PP masterbatch, also known as polypropylene masterbatch, is a granular material made on the basis of polypropylene (PP) resin by adding various additives (such as pigments, fillers, plasticizers, antioxidants, etc.) and undergoing processes such as mixing and granulation.
Classification of PP masterbatch
PP masterbatch, also known as polypropylene masterbatch, can usually be classified according to function and purpose as follows:
Filling masterbatch:
Mainly composed of PP resin, calcium carbonate and other filling materials, as well as a small amount of additives. By adding filler masterbatch, the cost of PP products can be reduced, while also improving certain properties of the products, such as increasing hardness and dimensional stability. Generally, it is widely used in fields that are cost sensitive and do not have particularly high requirements for product performance, such as ordinary plastic pipes, injection molded parts, etc.
Flame retardant masterbatch:
It is made by adding halogen based, phosphorus based, nitrogen based flame retardants and related additives to PP resin. It can endow PP material with good flame retardant properties, making it comply with different fire safety standards. Commonly used in fields such as electronic and electrical enclosures, wires and cables that require flame retardant performance to improve product safety and reduce fire risks.
Anti aging masterbatch:
Contains ingredients such as UV absorbers and antioxidants. It can effectively improve the aging resistance of PP products in outdoor environments or long-term use, and prevent PP materials from degrading, discoloring, and becoming brittle due to factors such as light, oxygen, and temperature. Widely used in outdoor plastic products, such as shade nets, agricultural films, automotive parts, etc., to extend the service life of products.
Antibacterial masterbatch:
It is made by adding antibacterial agents such as silver and copper to PP resin. It can inhibit the growth and reproduction of microorganisms such as bacteria and mold on the surface of PP products, and maintain the cleanliness and hygiene of the products. Commonly used in the fields of food packaging, medical devices, daily necessities, etc., to provide antibacterial function for products and ensure the health of users.
Toughened masterbatch:
Usually composed of elastomers, compatibilizers, etc. It can improve the toughness and impact resistance of PP materials, making them less prone to cracking at low temperatures or under external impact. It is widely used in fields such as automotive interior parts, pipes, and injection molded toys that require material toughness to improve product durability and reliability.
Transparent masterbatch:
Adding nucleating agents and other additives can improve the transparency of PP products. Enable PP materials to have better optical properties while maintaining their original properties. Commonly used in fields that require high transparency, such as transparent plastic containers and packaging films, to enhance the appearance quality and visual effect of products.
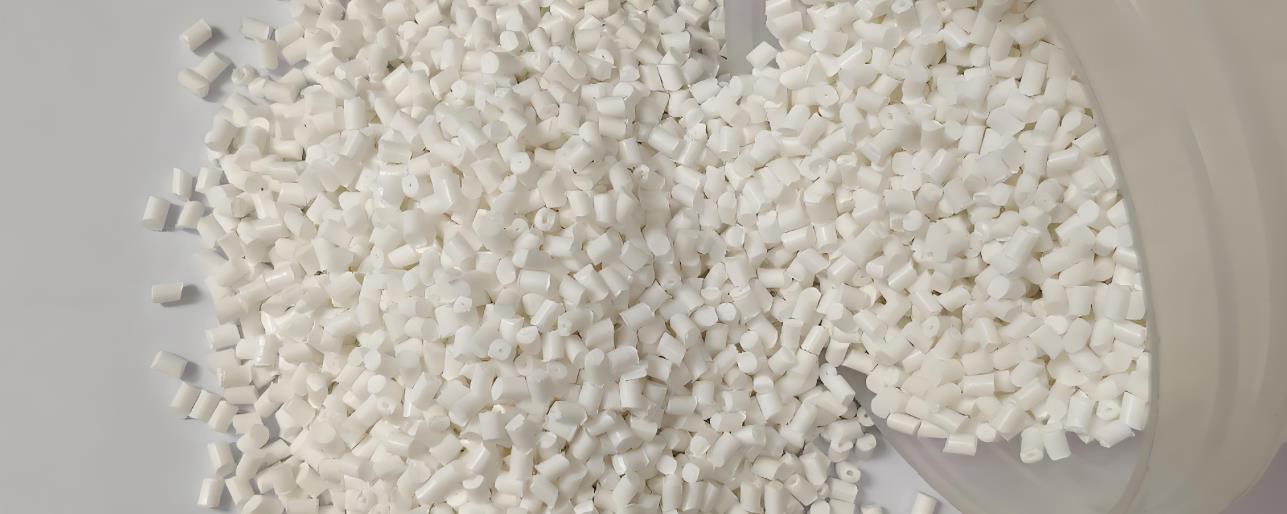
نسبة الصيغة
Filling masterbatch: PP resin is used as a carrier, and its content is usually between 15% and 36%. Filling materials such as calcium carbonate generally account for 60% -80% of the mass of the masterbatch. In addition, about 1% of titanium or aluminum esters will be added as coupling agents, as well as 3% -5% of processing modifiers to improve processing performance.
