PPS masterbatch is an additive used for polyphenylene sulfide (PPS) plastics. PPS is used as a carrier resin, and various functional additives (such as conductive agents, flame retardants, reinforcing agents, etc.) and other necessary additives are added to produce a granular product through mixing, extrusion, granulation and other processes.
Types
PPS masterbatch, also known as polyphenylene sulfide masterbatch, can be classified into the following types based on their functions and applications:
Enhanced PPS masterbatch
Usually, reinforcing materials such as glass fiber and carbon fiber are added. Adding glass fiber PPS masterbatch can improve the strength, rigidity, and dimensional stability of products, and is widely used in automotive parts, electronic appliances, and other fields, such as automotive engine peripheral components, electronic device casings, etc; PPS masterbatch with added carbon fiber not only has high strength and rigidity, but also endows the product with good electrical and thermal conductivity, making it suitable for high-end electronic device components that require electromagnetic shielding and heat dissipation performance.
Flame retardant PPS masterbatch
By adding flame retardants to achieve flame retardant effects. According to different flame retardant level requirements, the types and contents of flame retardants added may vary. This type of masterbatch has good flame retardant properties and can meet the strict requirements for material flame retardancy in fields such as electronics and aerospace. It can be used to manufacture insulation layers for wires and cables, shells for electronic and electrical products, etc., effectively preventing the occurrence and spread of fires.
Wear resistant PPS masterbatch
Generally, solid lubricants such as molybdenum disulfide and graphite or wear-resistant materials such as ceramic powder are added. Products made from wear-resistant PPS masterbatch have excellent wear resistance and self-lubricating properties, and can be used to manufacture mechanical components such as bearings, gears, sliders, etc. They can maintain good performance in high friction and high wear working environments, extending the service life of components.
Conductive PPS masterbatch
Add conductive materials such as carbon black, carbon fiber, and metal powder to give it good conductivity. Mainly used in the electronic industry where electrostatic protection or electromagnetic shielding is required, such as packaging materials for electronic devices, shielding covers for circuit boards, etc., it can effectively prevent static electricity accumulation and electromagnetic interference, and protect the normal operation of electronic devices.
High fluidity PPS masterbatch
By modifying PPS resin to reduce its melt viscosity and improve its flowability. This type of masterbatch is suitable for the molding of complex shaped and thin-walled products, and can quickly fill the mold cavity during the injection molding process, improving production efficiency and product quality. It is commonly used to manufacture small and precision electronic components and automotive interior parts.
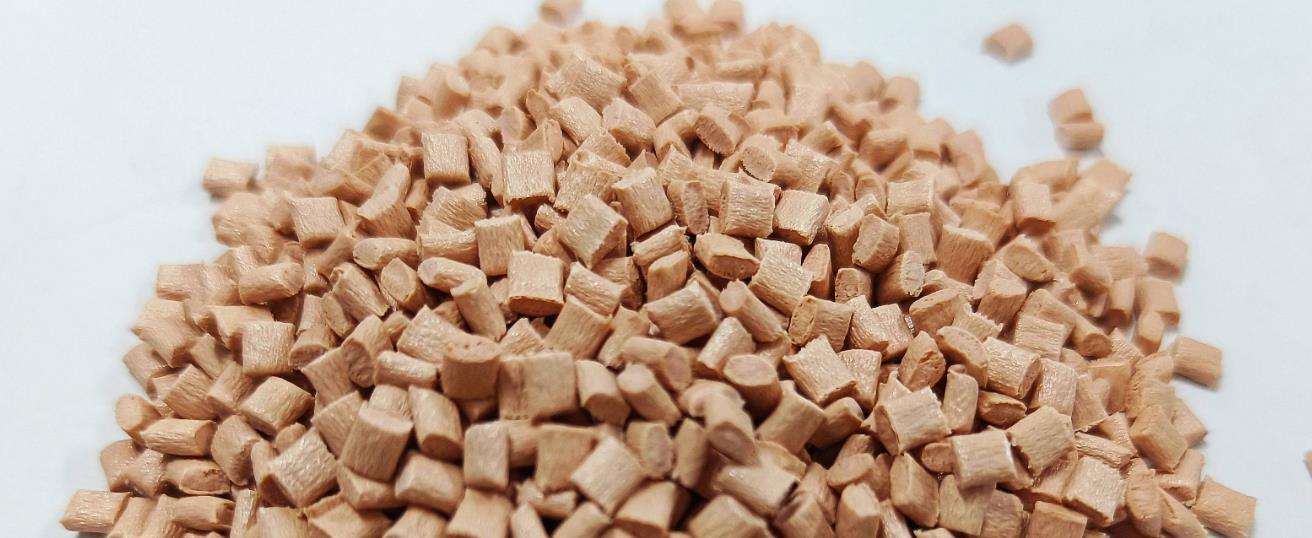
Fórmula
The proportion of different types of PPS masterbatch formulations may vary due to specific performance requirements, production processes, and raw material characteristics. Here are some examples of approximate formula ratios for common types of PPS masterbatch:
Enhanced PPS masterbatch
PPS resin: 60% -80%
Fiberglass: 20% -40%. If it is carbon fiber, the general addition amount is between 10% and 30%.
