PBAT masterbatch is a granular material made by mixing PBAT resin with additives, fillers, etc., and then extruding, cutting, and other processes. Its core component PBAT is a biodegradable polyester synthesized through esterification or ester exchange reactions of 1,4-butanediol (BDO), adipic acid (AA), and terephthalic acid (PTA), which has good flexibility and processability.
Core features
Biodegradability
Under industrial composting conditions, PBAT masterbatch products can be completely degraded into carbon dioxide and water within 6-12 months, significantly reducing environmental pollution.
Physical property
Mechanical properties: High tensile strength (up to 20-30 MPa), excellent elongation at break (500% -800%), and better toughness than traditional plastics.
Processing performance: Melting point range of 120-180 ℃, density of 1.4-1.5g/cm ³, suitable for various processes such as blown film, injection molding, extrusion, etc.
Surface performance: High glossiness, strong printing adaptability, can meet the aesthetic requirements of packaging materials.
Environmental advantages
In line with the global trend of “plastic limit regulations”, it effectively replaces disposable plastic products and reduces white pollution.
Types
PBAT masterbatch is a biodegradable thermoplastic polyester typically composed of butyl adipate (BA) and butyl terephthalate (BT). According to different performance and application requirements, PBAT masterbatch can be divided into the following types:
Universal type: It has good comprehensive performance, such as mechanical strength, flexibility, processing performance, etc., and can be widely used in packaging, agriculture, medical and other fields.
High impact resistance type: By using a special formula and production process, the impact resistance of PBAT masterbatch is improved, making it less likely to break or be damaged when subjected to external impact. It is suitable for occasions that require high impact resistance of the product, such as injection molded products, films, etc.
High heat resistance type: It has high thermal stability and heat-resistant deformation temperature, can maintain its performance stability at high temperatures, is not easy to deform or degrade, and is commonly used in products that require high temperature resistance, such as electronic and electrical components, automotive parts, etc.
Smooth type: PBAT masterbatch is added with lubricants and other additives to give it good smooth performance, which can reduce the friction coefficient of the product surface, improve the processing efficiency and performance of the product, and is commonly used in the production of films, pipes and other products.
Antibacterial type: By adding functional additives such as antibacterial agents, PBAT masterbatch has antibacterial and anti mold functions, which can effectively inhibit the growth and reproduction of bacteria and mold, improve the hygiene performance and service life of the product, and is suitable for fields with high hygiene requirements such as medical and food packaging.
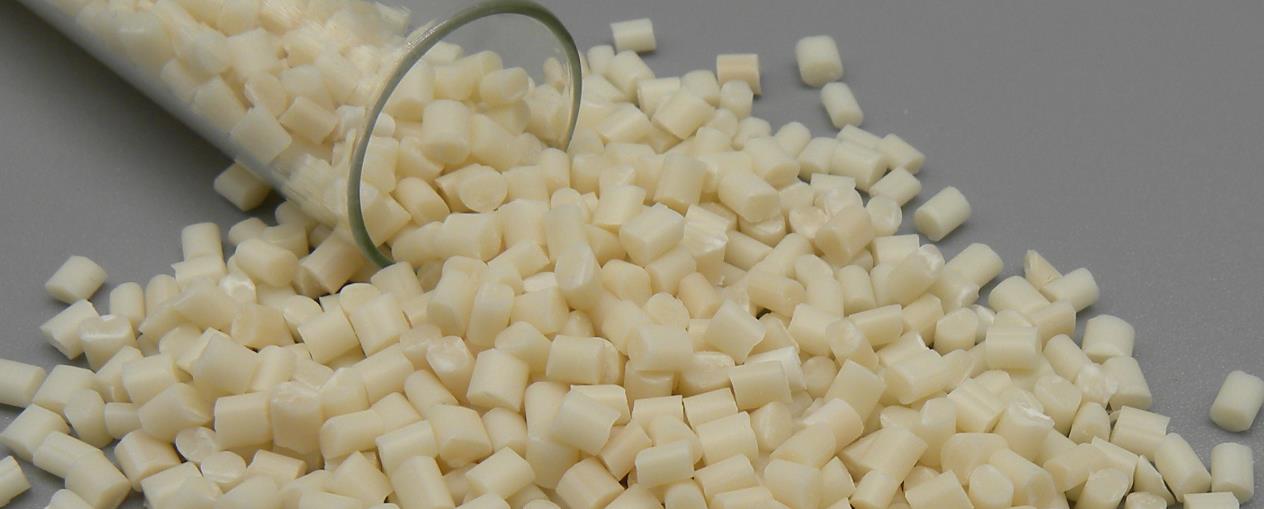
Fórmula
The formula ratio of PBAT masterbatch may vary depending on different application and performance requirements. Here are some common formula ratio examples:
High strength PBAT/starch biodegradable masterbatch: PBAT 55-70 parts, starch 15-30 parts, plasticizer 5-9 parts, reinforced polymer 10-30 parts, lubricant 1-4 parts, coupling agent 0.3-0.7 parts, antioxidant 0.2-0.5 parts.
