EPDM masterbatch, also known as maleic anhydride grafted EPDM, is a type of ultra tough and cold resistant nylon modified special toughening and cold resistant masterbatch, also known as rubber particle grafted MAH. EPDM masterbatch has a certain demand in the market, especially in the fields of nylon modification and toughening agents.
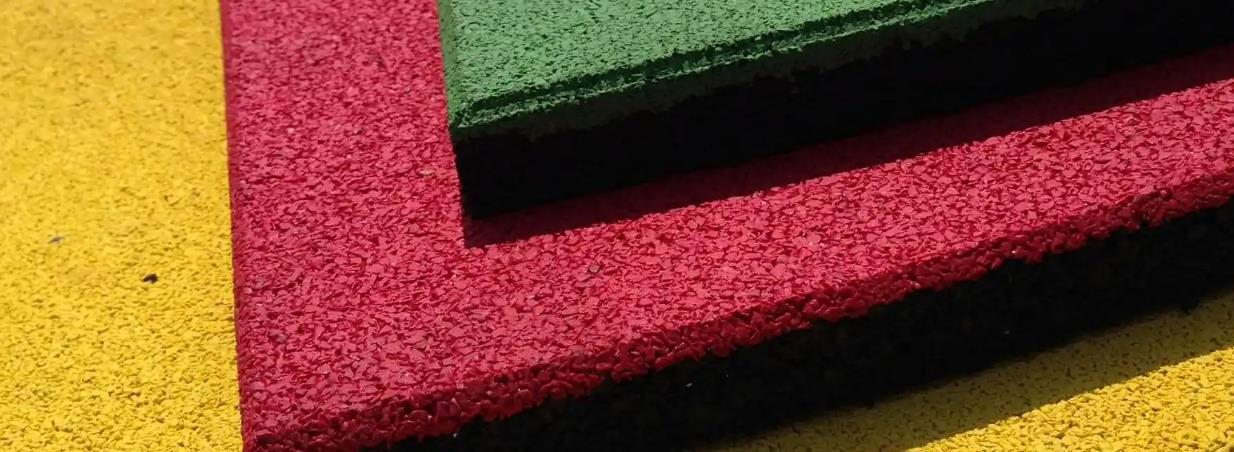
Types
EPDM masterbatch is usually classified based on its composition, performance characteristics, and application fields. The following are some common types:
Classified by rubber type
Ethylene propylene diene monomer (EPM) masterbatch: It is polymerized from two monomers, ethylene and propylene, and has good aging resistance, ozone resistance, and chemical corrosion resistance. However, due to the absence of double bonds on the molecular chain, the vulcanization rate is slow and the processing performance is relatively poor.
EPDM masterbatch: On the basis of ethylene and propylene, a third monomer such as ethylidene norbornene (ENB), dicyclopentadiene (DCPD), etc. is introduced, which contains double bonds on the rubber molecular chain, accelerates the vulcanization rate, improves the processing performance, and maintains the excellent properties of EPDM rubber.
Classified by filler type
Carbon black filled EPDM masterbatch: Carbon black is a commonly used filler that can improve the strength, wear resistance, conductivity, and aging resistance of rubber when added to EPDM masterbatch. According to the variety and dosage of carbon black, EPDM masterbatch with different properties can be obtained, which is suitable for different application fields. For example, EPDM masterbatch filled with high abrasion resistant carbon black can be used to manufacture products such as tire sidewalls and rubber hoses that require high abrasion resistance.
White carbon black filled EPDM masterbatch: White carbon black has good reinforcement and aging resistance, which can improve the hardness, tensile strength, and tear strength of EPDM rubber. At the same time, EPDM masterbatch filled with white carbon black also has good water resistance and electrical insulation properties, and is commonly used in the manufacture of insulation layers, waterproof rolls, seals, and other products for wires and cables.
Calcium carbonate filled EPDM masterbatch: Calcium carbonate is a low-cost and widely available filler that can be added to EPDM masterbatch to reduce costs and improve the processing performance of rubber. EPDM masterbatch filled with calcium carbonate can be used to manufacture some rubber products that do not require particularly high performance, such as ordinary rubber gaskets, shoe soles, etc.
Classified by functional additives
Flame retardant EPDM masterbatch: Flame retardants such as aluminum hydroxide, magnesium hydroxide, decabromodiphenyl ether, etc. are added to EPDM masterbatch to give it good flame retardant properties. Flame retardant EPDM masterbatch can be used to manufacture products with high fire safety requirements, such as wires and cables, automotive interior parts, etc.
