PESU masterbatch, also known as polyethersulfone masterbatch, is a granular concentrate made from polyethersulfone (PESU) resin as the substrate, with the addition of specific functional additives and fillers. PESU, as a high-performance thermoplastic, has excellent heat resistance, chemical corrosion resistance, mechanical properties, and good biocompatibility. Therefore, PESU masterbatch has a wide range of applications in multiple fields.
Characteristic
1. Excellent heat resistance: PESU masterbatch has a high glass transition temperature (about 225 ℃) and thermal deformation temperature (up to 203 ℃ under a load of 1.82MPa), and can be used in high-temperature environments for a long time. It can withstand multiple high-temperature disinfections, such as conventional steam sterilization and ethylene oxide sterilization in the medical field, without significant performance changes.
2. Good mechanical performance: It has high strength and rigidity, with a tensile strength of about 80MPa and a bending strength of about 120MPa. At the same time, it also has good toughness, and its fracture elongation is generally between 50% and 100%. This allows products made of PESU masterbatch to withstand large external forces without easily breaking or deforming, making them suitable for manufacturing various components that require a certain level of mechanical strength.
3. Outstanding chemical stability: PESU masterbatch has good tolerance to most organic solvents, acids, bases, etc., and can maintain stable performance in different chemical environments. For example, in some chemical production equipment, the components made from it can be exposed to corrosive media for a long time without being damaged, and have a longer service life.
4. Excellent electrical insulation performance: PESU masterbatch has high insulation resistance and low dielectric constant, which can maintain good electrical insulation performance even in harsh environments such as high temperature and humidity. It can be used to manufacture insulation components in the field of electronic appliances, such as insulation layers for wires and cables, and casings for electrical equipment, effectively preventing leakage and short circuits.
5. Good processing performance: PESU masterbatch has good fluidity and formability, and can be processed using various methods such as injection molding, extrusion, blow molding, etc. to produce various complex shaped products. During the processing, it can be rapidly formed with high production efficiency, and the dimensional accuracy and surface quality of the product are good.
6. Environmentally friendly and non-toxic: PESU masterbatch itself is non-toxic and meets relevant environmental standards. It will not release harmful substances during use and is harmless to human health and the environment. This characteristic makes it widely used in fields such as food packaging and medical care that require high hygiene and safety requirements.
7. Good Transparency: Products made from PESU masterbatch have a certain degree of transparency, with a light transmittance of about 80%. They can be used to manufacture products that require transparency, such as food packaging containers, optical lenses, etc. They can meet the requirements of packaging and optical performance while maintaining good physical and chemical properties.
Types
PESU masterbatch can have multiple types according to different classification criteria. The following are some common classification methods and corresponding types:
Function
PESU masterbatch for electronic and electrical appliances: It has excellent electrical insulation performance, heat resistance, and mechanical properties, and is suitable for manufacturing electronic and electrical components such as sockets, switches, coil frames, integrated circuit packaging materials, etc.
PESU masterbatch for automotive industry: It is required to have high strength, rigidity, heat resistance, and chemical corrosion resistance to meet the usage requirements of automotive engine peripheral components, automotive electronic equipment casings, etc. in harsh environments.
PESU masterbatch used in the medical field: It needs to have good biocompatibility, non toxicity, resistance to cooking and chemical disinfection, and is commonly used in the manufacture of syringes, infusion sets, medical device casings, medical tubing, etc.
PESU masterbatch for food packaging: It is non-toxic, odorless, heat-resistant, water-resistant, and has good barrier properties. It can be used to produce food containers, packaging films, bottle caps, etc., effectively protecting food quality and safety.
Classified by additives
Enhanced PESU masterbatch: Adding reinforcing materials such as glass fiber and carbon fiber can significantly improve the mechanical strength, rigidity, and dimensional stability of PESU, making it suitable for applications with high mechanical performance requirements, such as component manufacturing in aerospace, high-end electronic equipment, and other fields.
Flame retardant PESU masterbatch: flame retardant is added to give it good flame retardant properties, which can meet the requirements of material fire safety in industries such as electronics and construction, and reduce fire risks.