PBAT masterbatch is used to prepare cling film: 20-50 parts PBAT, 0.5-2 parts lubricant, 0.5-2 parts antioxidant, 2-3 parts compatibilizer, 5-15 parts inorganic micro powder, 5-10 parts moisture absorbing material, 5-10 parts organic porous material, 0.6-2.2 parts mold inhibitor.
Fully biodegradable plastic film masterbatch: PBAT 70% -80%, modified nano silica 10% -30%, dispersant 4% -7%, lubricant processing aid 3% -6%, color powder 0% -5%.
In actual production, it is necessary to optimize and adjust the formula ratio based on specific production processes, equipment, and the final usage requirements of the product.
Proceso de producción
The production process of PBAT masterbatch usually includes the following main steps:
Preparación de la materia prima
Select PBAT resin, additives (such as plasticizers, antioxidants, lubricants, etc.) and other possible auxiliary materials to ensure that the quality and performance of the raw materials meet production requirements. Dry the raw materials to remove moisture and prevent defects such as bubbles and degradation caused by moisture during processing.
Mezcla de ingredientes
According to the performance requirements of the product, accurately weigh various raw materials according to a certain formula ratio. Add the weighed raw materials into the high-speed mixer for thorough mixing, so that various raw materials are evenly dispersed and form a premix.
Melt extrusion
Add the premix into the twin-screw extruder. The twin-screw extruder heats the material to above the melting point of PBAT (usually between 160-220 ℃) through a heating device, causing the material to melt. Under the rotation and pushing of the screw, the molten material is subjected to shear, extrusion and other effects in the extruder, further mixing evenly, while the additive is fully combined with PBAT resin. Then, the molten material is extruded through the die of the extruder head to form continuous strips or filaments.
Cooling pitching
The extruded strip or filamentous material is cooled by a water tank or air cooling device to rapidly solidify and shape, forming semi-finished masterbatch with certain strength and shape.
Diced
The cooled material is cut into particles of a certain size by a granulator to obtain PBAT masterbatch. The size of the cut particles can be adjusted according to the customer’s needs, with a general particle size of around 2-5mm.
Package
Sift the cut PBAT masterbatch to remove particles that are too large or too small, as well as potential impurities. Then, pack the qualified masterbatch into packaging bags and seal them for storage and transportation.
Throughout the entire production process, it is necessary to strictly control the process parameters of each link, such as temperature, speed, pressure, etc., to ensure the quality stability and performance compliance of PBAT masterbatch. At the same time, regular maintenance and upkeep of production equipment are necessary to ensure its normal operation, improve production efficiency and product quality.
Production equipment
The production process of PBAT masterbatch involves various equipment, and the following is an introduction to the main production equipment:
1. High speed mixer: used to thoroughly mix various raw materials such as PBAT resin and additives according to a certain formula ratio. By using high-speed rotating stirring blades, the raw materials can be uniformly mixed in a short period of time, preparing for the subsequent processing.
2. Twin screw extruder: It is the core equipment for PBAT masterbatch production. It has two interlocking screws that can efficiently transport, mix, shear, and plasticize materials. By precisely controlling parameters such as temperature, screw speed, and feed rate of the extruder, PBAT resin and additives can be fully and uniformly mixed in a molten state, ensuring the quality and stability of the masterbatch.
