PPA masterbatch is made by blending LLDPE (linear low-density polyethylene) as the carrier resin, adding high concentration fluorinated polymers, and granulation through a special process. PPA masterbatch is a modified organic fluorine plastic processing functional masterbatch, mainly used to improve the processing performance of polyolefin resins. It is widely used in blown film, blow molding, extrusion, extrusion and other process products, such as films, cast films, pipes, wires, sheets, monofilaments, fibers, etc.
Classification
PPA masterbatch is usually classified in the following ways:
Classification by function
Rheological masterbatch: also known as leveling masterbatch, is a modified organic fluorine plastic processing functional masterbatch. It can effectively improve the processing performance of polyolefin resin with extremely low addition amount, such as reducing surface defects and eliminating melt fracture. It is widely used in blown film, blow molding, extrusion and other process products, such as films, pipes, wires, etc.
Anti static masterbatch: It can endow plastic products with anti-static properties, prevent the accumulation of dust on the surface of the product due to static electricity, improve the cleanliness and performance of the product, and is commonly used in fields such as electronics and packaging that are sensitive to static electricity.
Flame retardant masterbatch: Adding it to plastics can make them flame retardant, effectively prevent or delay the combustion of plastics, and improve the fire safety performance of plastic products. It is widely used in industries such as construction, automotive, and electronics.
Color masterbatch: Used for coloring plastics, it can evenly disperse various colors of pigments in the carrier resin to produce color masterbatch, and then add it to the plastic matrix to obtain the desired color for plastic products. It has the advantages of bright color, good dispersibility, and easy use.
Classification by carrier
Polyolefin carrier masterbatch: such as PPA masterbatch supported by polyolefins such as low-density polyethylene (LDPE), linear low-density polyethylene (LLDPE), high-density polyethylene (HDPE), polypropylene (PP), etc. This type of masterbatch has good compatibility with polyolefin resin and can play a good role in polyolefin plastic processing, widely used in the production of polyolefin plastic products.
Other carrier masterbatch: In addition to polyolefin carriers, there are also PPA masterbatch based on polyester (PET), polyamide (PA) and other carriers, which are suitable for processing corresponding engineering plastics. Depending on the performance requirements and processing characteristics of different engineering plastics, suitable carrier PPA masterbatch can be selected to improve their processing performance or give them specific functions.
Classification by Fluorinated Polymer Type
Fluoroelastomer PPA masterbatch: It has good elasticity and flexibility, which can improve the weather resistance, chemical corrosion resistance, and wear resistance of plastic products to a certain extent. It is commonly used in outdoor plastic products or occasions with high requirements for chemical resistance.
Fluororesin based PPA masterbatch: PPA masterbatch based on polytetrafluoroethylene (PTFE), polyvinylidene fluoride (PVDF), etc. Fluororesin has excellent properties such as high temperature resistance, chemical corrosion resistance, and low friction coefficient. Adding it to plastics can significantly improve the relevant properties of plastic products, making it suitable for some special fields with high performance requirements, such as aerospace, chemical, electronics, etc.