Anti aging EPDM master batch: anti aging additives such as antioxidant and light stabilizer are added, which can improve the aging resistance of EPDM rubber during long-term use and prevent rubber products from cracking, hardening, embrittlement and other aging phenomena. Anti aging EPDM masterbatch is suitable for outdoor rubber products, such as building sealant strips, automobile door and window sealant strips, etc.
Plasticized EPDM masterbatch: Added plasticizers such as phthalates and sebacic acid esters, which can reduce the hardness of EPDM rubber, improve its flexibility and plasticity, and enhance its processability and low-temperature performance. Plasticized EPDM masterbatch is commonly used to manufacture rubber products that require a soft texture, such as rubber hoses, rubber toys, etc.
Classified by application field
EPDM masterbatch for automobiles: EPDM masterbatch with different performance characteristics has been developed to meet the special requirements of the automotive industry. For example, EPDM masterbatch used for automotive door and window sealing strips requires good weather resistance, ozone resistance, and sealing performance; EPDM masterbatch used for rubber products around automotive engines needs to have high heat and oil resistance.
EPDM masterbatch for wires and cables: EPDM masterbatch used for the insulation layer and sheath of wires and cables, in addition to requiring good electrical insulation performance, also needs to have aging resistance, wear resistance, low temperature resistance and other properties to ensure the safe operation of wires and cables under different environmental conditions.
EPDM masterbatch for construction: In the field of construction, EPDM masterbatch is commonly used to manufacture waterproofing membranes, sealing strips, rubber bearings, and other products. EPDM masterbatch for construction needs to have good weather resistance, water resistance, and UV resistance to ensure the long-term service life and waterproof sealing effect of building materials.
Fórmula
The formula ratio of EPDM masterbatch may vary depending on different types, performance requirements, and application scenarios. Here are some common examples of EPDM masterbatch formula ratios:
Universal EPDM masterbatch
EPDM rubber: 50-70 parts, providing basic elasticity, aging resistance and other properties.
Carbon black: 20-40 parts, used for reinforcement, improving strength, wear resistance, and aging resistance.
Zinc oxide: 3-5 parts, used as an active agent to promote sulfurization reaction.
Stearic acid: 1-2 parts, providing lubrication and promoting dispersion.
Vulcanizing agent: 1-2 parts, such as sulfur, to cause cross-linking reaction of rubber, form a three-dimensional network structure, and improve the performance of rubber.
Accelerator: 1-2 parts, accelerate the vulcanization reaction rate.
High hardness EPDM masterbatch
EPDM rubber: 40-60 parts.
White carbon black: 30-50 parts. White carbon black has a good reinforcement effect and can improve hardness and strength.
Zinc oxide: 4-6 parts.
Stearic acid: 1-2 parts.
Vulcanizing agent: 1-2 parts.
Accelerator: 1-2 parts.
Plasticizer: 5-10 parts, an appropriate amount of plasticizer can increase hardness while maintaining a certain degree of flexibility.
Flame retardant EPDM masterbatch
EPDM rubber: 40-60 parts.
Aluminum hydroxide: 50-80 parts, aluminum hydroxide is a commonly used flame retardant with good flame retardant effect and smoke suppression.
Zinc oxide: 3-5 parts.
Stearic acid: 1-2 parts.
Vulcanizing agent: 1-2 parts.
Accelerator: 1-2 parts.
Antioxidant: 1-2 parts, improve the antioxidant performance of rubber, and prevent aging during processing and use.
Cold resistant EPDM masterbatch
EPDM rubber: 50-70 parts.
Carbon black: 20-30 parts.
Zinc oxide: 3-5 parts.
Stearic acid: 1-2 parts.
Vulcanizing agent: 1-2 parts.
Accelerator: 1-2 parts.
Cold resistant plasticizer: 10-20 parts, such as dioctyl sebacate (DOS), can lower the glass transition temperature of rubber and improve its cold resistance.
It should be noted that the above formula ratios are for reference only. In actual production, adjustments and optimizations need to be made based on specific product requirements, raw material properties, and processing techniques. At the same time, there may be differences in the quality and performance of raw materials from different manufacturers, so sufficient testing and validation are needed before determining the formula.
Proceso de producción
The production process of EPDM masterbatch usually includes the following main steps:
Preparación de la materia prima
Rubber selection: Choose suitable EPDM rubber according to product performance requirements, such as varieties with different ethylene content and Mooney viscosity.
