TPV masterbatch is a functional masterbatch made from thermoplastic vulcanized rubber as the base material. TPV is a high-performance polymer material that lies between rubber and plastic, possessing the physical properties of vulcanized rubber and the processability of thermoplastic. It also has excellent weather resistance, heat aging resistance, tensile strength and toughness, resilience, compression permanent deformation resistance, and electrical insulation.
Types
TPV masterbatch can be classified into various types based on different matrix resins, performance characteristics, and application fields. The following are some common types:
Classified by matrix resin
PP based TPV masterbatch: made of polypropylene (PP) as the matrix resin, it has good chemical corrosion resistance, heat resistance, and processing performance. Products made from PP based TPV masterbatch have high surface hardness and good rigidity, and are commonly used in fields such as automotive parts, wires and cables, and building materials.
PE based TPV masterbatch: Made of polyethylene (PE) as the matrix resin, it has excellent flexibility, low temperature resistance, and water resistance. The products produced from PE based TPV masterbatch are soft, comfortable, and have good elasticity, suitable for manufacturing seals, pipes, films, and outdoor products that require good weather resistance.
Classified by performance characteristics
High elasticity TPV masterbatch: This type of TPV masterbatch has excellent elasticity and resilience, and can quickly restore its original state within a large deformation range. It is usually used to manufacture products that require high elasticity, such as automotive shock absorbers, shoe soles, rubber hoses, etc.
High strength TPV masterbatch: It has high mechanical properties such as tensile strength, tear strength, and puncture resistance. Suitable for applications that require high product strength, such as industrial conveyor belts, engineering plastic modification, aerospace, and other fields.
Aging resistant TPV masterbatch: After special formula design and additive modification, it has good properties such as UV resistance, ozone resistance, and heat oxidative aging resistance. Products that can be used for long-term outdoor use, such as building sealing strips, wire and cable sheaths, outdoor shading materials, etc., can extend the service life of products and reduce performance degradation and damage caused by aging.
Chemical resistant TPV masterbatch: It has good resistance to various chemical substances and is not easily corroded by chemical media such as acid, alkali, salt, etc. Commonly used in chemical pipelines, container liners, sealing gaskets, and other applications that come into contact with chemical substances, to ensure that the product can maintain good performance and stability even in harsh chemical environments.
Classified by application field
TPV masterbatch for automobiles: designed and produced to meet the special requirements of the automotive industry, it has good heat resistance, oil resistance, weather resistance, and mechanical properties. It can be used to manufacture automotive interior parts, exterior parts, seals, shock absorber components, etc., such as automotive dashboard skin, door sealing strips, engine peripheral rubber products, etc., to meet the requirements of automotive use in different working conditions.
TPV masterbatch for electronic appliances: It has excellent electrical insulation performance, flame retardant performance, and processing performance. Suitable for the shell, plug socket, wire and cable insulation layer and other components of electronic and electrical products, it can ensure the safe and reliable operation of electronic and electrical equipment, while meeting the requirements of environmental protection and flame retardant standards.
Medical TPV masterbatch: meets medical grade standards, has good biocompatibility, is non-toxic, odorless, and resistant to disinfection. It can be used to manufacture medical devices such as medical catheters, syringe pistons, and medical seals, ensuring safety and reliability when in contact with the human body.
TPV masterbatch for daily necessities: used in the production of various daily necessities, such as kitchenware handles, bathroom anti slip mats, stationery, etc. This type of TPV masterbatch usually focuses on the soft touch, vivid color, and processing performance of the product to meet consumers’ comfort and aesthetic requirements for daily necessities.
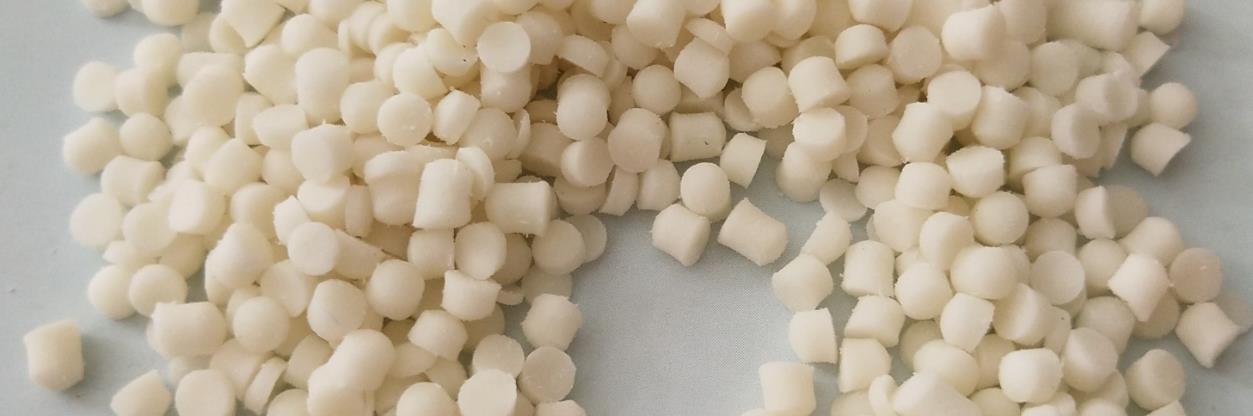
Fórmula
The formula ratio of TPV masterbatch may vary depending on different matrix resins, performance requirements, and application fields. The following is a typical PP based TPV masterbatch formula ratio example for your reference:
PP (polypropylene): 40% -60%
As a matrix resin, it provides the basic rigidity, heat resistance, and processing performance of the product.