Toughened PESU masterbatch: By adding toughening agents, the toughness and impact resistance of PESU are improved, reducing the possibility of products breaking due to external impact during use. It is suitable for manufacturing components that are easily affected by impact, such as automotive interior parts, sports equipment, etc.
Conductive PESU masterbatch: Conductive fillers such as carbon nanotubes and metal powders are added to give PESU masterbatch a certain degree of conductivity, which can be used to manufacture products that require electrostatic dissipation, electromagnetic shielding, and other functions, such as shielding covers for electronic devices and anti-static packaging materials.
Classified by molecular weight
High molecular weight PESU masterbatch: It has high strength, heat resistance, and chemical corrosion resistance, but is relatively difficult to process. It is generally used in special fields with extremely high performance requirements, such as aerospace, high-end medical equipment, etc.
Medium molecular weight PESU masterbatch: with good comprehensive performance and excellent processing performance, it is the most common type and widely used in various fields such as electronics, automotive, medical, food packaging, etc.
Low molecular weight PESU masterbatch: It has good flowability and is easy to process, but its mechanical properties are relatively low. It is commonly used in applications that require high processing performance but not particularly strict mechanical properties, such as certain plastic films, coating materials, etc.
Fórmula
The proportion of different types of PESU masterbatch formulations may vary due to factors such as manufacturers and specific application requirements. The following are some examples of common types of PESU masterbatch formulation proportions for reference only:
Enhanced PESU masterbatch
PESU resin: 70% -85%
Fiberglass: 15% -30%
Coupling agent: 0.5% -2% (used to improve the bonding strength between glass fiber and PESU resin)
Flame retardant PESU masterbatch
PESU resin: 75% -90%
Flame retardants: 10% -25%, such as bromine based flame retardants, phosphorus based flame retardants, or their compound systems.
Synergistic agent: 0.5% -3%, such as antimony trioxide, used in combination with flame retardants to improve flame retardancy.
Toughened PESU masterbatch
PESU resin: 80% -90%
Toughening agent: 10% -20%, common toughening agents include thermoplastic elastomers, rubber elastomers, etc.
Compatibility agent: 0.5% -3% (used to improve the compatibility between PESU resin and toughening agent)
Conductive PESU masterbatch
PESU resin: 80% -95%
Conductive filler: 5% -20%, for example, the addition amount of carbon nanotubes is generally 1% -5%, and the addition amount of metal powder may be 5% -20%, depending on the type and performance requirements of the conductive filler.
Dispersant: 0.5% -3% (helps to evenly disperse conductive fillers in PESU resin)
It should be noted that these formula ratios are not fixed and need to be optimized and adjusted according to the specific performance of PESU resin, additive characteristics, and the final performance requirements of the product in actual production. Meanwhile, different manufacturers may use different production processes and auxiliary additives, which can also have an impact on the formula ratio.
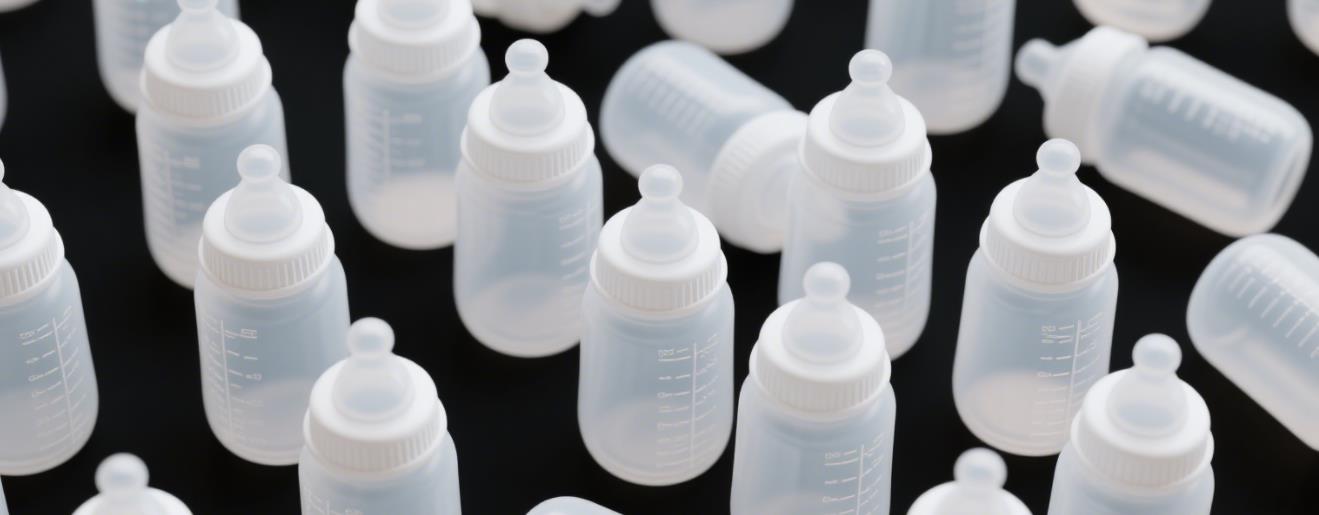
Proceso de producción
The production process of PESU (polyethersulfone) masterbatch involves multiple steps, each of which requires strict control to ensure the quality and performance of the final product. Here is a detailed introduction for you:
1. Preparación de la materia prima
PESU resin: Select appropriate models and specifications of PESU resin based on the performance requirements of the product. Generally speaking, PESU resin needs to be dried before use to remove any moisture. The drying conditions are usually at a temperature of 150-180 ℃ for 3-6 hours to prevent moisture from causing problems such as bubbles and hydrolysis in the product during processing.
Additives: Accurately weigh various additives according to the formula, such as reinforcing materials (glass fiber, carbon fiber), flame retardants, toughening agents, conductive fillers, etc. At the same time, pre-treatment should be carried out based on the characteristics of the additives. For example, surface treatment can be applied to glass fibers to enhance their compatibility with PESU resin; For some powdered additives, pre mixing can be carried out to ensure their uniform dispersion.
2. Mezcla
High speed mixing: Put the dried PESU resin and pre treated additives into the high-speed mixer. The high-speed mixer uses high-speed rotating stirring blades to thoroughly mix materials in a short period of time. The mixing time is generally 5-15 minutes, and the specific duration can be adjusted according to the characteristics of the material and the performance of the mixer. During the mixing process, some additives such as dispersants and lubricants can be added appropriately to improve the mixing effect and material flowability.
Mixing: For some formulas that require high mixing uniformity, a mixing machine can be used for further mixing. The internal mixer exerts strong shear and kneading effects on the material through the rotation and interaction of the rotor, making the additives more evenly dispersed in the PESU resin. The mixing temperature is generally controlled at 280-320 ℃ for 10-20 minutes.
3. Melt extrusion
Equipment selection: Double screw extruders are usually used for melt extrusion. Twin screw extruders have excellent mixing, plasticizing, and conveying capabilities, ensuring that materials are fully melted and uniformly mixed at high temperatures.
Temperature control: The temperature setting of the extruder is crucial and is generally divided into multiple temperature sections, with the temperature gradually increasing from the feeding section to the machine head. The temperature of the feeding section is controlled at 260-280 ℃, the temperature of the compression section is 280-300 ℃, the temperature of the metering section is 300-320 ℃, and the temperature of the machine head is 320-340 ℃. Different PESU resin and additive formulations may require appropriate temperature adjustments.
Screw speed: The screw speed is generally between 100-300 revolutions per minute. Excessive rotational speed may result in short material residence time and uneven mixing; If the speed is too low, it will affect production efficiency. The appropriate screw speed should be selected based on the characteristics of the material and the performance of the extruder.
4. Granulación
Underwater Particle Cutting: The molten material extruded from the extruder head is directly introduced into water, and the material is cut into particles by a high-speed rotating cutter. The particles are rapidly cooled and shaped in water. This method produces particles with regular shapes, smooth surfaces, and uniform particle sizes, making it suitable for large-scale production of high-quality PESU masterbatch.
