Plant fiber masterbatch is a granular material made by compounding plant fibers (such as wood powder, bamboo powder, straw fiber, etc.) as reinforcing phases with thermoplastic polymers (such as polypropylene PP, polyethylene PE) and modification agents (such as silane coupling agents, maleic anhydride grafted polypropylene). Plant fiber masterbatch is widely used in plastic modification, composite material reinforcement, and environmental protection fields.
Characteristic
Plant fiber masterbatch is a functional masterbatch made from plant fibers (such as bamboo fiber, wood fiber, straw fiber, etc.) as the main raw material, mixed with polymer resins and additives for granulation. It is mainly used in the fields of plastic modification, environmental protection materials, etc. Its characteristics can be summarized as follows:
1. Environmentally friendly and renewable
Natural raw materials: with plant fibers as the core component, widely sourced (such as agricultural and forestry waste), belonging to renewable resources, reducing dependence on petroleum based plastics.
Degradability: Some plant fiber masterbatch can be combined with biodegradable resin to enhance the biodegradability of the product and reduce white pollution.
Low carbon and energy-saving: The production process has low carbon emissions, which is in line with the trend of green manufacturing.
2. Improve material properties
Enhanced mechanical properties: The addition of plant fibers can improve the rigidity, strength, and dimensional stability of plastics, especially suitable for replacing some traditional fillers (such as calcium carbonate).
Lightweight: With low fiber density, it can reduce the weight of products while maintaining a certain strength, making it suitable for lightweight demand scenarios such as automobiles and packaging.
Thermal insulation and sound insulation: The porous structure of plant fibers can enhance the thermal insulation and sound insulation effects of materials, which are used in fields such as construction and home furnishings.
3. Strong processing adaptability
Good dispersibility: Through surface modification treatment, the fiber and resin have good compatibility and are easily dispersed during extrusion, injection molding and other processing, without affecting the molding efficiency.
Adjustable: The fiber type (such as long fiber, short fiber), particle size, and formula can be adjusted according to the needs to meet the performance requirements of different products (such as hardness and toughness).
4. Functional Expansion
Natural characteristics preservation: Some plant fibers come with antibacterial properties (such as bamboo fibers), moisture absorption and breathability, giving the product additional characteristics.
Low moisture absorption: After modification treatment, the fiber water absorption rate can be reduced to avoid performance degradation caused by moisture in the product.
5. Widely applicable scenarios
Packaging materials: used for environmentally friendly plastic bags, express boxes, tableware, etc., balancing strength and degradability.
Automotive interior: Replace some plastic parts, reduce weight and improve environmental friendliness.
3D printing: As a bio based consumable material, it supports sustainable manufacturing.
6. Limitations
Insufficient water resistance: unmodified plant fibers are prone to water absorption and require surface treatment (such as coupling agent modification) to improve water resistance.
Limited high temperature resistance: Fibers are prone to decomposition at high temperatures, limiting their application in high heat resistant scenarios.
Plant fiber masterbatch combines environmental friendliness and functionality, and is an important material for promoting the greening of the plastic industry, especially suitable for fields that require strength, lightweight, and degradability. However, its water and heat resistance properties need to be optimized through modification technology to expand its application scope.
Types
According to the source of raw materials, fiber morphology, functional characteristics, and application scenarios of plant fiber masterbatch, its types can be classified from the following dimensions:
Classification by raw material source
1. Wood fiber masterbatch
Raw materials: wood processing waste (such as sawdust, wood powder), pulp fibers, etc., with a wide range of sources and low costs.
Characteristics: The fiber structure is uniform and can improve material rigidity and dimensional stability. It is commonly used in packaging and furniture board modification.
2. Bamboo fiber masterbatch
Raw materials: bamboo processing residues (such as bamboo chips and bamboo powder), with delicate fibers and natural antibacterial properties.
Characteristics: It combines high strength and antibacterial properties, suitable for fields with high hygiene requirements such as food packaging and baby products.
3. Straw fiber masterbatch
Raw materials: Crop straw (such as corn straw, rice husk, and wheat straw), which belongs to agricultural waste utilization and is environmentally friendly and low-carbon.
Features: The fiber surface is porous, which can improve the insulation and moisture absorption of materials. It is commonly used in biodegradable packaging, flower pots, etc.
4. Other natural fiber masterbatch
Such as coconut shell fiber, hemp fiber (jute, sisal), cotton fiber masterbatch, etc., adapted to different scenarios based on fiber characteristics (such as hemp fiber-reinforced composite materials).
Classified by fiber morphology
1. Long fiber masterbatch
The fiber length is relatively long (usually>1mm), in a bundle or continuous shape, significantly improving the impact strength and fatigue resistance of the material, suitable for automotive parts and sports equipment.