Other additives (such as coupling agents, lubricants, etc.): 0.5% -5%. Coupling agents can enhance the adhesion between fibers and resins, while lubricants can improve processing performance.
Flame retardant PPS masterbatch
PPS resin: 70% -90%
Flame retardant: 10% -30%. Common flame retardants include bromine based flame retardants, phosphorus based flame retardants, inorganic flame retardants, etc.
Other additives (such as anti drip agents, stabilizers, etc.): 0.5% -5%. Anti drip agents can prevent the phenomenon of melting droplets during combustion, while stabilizers help improve the stability of materials.
Wear resistant PPS masterbatch
PPS resin: 75% -90%
Wear resistant additives: 10% -25%. The addition amount of molybdenum disulfide and graphite is usually between 5% and 15%, while the addition amount of ceramic powder is generally between 10% and 20%.
Other additives (such as dispersants, etc.): 0.5% -5%. Dispersants can evenly disperse wear-resistant additives in resins.
Conductive PPS masterbatch
PPS resin: 70% -90%
Conductive filler: 10% -30%. The addition amount of carbon black is generally between 10% and 20%, carbon fiber is between 10% and 30%, and metal powder is between 15% and 30%.
Other additives (such as compatibilizers, etc.): 0.5% -5%. Compatibilizers can improve the compatibility between conductive fillers and resins.
High fluidity PPS masterbatch
PPS resin: 90% -98%
Liquidity improver: 2% -10%.
Other additives (such as antioxidants, etc.): 0.5% -5%. Antioxidants can prevent the oxidation and degradation of resins during processing.
These formula ratios are for reference only. In actual production, adjustments and optimizations need to be made based on specific product requirements, production equipment, and processes to obtain high-performance PPS masterbatch products.
Proceso de producción
The production process of PPS masterbatch generally includes the following main steps:
Preparación de la materia prima
PPS resin: Select appropriate PPS resin particles based on product performance requirements, and ensure that their molecular weight, viscosity, and other indicators meet production standards.
Additives: Accurately weigh various additives according to the formula, such as reinforcing materials (glass fiber, carbon fiber, etc.), flame retardants, wear-resistant agents, conductive fillers, flow improvers, and various additives (coupling agents, lubricants, anti drip agents, stabilizers, dispersants, compatibilizers, antioxidants, etc.). Ensure the quality and purity of additives to prevent impurities from affecting product performance.
Mix
High speed mixing: Add PPS resin and additives into the high-speed mixer for thorough mixing. By using high-speed rotating stirring blades, resin particles and additives are uniformly dispersed in a short period of time to form a preliminary mixed material. The mixing time is usually around 10-30 minutes, depending on the formula and equipment performance.
Pre mixing treatment: For some additives that are difficult to disperse, such as carbon fiber, ceramic powder, etc., pre mixing treatment can be carried out first. Pre mix these additives with some PPS resin in a small mixing device, and then add them to a high-speed mixer to mix with other materials to improve their dispersibility in the resin.