ماسترباتش مقاوم للهب
Halogen flame retardant PP masterbatch: carrier resin (PP) accounts for 40% -50%, bromine based flame retardants (such as decabromodiphenyl ether or brominated polystyrene) account for 30% -40%, antimony trioxide (synergist) accounts for 5% -10%, dispersants (such as polyethylene wax) account for 2% -3%, lubricants (such as calcium stearate) account for 1% -2%, antioxidants (such as 1010 or 168) account for 0.5% -1%.
Halogen free flame retardant PP masterbatch: carrier resin (PP) accounts for 30% -40%, phosphorus based flame retardants (such as ammonium polyphosphate APP or red phosphorus) account for 20% -30%, nitrogen based flame retardants (such as melamine cyanurate MCA) account for 10% -15%, magnesium hydroxide or aluminum hydroxide account for 20% -30%, dispersants (such as polyethylene wax) account for 2% -3%, lubricants (such as zinc stearate) account for 1% -2%, antioxidants (such as 1010 or 168) account for 0.5% -1%.
Anti aging masterbatch: generally, PP resin accounts for a large proportion, about 80% -95%, and anti-aging additives such as ultraviolet absorbers and antioxidants account for 5% -20%. The specific ratio should be determined based on the required aging resistance and usage environment of PP products.
Toughened masterbatch: PP resin usually accounts for 60% -80%, elastomers (such as ethylene propylene rubber, POE, etc.) account for 20% -30%, and compatibilizers account for 5% -10%. For example, in some antibacterial and anti-aging polypropylene plastic products using toughening modified masterbatch, the weight ratio of composite toughening agent, POE, and auxiliary agent is 3:5:0.2, and the auxiliary agent is composed of dispersant, lubricant, and crosslinking agent in a weight ratio of 1:1:2.
Transparent masterbatch: PP resin is the main component, accounting for 90% -98%, and nucleating agents and other additives account for 2% -10%. The type and amount of nucleating agent have a significant impact on the transparency of PP products, and need to be selected and adjusted according to specific resin models and product requirements.
عملية الإنتاج
The production process of different types of PP masterbatch has similarities in steps such as raw material preparation, additive selection, and mixing, but key process steps may vary depending on the type of masterbatch. The following are the production processes for several common types of PP masterbatch:
ملء ماسترباتش
1. Raw material preparation: Polypropylene (PP) resin is selected as the matrix resin, usually in granular or powdered form. Calcium carbonate is usually chosen as the filling material, which requires uniform particle size distribution and high purity. Meanwhile, prepare an appropriate amount of dispersants, coupling agents, and other additives.
2. Mixing: Add PP resin, calcium carbonate, and additives in a certain proportion to a high-speed mixer for thorough mixing. By high-speed stirring, calcium carbonate is uniformly dispersed on the surface of PP resin particles, and the auxiliary agent can also fully contact with the raw materials, preparing for subsequent processing.
3. Melt extrusion: The mixed material enters the twin-screw extruder and melts the PP resin at high temperature (usually 180-220 ℃). At the same time, the rotation of the screw pushes the material forward. In this process, calcium carbonate is further uniformly dispersed in the PP melt.
4. Cooling granulation: The molten material extruded by the extruder forms filaments through the die head, and then enters the cooling water tank for cooling and shaping. After cooling, the silk strands are cut into uniform particles by a granulator to obtain the filling masterbatch.
ماسترباتش مقاوم للهب
1. Raw material selection: PP resin is used as the basic raw material, and suitable flame retardants such as halogen, phosphorus, or nitrogen flame retardants are selected according to the required flame retardant level and performance requirements. At the same time, appropriate synergists, antioxidants, and other additives are added.