Additive preparation: Accurately weigh various additives, such as fillers (carbon black, white carbon black, calcium carbonate, etc.), vulcanizing agents, accelerators, plasticizers, antioxidants, etc., to ensure that the quality and purity of the additives meet the requirements.
Banburying
Add rubber and additives: Put EPDM rubber into the mixer, wait for the rubber to soften, and then add various additives in a certain order. Usually, fillers, plasticizers, etc. are added first, and after mixing evenly, vulcanizing agents, accelerators, etc. are added.
Control mixing conditions: Set appropriate mixing temperature, time, and speed. The mixing temperature is usually between 120-160 ℃ for 10-20 minutes, and the speed depends on the specific equipment and formula. By mixing rubber and additives thoroughly through compounding, a uniform mixture is formed, and at the same time, the rubber molecular chains are degraded to a certain extent, improving their processing performance.
Open refining
Further mixing and thinning: Transfer the mixed rubber material to the open mill for further mixing and thinning operations. By adjusting the roller spacing of the open mill, the rubber material is repeatedly passed between the rollers, further improving the uniformity and plasticity of the rubber material. The number of thin passes is generally 3-5 times.
Adjust the temperature and roller spacing of the rubber material: During the refining process, it is important to control the temperature of the rubber material, which should generally not be too high, to avoid causing the rubber material to burn. At the same time, adjust the roller spacing according to the state of the rubber material in a timely manner to achieve the appropriate softness and plasticity of the rubber material.
Granulación por extrusión
Extrusion of rubber material: The opened rubber material is fed into an extruder, and through the rotation of the extruder’s screw, the rubber material is subjected to compression and shear forces in the barrel, thereby being extruded into strips. The temperature setting of the extruder should be adjusted according to the characteristics of the rubber material and product requirements. Generally, the temperature gradually increases from the feeding section to the head, and the head temperature is controlled at around 100-120 ℃.
Granulation: The extruded rubber strip is cooled and shaped by air or water cooling, and then enters the granulator for granulation. Granulators usually use hot or cold cutting methods to cut rubber strips into particles of a certain size, thus obtaining EPDM masterbatch.
Package
Screening and packaging: Screen the EPDM masterbatch after granulation to remove particles that are too large or too small, as well as possible impurities. Then pack the qualified masterbatch into a packaging bag, taking care to prevent moisture and contamination during the packaging process. Packaging bags are generally made of plastic woven bags or composite bags with good moisture resistance, and the product name, specifications, production date, shelf life and other information are marked on the bag.
Throughout the entire production process, it is necessary to strictly control the process parameters of each link to ensure the quality stability and performance compliance of EPDM masterbatch. At the same time, regular maintenance and upkeep of production equipment should be carried out to ensure its normal operation, thereby improving production efficiency and product quality.
Production equipment
The equipment for producing EPDM masterbatch mainly includes the following types:
Equipos de mezcla
Internal mixer: It is a key mixing equipment in the production of EPDM masterbatch. Through two relatively rotating rotors, strong shearing, stirring, and mixing of rubber and additives are carried out in a closed mixing chamber to evenly disperse each component. The common ones are X (S) M series mixers, which are distinguished based on parameters such as rotor speed and mixing chamber capacity. For example, X (S) M-50/40 represents a total volume of 50 liters in the mixing chamber and a rotor speed of 40 revolutions per minute.
Refining equipment
Open mill: mainly used for further mixing, thinning, and adjusting the plasticity of the rubber material after mixing. Composed of two parallel rollers, the rubber material is repeatedly passed between the rollers by adjusting the spacing, speed, and temperature of the rollers, achieving uniform mixing and improving processing performance. Common models include SK-400, SK-550, etc. The number represents the diameter of the roller (in millimeters).
Extrusion granulation equipment
Extruder: Extrude the processed rubber material into strips. The design of its screw and barrel has a significant impact on the conveying, plasticizing, and extrusion quality of the rubber material. There are various specifications to choose from based on the diameter and aspect ratio of the screw, such as SJ-65/30, which means the screw diameter is 65 millimeters and the aspect ratio is 30.
Granulator: Used in conjunction with an extruder to make the extruded rubber strip into granules. Divided into hot cutting granulator and cold cutting granulator. The hot cutting granulator is used to cut the rubber strip into particles with a rotating tool while it is hot after extrusion, and the particle shape is relatively regular; The cold cutting granulator first cools the rubber strip before cutting, which is suitable for situations where high requirements are placed on the appearance and dimensional accuracy of the particles.