2. Short fiber masterbatch
Fiber short cutting to a certain length (such as 0.1-1mm) has good dispersibility, balances reinforcement effect and processing fluidity, and is commonly used in injection molded products (such as toys and daily necessities).
3. Powder/microfiber masterbatch
Fiber is crushed into micrometer sized powder, mainly used as a filler to improve material rigidity and surface texture, for films, boards, etc.
Classified by functional modification
1. Enhanced plant fiber masterbatch
Compound coupling agents (such as silane and titanate) improve the interfacial bonding between fibers and resins, significantly enhance the tensile strength and bending modulus of composite materials, and replace glass fibers for lightweight applications.
2. Flame retardant plant fiber masterbatch
Adding environmentally friendly flame retardants (such as phosphorus based and nitrogen based) to endow materials with flame retardant properties, suitable for electronic and electrical enclosures, and building decoration materials.
3. Antibacterial plant fiber masterbatch
Using natural antibacterial ingredients such as bamboo fiber or adding antibacterial agents for food contact materials and medical product packaging.
4. Biodegradable plant fiber masterbatch
Composite with biodegradable resins such as PLA and PBAT to enhance the biodegradation rate of products, with a focus on “fully bio based” environmentally friendly packaging and disposable tableware.
5. Functional composite masterbatch
Simultaneously possessing multiple properties (such as enhancement+degradation, antibacterial+flame retardant) to meet high-end customization needs.
Classified by application field
1. Plant fiber masterbatch for packaging
Focusing on environmental degradation, used for shopping bags, express envelopes, food boxes, etc., to reduce white pollution.
2. Plant fiber masterbatch for automobiles
Lightweight and high-strength, used for interior parts (dashboard, door panels), seat frames, reducing vehicle weight and meeting environmental standards of car manufacturers.
3. 3D printing consumables masterbatch
Composite with thermoplastic resins such as PLA to create printable biobased materials that support sustainable 3D printing.
4. Building and Home Masterbatch
Improve the thermal and sound insulation performance of the board, used for integrated wall panels, floor substrates, and insulation materials.
5. Masterbatches for daily necessities and consumer goods
Such as baby bottles, toys, and furniture accessories, balancing safety, environmental protection, and mechanical performance.
Classified by compatibility of matrix resin
1. Thermoplastic resin based masterbatch
Suitable for PP (polypropylene), PE (polyethylene), PLA (polylactic acid), etc., it is the most widely used and can be processed through extrusion and injection molding.
2. Thermosetting resin based masterbatch
Used for epoxy resin, unsaturated polyester, etc., rarely seen, mainly used for high-strength composite materials (such as wind turbine blade interlayer).
There are various types of plant fiber masterbatch, and the core differences stem from the selection of raw materials, fiber processing techniques, and functional modification directions. Users can choose the appropriate type based on specific needs such as environmental protection level, mechanical properties, and processing methods. In the future, with the advancement of modification technologies such as nanoscale surface treatment and composite functional integration, its application scenarios will be further expanded.
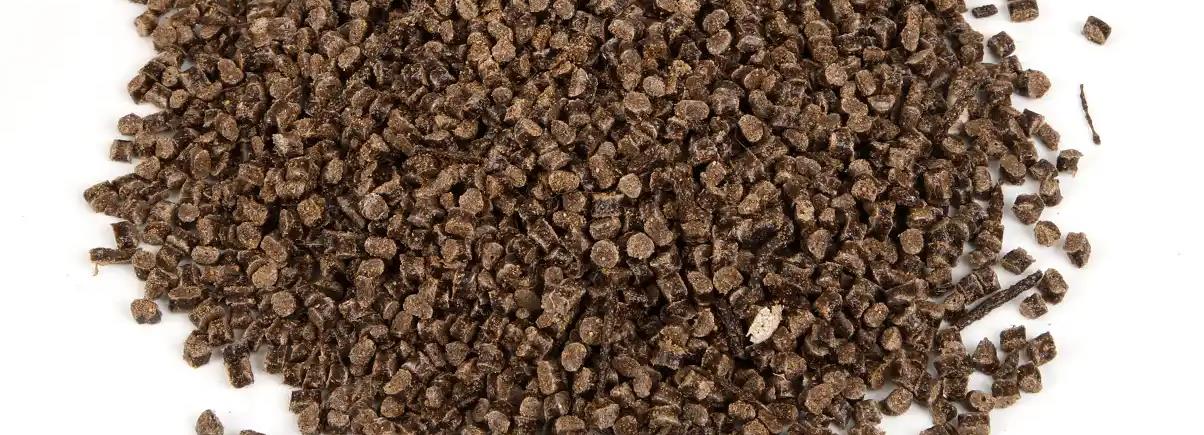
Fórmula
The formula ratio of plant fiber masterbatch varies significantly depending on the source of raw materials, functional requirements, and application scenarios. Based on industry practice and patented technology, a specific analysis will be conducted from six core types:
Formula ratio classified by raw material source
1. Wood fiber masterbatch
Typical formula (weight percentage):
Wood fiber (sawdust/wood powder) 50-70%, polypropylene (PP) 20-30%, maleic anhydride grafted polypropylene (compatibilizer) 3-8%, silane coupling agent 0.5-2%, lubricant (calcium stearate) 0.5-1%.