EPDM (Ethylene Propylene Diene Monomer Rubber): 30% -50%
Endow TPV masterbatch with good elasticity, weather resistance, and chemical corrosion resistance.
Crosslinking agent: 0.5% -2%
Usually peroxides, such as diisopropylbenzene peroxide (DCP), are used to initiate crosslinking reactions between PP and EPDM, forming a stable three-dimensional network structure and improving the mechanical properties and heat resistance of the product.
Crosslinking agent: 0.5% -2%
Triallyl isocyanurate (TAIC) can assist crosslinking agents in improving crosslinking efficiency, making crosslinking reactions more uniform, and further improving product performance.
Filler: 5% -20%
Common ones include calcium carbonate, talc powder, etc., which can reduce costs while improving the hardness, dimensional stability, and heat deformation resistance of the product. The type and dosage of fillers need to be selected and adjusted according to specific performance requirements.
Plasticizer: 0-10%
When it is necessary to improve the flexibility and processing performance of the product, an appropriate amount of plasticizer can be added, such as dioctyl phthalate (DOP) or epoxidized soybean oil. But in some application fields with high environmental requirements, it is necessary to choose environmentally friendly plasticizers or reduce the use of plasticizers.
Stabilizer: 0.5% -2%
Including antioxidants and light stabilizers, such as hindered phenolic antioxidant 1010 and light stabilizer UV-531, used to prevent oxidation and photo aging of TPV masterbatch during processing and use, and extend the service life of the product.
Lubricant: 0.5% -2%
Such as stearic acid, polyethylene wax, etc., can improve the flowability of materials during processing, reduce friction between materials and processing equipment, improve processing efficiency and product surface quality.
It should be noted that this is only a rough range of formula ratios, and actual production needs to be optimized and adjusted based on specific product performance requirements, processing technology, and cost factors. In addition, there may be differences in the performance of raw materials produced by different manufacturers, which can also affect the formula ratio. If you need a more precise formula ratio, it is recommended to consult a professional TPV masterbatch manufacturer or conduct relevant experimental research.
Proceso de producción
The production process of TPV masterbatch usually includes the following main steps:
Preparación de la materia prima
Accurately weigh various raw materials according to the designed formula, including matrix resins (such as PP, PE, etc.), rubber (such as EPDM, etc.), crosslinking agents, crosslinking aids, fillers, plasticizers, stabilizers, lubricants, etc. Ensure that the quality and purity of raw materials meet production requirements.
Mix
Add the weighed raw materials into the high-speed mixer for thorough mixing. During the mixing process, each component is uniformly dispersed by high-speed stirring to form a premix. This step is crucial for ensuring consistency in product performance.
Banburying
Add the premix to the mixer for mixing. The internal mixer provides a high temperature, high pressure, and strong shear environment, allowing the rubber to fully mix with the matrix resin and begin partial cross-linking reactions. The mixing temperature is generally controlled between 150-200 ℃, and adjusted according to the specific formula and raw material characteristics. The mixing time is usually 10-30 minutes to achieve the desired mixing and cross-linking effect.
Squeeze out
The material after mixing is discharged from the mixing machine and sent to a single screw or twin-screw extruder for extrusion. The extruder further plasticizes the material evenly and extrudes it into strips through the die of the machine head. The extrusion temperature is generally around 160-220 ℃, and the screw speed is adjusted according to the flowability of the material and product requirements. During the extrusion process, an appropriate amount of cooling medium, such as cooling water or air, can be added as needed to cool and shape the extruded material.
Diced
The extruded strip material enters the granulator through a traction device and is cut into particles of a certain length to obtain TPV masterbatch. The tool speed and traction speed of the granulator need to be adjusted in coordination to ensure uniform particle size.