2. Pre mixing: PP resin is preliminarily mixed with flame retardants, additives, etc. in a low-speed mixer to achieve uniform distribution of each component.
3. Mixing: The pre mixed material enters the mixing machine for mixing. During the mixing process, the flame retardant is fully mixed with PP resin and undergoes a certain chemical reaction through high temperature (190-230 ℃) and strong shear action, which improves the dispersion and bonding strength of the flame retardant in PP.
4. Extrusion granulation: The material after mixing is then fed into a single screw or twin-screw extruder for extrusion granulation. During the extrusion process, further adjust process parameters such as temperature, screw speed, etc. to ensure the uniformity and stability of the material. The extruded melt is cooled and pelletized to obtain flame-retardant masterbatch.
ماستر باتش مضاد للشيخوخة
1. Raw material preparation: PP resin is used as the matrix, and efficient ultraviolet absorber, antioxidant and other anti-aging additives are selected. These additives need to have good thermal stability and compatibility.
2. Mixing: add PP resin and anti-aging additives into the mixer in proportion and fully mix them. To improve the mixing effect, a step-by-step mixing method can be used. First, mix a small amount of resin with additives evenly, and then gradually add the remaining resin.
3. Melt blending: The mixed materials are put into a twin-screw extruder for melt blending. The temperature of the extruder is set at about 180-220 ℃. Through the rotation and shearing of the screw, the anti-aging additives are evenly dispersed in the melt of PP resin to form a stable blend system.
4. Granulation: The melt extruded by the extruder is cooled by water cooling or air cooling, and then cut into granules by the pelletizer to make anti-aging master batch.
Toughened masterbatch
1. Raw material selection: The main raw materials include PP resin, elastomers (such as ethylene propylene rubber, POE, etc.), and compatibilizers. The selection of elastomers should be determined based on the performance requirements and usage environment of PP, and compatibilizers are used to improve the compatibility between elastomers and PP resins.
2. Ingredient mixing: Mix PP resin, elastomer, and compatibilizer in a high-speed mixer in a certain proportion. During the mixing process, attention should be paid to controlling the stirring speed and time to ensure uniform mixing of all components.
3. Dynamic vulcanization: Add the mixed materials into a twin-screw extruder with dynamic vulcanization function. In the extruder, the elastomer is dynamically vulcanized in the PP resin matrix through high temperature (usually 190-230 ℃) and strong shear action, forming a blend with a microscopic sea island structure, in which the elastomer particles are uniformly dispersed in the continuous phase of the PP resin.
4. Cooling granulation: After dynamic vulcanization, the material is extruded from the extruder, cooled by air or water cooling system, and then cut into particles of specified size by the granulator to obtain toughening masterbatch.
معدات الإنتاج
The equipment for producing different types of PP masterbatch is basically the same, mainly including batching equipment, mixing equipment, extrusion equipment, cooling equipment, and cutting equipment. The following is a specific introduction:
1. Ingredient equipment
Electronic scale: used for precise weighing of various raw materials, such as PP resin, additives, fillers, etc. According to the production scale and accuracy requirements, electronic scales with different ranges and accuracies can be selected, with a general accuracy requirement between ± 0.1g and ± 1g.
Ingredient hopper: usually made of stainless steel, used for storing and supplying various raw materials. The ingredient hopper has a certain capacity and can be designed according to production needs. It is also equipped with an automatic feeding device that can transport raw materials to the mixing equipment according to the set ratio.
2. المعدات الهجينة
High speed mixer: It is a commonly used mixing equipment in the production of PP masterbatch. It uses high-speed rotating stirring blades to achieve uniform mixing of materials in a short period of time. The material of the mixer is generally stainless steel, which has good corrosion resistance and wear resistance. Its working principle is to use the high-speed rotation of the propeller blades to generate strong vortices, causing the materials to flip up and down and collide with each other in the container, thereby achieving uniform mixing.
Internal mixer: For some formulas that require more thorough mixing and dispersion, such as flame retardant masterbatch, internal mixer is a commonly used equipment. The internal mixer has two relatively rotating rotors with special spiral edges. In a closed mixing chamber, materials are strongly sheared, squeezed, and stirred by the rotors, which can achieve more uniform mixing and higher dispersion.