3. Cooling equipment: Common cooling equipment includes water-cooled tanks and air-cooled devices. Water cooling tank is used to allow extruded strip or filamentous materials to pass through the tank, utilizing the cooling effect of water to rapidly cool and solidify the materials; The air cooling device cools the material by blowing cold air from the fan, which is suitable for situations where the cooling speed is not particularly high, or for special formulas that are not suitable for contact with water.
4. Granulator: used to cut the cooled and solidified material into particles of a specified size. According to different cutting methods, it can be divided into hot cutting machines and cold cutting machines. Hot cutting machine is used to cut materials in a hot and soft state, with fast cutting speed and high efficiency, but it requires high operational requirements; The cold granulator cuts the material completely after it has cooled down, with high precision and regular particle shape.
5. Screening equipment: Generally, vibrating screens or rotary screens are used to screen the PBAT masterbatch after cutting, separating out oversized or undersized particles that do not meet the particle size requirements, as well as impurities that may be mixed in, to ensure the uniformity and purity of the product’s particle size.
6. Packaging equipment: including automatic measuring devices and sealing machines, etc. The automatic measuring device can accurately measure the weight of the masterbatch in each packaging bag, ensuring the accuracy and consistency of the packaging weight; The sealing machine is used to seal packaging bags containing masterbatch to prevent moisture, oxidation, or other contamination of the masterbatch, facilitating storage and transportation.
In addition to the main equipment mentioned above, the production workshop may also be equipped with auxiliary equipment such as raw material storage tanks, feeding devices, and air compressors to ensure the smooth progress of the entire production process.
PBAT masterbatch extruder
Kerke’s masterbatch extruder can be used to produce PBAT masterbatch. Our PBAT masterbatch extruder has multiple models to choose from, which can meet different production requirements.
-
Extrusora de doble husillo para laboratorio
¿Cuándo necesitará una extrusora de doble husillo de laboratorio? Si desea realizar ensayos y pruebas de...
-
Extrusora de doble husillo paralelo
Nuestra extrusora de doble husillo paralelo corrotante está diseñada para la fabricación de compuestos y...
-
Extrusor triple (3 tornillos)
La extrusora de 3 tornillos es una nueva tecnología que tiene muchas ventajas. La extrusora de triple tornillo se utiliza principalmente...
-
Sistema de extrusión de doble etapa
El sistema de extrusión madre-bebé está diseñado para materiales especiales que no pueden procesarse en una extrusora de una etapa,...
-
Línea de amasado Banbury
Nuestra amasadora + extrusora está diseñada para realizar aplicaciones especiales con una capacidad de producción de 30kg/h a 1000kg/h....
-
Sistema de corte / Sistema de granulación
Diferentes materiales necesitan diferentes sistemas de corte, Kerke ofrece todo tipo de sistemas de corte, aquí está la explicación de...
Related requirements
The requirements for the extruder in PBAT masterbatch production are mainly reflected in the following aspects:
Plasticizing capacity
High torque output: PBAT resin requires a large torque during the melting process to achieve full plasticization, so the extruder should have a high torque screw drive system to ensure that PBAT and additives can be uniformly plasticized at different production speeds and raw material formulations, so that the masterbatch has good performance consistency.
Optimized screw design: The structural design of the screw is crucial for the plasticizing effect. Usually, gradient or mutation type screws are used, with a length to diameter ratio between 25-40, to provide sufficient plasticizing length and time. Meanwhile, parameters such as groove depth and compression ratio on the screw need to be optimized based on the characteristics of PBAT to promote material melting, mixing, and transportation.
Mixing performance
Efficient mixing components: In order to fully and uniformly mix PBAT resin with various additives, the extruder needs to be equipped with efficient mixing components such as static mixers, kneading blocks, etc. These components can generate strong shear and dispersion effects during material transportation, ensuring that additives are evenly distributed in the PBAT matrix, thereby ensuring the stability and reliability of the masterbatch performance.
Good temperature control: Temperature control during the mixing process also has a significant impact on the quality of PBAT masterbatch. The extruder should have a precise temperature control system that can control the material temperature within an appropriate range at different production stages (generally PBAT processing temperature is between 160-220 ℃), avoiding PBAT degradation caused by high temperature or uneven mixing caused by low temperature.