Granulación por extrusión
Melt extrusion: Add the mixed material into a twin-screw extruder. Twin screw extruders have excellent mixing, shearing, and conveying capabilities, which can fully melt and uniformly mix materials at high temperatures. The material undergoes multiple temperature zones in the extruder, from the feeding section to the extrusion section, and the temperature gradually increases. Generally, the melting temperature of PPS resin is between 280-320 ℃. During the melting process, additives are fully combined with PPS resin to form PPS masterbatch with specific properties.
Shear and mixing: The screw structure design of the twin-screw extruder causes strong shear and mixing effects on the material during the extrusion process. This shear force can evenly disperse additives in the PPS resin matrix, while also providing appropriate orientation and degradation of PPS resin molecular chains, thereby improving the processing and physical properties of the material. By adjusting the speed and combination of the screw, the degree of shearing and mixing can be controlled to meet the requirements of different products.
Extrusion granulation: After thorough mixing, the molten material is extruded from the head of the extruder to form continuous strips or filaments. Then, the PPS masterbatch is obtained by cutting it into particles of a certain length using a granulator. The cutting speed and tool adjustment should be based on the specifications of the masterbatch to ensure uniform particle size.
Cooling and drying
Cooling: The PPS masterbatch after cutting needs to be cooled in a timely manner to prevent particle adhesion and deformation. Usually, water or air cooling is used for cooling. The water cooling method has a fast cooling speed, but it may cause moisture adsorption on the surface of the particles, requiring subsequent drying treatment; The air cooling method is relatively mild, with dry particle surfaces but lower cooling efficiency. In actual production, suitable cooling methods or a combination of both can be selected according to specific circumstances.
Drying: For PPS masterbatch produced by water cooling or in humid environments, drying is an essential process. The purpose of drying is to remove moisture from the surface and interior of particles, preventing moisture from causing defects such as bubbles and silver lines during subsequent processing, which can affect product quality. The commonly used drying methods include hot air drying, vacuum drying, etc. The drying temperature is generally between 80-120 ℃, and the drying time depends on the moisture content of the particles and the performance of the drying equipment, usually 2-6 hours.
Packaging and Inspection
Packaging: Dry PPS masterbatch is packaged in sealed bags or plastic drums to prevent moisture, oxidation, or other contamination during storage and transportation. The packaging should indicate the product’s model, specifications, production date, shelf life, and other information for easy identification and management.
Inspection: Conduct quality inspection on the produced PPS masterbatch, including visual inspection (particle shape, color, size uniformity, etc.), physical property testing (such as melt index, density, tensile strength, bending strength, impact strength, etc.), and chemical property analysis (such as flame retardancy, conductivity, composition content, etc.). Only products that pass inspection can enter the market for sale or be used for subsequent processing and production.
Different manufacturers may make appropriate adjustments and optimizations to their production processes based on their own equipment conditions, technological level, and product characteristics, in order to improve production efficiency, reduce costs, and enhance product quality.
Production equipment
The main equipment for producing PPS masterbatch is as follows:
1. High speed mixer
Function: Used to thoroughly mix PPS resin with various additives, and achieve uniform dispersion of the material in a short period of time through high-speed rotating stirring blades.
Selection points: Choose the appropriate volume according to the production scale. Generally, small production lines can choose models with a capacity of 50-200L, while large production lines can choose models with a capacity of 500-2000L. At the same time, the material and shape of the stirring blades should be considered to ensure good mixing effect and wear resistance.
2. Twin screw extruder
Function: It is the core equipment for PPS masterbatch production, with efficient mixing, shearing, and conveying capabilities. It can fully melt materials at high temperatures and achieve uniform mixing and good dispersion of additives and PPS resin through the rotation and combination of screws. At the same time, it can also modify the materials to a certain extent.
Selection criteria: Choose the appropriate screw diameter and aspect ratio based on production capacity and product requirements. Generally speaking, the diameter of the screw is between 35-120mm, and the aspect ratio is between 20-40. For PPS masterbatch with high filling or performance requirements, screws with larger aspect ratios can be used to improve mixing and dispersion effects. In addition, parameters such as the heating method, cooling system, and driving power of the extruder need to be considered.