3. معدات البثق
Twin screw extruder: It is one of the core equipment for PP masterbatch production. It consists of two parallel screws and a barrel, and the screws have different thread structures and functional sections, such as conveying section, compression section, mixing section, and extrusion section. Twin screw extruders can provide strong shear force and mixing effect, allowing materials to fully melt, mix, and homogenize under high temperature and high pressure. According to production capacity and product requirements, twin-screw extruders with different specifications and aspect ratios can be selected.
Single screw extruder: In some situations where mixing requirements are not high and production scale is small, single screw extruders are also used. Single screw extruder has a relatively simple structure and lower cost, but its mixing effect is not as good as that of twin-screw extruder. It mainly pushes the material forward through the rotation of the screw, and melts and extrudes the material under the heating effect of the barrel.
4. معدات التبريد
Cooling water tank: used for cooling and shaping the extruded PP masterbatch filament. The sink is generally made of stainless steel material and equipped with a circulating water system inside, which can control the water temperature within a certain range, ensure rapid cooling of the wire, and improve production efficiency and product quality.
Air cooling system: For some situations where water cooling is not suitable, such as the production of certain special functional masterbatch, an air cooling system can be used. The air cooling system blows cold air towards the extruded filaments or particles through a fan, allowing them to cool naturally in the air. The advantage of an air-cooled system is that it does not introduce moisture, avoiding some possible quality issues, but the cooling efficiency is relatively low.
5. معدات التحبيب
Underwater pelletizer: It is currently a widely used pelletizing equipment in the production of PP masterbatch. It directly cuts the extruded melt into particles underwater, with advantages such as uniform cutting, regular particle shape, and high production efficiency. The working principle of the underwater pelletizer is that the molten material is extruded from the die and immediately enters the pelletizing chamber filled with water. It is cut into particles by the high-speed rotating cutter and then transported to the dehydration and drying system together with water.
Air cooled granulator: suitable for occasions where the appearance requirements for particles are not particularly high. It cools and solidifies the extruded filament by air cooling, and then cuts the filament into particles by a cutting knife. The air-cooled pelletizer has a simple structure and easy operation, but the pelletizing quality and production efficiency are relatively low compared to underwater pelletizers.
6. المعدات المساعدة
Drying equipment: used for drying raw materials or masterbatch to remove moisture and volatile substances, in order to prevent quality problems such as bubbles and hydrolysis during the production process. Common drying equipment includes ovens, boiling dryers, dehumidifiers, etc.
Filtering equipment: During the extrusion process, in order to ensure product quality, it is necessary to filter the melt to remove impurities and unmelted particles. Filtering equipment usually uses filters, filter cartridges, or dynamic filtering devices, installed on the head or barrel of the extruder.
Packaging equipment: used for packaging the produced PP masterbatch. Packaging equipment includes automatic measuring scales, sealing machines, labeling machines, etc., which can achieve quantitative packaging of masterbatch and label pasting, improving packaging efficiency and quality.
PP masterbatch extruder
Kerke’s masterbatch extruder can be used to produce PP masterbatch. Our PP masterbatch extruder has multiple models to choose from, which can meet different production requirements.
-
آلة البثق اللولبية المزدوجة للمختبر
متى ستحتاج إلى آلة بثق ثنائية اللولب للمختبر؟ إذا كنت ترغب في إجراء تجارب واختبارات...
-
آلة البثق ذات اللولب المزدوج المتوازي
تم تصميم آلة البثق ذات المسمار المزدوج ذات الدوران المتوازي لدينا لتصنيع المركبات والدفعات الرئيسية مع سعة إنتاج تتراوح من...
-
طارد ثلاثي (3 براغي)
آلة البثق ثلاثية البراغي هي تقنية جديدة ذات مزايا عديدة. تُستخدم آلة البثق ثلاثية البراغي بشكل رئيسي...
-
نظام البثق ثنائي المرحلة
تم تصميم نظام بثق الأم والطفل للمواد الخاصة التي لا يمكن معالجتها على مرحلة واحدة من البثق، المرحلة الأولى...
-
خط تصنيع العجنات في بانبوري
تم تصميم آلة العجن والبثق الخاصة بنا لصنع تطبيقات خاصة بسعة إنتاج تتراوح من 30 كجم / ساعة إلى 1000 كجم / ساعة.