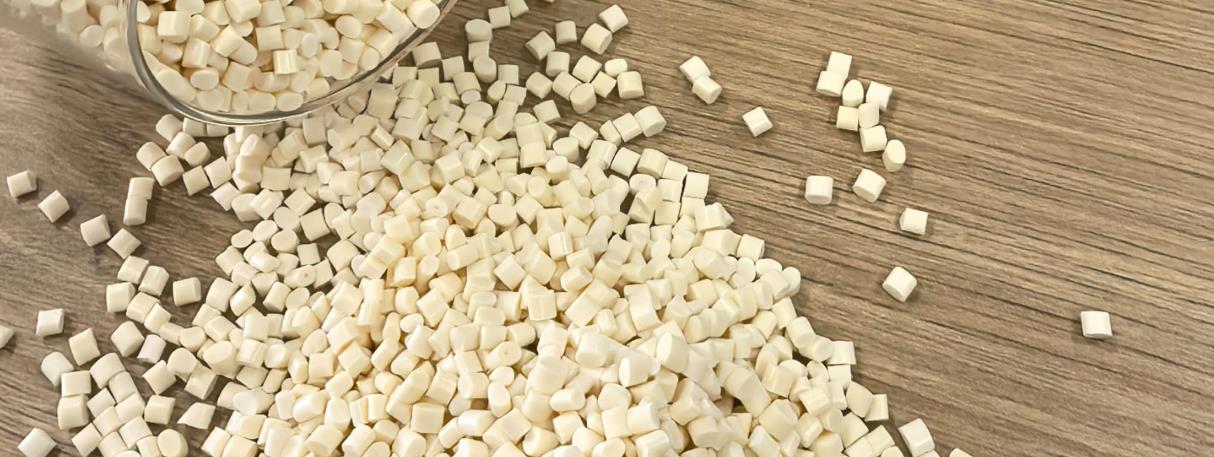
Fórmula
The formula ratio of PPA masterbatch may vary depending on different functions, carriers, and application requirements. Here are some examples of approximate formula ratios for common PPA masterbatch:
Rheological masterbatch
Fluoropolymer: generally accounting for 1% -10% of the total mass of the masterbatch, such as commonly used polytetrafluoroethylene (PTFE) micro powder or fluoroelastomer, which can effectively improve the processing rheological properties.
Carrier resin: usually accounting for 80% -95%, commonly used polyolefin resins include low-density polyethylene (LDPE), linear low-density polyethylene (LLDPE), or polypropylene (PP), which provide good processing performance for masterbatch and compatibility with matrix resin.
Dispersant: with a content of about 3% -10%, such as stearic acid, stearic acid salts, etc., it helps to evenly disperse fluorinated polymers in the carrier resin.
Antistatic masterbatch
Antistatic agents: accounting for 5% -20% of the mass of the masterbatch, commonly including quaternary ammonium salts, ethoxylated amines, etc., are key components that endow plastic products with anti-static properties.
Carrier resin: usually accounts for 60% -85%, and resins with good compatibility with the processed plastic, such as PE, PP, etc., can be selected to evenly disperse anti-static agents in plastic products.
Other additives: including dispersants, antioxidants, etc., with a total amount generally around 5% -15%, used to improve the processing performance and stability of masterbatch.
Flame retardant masterbatch
Flame retardant: It has a high content, generally accounting for 40% -80% of the total mass of the masterbatch. Common inorganic flame retardants include halogen based flame retardants, phosphorus based flame retardants, aluminum hydroxide, magnesium hydroxide, and their composite systems, which are the core components for achieving plastic flame retardant function.
Carrier resin: accounting for 15% -40%, suitable resin can be selected according to different plastic matrices, such as PP, PE, PET, etc., to carry and disperse flame retardants.
Synergistic agent: usually accounts for 5% -15%, such as antimony trioxide, etc. When used in combination with flame retardants, it can improve the flame retardant effect and reduce the amount of flame retardant used.
Masterbatch
Pigments: Depending on the required color depth and concentration, they generally account for 10% -50% of the mass of the masterbatch, including organic and inorganic pigments, and are key components that give color to plastic products.
Carrier resin: accounting for 40% -80%, commonly used include PE, PP, PET, etc. It is required to have good compatibility with the colored plastic matrix and be able to evenly disperse the pigment in the plastic product.
Dispersants: accounting for about 5% -10%, such as fatty acids and their esters, polyethylene wax, etc., help to fully disperse pigments in the carrier resin and improve the coloring effect of color masterbatch.
It should be noted that the above formula ratios are only a rough range. In actual production, optimization and adjustment are needed based on specific application requirements, types and properties of plastic matrices, processing technology, and other factors to obtain PPA masterbatch products with excellent performance.
Proceso de producción
The production process of PPA masterbatch usually includes steps such as raw material preparation, mixing, melt extrusion, cooling granulation, etc. The following is a specific introduction:
1. Preparación de la materia prima
Basic resin selection: Based on the application requirements of PPA masterbatch, select suitable basic resins such as polyethylene (PE), polypropylene (PP), polyamide (PA), etc. The base resin should have good fluidity, thermal stability, and compatibility with other additives.