Function optimization:
If water resistance needs to be improved, 3-7% high-density polyethylene (HDPE) can be added to form a coating layer through cross-linking.
2. Bamboo fiber masterbatch
Typical formula (weight parts):
30-50 parts bamboo fiber, 60-70 parts PP, 5-10 parts maleic anhydride grafted POE (interface adhesive), 5-10 parts vanillin (antibacterial agent), 5-10 parts EPDM grafted maleic anhydride (toughening agent).
Modification treatment:
After treatment with citric acid modified nano calcium carbonate, the compatibility of bamboo fiber with resin is improved, and the proportion of bamboo fiber can be increased to 42-48%. At the same time, 2-6% of photodegradation agent is added to achieve dual degradation function.
3. Straw fiber masterbatch
Typical formula (weight percentage):
Straw powder (corn straw/rice husk) 50-80%, thermoplastic resin (PP/PA6) 20-50%, compatibilizer (POE-g-MAH) 0.5-10%, antioxidant (1010/168 complex) 0.2-0.6%.
Special applications:
When used for biodegradable packaging, it can be compounded with PLA, with straw powder accounting for 30-40%, PLA 40-50%, Nano silica 3-6% improves heat resistance.
Formula proportion classified by functional modification
1. Enhanced plant fiber masterbatch
Three layer structural design (weight ratio):
Plant fiber (jute/sisal) 60-80%, middle layer (maleic anhydride grafted PP+polyethylene) 12-18%, outer layer PP 10-15%, silane coupling agent 0.5-2%.
Mechanical properties:
The tensile strength can reach 27.5-34.6 MPa, and the notch impact strength is 7.4-10.5 kJ/m ², suitable for automotive interior parts.
2. Flame retardant plant fiber masterbatch
Flame retardant system formula (weight percentage):
Plant fiber 3-12%, flame retardant polypropylene masterbatch (containing 80% bromine based flame retardant) 30-50%, glass fiber 10-30%, halogen-free flame retardant (FP-2200) 30%, compatibilizer 5-10%.
Flame retardant grade:
Tested to UL94 V0 level, with an oxygen index (LOI) of ≥ 28, suitable for electronic and electrical enclosures.
3. Antibacterial plant fiber masterbatch
Antibacterial agent ratio (weight percentage):
30-50% plant fiber, 50-70% resin (PP/PS), 5-10% vanillin (antibacterial agent), 5-10% maleic anhydride grafted POE (compatibilizer).
Antibacterial rate:
The antibacterial rate against Escherichia coli and Staphylococcus aureus is ≥ 99%, suitable for food contact materials.
4. Biodegradable plant fiber masterbatch
Whole biobased formula (weight parts):
100-200 parts of plant fiber (bamboo fiber/straw), 100 parts of polycaprolactone (PCL), 1-20 parts of compatibility additive (epoxy soybean oil modified glucosamine), and 50-100 parts of titanium dioxide (filler).
Degradation performance:
The degradation rate of soil burial after 180 days is ≥ 60%, which meets the EN 13432 standard.
Formula ratio classified by fiber morphology
1. Long fiber masterbatch
Reinforced composite material formula (weight percentage):
Long fiber (basalt fiber/hemp fiber) 10-50%, nylon (PA6/PA66) 30-50%, ABS 10-40%, coupling agent (KH550) 0.3-2%, compatibilizer (glycidyl methacrylate grafted ABS) 1-5%.
Application scenarios:
Used for car seat frames, the bending modulus can reach 4.5-6.2 GPa, reducing weight by 15-20%.
2. Short fiber masterbatch
Injection grade formula (weight percentage):
Short cut plant fibers (wood powder/rice husk powder) 30-50%, PP 40-60%, Maleic anhydride grafted PP 3-8%, lubricant (stearic acid) 0.5-1%.
Processing characteristics:
The melt flow rate (MFR) is 8-15g/10min, suitable for producing daily necessities such as toys and tableware.
Formula ratio classified by application field
1. Plant fiber masterbatch for packaging
Environmentally friendly plastic bag formula (weight percentage):
30-50% plant fiber (straw/bamboo fiber), PBAT 40-60%,PLA 5-10%, Chain extender (ADR-4368) 0.5-1%.
