cable insulation layers. It can effectively prevent current leakage, ensure the safety and stability of power transmission, and can withstand high working temperatures, improve the current carrying capacity of cables, and extend the service life of cables.
Sheath: When used for cable sheathing, XLPE masterbatch can enhance the cable’s wear resistance, chemical corrosion resistance, and UV resistance, protect the internal conductors and insulation layer from external environmental influences, and improve the overall performance and reliability of the cable.
Pipe manufacturing industry
Water supply pipe: Pipes made of XLPE masterbatch are non-toxic, hygienic, and corrosion-resistant, which can prevent the precipitation of harmful substances in water and ensure water quality safety. Meanwhile, its excellent temperature resistance and creep resistance enable the pipe to maintain stable performance under different water temperature conditions, making it less prone to deformation during long-term use.
Gas pipe: In the field of gas transmission, XLPE pipes have high strength and pressure resistance, and can withstand high pressure during gas transmission. Moreover, it has good aging resistance and environmental stress cracking resistance, which can effectively prevent cracks and ruptures in the pipes during long-term use, ensuring the safety of gas transportation.
Film production industry
Agricultural film: XLPE masterbatch can be used to produce greenhouse film and plastic film for agriculture. The made greenhouse film has good transparency, insulation, and weather resistance, which can provide a suitable growth environment for crops and promote their growth and development. Plastic film has functions such as insulation, moisture retention, and weed control, which can improve land use efficiency and crop yield.
Packaging film: In the field of packaging, XLPE film has high toughness, transparency, and puncture resistance, and can be used to package various products such as food, daily necessities, industrial products, etc. Its good sealing performance can effectively protect the product from external factors and extend the shelf life of the product.
Other areas
Foam material: XLPE masterbatch can be used to produce foam plastics, such as cross-linked polyethylene foam (XPE). XPE has the advantages of light weight, softness, good elasticity, thermal insulation, sound insulation, buffering, etc., and is widely used in fields such as building insulation, automotive interior, sports equipment, packaging buffering, etc.
Rubber products: In the rubber industry, XLPE masterbatch can be added as a modifier to rubber to improve its heat resistance, aging resistance, and mechanical strength. For example, in tire production, adding XLPE masterbatch can improve tire performance, enhance tire wear resistance and tear resistance.