Package
The cut TPV masterbatch is packaged using packaging materials such as plastic woven bags or kraft paper bags to prevent moisture, contamination, and oxidation of the masterbatch. Packaged products should be stored in a dry and ventilated warehouse, avoiding direct sunlight and high temperature environments.
Throughout the entire production process, it is necessary to strictly control various process parameters such as temperature, pressure, time, speed, etc. to ensure the stability and consistency of product quality. At the same time, it is necessary to conduct quality testing on the produced TPV masterbatch, including inspection of appearance, particle size, density, mechanical properties, cross-linking degree, and other indicators. Only products that meet quality standards can enter the market for sale.
Production equipment
The production process of TPV masterbatch requires the use of various equipment, and the following are the main production equipment and their functions:
1. High speed mixer: used to thoroughly mix various raw materials, such as matrix resin, rubber, crosslinking agent, filler, etc., to evenly disperse each component and form a premix. By using high-speed rotating stirring blades, uniform mixing of materials can be achieved in a short period of time, providing raw materials with uniform composition for subsequent production processes.
2. Internal mixer: Its working principle is to use two relatively rotating rotors to exert strong shearing, squeezing, and stirring effects on materials in a closed mixing chamber. Under high temperature and high pressure conditions, thoroughly mixing rubber with the matrix resin and initiating partial cross-linking reactions can help improve the uniformity and cross-linking degree of the material, and enhance product performance.
3. Extruder: Generally, single screw or twin-screw extruders are used. Single screw extruder has a simple structure and easy operation, suitable for occasions with low shear requirements; Twin screw extruders have better mixing performance and self-cleaning ability, which can effectively plasticize materials evenly and extrude them into strips through the head die. At the same time, additives can be added or further mixing reactions can be carried out during the extrusion process.
4. Granulator: Common types include hot pelletizers and cold pelletizers. Hot cutting granulator is used to cut materials in a thermoplastic state. By synchronously cooperating with the extruder, the extruded strip is cut into particles of the desired length; The cold granulator first cools and solidifies the extruded material before cutting, which is suitable for applications that require high precision in particle shape and size.
5. Traction device: located between the extruder and the pelletizer, its main function is to smoothly pull the strip material extruded by the extruder to the pelletizer, while controlling the traction speed to match the extrusion speed and pelletizing speed, to ensure the uniformity of particle size and the stability of the production process.
6. Cooling equipment: used to cool and shape the extruded strip to ensure product quality. There are two common cooling methods: air cooling and water cooling. Air cooled equipment takes away heat through forced air convection, with a simple structure and low cost, but relatively slow cooling speed; Water cooling equipment uses water as a cooling medium, which has a fast cooling speed and can effectively improve production efficiency and product quality, but requires corresponding water circulation systems.
7. Measuring equipment: including various electronic scales, flow meters, etc., used for precise weighing and measurement of the input amount of various raw materials, as well as controlling the amount of additives added to ensure the accuracy of the formula and the stability of product quality.
8. Packaging equipment: used to package the produced TPV masterbatch, commonly including automatic packaging machines, which can achieve automation of packaging processes such as measurement, filling, and sealing, improve packaging efficiency and quality, and ensure that the product is not damp or contaminated during storage and transportation.
TPV masterbatch extruder
Kerke’s masterbatch extruder can be used to produce TPV masterbatch. Our TPV masterbatch extruder has multiple models to choose from, which can meet different production requirements.
-
Extrusora de doble husillo para laboratorio
¿Cuándo necesitará una extrusora de doble husillo de laboratorio? Si desea realizar ensayos y pruebas de...
-
Extrusora de doble husillo paralelo
Nuestra extrusora de doble husillo paralelo corrotante está diseñada para la fabricación de compuestos y...
-
Extrusor triple (3 tornillos)
La extrusora de 3 tornillos es una nueva tecnología que tiene muchas ventajas. La extrusora de triple tornillo se utiliza principalmente...
-
Sistema de extrusión de doble etapa
El sistema de extrusión madre-bebé está diseñado para materiales especiales que no pueden procesarse en una extrusora de una etapa,...
-
Línea de amasado Banbury
Nuestra amasadora + extrusora está diseñada para realizar aplicaciones especiales con una capacidad de producción de 30kg/h a 1000kg/h....
-
Sistema de corte / Sistema de granulación
Diferentes materiales necesitan diferentes sistemas de corte, Kerke ofrece todo tipo de sistemas de corte, aquí está la explicación de...