Additive selection: Select corresponding additives based on the function of the masterbatch, such as rheological modifiers, antistatic agents, flame retardants, pigments, etc. Ensure that the purity, particle size, and performance of additives meet production requirements.
2. Mezcla
Pre mixing: Pre mix the base resin and additives according to the designed formula ratio in a high-speed mixer or other mixing equipment. By stirring, the additive is evenly dispersed on the surface of the base resin particles to form a preliminary mixture.
High speed mixing: In order to further improve the mixing effect, a high-speed mixer can be used for high-intensity mixing. During the high-speed mixing process, the material is subjected to strong shear and friction, which makes the mixing between the additive and the base resin more uniform, and also helps to increase the temperature of the material, preparing for subsequent melt extrusion.
3. Melt extrusion
Extruder selection: Choose the appropriate type and specification of extruder based on production scale and product requirements. Common types include single screw extruders and twin-screw extruders. Twin screw extruders have better mixing performance and self-cleaning ability, and are suitable for PPA masterbatch production that requires high mixing efficiency.
Heating and melting: Add the mixed material into the extruder hopper and heat it to a molten state through the extruder’s heating system. Different base resins and additives have different melting temperatures, and it is necessary to accurately control the temperature of each section of the extruder according to the specific situation to ensure that the material is extruded in a good flow state.
Screw extrusion: Under the rotation and pushing of the screw, the molten material is subjected to shear, extrusion, and mixing in the extruder barrel, further uniformly dispersing the additive in the base resin melt. The parameters such as screw speed, pitch, and compression ratio have a significant impact on the extrusion effect and mixing quality of materials, and need to be adjusted according to the actual production situation.
4. Cooling granulation
Cooling and shaping: The extruded molten material is extruded into strips or filaments through the die head, and then enters the cooling device for cooling and shaping. There are usually two cooling methods: air cooling and water cooling. Air cooling is suitable for masterbatch with high surface quality requirements, while water cooling has the advantages of fast cooling speed and high production efficiency.
Granulation: After cooling, the strip or silk material is cut into granules of a certain length by a granulator to obtain PPA masterbatch products. The tool speed and cutting length of the granulator can be adjusted according to product requirements to ensure uniform and consistent particle size of the masterbatch.
5. Embalaje
Quality inspection: Conduct quality inspection on the produced PPA masterbatch, including particle size distribution, appearance quality, additive content, performance indicators, and other aspects. Only products that meet quality standards can enter the packaging process.
Packaging and storage: PPA masterbatch that has passed inspection is packaged according to certain specifications and weights, usually in plastic woven bags or plastic bags, and sealed to prevent moisture and contamination of the masterbatch. The packaged masterbatch is stored in a dry and ventilated warehouse, waiting for shipment and sale.
Throughout the entire production process, it is necessary to strictly control the process parameters of each link to ensure the stable quality and reliable performance of PPA masterbatch. At the same time, in order to improve production efficiency and product quality, advanced production technologies and equipment such as online detection systems and automation control systems can also be adopted.
Production equipment
The PPA masterbatch production equipment mainly includes mixing equipment, extrusion equipment, cooling equipment, granulation equipment, etc. The following is a specific introduction:
1. Hybrid equipment
High speed mixer: used to preliminarily mix the base resin and additives according to the formula ratio. It uses high-speed rotating stirring blades to generate strong convection and shear in the mixing container, thereby achieving rapid and uniform mixing of materials. It has the advantages of high mixing efficiency and good mixing effect, and can mix various raw materials evenly in a short time.
Dual planetary mixer: suitable for occasions with high requirements for mixing uniformity. The stirring blade rotates while revolving, causing the material to experience complex motion and shear forces during the mixing process, effectively avoiding material agglomeration and stratification, and achieving finer mixing. Especially suitable for handling PPA masterbatch formulations containing multiple additives or with strict requirements for mixing quality.