Performance indicators:
The tensile strength is 18-22MPa, and the elongation at break is 300-500%, which meets the GB/T 38082-2019 standard.
2. Plant fiber masterbatch for automobiles
Interior component formula (weight percentage):
40-60% plant fiber (flax/sisal), PP 30-50%, Toughening agent (POE) 5-10%, antioxidant (1010/168) 0.3-0.5%.
Lightweight effect:
The density is 1.05-1.15g/cm ³, which is 10-15% lighter than traditional plastics and meets the environmental protection requirements of automotive companies.
Formula ratio classified by matrix resin
1. Thermoplastic resin based masterbatch
PP based masterbatch (weight percentage):
50-70% plant fiber, PP 30-50%, Compatibility agent (maleic anhydride grafted PP) 3-8%, lubricant 0.5-1%.
PE based masterbatch (weight percentage):
40-60% plant fiber, LDPE 30-50%, Silane coupling agent 0.5-2%, antioxidant 0.2-0.5%.
2. Thermosetting resin based masterbatch
Epoxy resin based masterbatch (weight percentage):
Plant fiber (hemp fiber/coconut shell fiber) 20-40%, epoxy resin 50-70%, curing agent (amine) 5-10%, coupling agent (KH560) 1-3%.
Application restrictions:
Limited high temperature resistance (≤ 150 ℃), mainly used as interlayer material for wind turbine blades.
Range of addition ratio of key additives
1. Compatibility agent:
Maleic anhydride grafted polymer (PP-g-MAH/POE-g-MAH): 3-10%, improves the interfacial bonding between fibers and resins.
2. Coupling agent:
Silanes (KH550/KH560): 0.3-2%, enhance fiber surface activity.
3. Lubricants:
Stearic acid/calcium stearate: 0.5-1.5%, reduces processing viscosity.
4. Antioxidants:
1010/168 compound: 0.2-0.5%, extends the service life of the material.
Summary and Design Suggestions
1. Environmental protection and performance balance:
If high degradability is pursued, the proportion of plant fibers can be increased to 70%, but the decrease in mechanical properties needs to be compensated for by compatibilizers (such as POE-g-MAH 5-10%).
2. Processing technology adaptation:
It is recommended to use side feeding extrusion for long fiber masterbatch to reduce fiber breakage; Short fiber masterbatch can improve dispersibility through compounding process (170-175 ℃).
3. Industry standard reference:
Packaging materials must comply with GB/T 38082-2019, and automotive materials must meet ISO 11469 biobased content certification.
By adjusting the formula ratio reasonably, plant fiber masterbatch can find the optimal solution between environmental friendliness, mechanical properties, and processing costs, promoting the sustainable development of the plastic industry.
Proceso de producción
According to the characteristics and common processing techniques of plant fiber masterbatch, its production process usually includes the following core steps, with a focus on solving the compatibility, dispersibility, and masterbatch performance stability between plant fibers and polymer matrices:
Raw material pretreatment
1. Plant fiber treatment
Screening and cleaning: Remove impurities (such as sediment and metal particles) from fibers, commonly using screening, air selection, or water washing to ensure fiber cleanliness.
Drying and dehydration: The fiber moisture content is reduced to below 1% by hot air drying (temperature 50-80 ℃, time 2-4 hours) or vacuum drying to avoid hydrolysis or bubbles of the matrix resin caused by moisture during processing.
Surface modification (key steps):
Using coupling agents (such as silane, titanate), surfactants, or compatibilizers (such as maleic anhydride grafted polyolefins) to treat the surface of fibers, improve the interfacial adhesion between fibers and resins, and reduce agglomeration.
Modification methods: solution immersion method, melt blending method, or mechanochemical method (such as adding modifier to high-speed mixer and high-speed stirring).
2. Preparation of matrix resin
Select resins that match the target application (such as PP, PE, PLA, etc.) and dry them to a moisture content of less than 0.1% (especially moisture absorbing resins such as PA, PLA) to avoid degradation during processing.
3. Pre treatment of additives
Grind dispersants (such as stearic acid, paraffin wax), stabilizers (antioxidants, light stabilizers), functional additives (such as flame retardants, antibacterial agents), etc. according to the formula into powder or pre mix them into masterbatch.
Ingredients and Mixing
Formula weighing: Accurately weigh each component according to the design ratio (such as 30-70% plant fiber, 20-60% matrix resin, 5-15% additives) to ensure batch stability.
Pre mixed:
Use a high-speed mixer (such as a horizontal mixer or twin-screw mixer) for dry mixing, with a speed of 500-1500rpm and a time of 5-10 minutes, to initially disperse the fibers, resin, and additives evenly and avoid local agglomeration.
For polar fibers (such as wood fibers) and non-polar resins (such as PP), compatibilizers (such as PP-g-MAH) can be added to enhance the interfacial bonding.