Air cooled pellet cutting: The extruded material is first cooled by an air cooling device, and then cut into pellets by a cutting blade. This method has relatively simple equipment and low cost, but the cooling effect and shape accuracy of the particles are relatively poor, making it suitable for situations where particle quality requirements are not particularly high.
5. Post processing
Drying: The granulated PESU masterbatch may contain some moisture and needs to be dried again to ensure product quality and storage stability. The drying conditions are similar to the drying of raw materials, with a temperature of 150-180 ℃ and a time of 3-6 hours.
Screening: Remove particles that do not meet the particle size requirements through screening equipment to ensure the uniformity of the product’s particle size.
Packaging: Qualified PESU masterbatch is packaged in sealed bags or plastic drums to prevent moisture and contamination during storage and transportation.
Production equipment
The PESU masterbatch production equipment is a key factor in ensuring product quality and production efficiency. The following are the main production equipment, their characteristics, and functions:
dryer
Types: Common ones include hot air circulation dryer, vacuum dryer, etc.
Function: Used to remove moisture from PESU resin raw materials, prevent defects such as bubbles and hydrolysis during processing, and ensure product quality. Hot air circulation dryer dries materials by circulating hot air, suitable for large-scale production; The vacuum dryer dries in a vacuum environment, which can better protect the material properties and is suitable for occasions with high drying requirements.
mixer
Type: High speed mixer, screw belt mixer, etc.
Function: Mix PESU resin with various additives to achieve a preliminary uniform dispersion of the material. High speed mixers generate strong stirring effects through high-speed rotating blades, suitable for rapid mixing of various materials; The spiral belt mixer is suitable for large capacity, low-speed mixing processes, ensuring the uniformity of material mixing.
internal mixer
Type: Rotary mixer.
Function: Further knead and mix the preliminarily mixed materials to ensure that the additives are fully and uniformly mixed with PESU resin, thereby improving the uniformity and compatibility of the materials. The rotor of the internal mixer rotates in a closed mixing chamber, applying high temperature, high pressure, and strong shear force to the material, thereby achieving good mixing effect.
extrusora de doble husillo
Type: co rotating twin-screw extruder, counter rotating twin-screw extruder.
Function: It is one of the core equipment for PESU masterbatch production. It has good conveying, mixing, plasticizing, and extrusion capabilities, and can melt and plasticize the mixed materials at high temperatures, and evenly extrude the materials through the rotation of the screw. The co rotating twin-screw extruder has strong self-cleaning ability and mixing effect, and is suitable for the production of most PESU masterbatch; The counter rotating twin-screw extruder has a higher extrusion pressure and is suitable for some formulations that require higher extrusion pressure.
underwater cutter
Type: including templates, cutters, circulating water systems, and other parts.
Function: Directly introduce the molten material extruded from the extruder head into water, and cut the material into particles through a high-speed rotating cutter. The particles are rapidly cooled and shaped in water, producing particles with regular shapes, smooth surfaces, and uniform particle sizes. It is currently a relatively advanced granulation method suitable for large-scale production of high-quality PESU masterbatch.
air cooled granulator
Type: There are different forms such as hot cut air cooling and cold cut air cooling.
Function: The extruded material is first cooled by an air cooling device, and then cut into particles by a cutting knife. This method has relatively simple equipment and low cost, but the cooling effect and shape accuracy of the particles are relatively poor, making it suitable for situations where particle quality requirements are not particularly high.
dryer (post treatment equipment)
Type: Similar to drying machines in the raw material processing stage, such as hot air circulation drying machines, vacuum drying machines, etc.
Function: To re dry the PESU masterbatch after granulation, remove the water absorbed during the granulation process, and ensure the quality and storage stability of the product.
screening machine
Type: vibrating screen machine, rotary screen machine, etc.
Function: Screen PESU masterbatch through different mesh sizes to remove particles that do not meet the particle size requirements, ensuring the uniformity of the product’s particle size. The vibrating screen machine uses a vibrating motor to generate high-frequency vibration on the screen, allowing materials to be quickly screened on the screen; The rotary screening machine screens materials through a rotating screening cylinder and is suitable for screening particles with different particle size ranges.
packer
Type: Automatic packaging machine, semi-automatic packaging machine, etc.