2. Equipos de extrusión
Twin screw extruder: It is a commonly used equipment in PPA masterbatch production. It has two interlocking screws that can generate strong shear force and conveying capacity during rotation. Twin screw extruders can better achieve material mixing, plasticization, and dispersion, and have good processing effects on materials with high additive content or difficult to disperse. At the same time, it also has good self-cleaning ability, which can reduce the residue of materials in the barrel and ensure the stability of product quality.
Single screw extruder: relatively simple structure and low cost. Suitable for the production of PPA masterbatch with low mixing requirements and small production scale. The single screw extruder transports materials forward through the rotation of the screw, and heats, plasticizes, and extrudes them during the conveying process. Its advantages are simple operation and easy maintenance, but it is slightly inferior to twin-screw extruders in terms of mixing effect and ability to handle complex formulas.
3. Cooling equipment
Sink: Used for water-cooled cooling. Directly place the strip or filamentous material extruded from the extruder into a water tank, and rapidly solidify and shape the material through the cooling effect of water. The sink is usually equipped with a circulating water system to maintain stable water temperature and ensure consistent cooling effect. The water cooling method has a fast cooling speed, which can improve production efficiency and is suitable for the cooling needs of most PPA masterbatch.
Air cooling system: composed of fans, air ducts, and cooling brackets. After the material is extruded from the extruder, it is cooled by flowing air in the air cooling system. The air cooling method can make the surface of the masterbatch smoother and avoid the problem of residual moisture caused by water cooling, especially suitable for PPA masterbatch with high surface quality requirements, such as color masterbatch used in high-end plastic products.
4. Equipo de granulación
Hot cutting granulator: When the material is in a molten state, the extruded strip or silk is cut into particles by a rotating tool. The contact time between the cutting tool and the material of the hot cutting granulator is short, the cutting speed is fast, and it can produce particles with uniform particle size and smooth surface. Suitable for producing PPA masterbatch of various specifications, especially for granulation of high viscosity materials.
Cold cutting granulator: First, the extruded material is cooled and shaped before cutting and granulating. The structure of a cold cutting granulator is relatively simple and easy to operate, but its production efficiency is relatively low. The surface quality and particle size accuracy of the particles may not be as good as those of a hot cutting granulator. Suitable for situations where particle appearance requirements are not particularly strict and production scale is small.
5. Auxiliary equipment
Feeding machine: used to automatically transport raw materials to the hopper of mixing equipment or extruder. Common ones include screw feeders, pneumatic feeders, etc. The feeding machine can improve the automation level of production, reduce the labor intensity of manual feeding, and ensure the stability and accuracy of raw material supply.
Measuring equipment: including electronic scales, flow meters, etc., used to accurately measure the amount of various raw materials added. Accurate raw material measurement is crucial for ensuring the stability of product quality in PPA masterbatch production. The measuring equipment can accurately add raw materials according to the set formula ratio, avoiding product performance fluctuations caused by inaccurate raw material usage.
Packaging machine: used for packaging the produced PPA masterbatch. Common types include automatic packaging machines and semi-automatic packaging machines, which can complete packaging processes such as weighing, bagging, and sealing of materials. The packaging speed and accuracy of the packaging machine directly affect production efficiency and product packaging quality. The appropriate packaging machine model can be selected according to production scale and packaging requirements.
PPA masterbatch extruder
Kerke’s masterbatch extruder can be used to produce PPA masterbatch. Our PPA masterbatch extruder has multiple models to choose from, which can meet different production requirements.
-
Extrusora de doble husillo para laboratorio
¿Cuándo necesitará una extrusora de doble husillo de laboratorio? Si desea realizar ensayos y pruebas de...
-
Extrusora de doble husillo paralelo
Nuestra extrusora de doble husillo paralelo corrotante está diseñada para la fabricación de compuestos y...
-
Extrusor triple (3 tornillos)
La extrusora de 3 tornillos es una nueva tecnología que tiene muchas ventajas. La extrusora de triple tornillo se utiliza principalmente...