Related requirements
The extruder plays a key role in the production of TPV masterbatch, and the following are some requirements for the extruder:
Good plasticizing ability: It can fully plasticize various raw materials with different properties, such as high melting point matrix resins and elastic rubber, at a certain temperature and pressure, making them a uniform melt, laying the foundation for subsequent molding and processing.
Accurate temperature control: Due to the strict temperature requirements of different raw materials and process stages in the production process of TPV masterbatch, the extruder needs to be equipped with a high-precision temperature control system that can accurately control the temperature of each heating zone within the temperature range of 160-220 ℃ to ensure that the material is plasticized, mixed, and extruded under appropriate temperature conditions, avoiding product performance degradation caused by high or low temperature.
Stable pressure output: During the extrusion process, it is necessary to provide stable pressure so that the material can be extruded through the die at a uniform speed, ensuring the dimensional accuracy and surface quality of the extruded material, and reducing problems such as uneven product thickness and surface roughness caused by pressure fluctuations.
Efficient mixing performance: For TPV masterbatch, a multi-component composite material, the extruder needs to have good mixing performance, which can fully mix various additives such as matrix resin, rubber, crosslinking agent, filler, etc. evenly in the melt to ensure the consistency of product performance. Twin screw extruders typically outperform single screw extruders in terms of mixing performance due to their stronger shear and dispersion capabilities.
Strong shearing ability: Appropriate shearing action helps to evenly disperse the rubber phase in the matrix resin and promote cross-linking reaction. The extruder should be able to provide appropriate shear strength according to different formulations and process requirements, so that the material can achieve ideal mixing and cross-linking effects during the extrusion process.
Reliable screw design: The screw is the core component of the extruder, and its structure and parameter design should be optimized based on the characteristics of TPV masterbatch and production process. For example, the length to diameter ratio, groove depth, compression ratio, and other parameters of the screw should be selected reasonably to meet the requirements of material transportation, plasticization, mixing, and extrusion. At the same time, the screw should have sufficient wear resistance and corrosion resistance to ensure stable operation under long-term high-speed rotation and high temperature and high pressure environments.
High degree of automation control: In order to improve production efficiency and product quality stability, extruders should have a high level of automation control, which can automatically monitor, adjust, and control key process parameters such as temperature, pressure, and speed, reduce manual operation errors, and can be linked with other production equipment to achieve automation of the entire production process.
Aplicación
TPV masterbatch (thermoplastic vulcanized rubber masterbatch) has good elasticity, weather resistance, chemical corrosion resistance and other characteristics, so it has a wide range of applications in multiple fields. The following are some of the main application areas:
Automotive industry
Seals: Used for sealing car doors, windows, engine compartments, trunk, and other parts, which can effectively prevent rainwater, dust, noise, etc. from entering the car, while also serving as shock absorbers and buffers.
Rubber hoses: Manufacturing cooling water pipes, fuel pipes, etc. for automobiles. TPV masterbatch has good oil resistance and high and low temperature resistance, which can ensure that rubber hoses will not experience aging, cracking, and other problems during long-term use.
Interior parts: such as car seat armrests, dashboard frames, etc. TPV masterbatch can provide a soft touch and good wear resistance, enhancing the quality and comfort of the interior.
Wire and cable
Insulation layer and sheath: TPV masterbatch has excellent electrical insulation performance and weather resistance, which can effectively protect wires and cables from external environmental influences, prevent leakage and short circuit accidents. At the same time, it also has good flexibility, making it easy to install and use wires and cables.
Construction industry
Waterproof membrane: The waterproof membrane made of TPV masterbatch has good water resistance, weather resistance, and puncture resistance, which can effectively prevent building leakage and extend the service life of buildings.
Sealing strip: Used for sealing building doors and windows, it can improve the sealing and insulation performance of doors and windows, and reduce energy consumption.
Medical equipment
Medical catheters: TPV masterbatch has good biocompatibility and chemical corrosion resistance, and can be used to manufacture medical catheters such as urinary catheters, infusion tubes, etc., which can meet the safety and reliability requirements of medical devices.
Medical device accessories: such as handles, buttons, etc. of medical devices, TPV masterbatch can provide comfortable grip and good wear resistance.
Other areas
Shoe material: Used for manufacturing shoe soles, edges, and other parts, TPV masterbatch has good elasticity and anti slip performance, providing a comfortable wearing experience.
Sports equipment: such as the inner liner of basketball, football and other balls, as well as the handle of sports equipment, TPV masterbatch can provide good elasticity and feel.
Electronic appliances: Used for manufacturing the shells, buttons, etc. of electronic and electrical products. TPV masterbatch has good insulation performance and weather resistance, which can protect electronic components from external environmental influences.