3. Granulator
Function: Cut the continuous strip or filamentous material extruded from the twin-screw extruder into particles of a certain length to obtain the finished shape of PPS masterbatch.
Selection key points: Select the type of granulator and the number of cutting blades based on the output of the extruder and the specifications of the masterbatch. Common pelletizers include hot pelletizers and cold pelletizers. Hot pelletizers are suitable for situations that require high particle appearance and dimensional accuracy, while cold pelletizers are suitable for situations that require high particle cooling. The material of the cutting blade should have good wear resistance and corrosion resistance to ensure the quality and stability of the cut particles.
4. Cooling equipment
Function: Cool the PPS masterbatch after cutting to prevent particle adhesion and deformation, ensuring the appearance and performance of the product.
Key selection points: Water cooling equipment should consider the length, width, and depth of the cooling water tank, as well as the flow rate and temperature control accuracy of the circulating water. For air-cooled equipment, attention should be paid to the air volume, air pressure, and cooling pipeline design of the fan to ensure uniform cooling effect. For PPS masterbatch with special requirements, such as moisture sensitive products, special cooling media or nitrogen protection cooling methods can be used.
5. Drying equipment
Function: Remove moisture from PPS masterbatch, prevent moisture from causing defects such as bubbles and silver lines during subsequent processing, and improve product quality.
Selection criteria: Choose the appropriate type of drying equipment based on production scale and drying requirements, such as hot air circulation drying oven, vacuum drying oven, or boiling dryer. Hot air circulation drying oven is suitable for small and medium-sized production, while vacuum drying oven is suitable for products with high drying requirements. Boiling dryer has the characteristics of fast drying speed and high efficiency, and is suitable for large-scale production. At the same time, parameters such as heating method, temperature control range, and uniformity of the drying equipment should be considered.
6. Packaging equipment
Function: The dried PPS masterbatch is packaged in sealed bags or plastic drums to prevent moisture, oxidation, or other contamination during storage and transportation.
Selection criteria: Choose appropriate packaging equipment based on packaging specifications and production efficiency, such as semi-automatic packaging machines or fully automatic packaging machines. The semi-automatic packaging machine is suitable for production lines with low output and requires manual assistance to complete some packaging operations; The fully automatic packaging machine can achieve automation of a series of operations from material conveying, measuring, packaging to sealing, and is suitable for large-scale production. In addition, the measurement accuracy, sealing quality, and packaging speed of the packaging equipment also need to be considered.
7. Testing equipment
Function: Conduct quality inspection on the produced PPS masterbatch, including appearance inspection, physical performance testing, chemical performance analysis, etc., to ensure that the product meets quality standards.
Selection points: Appearance inspection can use equipment such as optical microscopes or electron microscopes to observe the shape, size, and surface quality of particles. Physical performance testing equipment such as melt index meters, density meters, tensile testing machines, impact testing machines, etc. should be selected with appropriate range and accuracy based on the performance indicators of the product. Chemical performance analysis equipment such as elemental analyzers, infrared spectrometers, thermogravimetric analyzers, etc. are used to detect the composition, structure, and thermal stability of masterbatch. When selecting testing equipment, the reliability, accuracy, and ease of operation of the equipment should be considered, while complying with relevant national standards and industry norms.
PPS masterbatch extruder
Kerke’s masterbatch extruder can be used to produce PPS masterbatch. Our PPS masterbatch extruder has multiple models to choose from, which can meet different production requirements.
-
Extrusora de doble husillo para laboratorio
¿Cuándo necesitará una extrusora de doble husillo de laboratorio? Si desea realizar ensayos y pruebas de...
-
Extrusora de doble husillo paralelo
Nuestra extrusora de doble husillo paralelo corrotante está diseñada para la fabricación de compuestos y...
-
Extrusor triple (3 tornillos)
La extrusora de 3 tornillos es una nueva tecnología que tiene muchas ventajas. La extrusora de triple tornillo se utiliza principalmente...
-
Sistema de extrusión de doble etapa
El sistema de extrusión madre-bebé está diseñado para materiales especiales que no pueden procesarse en una extrusora de una etapa,...