Melt extrusion blending
Equipment selection: Adopting a twin-screw extruder (meshing type rotating in the same or opposite direction) with a screw length to diameter ratio (L/D) of 25-40 to ensure shear dispersion and mixing effect.
Process parameter control:
1. Temperature setting:
Feeding section: slightly lower than the melting point of the resin (such as 180-190 ℃ for PP) to avoid premature softening of the fibers.
Melting section/mixing section: 10-20 ℃ above the melting point of the resin (such as 200-230 ℃ for PP), ensuring that the resin is fully melted and the fibers are evenly dispersed.
Exhaust section: Maintain negative pressure, eliminate moisture, volatile substances, and residual air, and avoid product bubbles.
Head temperature: slightly lower than the melting section to ensure melt flowability and reduce degradation (such as 200-220 ℃).
2. Screw speed: 50-200rpm. High speed increases shear dispersion, but excessive speed can cause fiber breakage or thermal degradation.
3. Feeding speed: matched with the screw speed, controlled by a weight loss feeder to avoid screw overload or material retention.
Process characteristics:
Fiber addition method: It can be blended with resin through the main feeding port, or added separately through the side feeding port (suitable for high fiber content to avoid blockage).
Vacuum exhaust: effectively removes gas and low molecular weight volatiles adsorbed by fibers, improving the compactness of masterbatch.
Granulation and cooling
Melt extrusion and granulation:
The extruded material is formed into a strip shape through the die hole of the machine head (with a diameter of 1-3mm), and after being water-cooled or air-cooled (to avoid fiber water absorption), it is cut into particles (with a diameter of 2-4mm) by a hot cutting or cold cutting granulator.
Water cooling method: High efficiency, suitable for large-scale production, but requires subsequent drying (especially for hydrophilic fiber masterbatch).
Air cooling/air cooling method: avoids residual moisture and is suitable for systems sensitive to moisture content (such as PLA based masterbatch).
Particle screening: Remove powder and irregular particles through vibration screening to ensure uniform particle size.
Post processing and packaging
Drying treatment: If water-cooled granulation is used, it needs to be dried in a fluidized bed or oven (temperature 50-70 ℃, time 1-2 hours) to ensure that the moisture content of the masterbatch is ≤ 0.3%.
Performance testing: Testing the appearance of particles (color, roundness), melt flow rate (MFR), moisture content, dispersibility (observing fiber aggregation under a microscope), and mechanical properties (tensile and impact strength).
Packaging and storage: Sealed in moisture-proof bags or aluminum foil bags, stored in a dry and ventilated place, away from direct sunlight and humid environments, to prevent fibers from absorbing moisture and deteriorating.
Key technical difficulties and solutions
1. Poor fiber dispersibility:
Optimize the modification process (increase the lipophilicity of the fiber surface), increase the amount of compatibilizer, and adjust the extruder shear rate (such as increasing the number of kneading blocks).
2. Insufficient interface compatibility:
Choose fibers that match the polarity of the resin (such as wood fiber with PP/PE, bamboo fiber with PLA), or enhance interfacial bonding through surface grafting and coupling agent treatment.
3. Poor flowability of masterbatch:
Reduce the fiber filling amount, add lubricants (such as polyethylene wax), or choose a matrix resin with better fluidity (such as low melt viscosity PP).
4. Thermal stability issues:
Add antioxidants (such as hindered phenols) and control the extrusion temperature to not exceed the fiber thermal decomposition temperature (usually ≤ 250 ℃, avoiding long-term high-temperature retention).
The production process of plant fiber masterbatch needs to revolve around “fiber modification uniform dispersion interface compatibility stable processing”. By accurately controlling raw material pretreatment, extrusion parameters, and auxiliary formula, high-performance and highly dispersed masterbatch preparation can be achieved to meet subsequent processing needs such as injection molding and blow molding. In actual production, process parameters need to be flexibly adjusted according to fiber types (such as wood fiber, bamboo fiber, straw fiber), matrix resin, and target applications (packaging, 3D printing, injection molded products, etc.).
Production equipment
The production equipment for plant fiber masterbatch needs to be configured according to the process stages (pretreatment, mixing, extrusion, granulation, post-treatment), and the core equipment needs to meet the requirements of fiber dispersion, interface compatibility, and efficient production. The following are the main equipment and selection points for each stage:
Raw material pretreatment equipment
1. Plant fiber processing equipment
Screening and cleaning equipment
Vibration screening machine: removes impurities such as sediment and metal particles from fibers, and the mesh size of the screen is selected according to the fiber particle size (usually 40-100 mesh).
Wind sorter: uses airflow to separate light impurities (such as debris and dust), suitable for low-density fibers (such as straw fibers).