Auxiliary equipment
Ingredient system: including storage tanks, measuring devices, and conveying equipment for various raw materials, used for accurate weighing and conveying of rubber, additives, and other raw materials, ensuring the accuracy and stability of the formula.
Cooling system: used to cool the rubber material during mixing, opening, and extrusion processes, preventing performance degradation or burning caused by high temperature of the rubber material. Common cooling methods include water cooling and air cooling, which are achieved through cooling water pipelines or fans and other equipment.
Screening equipment: Screen the EPDM masterbatch after granulation to remove particles and impurities that do not meet the size requirements. The commonly used screening equipment is a vibrating screen, which screens based on the mesh size and vibration frequency of the sieve.
Packaging equipment: used to package the screened EPDM masterbatch. Including automatic weighing devices, sealing machines, etc., to achieve quantitative packaging and sealing of masterbatch, ensuring the quality of products during storage and transportation.
EPDM masterbatch extruder
Kerke’s masterbatch extruder can be used to produce EPDM masterbatch. Our EPDM masterbatch extruder has multiple models to choose from, which can meet different production requirements.
-
Extrusora de doble husillo para laboratorio
¿Cuándo necesitará una extrusora de doble husillo de laboratorio? Si desea realizar ensayos y pruebas de...
-
Extrusora de doble husillo paralelo
Nuestra extrusora de doble husillo paralelo corrotante está diseñada para la fabricación de compuestos y...
-
Extrusor triple (3 tornillos)
La extrusora de 3 tornillos es una nueva tecnología que tiene muchas ventajas. La extrusora de triple tornillo se utiliza principalmente...
-
Sistema de extrusión de doble etapa
El sistema de extrusión madre-bebé está diseñado para materiales especiales que no pueden procesarse en una extrusora de una etapa,...
-
Línea de amasado Banbury
Nuestra amasadora + extrusora está diseñada para realizar aplicaciones especiales con una capacidad de producción de 30kg/h a 1000kg/h....
-
Sistema de corte / Sistema de granulación
Diferentes materiales necesitan diferentes sistemas de corte, Kerke ofrece todo tipo de sistemas de corte, aquí está la explicación de...
Related requirements
The extruder plays a key role in the production of EPDM masterbatch, and the following are some requirements for the extruder:
Screw design
Length to diameter ratio: Generally, the length to diameter ratio is required to be between 20-30. A longer aspect ratio helps to fully mix, plasticize, and homogenize the rubber material inside the barrel, improving extrusion quality.
Groove depth: The groove depth should be designed according to the characteristics and production requirements of EPDM rubber. Deeper screw grooves can accommodate more rubber material, increase extrusion volume, but at the same time, they can also affect shear force and mixing effect; Shallow spiral grooves can enhance the shear effect, which is beneficial for the plasticization and dispersion of the rubber material, but the yield may be limited. Usually, the screw groove in the feeding section is deeper, while the screw grooves in the compression and metering sections gradually become shallower.
Compression ratio: The compression ratio is generally between 2-4. The appropriate compression ratio can subject the rubber material to appropriate compression and shear during extrusion, eliminate air in the rubber material, and improve the compactness and uniformity of the rubber material.
Driving system
Power: The driving power of the extruder should be selected based on factors such as the diameter of the screw, aspect ratio, production capacity, and the characteristics of the rubber material. Generally speaking, for extruders producing EPDM masterbatch, the driving power is around 15-55kW to ensure that the screw can provide sufficient torque and speed to smoothly extrude the rubber material.
Speed regulation performance: The drive system is required to have good speed regulation performance, which can accurately adjust the speed of the screw within a certain range to adapt to different production processes and product requirements. For example, when producing EPDM masterbatch with different specifications or properties, it may be necessary to adjust the screw speed to control the extrusion amount and the degree of plasticization of the rubber material.
Heating and cooling system
Heating method: Usually electric heating or thermal oil heating is used. The heating device should be able to uniformly heat the barrel, ensuring that the rubber material maintains a suitable temperature during the extrusion process. The heating temperature is generally between 100-200 ℃, and the specific temperature is adjusted according to factors such as the type and formula of EPDM rubber, as well as the characteristics of additives.
Cooling system: The cooling system should be able to timely and effectively control the temperature of the rubber material and the barrel, to prevent excessive temperature from causing the rubber material to burn or its performance to decrease. There are two cooling methods: water cooling and air cooling. Water cooling has a better effect, but corresponding cooling water pipelines and water sources need to be equipped; Air cooling is relatively simple and suitable for situations where cooling requirements are not particularly high. The cooling system should have good temperature control accuracy and be able to automatically adjust the cooling water or air volume according to changes in the temperature of the rubber material.