Stability and reliability
High quality mechanical structure: The mechanical structure of the extruder should have sufficient strength and rigidity to withstand long-term high load operation. Key components such as screws and barrels should be made of wear-resistant and corrosion-resistant materials to extend the service life of the equipment, reduce production interruptions and product quality fluctuations caused by equipment failures.
Advanced control system: Equipped with advanced automation control system, it can accurately monitor and control various process parameters of the extruder, such as temperature, pressure, screw speed, feeding amount, etc. At the same time, the control system should have good stability and anti-interference ability to ensure stable operation in different production environments, ensuring the stability and consistency of product quality.
Production capacity
Adjustable output range: The production capacity of the extruder should be able to be flexibly adjusted according to market demand and production plans. It can meet the production needs of small batches and multiple varieties, while also providing high output during large-scale production. Generally speaking, the output of extruders used for PBAT masterbatch production can be adjusted between tens to hundreds of kilograms per hour.
Efficient extrusion system: In order to achieve high output, the extrusion system of the extruder needs to have efficient material conveying and extrusion capabilities. For example, using large-diameter screws and optimized die design can improve the extrusion speed and uniformity of materials, thereby increasing production efficiency and reducing production costs.
Adaptability
Multi material compatibility: Various types and proportions of additives may be added to the formula of PBAT masterbatch, such as plasticizers, antioxidants, color masterbatch, etc. The extruder should be able to adapt to the characteristics and formula changes of different raw materials, ensuring good plasticization, mixing, and extrusion effects under various raw material combinations, and producing PBAT masterbatch that meets quality requirements.
Diversified production of products: With the diversified performance and specification requirements of PBAT masterbatch products in the market, extruders should have a certain degree of flexibility, which can produce PBAT masterbatch products with different performance and specifications by adjusting process parameters or replacing some components, such as masterbatch with different particle sizes, hardness, and functional characteristics, to meet the needs of different customers.
Aplicación
PBAT masterbatch has good biodegradability, thermal stability, and processability, making it widely used in multiple fields. The following are some of the main application areas:
Campo de envasado
Shopping bags: PBAT masterbatch can be used to produce biodegradable shopping bags that can gradually decompose in natural environments, reducing the white pollution caused by traditional plastic bags to the environment.
Food packaging: Due to its non-toxic, odorless, and excellent barrier properties, it can be used as a food packaging material, such as food packaging bags, cling film, etc. It can ensure the freshness and safety of food while also naturally degrading after disposal.
Disposable tableware: PBAT masterbatch can be used to make various disposable tableware, such as meal boxes, tableware, etc. After use, it can be decomposed in soil or compost conditions, which meets environmental protection requirements.
Agriculture
Agricultural film: The agricultural film produced from PBAT masterbatch has good insulation, moisture retention, and light transmission properties. At the same time, it can naturally degrade in the soil after use, avoiding the adverse effects of traditional agricultural film residues on soil structure and crop growth.
Seedling bowl: The biodegradable seedling bowl is made of PBAT mother granules, which can provide a good growth environment for seedlings during the seedling cultivation process. It does not need to be removed during transplantation and can be directly buried in the soil, reducing damage to the seedling roots and not causing soil pollution.
Sector médico
Medical dressings: PBAT masterbatch has good biocompatibility and can be used to produce medical dressings, such as wound dressings, gauze, etc. It can naturally degrade after wound healing, reducing the pain and infection risk of patients when changing dressings.
Drug sustained-release carrier: PBAT masterbatch can be made into a drug sustained-release carrier, which encapsulates the drug and achieves slow drug release, prolongs the drug’s action time, and improves the drug’s efficacy.
Other areas
3D printing material: PBAT masterbatch has good thermal stability and flowability, making it suitable as a 3D printing material. It can print various complex shaped products, and the printed products have certain strength and toughness.
Fiber: PBAT masterbatch can be used to produce fibers such as clothing fibers, home textile fibers, etc. These fibers have a soft and comfortable feel, as well as biodegradable properties, which are in line with the development trend of environmentally friendly fashion.
Injection molded products: PBAT masterbatch can be used for injection molding to produce various daily and industrial products, such as toys, stationery, automotive interior parts, etc., while meeting product performance requirements and reducing environmental impact.