-
Línea de amasado Banbury
Nuestra amasadora + extrusora está diseñada para realizar aplicaciones especiales con una capacidad de producción de 30kg/h a 1000kg/h....
-
Sistema de corte / Sistema de granulación
Diferentes materiales necesitan diferentes sistemas de corte, Kerke ofrece todo tipo de sistemas de corte, aquí está la explicación de...
Related requirements
In the production of polyphenylene sulfide (PPS) masterbatch, the extruder needs to meet various requirements such as high temperature control accuracy and strong shear mixing ability to ensure product quality and production efficiency. The following are specific requirements:
1. Temperature control
High temperature heating capacity: PPS has a high melting point, usually around 280 ℃ -300 ℃, so the extruder needs to have sufficient high temperature heating capacity to ensure that PPS resin can be fully melted. Generally, heating elements such as cast aluminum heating rings or ceramic heating rings are used to quickly heat the materials inside the barrel to the desired temperature.
Accurate temperature control: PPS masterbatch production requires extremely high temperature control accuracy, with temperature fluctuations controlled within ± 2 ℃. This is because excessive temperature may cause degradation of PPS resin, affecting product performance; If the temperature is too low, it will cause insufficient melting of the material, resulting in difficulties in extrusion and uneven surface of the product. Extruders are usually equipped with high-precision temperature sensors and intelligent temperature control systems, which can monitor and accurately adjust the temperature of each heating section in real time.
Rapid heating and cooling: During the production process, it is sometimes necessary to quickly adjust the temperature, such as during startup and shutdown cleaning. Therefore, the heating system of the extruder should have the ability to quickly raise temperature to shorten production preparation time; At the same time, the cooling system should also be able to respond quickly, achieve rapid cooling, and avoid material deterioration caused by prolonged residence at high temperatures.
2. Shear mixing ability
High strength screw: PPS resin has a high melt viscosity and requires an extruder to provide strong shear force to achieve good mixing and dispersion effects. Usually, a large aspect ratio (L/D) screw is used, with a typical L/D between 30-40, to increase the residence time and shear frequency of the material inside the screw. At the same time, the thread design of the screw is also crucial. The use of special mixing elements such as pin screws, barrier screws, etc. can enhance shear and mixing effects, allowing PPS resin to be uniformly mixed with various additives (such as fillers, additives, etc.).
Wear resistant and corrosion-resistant: Due to the corrosiveness of PPS and the significant wear of the material on the screw and barrel during the mixing process, wear-resistant and corrosion-resistant materials such as nitride steel, hard chromium plating, or tungsten carbide spraying need to be used for the screw and barrel to extend the service life of the equipment and ensure the stability of product quality.
3. Pressure control
Stable pressure maintenance: During the PPS masterbatch extrusion process, it is necessary to maintain a stable extrusion pressure to ensure the dimensional accuracy and appearance quality of the product. The hydraulic system or mechanical transmission system of the extruder should have good pressure stability and be able to maintain pressure fluctuations within a small range at different production speeds and material viscosities. Generally, pressure fluctuations should not exceed ± 5%.
High pressure output: In order to overcome the high viscosity of PPS melt and the resistance of extrusion molds, extruders need to have a high pressure output capability. The maximum extrusion pressure of the extruder is usually required to reach 30-50MPa to ensure that the material can pass smoothly through the head and mold, forming uniform masterbatch.
4. Material transportation
Uniform and stable: In the production of PPS masterbatch, it is required that the material be transported evenly and stably in the extruder to avoid material accumulation or breakage. This requires the design of the screw to adapt to the characteristics of PPS resin, ensuring that the material can move steadily forward in the screw groove. At the same time, the feeding device also needs to have precise metering and feeding functions, such as using weight loss feeders or volumetric feeders, which can accurately control the feeding amount of materials according to production process requirements, ensuring the stability of the extrusion process.
Preventing material degradation: PPS resin is prone to degradation at high temperatures, so during material transportation, it is important to minimize the residence time of materials in high-temperature areas. The screw speed and barrel structure design of the extruder should be reasonably optimized to enable materials to pass through the extruder quickly, while avoiding local overheating and retention of materials inside the barrel.