Function: Packaging qualified PESU masterbatch in sealed bags or plastic drums to prevent moisture and contamination during storage and transportation. Automatic packaging machines can achieve automatic measurement, filling, and sealing of materials, improving packaging efficiency and quality; The semi-automatic packaging machine requires manual assistance to complete some operations and is suitable for production occasions with small output.
PESU masterbatch extruder
Kerke’s masterbatch extruder can be used to produce PESU masterbatch. Our PESU masterbatch extruder has multiple models to choose from, which can meet different production requirements.
-
Extrusora de doble husillo para laboratorio
¿Cuándo necesitará una extrusora de doble husillo de laboratorio? Si desea realizar ensayos y pruebas de...
-
Extrusora de doble husillo paralelo
Nuestra extrusora de doble husillo paralelo corrotante está diseñada para la fabricación de compuestos y...
-
Extrusor triple (3 tornillos)
La extrusora de 3 tornillos es una nueva tecnología que tiene muchas ventajas. La extrusora de triple tornillo se utiliza principalmente...
-
Sistema de extrusión de doble etapa
El sistema de extrusión madre-bebé está diseñado para materiales especiales que no pueden procesarse en una extrusora de una etapa,...
-
Línea de amasado Banbury
Nuestra amasadora + extrusora está diseñada para realizar aplicaciones especiales con una capacidad de producción de 30kg/h a 1000kg/h....
-
Sistema de corte / Sistema de granulación
Diferentes materiales necesitan diferentes sistemas de corte, Kerke ofrece todo tipo de sistemas de corte, aquí está la explicación de...
Related requirements
In the production of PESU masterbatch, the performance and parameters of the extruder are crucial for product quality and production efficiency. The following are specific requirements:
Performance Requirement
Good plasticizing ability: PESU resin has a high melting point and requires an extruder to provide sufficient heat and shear force to fully plasticize it. The extruder should be able to uniformly mix and plasticize PESU resin and additives into a melt with good flowability within the set temperature range, ensuring that the material has a uniform texture and no unmelted particles or clumps during the extrusion process.
Accurate temperature control: Due to the sensitivity of PESU masterbatch production to temperature, the extruder needs to have a precise temperature control system. Being able to control the temperature of each section of the material barrel within ± 2 ℃ of the set value at different processing stages to ensure stable plasticization and extrusion of materials, and avoid unstable product performance or quality defects caused by temperature fluctuations.
Stable pressure output: In order to ensure the size accuracy and appearance quality of the extruded PESU masterbatch, the extruder needs to provide stable pressure output. During the entire extrusion process, pressure fluctuations should be controlled within a small range, usually requiring a pressure fluctuation of no more than ± 5%, to ensure that the material can be evenly and continuously extruded from the head, avoiding uneven thickness or uneven surface of the extruded material.
Efficient mixing and dispersion performance: The extruder should be able to thoroughly mix PESU resin with various additives to achieve good dispersion effect. By designing the screw structure and configuring the mixing elements reasonably, the material undergoes multiple shearing, stretching, and mixing effects during the extrusion process, ensuring that the additives are evenly distributed in the PESU matrix, thereby improving the consistency of the performance of the masterbatch.
Parameter requirements
Screw diameter: Choose the appropriate screw diameter based on production scale and product requirements. Generally speaking, when the production scale is large, extruders with screw diameters of 65-120mm can be selected; For small-scale production or laboratory research, a small extruder with a screw diameter of 30-50mm can be chosen. A larger screw diameter can provide greater extrusion capacity, but it also requires higher power and larger equipment space.
Length to diameter ratio (L/D): PESU masterbatch production typically requires a high length to diameter ratio, typically between 25-40. A longer aspect ratio is beneficial for the full plasticization, mixing, and exhaust of materials inside the screw, improving product quality. However, a large aspect ratio can also increase equipment costs and energy consumption, so it is necessary to optimize the selection based on specific material characteristics and production processes.