-
نظام القطع / نظام التكوير
تحتاج المواد المختلفة إلى نظام قطع مختلف، توفر شركة Kerke جميع أنواع أنظمة القطع، فيما يلي شرح لها…
Related requirements
In the production of PP masterbatch (polypropylene masterbatch), the extruder needs to meet various requirements such as plasticization, mixing, and temperature control to ensure product quality and production efficiency. Specifically, as follows:
Good plasticizing ability
Screw design: PP belongs to crystalline polymers with a high melting point, requiring the screw to provide sufficient shear force and heat to achieve good plasticization. Usually, a mutation type screw is used, which has a shorter compression section and can subject PP materials to strong shear and compression in a shorter period of time, rapidly heating and plasticizing. The aspect ratio of the screw is generally between 25-32 to ensure sufficient length for PP to fully plasticize. At the same time, the groove depth and helix angle of the screw also need to be optimized according to the characteristics of PP. Generally, the groove depth is moderate and the helix angle is large to improve plasticization efficiency.
Drive power: Due to the high energy consumption required for PP plasticization, the extruder needs to be equipped with a suitable power drive motor. For extruders with an extrusion rate of 100-500 kilograms per hour, the driving power is usually around 30-110 kilowatts to ensure stable rotation of the screw, overcome material resistance, and achieve good plasticizing effect.
Efficient mixing and dispersion performance
Mixing element: In order to evenly mix various additives (such as colorants, antioxidants, lubricants, etc.) in PP masterbatch with PP matrix, efficient mixing elements should be installed on the extruder screw. For example, using barrier type screws or screws with mixing pins can increase the turbulence level of materials and improve the mixing effect. At the same time, multiple kneading blocks are set on the screw, and the combination of kneading blocks at different angles and arrangements is used to achieve multiple shearing and mixing of the material, so that the additive can be uniformly dispersed in PP.
Strengthening measures: For some additives that are difficult to disperse, such as nanoscale fillers, the extruder can be equipped with a static mixer. The static mixer is installed inside the barrel or in front of the head of the extruder, which can further enhance the mixing and dispersion effect during the material flow process, ensuring that the additive forms a stable and uniform system in the PP masterbatch.
Accurate temperature control
Temperature control system: During the production process of PP masterbatch, temperature has a significant impact on product quality. The extruder needs to be equipped with a high-precision temperature control system, generally using electric heating or thermal oil heating methods, and monitoring the temperature of each heating section in real time through temperature sensors such as thermocouples or thermal resistors. The temperature control accuracy should be within ± 1 ℃ to ensure that PP is in the appropriate temperature range during melting, mixing, and extrusion processes, and to avoid product performance degradation caused by temperature fluctuations, such as embrittlement and discoloration.
Cooling system: After PP masterbatch extrusion, it is necessary to quickly reduce the temperature through a cooling device to prevent masterbatch adhesion and deformation. Extruders are usually equipped with air or water cooling systems to cool the head and extruded masterbatch. The air-cooled system uses a fan to force air flow to remove heat, while the water-cooled system uses circulating water for cooling. The cooling rate can be adjusted according to production speed and masterbatch specifications.
Stable pressure control
Extrusion pressure: Stable extrusion pressure is a key factor in ensuring the uniformity of PP masterbatch size and appearance quality. The hydraulic system or mechanical transmission system of the extruder should be able to provide stable pressure output, with pressure fluctuations generally controlled within ± 3%. Stable pressure can maintain a uniform flow rate of the material during extrusion, thereby producing PP masterbatch with high precision in diameter and length.
Adjustment device: In order to adapt to different production processes and product requirements, extruders should have flexible pressure adjustment devices. Operators can accurately adjust the extrusion pressure by adjusting the back pressure of the screw, changing the pressure parameters of the hydraulic system, or adjusting the throttle device of the machine head. For example, in the production of PP masterbatch with different properties, by adjusting the extrusion pressure reasonably, the flowability and molding effect of the material can be optimized, and the quality and performance of the product can be improved.
Reliable material transportation
Accurate feeding: The production of PP masterbatch requires precise control of the amount of various materials added, so the feeding device of the extruder should use high-precision feeding equipment. