TPE masterbatch, also known as thermoplastic elastomer masterbatch, is a new type of polymer material that combines the characteristics of rubber and plastic, and has a wide range of applications in multiple fields.
Proceso de producción
The production process of TPE masterbatch usually includes the following key steps:
1. Ingredients
Raw material selection: Based on the performance requirements of the product, choose the appropriate TPE matrix resin, such as SEBS, SBS, POE, etc. At the same time, select matching filling oils, additives (such as antioxidants, light stabilizers, color masterbatch, etc.), and other resins that may be added (such as PP, PS, etc.). Ensure that the quality of all raw materials meets production requirements and has corresponding quality inspection reports.
Accurate weighing: Use high-precision electronic scales to accurately weigh various raw materials according to the product formula. The ratio of each raw material varies for different types of TPE masterbatch. For example, when producing SEBS based TPE masterbatch, SEBS、 The proportion of filling oil, PP or PS, and additives should be accurately adjusted based on the hardness, elasticity, weather resistance, and other properties of the target product.
2. Mezcla
Pre mixing: Add the weighed raw materials into a high-speed mixer for pre mixing. The high-speed mixer achieves preliminary uniform dispersion of various raw materials in a short period of time through the high-speed rotating stirring blades. During the pre mixing process, an appropriate amount of processing aids can be added as needed to improve the processing performance and mixing effect of the raw materials.
Adequate mixing: The pre mixed material enters the feed inlet of the twin-screw extruder, and in the conveying and mixing sections of the twin-screw extruder, the material is further thoroughly mixed under the rotation and shearing of the screw. The screw structure and speed setting of twin-screw extruders play a key role in the mixing effect of materials, and usually need to be optimized and adjusted according to the characteristics of the raw materials and product requirements.
3. Melt extrusion
Heating plasticization: The twin screw extruder barrel is equipped with multiple heating zones, which gradually heat the material inside the barrel to a molten state through heating devices. Different TPE raw materials have different melting points and processing temperature ranges. For example, the processing temperature of SEBS based TPE is generally between 180-220 ℃, while the processing temperature of polyurethane TPE may be higher, usually around 200-250 ℃. It is necessary to precisely control the temperature of each heating zone to ensure that the material can be uniformly plasticized during the extrusion process.
Extrusion molding: After the material is melted and plasticized, the screw of the twin-screw extruder pushes the molten material forward and extrudes it into continuous strips or sheets through the extrusion mold. The design of the extrusion mold determines the initial shape and size of TPE masterbatch. Common mold head shapes include circular, square, etc., which can be selected according to the requirements of subsequent granulation. At the same time, by adjusting the screw speed and feeding speed of the extruder, the output and line speed of the extruded material can be controlled, ensuring the stability of production efficiency and product quality.
4. Cooling and shaping
Water cooling: For TPE masterbatch production that requires high cooling speed, water cooling is often used. Directly introduce the TPE strip or sheet extruded from the extrusion mold into the water cooling tank, and rapidly solidify and shape the TPE material through the rapid cooling of circulating water. The water temperature in the water-cooled tank needs to be controlled within a certain range, usually 20-40 ℃, to avoid internal stress or surface defects in the product caused by too fast cooling rate.
Air cooling: The air cooling method is relatively mild and suitable for TPE masterbatch that is sensitive to moisture or has high requirements for product surface quality. Blow cold air towards the extruded TPE material through a fan, gradually cooling and shaping it in the air. The cooling speed of air cooling is slow, but it can effectively avoid the problem of residual moisture during the water cooling process, and also reduce defects such as water marks on the surface of the product caused by water cooling.
5. Granulation
Hot cutting: The hot cutting granulator is a device that cuts TPE materials while they are in a hot state. It usually uses a rotating tool to cut the extruded continuous TPE strip into particles of the desired length. The advantages of the hot cutting method are high production efficiency, regular particle shape, and good size uniformity, making it suitable for large-scale industrial production. But the equipment is relatively complex and requires specialized heating and cooling systems to ensure the smooth progress of the granulation process.
Cold cutting: A cold granulator is a device that cuts TPE materials after they have completely cooled down. It usually uses a fixed cutting tool to cut the cooled TPE strip into particles through a mechanical transmission device. The equipment structure of cold cutting method is simple, with lower operation and maintenance costs, but the cutting speed is relatively slow, and the uniformity of particle size may not be as good as that of hot cutting method. Suitable for some small-scale production or occasions where particle shape requirements are not particularly strict.
6. Packaging
Measurement packaging: The TPE masterbatch after granulation is quantitatively packaged through an automatic measuring device. According to the sales specifications of the product and customer needs, common packaging specifications include 25kg/bag, 50kg/drum, etc. The automatic measuring packaging machine can accurately control the packaging weight, improve packaging efficiency and accuracy.
Packaging material selection: Choose suitable packaging materials, such as plastic woven bags, composite packaging bags, or plastic drums, to package TPE masterbatch. The packaging material should have good moisture, dust, and damage resistance to protect the quality of TPE masterbatch during storage and transportation from being affected. At the same time, the product name, specifications, production date, shelf life and other relevant information should be indicated on the packaging for easy management and traceability.
Production equipment
The production process of TPE masterbatch involves various equipment, and the following are the main production equipment and their functions:
1. Equipo de ingredientes
Electronic scale: used for precise weighing of various raw materials to ensure the accuracy of ingredient ratios. Its accuracy is usually required to reach ± 0.1g or even higher to meet the precise requirements of different product formulas for raw material dosage.
Raw material storage tank: used to store various raw materials, such as TPE matrix resin, filling oil, additives, etc. Storage tanks typically have different capacities, selected based on production scale and raw material usage, typically ranging from 0.5 to 5 cubic meters.
2. Hybrid equipment
High speed mixer: By using high-speed rotating stirring blades, the raw materials are initially uniformly mixed in a short period of time. It has a fast mixing speed and can generally complete a mixing process within 5-15 minutes, which can effectively improve production efficiency.
Twin screw extruder: plays a key role in TPE masterbatch production, as it not only achieves sufficient mixing of materials, but also performs melt extrusion on the materials. The parameters such as screw diameter, aspect ratio, and groove depth of twin-screw extruders can affect the mixing effect and processing performance of materials. Common screw diameters are 35-90mm, and aspect ratios are between 20-40.
3. Melt extrusion equipment
Heating device: installed on the barrel of a twin-screw extruder, used to heat the material inside the barrel to a molten state. Heating methods usually include resistance heating, electromagnetic heating, etc. The heating temperature can be precisely controlled according to different TPE raw materials, with an accuracy generally within ± 5 ℃.
Extrusion mold: determines the initial shape and size of TPE masterbatch, and common mold head shapes include circular, square, etc. The design and processing accuracy of molds have a significant impact on the appearance quality and dimensional accuracy of products, and their materials are generally made of wear-resistant and corrosion-resistant alloy steel.
4. Cooling and shaping equipment
Water cooling tank: used for rapid cooling and shaping of extruded TPE materials. The length, width, and depth of the water cooling tank are designed according to the production scale and product specifications. Generally, the length is between 2-5 meters, and the width and depth are around 0.2-0.5 meters.
Air cooling system: composed of fans, air ducts, etc., it gradually cools and shapes the extruded TPE material by blowing cold air towards it in the air. The fan power and air volume of the air-cooled system need to be adjusted according to production speed and product requirements to ensure cooling effect.
5. Granulation equipment
Hot cutting machine: Cutting TPE materials in a hot state, with high production efficiency, regular particle shape, and good size uniformity. It mainly consists of rotating cutting tools, transmission devices, heating and cooling systems, etc. The cutting speed can be adjusted according to production needs, and can generally cut thousands or even more particles per minute.
Cold granulator: The TPE material is completely cooled before being pelletized. The equipment has a simple structure and low operation and maintenance costs. Cold granulators usually use fixed cutting tools to cut the cooled TPE strips into particles through mechanical transmission devices. The cutting speed is relatively slow, usually several hundred times per minute.