Drum cleaning machine/spiral cleaning machine: Water washing removes surface pollutants from fibers, equipped with a water circulation filtration system to reduce sewage discharge.
drying equipment
Hot air circulation oven: atmospheric pressure drying, temperature 50-80 ℃, suitable for large-scale production, requires a dehumidification fan.
Vacuum drying machine: Low temperature drying (30-60 ℃) to avoid damage to fiber structure caused by high temperature, suitable for heat sensitive fibers (such as wood fibers).
Fluidized bed dryer: The airflow drives the flow of fibers, resulting in high drying efficiency and suitable for granular or short fibers.
Surface modification equipment
High speed mixer (horizontal/vertical): speed 500-2000rpm, built-in temperature control system, can add coupling agent for surface coating during mixing (such as silane modified wood fiber).
Kneading machine: Strong shear mixing, suitable for high viscosity modifiers (such as molten compatibilizers mixed with fibers), commonly used for mechanochemical modification.
2. Resin and additive treatment equipment
Resin drying machine: For moisture absorbing resins such as PA and PLA, a dehumidification drying machine (dew point below -40 ℃) is used, with a drying temperature of 80-120 ℃ and a time of 2-4 hours.
Additive grinder: Grind solid additives (such as antioxidants and flame retardants) to the micrometer level (usually ≤ 50 μ m), commonly using ball mills and airflow crushers.
Ingredients and mixing equipment
1. Measuring equipment
Weight loss feeder: high-precision measurement (error ≤ 0.5%), suitable for quantitative conveying of resin, fiber, and additives in continuous production, and can be linked with an extruder to control the feeding speed.
Electronic scale/platform scale: Used for batch batching, it must have explosion-proof function (if organic solvent modification is involved).
2. Pre mixing equipment
Horizontal double screw belt mixer: low-speed mixing (50-100rpm), suitable for initial mixing of large batches of raw materials, with a capacity ranging from 50L to 2000L.
Twin screw mixer: equipped with screw conveying and shearing functions, suitable for initial dispersion of fibers and resins, avoiding local agglomeration.
Melt extrusion blending equipment
1. Core equipment: Twin screw extruder
Structural features:
Screw type: Same direction meshing twin-screw (mainstream, suitable for high dispersion requirements), length to diameter ratio (L/D) 25-40, commonly 32-36, to ensure sufficient dispersion of fibers in the melting section.
Modular design: replaceable kneading block and conveying block combination, adjustable shear strength (high shear block is used for fiber dispersion, low shear block is used to reduce fiber breakage).
Heating method: electric heating or oil heating, segmented temperature control (feeding section 180-190 ℃, melting section 200-230 ℃, exhaust section 190-220 ℃).
Key components:
Exhaust system: equipped with a vacuum device (vacuum degree -0.06~-0.09MPa) to remove moisture and volatile substances adsorbed by fibers.
Side feeder: Used when the fiber content is high (>50%) to avoid blockage of the main feeding port, single screw or twin-screw side feeding is used.
2. Auxiliary equipment
Melt filter: installed in front of the machine head, filters impurities and undispersed fiber aggregates, with a filter mesh accuracy of 100-200 mesh.
Pressure sensor: Real time monitoring of extrusion pressure to avoid screw overload (safety pressure threshold set according to resin viscosity).
Granulation and cooling equipment
1. Cooling system
Water cooling system:
Water bath: temperature 20-40 ℃, bath length 3-5m, ensuring rapid cooling and solidification of the melt strip, suitable for PP/PE based masterbatch.
Drying device: Air knife or fan removes surface moisture from particles to prevent excessive drying load in the future.
Air cooling system:
Air cooled tunnel: using cold air circulation to cool the melt strip, avoiding moisture contact (suitable for moisture absorbing resin based masterbatch such as PLA), with high energy consumption but low particle moisture content.
2. Granulation equipment
Strip cutting machine (commonly used):
Hot cutting type: Cut directly when the molten strip is not completely cooled, with uniform particle size (2-4mm), and match the water cooling speed.
Cold cutting method: Cut after the molten strip is completely cooled, suitable for hard and brittle masterbatch, to avoid sticking to the knife.
Underwater Particle Cutting Machine: High end configuration, the melt is directly cut underwater, with high particle roundness, suitable for high output and precision requirements (such as 3D printing masterbatch), but the equipment cost is high.
3. Screening equipment
Vibration screening machine: aperture 2-5mm, removes powder and irregular particles, ensuring uniform particle size of the finished product (pass rate ≥ 98%).
Post processing and auxiliary equipment
1. Drying equipment (after water-cooled granulation)
Fluidized bed dryer: Hot air fluidized particles, quickly removing surface moisture (temperature 50-70 ℃, time 30-60 minutes), suitable for large-scale continuous production.