Screw speed: The screw speed should be adjusted according to the characteristics of the material, the specifications of the extruder, and production requirements. In general, the screw speed for PESU masterbatch production is between 100-300r/min. Lower rotational speeds are suitable for high viscosity materials or additives that are sensitive to shear, in order to avoid excessive shear and reduce material performance; Higher rotational speeds can be used to improve production efficiency, but attention should be paid to controlling the residence time and temperature rise of materials.
Motor power: The motor power of the extruder needs to be determined based on factors such as screw diameter, aspect ratio, speed, and material processing difficulty. Generally speaking, for extruders with a screw diameter of 65mm, the motor power is usually around 30-55kW; The extruder with a screw diameter of 120mm may have a motor power between 75-160kW. Adequate motor power is the key to ensuring the normal operation of the extruder and meeting production capacity.
Heating and cooling system: The heating system should have the ability to quickly raise the temperature of the material cylinder to the set value in a short period of time. The cooling system should be able to control the temperature in a timely and effective manner to prevent material overheating. The heating power is generally configured according to the specifications of the extruder and the heating requirements of the material. The heating power per 100mm screw diameter is usually around 10-15 kW. Cooling methods often use air or water cooling, and the cooling capacity should be able to meet the cooling requirements of materials under maximum production load.
The following are general settings for extruder parameters in PESU masterbatch production. In actual production, adjustments need to be made based on specific raw material characteristics, product requirements, and equipment performance:
Temperature parameters
The temperature of the front section of the material cylinder is usually set at 320-340 ℃. PESU resin exhibits good fluidity in this temperature range, while ensuring better integration of additives and resin, and preventing material decomposition due to high temperature.
The temperature in the middle section of the material barrel is generally controlled between 330-350 ℃. This area is the main plasticizing section of the material, and higher temperatures help to fully plasticize the PESU resin, making the molecular chain segments inside the material more active and further improving the uniformity of the material.
The temperature of the rear section of the material cylinder is set at 300-320 ℃. The relatively low temperature in the later stage is mainly to prevent premature melting of materials near the feed inlet, ensure stable entry of materials into the screw, and also help reduce the impact of high temperature on the mechanical components at the back end of the barrel.
Head temperature: generally between 320-330 ℃. The stability of the head temperature is crucial for the appearance quality and dimensional accuracy of the extruded material. This temperature range enables the molten material to have appropriate fluidity during extrusion at the head, making it easier to form.
Screw speed parameters
For the initial debugging phase, the screw speed can be set at 100-150r/min. At this point, the material can be slowly added to the extruder to observe the plasticization of the material, extrusion pressure, and preliminary quality of the product, in order to promptly detect problems and make adjustments, such as checking whether the material can be uniformly plasticized, whether there are local overheating or poor plasticization phenomena.
During normal production, the screw speed can be gradually increased to 150-300r/min according to the requirements of production efficiency and product quality. When producing ordinary specification PESU masterbatch with certain requirements for production efficiency, a higher rotational speed can be chosen; For some PESU masterbatch with added special additives or high requirements for product performance, it may be necessary to choose a lower rotational speed to ensure sufficient residence time of the material in the screw, achieving sufficient mixing and plasticization.
Pressure parameters
Back pressure: The back pressure is generally controlled between 1-5 MPa. Appropriate back pressure helps improve the plasticization quality and uniformity of materials, allowing them to experience greater compression and shear within the screw. When producing high-performance PESU masterbatch, higher back pressure may be required to ensure sufficient mixing of additives and PESU resin; For formulas that are more sensitive to shear, lower back pressure is more appropriate to avoid the impact of excessive shear on material properties.
Extrusion pressure: The extrusion pressure is usually between 10-30 MPa. The extrusion pressure is influenced by various factors, such as the viscosity of the material, screw speed, and the structure of the die head. During the production process, adjustments need to be made according to specific circumstances to ensure the quality and stability of the extruded material. If the extrusion pressure is too high, it may lead to material leakage from the machine head or increased wear of equipment components; If the extrusion pressure is too low, it may result in insufficient density or defects such as bubbles in the extruded material.