6. Packaging equipment
Automatic measuring packaging machine: capable of accurately controlling the packaging weight of TPE masterbatch, improving packaging efficiency and accuracy. Its measurement accuracy can reach within ± 0.1kg, and the packaging speed varies depending on different specifications and models. Generally, it can pack 10-50 bags (barrels) per hour.
Packaging material processing equipment: such as plastic woven bag printing machines, composite packaging bag making machines, etc., used to process and print packaging materials to meet the requirements of product packaging. The production speed and processing accuracy of these devices will affect the quality and efficiency of packaging.
TPE masterbatch extruder
Kerke’s masterbatch extruder can be used to produce TPE masterbatch. Our TPE masterbatch extruder has multiple models to choose from, which can meet different production requirements.
-
Extrusora de doble husillo para laboratorio
¿Cuándo necesitará una extrusora de doble husillo de laboratorio? Si desea realizar ensayos y pruebas de...
-
Extrusora de doble husillo paralelo
Nuestra extrusora de doble husillo paralelo corrotante está diseñada para la fabricación de compuestos y...
-
Extrusor triple (3 tornillos)
La extrusora de 3 tornillos es una nueva tecnología que tiene muchas ventajas. La extrusora de triple tornillo se utiliza principalmente...
-
Sistema de extrusión de doble etapa
El sistema de extrusión madre-bebé está diseñado para materiales especiales que no pueden procesarse en una extrusora de una etapa,...
-
Línea de amasado Banbury
Nuestra amasadora + extrusora está diseñada para realizar aplicaciones especiales con una capacidad de producción de 30kg/h a 1000kg/h....
-
Sistema de corte / Sistema de granulación
Diferentes materiales necesitan diferentes sistemas de corte, Kerke ofrece todo tipo de sistemas de corte, aquí está la explicación de...
Related requirements
In the production process of TPE (thermoplastic elastomer) masterbatch, the extruder needs to have the following properties to meet the characteristics of TPE materials and production process requirements:
Good plasticizing and mixing ability
Screw design: TPE is usually composed of a rubber phase and a plastic phase. In order to evenly mix and fully plasticize the two phases, the screw needs to have a suitable structure. Generally, a gradient screw is used, which has a longer compression section and can achieve smooth plasticization of the material under gradually increasing pressure and temperature. The aspect ratio is generally between 28-36 to provide sufficient plasticization and mixing length. In addition, appropriate mixing elements such as pins and kneading blocks should be installed on the screw to enhance the shearing and mixing effect of the material, so that various components in TPE can be uniformly dispersed.
Drive power: Due to the energy consumption required for plasticizing TPE materials, the extruder needs to be equipped with a sufficiently powerful drive motor. For extruders with different output rates, such as equipment with an hourly output of 50-300 kilograms, the driving power is usually around 15-75 kilowatts to ensure that the screw can rotate at the appropriate speed, overcome material resistance, and achieve good plasticization and mixing.
Accurate temperature control
Temperature control system: TPE masterbatch production has strict temperature requirements. Excessive temperature may lead to material degradation and performance degradation, while low temperature may affect plasticization effect and product quality. The extruder should be equipped with a high-precision temperature control system, using electric heating or thermal oil heating methods, and precise temperature monitoring and feedback control through temperature sensors such as thermocouples. The temperature control accuracy should be within ± 1 ℃ to ensure that TPE can be in the appropriate temperature range at all processing stages. For example, in the melting stage of TPE, the temperature is generally controlled between 160-200 ℃, and the specific temperature is adjusted according to the formula and performance requirements of TPE.
Cooling system: After TPE masterbatch is extruded, it needs to be quickly cooled and shaped to prevent masterbatch adhesion and deformation. Extruders are usually equipped with air or water cooling devices to cool the head and extruded masterbatch. The air-cooled system controls the cooling speed by adjusting the wind speed and volume of the fan, while the water-cooled system achieves cooling by circulating water flow and temperature. The cooling rate should be adjusted reasonably according to the size, shape, and production speed of the masterbatch to ensure that the masterbatch has good appearance and performance.