-
Sistema de extrusión de doble etapa
El sistema de extrusión madre-bebé está diseñado para materiales especiales que no pueden procesarse en una extrusora de una etapa,...
-
Línea de amasado Banbury
Nuestra amasadora + extrusora está diseñada para realizar aplicaciones especiales con una capacidad de producción de 30kg/h a 1000kg/h....
-
Sistema de corte / Sistema de granulación
Diferentes materiales necesitan diferentes sistemas de corte, Kerke ofrece todo tipo de sistemas de corte, aquí está la explicación de...
Related requirements
In the production of PPA masterbatch, the performance of the extruder is crucial for product quality and production efficiency. The following are specific requirements for the extruder:
Good plasticizing ability
Accurate heating system: The heating system of the extruder should be able to accurately control the temperature, so that PPA raw materials can be uniformly plasticized within the set temperature range. Usually, the processing temperature of PPA raw materials is relatively high, usually around 280-320 ℃. Different types of PPA and different additives added will have different requirements for the processing temperature. The heating system needs to have a temperature control accuracy of ± 2 ℃ to ensure that the material reaches a good plasticization state, avoiding material decomposition caused by high temperature or poor plasticization caused by low temperature.
Reasonable screw design: The length to diameter ratio, compression ratio and other parameters of the screw should be designed reasonably according to the formula and production requirements of PPA masterbatch. The aspect ratio is generally between 25-40, and a larger aspect ratio is beneficial for the full plasticization and mixing of materials; The compression ratio is usually between 3-5, and an appropriate compression ratio can gradually compact and plasticize the material during the screw pushing process, improving the plasticization quality.
Efficient mixing performance
Optimization of screw structure: Specially designed hybrid screw components, such as pin screws, barrier screws, etc., are used to increase the shear and mixing effects of materials inside the screw barrel, allowing PPA resin to be uniformly mixed with various additives. For example, the pins on the screw can disrupt the flow path of the material, promote mutual diffusion and mixing between different components, ensure uniform dispersion of additives in the PPA matrix, and thus improve the performance stability of the masterbatch.
Equipped with lateral feeding function: In order to better add some special additives or fillers, the extruder should have a lateral feeding device. The position and structure of the lateral feeding port should be designed reasonably, so that additives can be added in a timely manner during the material plasticization process and fully mixed with PPA resin. This can prevent some heat sensitive additives from degrading or deteriorating when extruded together with the main material at high temperatures for a long time, and also help improve the mixing effect, especially for some additives that are difficult to disperse. Lateral feeding can significantly improve their dispersibility in the masterbatch.
Stable extrusion accuracy
Stable extrusion volume: The screw speed and drive system of the extruder should have good stability to ensure that the fluctuation of extrusion volume is controlled within a small range during the production process. It is generally required that the fluctuation coefficient of extrusion volume should not exceed ± 3% in order to ensure that the produced PPA masterbatch has high consistency in quality and performance. By using high-precision motors, reducers, and advanced control systems, precise control of screw speed can be achieved, thereby stabilizing extrusion volume.
Accurate pressure control: During the extrusion process, changes in pressure inside the screw barrel can affect the extrusion stability of the material and product quality. The extruder needs to be equipped with precise pressure sensors and control systems to monitor and adjust the pressure inside the screw in real time. For example, when the pressure is too high, the control system automatically adjusts the screw speed or feed rate to reduce the pressure; When the pressure is too low, timely measures should be taken to increase the pressure, ensuring that the pressure fluctuation is controlled within ± 0.5MPa, thereby ensuring the stability of the extrusion process and the reliability of product quality.
High wear resistance and corrosion resistance
Excellent material selection: Due to the production process of PPA masterbatch, the material causes significant wear on the screw and barrel, especially when the formula contains fillers such as glass fiber and talcum powder, the wear is more severe. Therefore, screws and screw barrels are usually made of high wear-resistant alloy steel, such as 38CrMoAlA, and undergo nitriding treatment or hard chromium plating treatment to improve their surface hardness and wear resistance, and extend the service life of the equipment. Generally, it is required that the wear resistance of screws and screw barrels can meet the continuous production of 5000-8000 hours or more without the need for large-scale maintenance or replacement.