5. Automation control
Comprehensive parameter monitoring: Advanced automation control system is crucial for PPS masterbatch production. The system should be able to monitor various operating parameters of the extruder in real time, including temperature, pressure, screw speed, material flow rate, etc., and provide feedback to the operator or automatic control system. By real-time analysis and adjustment of these parameters, abnormal situations in the production process can be detected in a timely manner, and corresponding measures can be taken to handle them, ensuring the stability of the production process and the consistency of product quality.
Fault diagnosis and warning: The automation control system should also have fault diagnosis and warning functions, which can monitor the key components and systems of the extruder in real time. Once hidden faults are discovered, alarm signals should be issued in a timely manner, and corresponding fault handling suggestions should be provided. In addition, the system can also predict possible equipment failures through analysis of historical data, perform maintenance and upkeep in advance, and avoid the impact of equipment failures on production.
Aplicación
PPS masterbatch has excellent performance and is therefore widely used in multiple fields. The following are some of the main application areas:
Electronic and electrical field
Connector: PPS masterbatch has good electrical insulation performance, high temperature stability, and mechanical strength, which can meet the requirements of connectors in various complex environments, ensuring the stability and reliability of signal transmission.
Sockets and switches: Their flame retardant and arc resistant properties make them ideal materials for manufacturing electrical components such as sockets and switches, which can effectively prevent electrical fires and improve the safety of electrical use.
Coil skeleton: PPS masterbatch can maintain good dimensional stability at high temperatures, withstand the stress of coils during winding and use, and have excellent insulation properties to prevent coil short circuits and improve the performance and reliability of electronic devices.
Automotive industry field
Engine peripheral components: such as intake manifold, throttle body, engine hood, etc. PPS masterbatch can maintain stable performance in environments with high temperature, high humidity, and various chemical media. It has good oil resistance, corrosion resistance, and mechanical strength, which can reduce engine weight, improve fuel economy, and ensure the normal operation of the engine.
Automotive electronic components: used to manufacture electronic control unit (ECU) housings, sensor housings, etc. for automobiles. The electromagnetic shielding performance and good electrical insulation performance of PPS masterbatch can effectively protect electronic components from external electromagnetic interference, ensuring the stable operation of automotive electronic systems.
Car headlight components: PPS masterbatch can be used to manufacture components such as reflectors and lamp sockets for car headlights. It has high glossiness, good heat resistance, and dimensional stability, and can maintain its shape and performance unchanged in the high-temperature environment generated by long-term use of the car lamp, while ensuring the optical performance of the car lamp.
Aerospace field
Internal components of aircraft, such as seat frames, luggage racks, interior panels, etc. Components made from PPS masterbatch have the advantages of light weight, high strength, and good flame retardancy, which can reduce the overall weight of the aircraft, improve fuel efficiency, and ensure passenger safety.
Aircraft engine components: PPS masterbatch is also used in some non critical components of aircraft engines, such as fixed parts of fan blades and insulation parts of engine compartments. It can withstand high temperatures and vibrations during the operation of aircraft engines, has good wear resistance and fatigue resistance, and improves the reliability and service life of the engine.
Industrial sector
Mechanical parts: can be used to manufacture various mechanical parts, such as gears, bearings, cams, etc. PPS masterbatch has high hardness, wear resistance, and self-lubricating properties, which can reduce the friction coefficient between mechanical parts, reduce wear, improve the efficiency and reliability of mechanical transmission, and extend the service life of mechanical parts.
Chemical pipelines and valves: Due to the excellent chemical corrosion resistance of PPS masterbatch, it can be used to manufacture equipment components such as chemical pipelines, valves, and pump bodies. It can resist the erosion of various strong acids, strong bases, and organic solvents, ensuring the safe and stable operation of chemical production processes.
Filter material: Fibers made from PPS masterbatch can be used to produce high-temperature filter materials for industrial waste gas, wastewater treatment, and other fields. It has good high temperature resistance and chemical stability, and can effectively filter dust and impurities in high temperature, high humidity, and highly corrosive environments, protecting the environment and equipment.