Stable pressure control
Extrusion pressure: Stable extrusion pressure is crucial for ensuring the dimensional accuracy and appearance quality of TPE masterbatch. The hydraulic or mechanical transmission system of the extruder should be able to provide stable pressure output, with pressure fluctuations generally controlled within ± 3%. Stable pressure can maintain a uniform flow rate of the material during extrusion, thereby producing TPE masterbatch with smaller diameter and length tolerances.
Adjustment device: In order to adapt to different production processes and product requirements, extruders should have flexible pressure adjustment devices. Operators can precisely control the extrusion pressure by adjusting the back pressure of the screw, changing the pressure parameters of the hydraulic system, or adjusting the throttle device of the machine head. For example, when producing high hardness TPE masterbatch, it may be necessary to increase the extrusion pressure appropriately to ensure that the material can fully fill the mold and achieve good molding results.
Reliable material transportation
Accurate feeding: The production of TPE masterbatch requires precise control of the amount of various materials added, so the feeding device of the extruder should use high-precision feeding equipment, such as weight loss feeders or screw feeders. These feeders can accurately deliver TPE raw materials, additives, and other materials to the extruder according to the set formula ratio. At the same time, the feeder should have good sealing and stability to prevent material leakage and uneven feeding, ensuring accurate proportioning of materials during the production process.
Screw conveying accuracy: The machining accuracy and assembly quality of the screw directly affect the stability of material conveying. The pitch and diameter tolerances of the screw should be controlled within a small range, generally with a pitch tolerance of no more than ± 0.05 millimeters and a diameter tolerance of no more than ± 0.03 millimeters, to ensure that the material can be stably conveyed forward in the screw groove and avoid material retention or fluctuation. In addition, the gap between the screw and the barrel should be uniform and consistent. If the gap is too large, it can easily cause material reflux and affect conveying efficiency; If the gap is too small, it may cause excessive material shearing and screw wear.
Corrosion resistance and wear resistance
Corrosion resistant materials: Some corrosive additives or additives may be used in the TPE production process, so components such as the extruder barrel and screw that come into contact with the material need to be made of corrosion-resistant materials. The barrel is usually protected by lining with stainless steel or spraying a corrosion-resistant coating, while the screw can be made of alloy steel with good corrosion resistance and surface treated, such as hard chromium plating or electroless nickel plating, to improve its corrosion resistance and extend the service life of the equipment.
Wear resistant design: In the production process of TPE masterbatch, there will be certain friction between the material and the screw and barrel, especially in the case of high-speed extrusion or adding fillers, the wear is more obvious. In order to improve the wear resistance of the equipment, the surface of the screw and barrel should have high hardness and wear resistance. In addition to selecting suitable materials, special heat treatments such as quenching and tempering can also be applied to the screw and barrel to improve their surface hardness. In addition, wear-resistant liners can be installed in the feeding section and easily worn parts of the barrel for regular replacement and to reduce equipment maintenance costs.
Automated Control and Monitoring
Control System: Modern TPE masterbatch production extruders are typically equipped with advanced automation control systems, such as PLC (Programmable Logic Controller) or DCS (Distributed Control System). These systems can achieve real-time monitoring and precise control of parameters such as temperature, pressure, screw speed, and material flow rate of the extruder. Operators can easily set and adjust production parameters through the human-machine interface (HMI), monitor and manage the production process, and improve production efficiency and product quality stability.
Fault diagnosis and warning: The automation control system should also have fault diagnosis and warning functions. The system can monitor the operating status of equipment in real time. When abnormal situations occur, such as high temperature, abnormal pressure, motor overload, etc., it can promptly issue alarm signals and automatically take corresponding protective measures, such as stopping the machine or reducing production speed. At the same time, the system can also record fault information to help maintenance personnel quickly locate and troubleshoot faults, reduce equipment downtime, and improve production continuity and reliability.