Head design
Shape and size: The shape and size of the machine head should be designed according to the product specifications and shape requirements of EPDM masterbatch. For example, when producing masterbatch for cylindrical particles, the machine head usually uses a circular die mouth; When producing masterbatch in the form of flakes or other special shapes, it is necessary to design corresponding shaped molds. The dimensional accuracy of the mold mouth should be high to ensure that the extruded masterbatch size is uniform and consistent.
Flow channel design: The flow channel of the machine head should be designed reasonably, so that the rubber material can flow evenly from the barrel to the mold mouth, avoiding uneven or stagnant rubber material flow rate, and preventing defects such as bubbles and cracks. The surface of the flow channel should be smooth to reduce the flow resistance of the rubber material, improve extrusion efficiency and product quality.
Control system
Temperature control: The control system should be able to accurately control the temperature of each section of the extruder, including the temperature of the barrel, head, and screw. Real time monitoring of temperature through temperature sensors and comparison with set values, automatically adjusting the working status of heating or cooling devices to maintain the temperature within the set range.
Pressure control: It can monitor and control the pressure changes during the extrusion process. When the pressure is too high or too low, it will promptly issue an alarm signal and take corresponding measures to adjust, such as adjusting the screw speed or cleaning the machine head filter screen, to ensure the stability of the extrusion process and product quality.
Production control: Based on the production plan and product requirements, the extrusion output of EPDM masterbatch is precisely controlled by adjusting parameters such as screw speed and feeding speed, achieving stable and efficient production. At the same time, the control system should also have data recording and storage functions to facilitate traceability and analysis of the production process.
Aplicación
EPDM masterbatch has excellent weather resistance, aging resistance, chemical corrosion resistance, as well as good elasticity and insulation properties, making it widely used in multiple fields. The following are some of the main application aspects:
Automotive industry
Sealing element: A sealing strip used for car doors, windows, engine compartment, trunk and other parts, which can effectively prevent rainwater, dust, noise, etc. from entering the car, and also play a role in shock absorption and buffering. The weather resistance and aging resistance of EPDM masterbatch can ensure that the sealing components maintain good performance during long-term use.
Rubber hoses: Rubber hoses are required for the cooling system, fuel system, air conditioning system, etc. of automobiles. Rubber hoses made of EPDM masterbatch have good corrosion resistance and high temperature resistance, and can withstand corrosion from different media and high temperature environments, ensuring the normal operation of various systems in automobiles.
Dust cover: a dust cover used for automotive suspension systems, steering systems, and other parts, which can prevent dust, sand, and other impurities from entering the interior of the components, reduce wear, and extend the service life of the components. The elasticity and wear resistance of EPDM masterbatch enable it to adapt to the movement and deformation of components.
Wire and cable
Insulation layer: As an insulation material for wires and cables, EPDM masterbatch has good insulation performance and weather resistance, which can effectively prevent current leakage and external environmental erosion of wires and cables, and improve the safety and reliability of wires and cables.
Sheath: EPDM masterbatch is usually used for the sheath of wires and cables, which has characteristics such as wear resistance, chemical corrosion resistance, and UV resistance. It can protect the conductors and insulation layers inside the wires and cables from external factors and extend the service life of the wires and cables.
Construction industry
Waterproof membrane: EPDM masterbatch is one of the important raw materials for producing waterproof membrane. The waterproof membrane produced has excellent weather resistance, water resistance, and puncture resistance, which can effectively prevent building leakage and is widely used in waterproofing projects such as roofs, basements, tunnels, etc.
Sealing material: A sealing material used for building doors, windows, curtain walls, expansion joints, and other parts, which can play a role in waterproofing, sound insulation, and thermal insulation. The elasticity and aging resistance of EPDM masterbatch can ensure that the sealing material maintains good sealing effect during long-term use.
Other areas
Rubber products: such as shoe soles, sports equipment, rubber hoses, etc. EPDM masterbatch can improve the performance of rubber products, enhance their weather resistance, wear resistance, and elasticity, and extend their service life.
Plastic modification: Adding EPDM masterbatch to plastics can improve their toughness, impact resistance, and weather resistance, expanding their application range. For example, adding EPDM masterbatch to polypropylene (PP), polyethylene (PE) and other plastics can improve their low-temperature toughness and anti-aging properties.