Corrosion resistant design: If the PPA masterbatch formula contains some corrosive additives, such as certain flame retardants, antioxidants, etc., the screw and barrel of the extruder also need to have good corrosion resistance. In addition to selecting suitable corrosion-resistant materials, special anti-corrosion coatings or liners such as polytetrafluoroethylene coatings can also be used on the surface of screws and screw barrels to prevent corrosive substances from corroding the equipment, ensuring the normal operation of the equipment and product quality are not affected.
High degree of automation control
Intelligent control system: The extruder should be equipped with an advanced automation control system to achieve real-time monitoring and automatic adjustment of key parameters such as temperature, pressure, screw speed, and feed rate. Through the Human Machine Interface (HMI), operators can easily set and modify process parameters, and visually view the operating status and production data of the equipment. The intelligent control system should also have fault diagnosis and alarm functions, which can timely detect problems in equipment operation and issue alarms, prompting operators to take corresponding measures to improve production safety and efficiency.
Data recording and traceability: In order to ensure the traceability of product quality and optimize the production process, the automation control system of the extruder should have data recording and storage functions, which can record various process parameters and production data during the production process, such as production time, temperature changes, extrusion volume, etc. for each batch. These data can be saved for several years or even longer, facilitating production management, quality analysis, and product traceability for enterprises, while also providing a basis for process improvement and equipment optimization.
Aplicación
PPA masterbatch has excellent performance and is widely used in multiple fields. The following are some of its main applications:
Plastic Modification
Improving heat resistance: PPA masterbatch can be used to enhance the heat resistance of general plastics such as polypropylene (PP), polyethylene (PE), etc. In the field of electronics and electrical appliances, many components need to work stably at high temperatures. By adding PPA masterbatch, plastic parts can maintain good mechanical properties and dimensional stability in high temperature environments of 150-200 ℃, meeting the high temperature resistance requirements of electronic and electrical products.
Enhanced mechanical properties: PPA masterbatch can significantly enhance the mechanical properties of plastics, such as tensile strength, bending strength, and impact strength. In the manufacturing of automotive components, such as car interior parts and engine peripheral components, adding PPA masterbatch to plastics can withstand greater external forces and impacts, improving the reliability and service life of components.
Improving chemical resistance: PPA masterbatch can enhance the chemical corrosion resistance of plastics. In the fields of chemical engineering, food packaging, etc., plastic containers and pipelines need to come into contact with various chemical substances. The plastic added with PPA masterbatch can resist the erosion of chemicals such as acid, alkali, and organic solvents, ensuring the safety and stability of the packaging and transportation process.
Fiber manufacturing
Production of high-performance fibers: In synthetic fiber production, adding PPA masterbatch can produce fibers with high modulus, high strength, and high temperature resistance. These high-performance fibers can be used to manufacture parachutes and flight suits in the aerospace industry, as well as bulletproof vests and ropes in the military field, capable of withstanding extreme stress and friction under extreme conditions.
Improving the dyeing performance of fibers: PPA masterbatch can enhance the dyeing performance of fibers, making them easier to color and resulting in brighter and more durable colors after dyeing. In the textile industry, this helps to produce high-quality, colorful textiles that meet the needs of fashion and functional clothing.
Thin film applications
Manufacturing high-performance packaging films: In the packaging field, PPA masterbatch can be used to produce packaging films with high barrier properties, high strength, and good heat sealing performance. This film can effectively block oxygen, water vapor, and odors, protect food, medicine, and other products inside the packaging from external environmental influences, and extend the shelf life of the products.
Agricultural film: Agricultural film with added PPA masterbatch has better weather resistance and insulation performance. It can be used outdoors for a long time without aging or cracking, while effectively maintaining soil temperature and humidity, promoting crop growth, and improving crop yield and quality.