Type
There are various types of TPE (thermoplastic elastomer) masterbatch, and the following are some common classifications and characteristics:
According to the classification of basic polymers
Styrene TPE masterbatch
Based on styrene block copolymers, such as SBS (styrene butadiene styrene block copolymer), SEBS (hydrogenated styrene butadiene styrene block copolymer), etc.
It has good elasticity, flexibility, and low-temperature performance, as well as good processing performance, and can be formed and processed on various processing equipment.
Widely used in shoe materials, wires and cables, automotive interiors, toys and other fields. For example, in shoe materials, it can be used to make shoe soles, providing good elasticity and comfort; In wires and cables, as insulation and sheath materials, it has good weather resistance and flexibility.
Polyolefin TPE masterbatch
It is usually prepared by blending polyolefin resins (such as PP, PE) with elastomers (such as POE, EPDM, etc.) through processes such as blending or reactive extrusion.
It has excellent chemical corrosion resistance, weather resistance, and heat resistance, as well as low density and relatively low cost.
Commonly used in fields such as automotive parts, pipes, films, injection molded products, etc. For example, in automotive components, it can be used to manufacture bumpers, dashboards, etc., with good rigidity and toughness; In the field of pipe materials, it can be used to produce pipes with high pressure resistance and environmental stress cracking resistance.
Polyurethane TPE masterbatch
Made by polymerization reaction of isocyanates, polyols, and chain extenders.
It has excellent properties such as high elasticity, high strength, wear resistance, oil resistance, and also has good biocompatibility.
Commonly used in fields such as medical supplies, sports equipment, clothing, shoe soles, etc. In medical supplies, it can be used to manufacture catheters, artificial organs, etc; In sports equipment, insoles, ball shells, etc. used to make sports shoes provide good elasticity and support.
Polyester TPE masterbatch
Obtained by blending polyester resin as the matrix and modifying it with elastomers or other additives.
It has good mechanical properties, heat resistance, and water resistance, as well as good processing performance and dimensional stability.
Applied in fields such as electronics, automobiles, textiles, etc. In electronic appliances, it can be used to manufacture insulation layers for wires and cables, casings for electronic components, etc; In the textile industry, it can be used to produce fibers and fabrics with elasticity.
Classify based on performance characteristics
Universal TPE masterbatch
Having general physical and processing properties, it can meet the requirements of most ordinary application scenarios.
The price is relatively low and has a wide range of applications, such as daily necessities, toys, simple plastic products, and other fields.
High performance TPE masterbatch
It has high strength, hardness, heat resistance, chemical resistance and other special properties to meet some application fields with high requirements for material properties.
For example, in high demand fields such as automotive engine peripheral components, aerospace, electronics, etc., high-performance TPE masterbatch is needed to ensure the reliability and stability of products in harsh environments.
Special functional TPE masterbatch
Including TPE masterbatch with special functions such as flame retardancy, conductivity, anti-static, antibacterial, and degradability.
In order to prevent static electricity accumulation and fire hazards in electronic device casings, flame-retardant and anti-static TPE masterbatch will be used; In some medical products, antibacterial TPE masterbatch is used to prevent bacterial growth.