Drum dryer: The rotary drum body is ventilated with hot air, suitable for masterbatch with good particle flowability and low energy consumption.
2. Testing equipment
Melt Flow Rate Meter (MFR): tests the flowability of masterbatch to ensure batch stability (standard ASTM D1238).
Moisture analyzer: Quickly detect moisture content (such as Karl Fischer titration instrument, target ≤ 0.3%).
Microscope/Scanning Electron Microscope (SEM): Observe fiber dispersion and interfacial bonding (for sampling).
3. Packaging and storage equipment
Automatic packaging machine: Weighing packaging (commonly 25kg/bag), equipped with moisture-proof bags or aluminum foil bags, with built-in deoxidizer.
Metal detection machine: online detection of whether metal impurities are mixed in particles to avoid damaging downstream processing equipment (such as injection molding machine screws).
Key principles for equipment selection
1. Fiber characteristic matching:
Long fibers (such as hemp fibers) require high shear dispersing equipment (increasing the number of kneading blocks), while short fibers (such as wood powder) can reduce shear to minimize breakage.
2. Capacity demand:
Small experimental line: Twin screw extruder with a production capacity of 5-50kg/h, equipped with laboratory grade mixer and small granulator.
Industrial production line: with a capacity of 500-2000kg/h, it needs to be equipped with large twin-screw (diameter 75-120mm), automated feeding and cooling systems.
3. Environmental requirements:
The cleaning wastewater needs to be equipped with a filtration and biochemical treatment device, and the extruded exhaust gas should be adsorbed by activated carbon or catalytically burned (VOCs emissions meet standards).
Typical production line configuration example
Raw material pretreatment line: vibrating screen → drum cleaning machine → hot air dryer → high-speed mixer (modified)
Extrusion granulation line: Weight loss feeder → Twin screw extruder (with side feeding) → Water bath cooling tank → Strip cutting machine → Vibration screen → Fluidized bed dryer → Automatic packaging machine
By properly matching equipment, efficient production of plant fiber masterbatch can be achieved while meeting dispersion, compatibility, and environmental requirements. The actual selection needs to be based on the fiber type (wood fiber/bamboo fiber/straw fiber), target masterbatch performance (mechanics/degradability/functionality), and comprehensive investment budget decision-making.
Plant Fiber Masterbatch Extruder
Kerke’s masterbatch extruder can be used to produce Plant Fiber Masterbatch. Our Plant Fiber Masterbatch extruder has multiple models to choose from, which can meet different production requirements.
-
Extrusora de doble husillo para laboratorio
¿Cuándo necesitará una extrusora de doble husillo de laboratorio? Si desea realizar ensayos y pruebas de...
-
Extrusora de doble husillo paralelo
Nuestra extrusora de doble husillo paralelo corrotante está diseñada para la fabricación de compuestos y...
-
Extrusor triple (3 tornillos)
La extrusora de 3 tornillos es una nueva tecnología que tiene muchas ventajas. La extrusora de triple tornillo se utiliza principalmente...
-
Sistema de extrusión de doble etapa
El sistema de extrusión madre-bebé está diseñado para materiales especiales que no pueden procesarse en una extrusora de una etapa,...
-
Línea de amasado Banbury
Nuestra amasadora + extrusora está diseñada para realizar aplicaciones especiales con una capacidad de producción de 30kg/h a 1000kg/h....
-
Sistema de corte / Sistema de granulación
Diferentes materiales necesitan diferentes sistemas de corte, Kerke ofrece todo tipo de sistemas de corte, aquí está la explicación de...
Aplicación
Plant fiber masterbatch has achieved diversified applications in multiple fields due to its environmental protection, biodegradability, and enhanced modification characteristics, especially playing a key role in plastic modification and green manufacturing. The following are its main application areas and scenarios:
Campo de envasado
1. Plastic packaging products
Shopping bag/courier bag:
Add to PE/PP to prepare biodegradable or high-strength packaging bags, reduce the amount of pure resin used (substitution ratio of 10% -30%), improve impact resistance and stiffness, while reducing white pollution.
Food packaging film/tray:
Blending with biodegradable resins such as PLA and PBAT to produce compostable food contact materials (such as takeaway boxes and fruit netting), utilizing the barrier properties of fibers to delay oil/water penetration and extend shelf life.
Industrial packaging cushioning materials:
Instead of foam plastic, it is used for filling film and shockproof pad. The cushioning performance is improved through fiber reinforcement, which has the advantages of lightweight and environmental protection.
2. Paper plastic composite packaging
As an interlayer adhesive or reinforcement layer, it improves the compatibility between paper-based and plastic films, and is used for milk cartons, Tetra Pak bags, etc., reducing the amount of glue and improving overall strength.