Feeding speed parameters
The feeding speed should match the screw speed and the production capacity of the extruder. In actual production, the principle is usually to ensure that materials can enter the extruder continuously and stably without overloading or material breakage. Generally speaking, for small extruders, the feeding speed may be between 1-5kg/h; For large extruders, the feeding speed can be adjusted to 10-50kg/h or even higher according to the production scale. In the production process, it is necessary to accurately control the feeding speed by adjusting the speed or feeding frequency of the feeder based on the characteristics of the material, screw speed, and the actual operation of the extruder.
Aplicación
PESU (Polyether Sulfone) masterbatch has excellent heat resistance, chemical resistance, mechanical properties, and electrical properties, and therefore has a wide range of applications in multiple fields. The following are some of the main application aspects:
Electronic and electrical field
Integrated circuit packaging: PESU masterbatch has good heat resistance and electrical insulation, which can withstand the high temperature environment during the integrated circuit packaging process, while ensuring electrical isolation between the chip and the external environment, improving the reliability and stability of the packaging.
Electronic component casing: A casing used to manufacture electronic components such as resistors, capacitors, inductors, etc. The shell made of PESU masterbatch has excellent mechanical strength and flame retardant properties, which can protect internal components from external physical damage and electrical interference. At the same time, it has good flame retardant effect in the event of a fire, reducing the risk of fire.
Insulation layer of wires and cables: As the insulation material of wires and cables, PESU masterbatch has good insulation performance and chemical corrosion resistance, which can ensure the safe operation of wires and cables under different environmental conditions and prevent accidents such as leakage and short circuits.
Automotive industry field
Automotive engine components: Due to the high heat resistance and mechanical strength of PESU masterbatch, it can be used to manufacture some components of automotive engines, such as engine hood, intake manifold, turbocharger housing, etc. These components need to withstand high temperature and high pressure environments during the operation of the car. Components made of PESU masterbatch can meet their performance requirements and improve the reliability and efficiency of the engine.
Automotive electrical system: In the electrical system of automobiles, PESU masterbatch can be used to manufacture components such as connectors, sockets, switches, etc. Its excellent electrical performance and chemical resistance can ensure the stable operation of these components in the complex electrical environment of automobiles, preventing the occurrence of electrical faults and corrosion phenomena.
Sector médico
Medical devices: PESU masterbatch has good biocompatibility and chemical stability, and can be used to manufacture various medical devices such as syringes, infusion sets, blood dialyzers, surgical instruments, etc. These devices require direct contact with human tissues and body fluids, and devices made from PESU masterbatch can meet biosafety requirements without causing harmful effects on the human body.
Medical equipment casing: used to manufacture the casing of medical equipment, such as X-ray machines, CT machines, ultrasound diagnostic instruments, etc. The shell made of PESU masterbatch has good mechanical properties and appearance quality, which can protect the precision components inside the equipment, and is easy to clean and disinfect, meeting the hygiene requirements of medical environments.
Aerospace field
Aircraft interior parts: PESU masterbatch can be used to manufacture aircraft interior parts, such as seat armrests, luggage racks, cabin wall panels, etc. It has the characteristics of light weight, high strength, flame retardancy, etc., which can reduce the weight of the aircraft, improve fuel efficiency, and ensure the safety and comfort of interior parts during aircraft flight.
Aircraft engine components: In aircraft engines, PESU masterbatch can be used to manufacture some high-temperature and corrosion-resistant components, such as engine blades, combustion chamber liners, etc. These components need to work in extreme high temperature and high pressure environments, and the high performance of PESU masterbatch can meet the demanding requirements of aviation engines, improving engine performance and reliability.
Other areas
Fiber spinning: PESU masterbatch can be used to produce high-performance fibers, such as for manufacturing protective clothing, filter materials, aerospace fabrics, etc. PESU fibers have excellent heat resistance, chemical resistance, and mechanical properties, and can maintain stable performance under harsh environmental conditions.
Thin film application: The PESU thin film produced has excellent electrical insulation performance, heat resistance, and chemical resistance, and can be used as an insulation film in the field of electronics and electrical appliances, as well as a packaging film for solar cells.