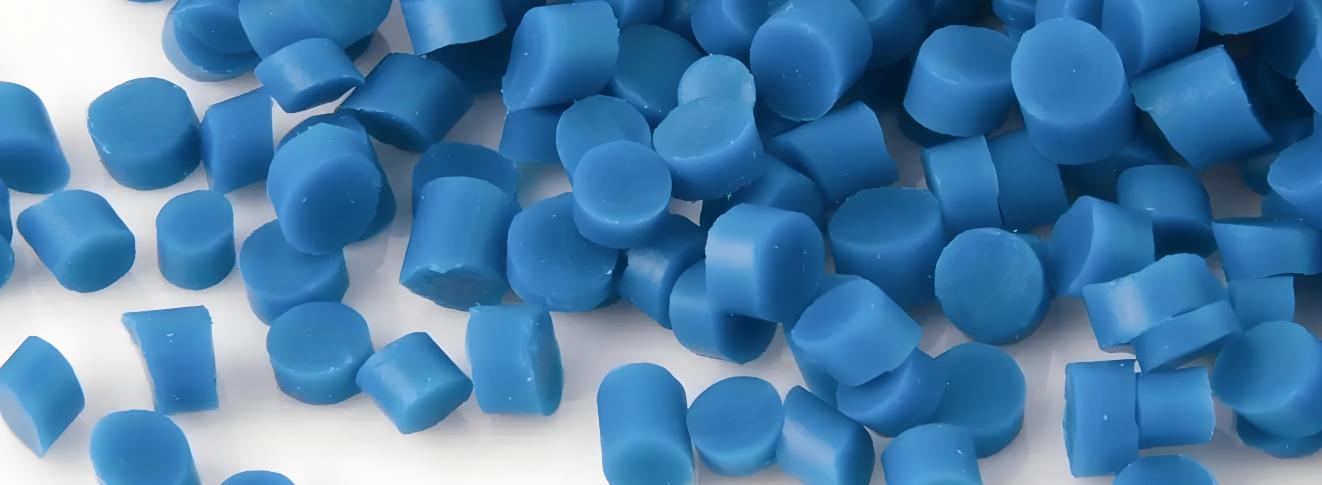
Fórmula
The ratio of TPE masterbatch may vary depending on different types, performance requirements, and application scenarios. Here are some examples of the approximate ratio range for common types of TPE masterbatch:
Styrene TPE masterbatch
SBS type
SBS resin: 30% -60%, providing elasticity and flexibility.
Filling oil: 30% -50%, used to reduce costs, improve processing performance, and enhance softness.
Calcium carbonate and other fillers: 0-20%, can increase hardness and reduce costs, but excessive use can affect elasticity.
Antioxidants and other additives: 0.5% -2%, prevent material aging and improve service life.
SEBS type
SEBS resin: 40% -70%, due to its hydrogenated structure, it has better weather resistance and stability.
Fill oil: 20% -40%, adjust hardness and processing performance.
Filler (such as talcum powder): 5% -20%, improves the rigidity and dimensional stability of the material.
Other additives (such as light stabilizers): 0.5% -3% to enhance light and aging resistance.
Polyolefin TPE masterbatch
PP/POE type
Polypropylene (PP): 50% -80%, providing rigidity and heat resistance.
Ethylene octene copolymer (POE): 20% -50%, endows the material with elasticity and toughness.
Compatibility agent: 2% -10%, improves the compatibility between PP and POE, and enhances the interfacial bonding strength.
Antioxidants, lubricants, etc.: 0.5% -3% to improve processing performance and material stability.
PE/EPDM type
Polyethylene (PE): 40% -70%, the material properties can be adjusted according to different types of PE (such as LDPE, HDPE).
Ethylene propylene diene monomer (EPDM): 30% -60%, providing good weather resistance, chemical resistance, and elasticity.
Crosslinking agent: 0.5% -3%, used to crosslink EPDM during processing, improving the strength and heat resistance of the material.
Other additives (such as UV absorbers): 0.5% -3% to enhance the weather resistance of the material.
Polyurethane TPE masterbatch
Conventional type
Polyester or polyether polyols: 40% -60%, are the soft segment of polyurethane, determining the elasticity and flexibility of the material.
Isocyanates: 20% -30%, react with polyols to form hard segments of polyurethane, providing strength and hardness.
Chain extender: 5% -15%, used to increase molecular chain length and improve material performance.
Catalyst: 0.1% -1%, accelerates the reaction.
Additives (such as anti yellowing agents): 0.5% -3% to prevent the material from turning yellow during use.
Polyester TPE masterbatch
PET/Elastic Type
Polyethylene terephthalate (PET): 50% -80%, providing excellent mechanical properties and heat resistance.
Elastic materials (such as TPU, TPEE, etc.): 20% -50%, improve the flexibility and elasticity of PET.
Plasticizer: 5% -15%, reduces the hardness of the material, improves processing performance and flexibility.
Stabilizer: 0.5% -3%, to prevent material degradation during processing and use.