In the field of automobiles and transportation
1. Interior components
Instrument panel, door panel, seat frame:
Filled into PP/ABS, replacing traditional fillers such as talcum powder and glass fiber, reducing density (weight loss of 5% -15%), while improving heat resistance (heat deformation temperature increased by 10-20 ℃) and surface texture (reducing shrinkage marks).
Sound and heat insulation materials:
Preparation of car roof sound insulation layer by blending EVA/EPDM, utilizing fiber porous structure to absorb vibration noise, with advantages of lightweight and low cost.
2. Exterior and structural components
High modulus fiber masterbatch (such as linen fiber/PET composite) is used for truck cargo box boards and bumpers, replacing metal or fiberglass reinforced plastics, reducing energy consumption and meeting lightweight design requirements.
Building Materials and Home Furnishings
1. Wood plastic composites (WPC)
Floor, wall panels, outdoor boardwalk:
Blended with HDPE/PP (fiber content of 30% -70%), producing profiles with a wood like feel, better weather resistance than pure wood, no paint and maintenance, widely used in landscaping and interior decoration.
Pipes and profiles:
Add low foaming pipes (such as drainage pipes and decorative lines) to PVC to reduce density and improve rigidity, while reducing the amount of PVC resin used (saving 15% -25% of costs).
2. Decorative materials
Integrated wall panels and ceiling panels:
Blending with PS/ABS to produce lightweight decorative panels, achieving wood and stone grain effects through fiber coloring or surface treatment, environmentally friendly and formaldehyde free, suitable for rapid assembly in high-end rooms.
Agriculture and Horticulture
1. Agricultural films and products
Degradable plastic film:
Blended with PBAT/PLA (fiber content 10% -20%), a photo/biodegradable film is prepared to reduce soil residue, while fiber reinforcement can delay film damage and extend the service life.
Nursery pots and planting bags:
Fiber masterbatch endows the product with breathability and a certain strength. When transplanted, it can be directly buried in the soil and degraded into organic fertilizer, simplifying the seedling cultivation process.
2. Fishing gear and aquaculture facilities
Fishing nets, aquaculture floats, etc. are made of fiber-reinforced PP/PE to enhance their resistance to seawater corrosion and reduce the harm of abandoned fishing gear to marine ecology.
3D Printing and Special Materials
1. 3D printing consumables
PLA based fiber masterbatch:
Produce 3D printed wires with wood/bamboo textures, with printed models that have a natural texture, suitable for cultural and creative products, architectural models, and are biodegradable.
High strength composite wire material:
Carbon fiber/plant fiber hybrid masterbatch reinforced nylon (PA) is used for printing functional components such as drone frames, balancing strength, toughness, and printing fluidity.
2. Functional masterbatch
Antibacterial masterbatch: adding bamboo fiber/chitin fiber for the preparation of food contact grade antibacterial plastics (such as kitchen utensils), utilizing the antibacterial properties of natural fibers to reduce the use of chemical additives.
Conductive masterbatch: Carbon/metal coating on the surface of wood fibers, blended with ABS to produce anti-static packaging materials for electronic component turnover boxes.
Textiles and nonwoven fabrics
1. Composite fiber fabric
Blended with PET/PA chips to produce functional yarns containing plant fibers (such as linen fiber-reinforced polyester), improving the breathability, moisture absorption, and wear resistance of the fabric, used for outdoor clothing and workwear.
2. Non woven fabric
Shopping bags, medical dressings:
Adding fiber masterbatch to PP spunbond nonwoven fabric enhances tensile strength (by 10% -20%) and reduces weight; Or composite with PLA meltblown fabric to prepare degradable inner layer materials for masks.
Other emerging applications
Bio based foam: it is blended with PU resin to prepare low-density foam, which is used for furniture filling, packaging and buffering, replacing traditional petroleum based foam and reducing carbon emissions.
Electronic appliances: Flame retardant fiber masterbatch (such as bamboo fiber/PP composite) is used to prepare household appliance casings (such as refrigerator liners and washing machine components), meeting UL94 V-0 flame retardant rating while reducing weight.
Future Trends
1. Fully biodegradable system: Focusing on PLA/plant fibers/natural additives, the fully bio based masterbatch meets strict degradation standards such as EU EN 13432 and US ASTM D6400.
2. High performance: Develop nano-sized plant fiber masterbatch (such as cellulose nanocrystals) to achieve high strength and high barrier properties while maintaining environmental protection (such as replacing petroleum based barrier resins for food packaging).
3. Circular economy: Design a recyclable/reusable fiber masterbatch system to promote the closed-loop industrial chain of “plastics fiber masterbatch products”.
The application of plant fiber masterbatch is expanding from traditional filling modification to multifunctionality and high-end, especially under the “dual carbon” goal. Its low-carbon and environmentally friendly characteristics will further drive the green transformation of industries such as packaging, automotive, and building materials.