It should be noted that the above ratio is only a general reference range. In actual production, it needs to be optimized and adjusted according to specific product requirements, raw material characteristics, and processing technology factors.
Aplicación
TPE masterbatch has a wide range of applications, including the following main areas:
1. Automotive industry
Interior parts: Used as skin materials for manufacturing car seats, steering wheels, instrument panels, etc., providing a soft touch and good wear resistance, while also having excellent weather resistance and chemical resistance, able to adapt to the complex environment inside the car.
Exterior components: can be used for car bumpers, mudguards, door seals, etc., with good elasticity and impact resistance, can provide cushioning in the event of a collision, and can resist the erosion of natural factors such as ultraviolet rays and rain.
Engine peripheral components, such as engine seals, oil pipes, etc., products made of TPE masterbatch have good heat resistance and oil resistance, and can maintain stable performance in high temperature and oily environments.
2. Electronic appliances
Wire and cable: As the insulation layer and sheath material of wire and cable, TPE masterbatch has good flexibility, bending resistance, and insulation performance, which can effectively protect the conductors inside the wire and cable, and is easy to install and use.
Electronic component casing: Used for manufacturing casings of electronic devices such as mobile phones, computers, and home appliances, it has good hand feel, scratch resistance, and impact resistance. At the same time, flame retardants and other additives can be added as needed to improve product safety.
Keyboard keys: The keyboard keys made of TPE masterbatch have good elasticity and touch, providing a comfortable typing experience and a long service life.
3. Medical field
Medical catheters: such as urinary catheters, infusion tubes, etc. TPE masterbatch has good biocompatibility, flexibility, and chemical resistance, which can meet the requirements of medical catheter use and reduce stimulation to human tissues.
Medical equipment accessories: used to manufacture some sealing components, gaskets and other accessories in medical equipment, with good corrosion resistance and elasticity, which can ensure the normal operation of medical equipment.
Artificial organs: In the manufacturing of some artificial organs, TPE masterbatch can be used as a substitute material with good biocompatibility and physical properties, which can simulate the characteristics of human tissue.
4. Shoe material industry
Sole: The sole made of TPE masterbatch has good elasticity, comfort, and anti slip performance, providing good support and cushioning effect. At the same time, the hardness and color can be adjusted according to different needs.
Shoe edge strip: Used for decoration and protection of shoe edges, it has good flexibility and wear resistance, and can be well combined with shoe upper materials.
Insole: The insole made of TPE masterbatch has good elasticity and breathability, which can effectively absorb foot pressure and provide a comfortable wearing experience.
5. Toy industry
Toy shell: TPE masterbatch has good processing performance and safety, and can be made into various shapes and colors of toy shells. At the same time, it has good impact resistance and can protect the internal structure of toys.
Toy accessories: such as toy wheels, handles, etc., have good elasticity and wear resistance, and can meet the requirements of toy use.
Soft toys: TPE masterbatch can be used to manufacture soft toys with a soft touch and good elasticity, which can increase the fun and playability of toys.
6. Packaging industry
Packaging film: Packaging film made from TPE masterbatch has good flexibility, transparency, and tear resistance, which can effectively protect packaging items. At the same time, anti-static agents and other additives can be added as needed to improve packaging performance.
Sealing element: Used for sealing packaging containers, it has good elasticity and sealing properties, and can prevent leakage of packaging items.
Labels made of TPE masterbatch have good adhesion and water resistance, and can be firmly attached to different packaging materials. At the same time, they have good weather resistance and are not easily faded or damaged.
7. Textile industry
Elastic fiber: TPE masterbatch can be used to produce elastic fibers such as spandex, which can endow textiles with good elasticity and resilience, and improve wearing comfort.
Fabric coating: Used for coating treatment of fabrics, it can improve the waterproof, windproof, and breathable properties of fabrics, while increasing the softness and hand feel of fabrics.
Clothing accessories: such as elastic bands and buttons for clothing, TPE masterbatch products have good elasticity and wear resistance, which can meet the requirements of clothing use.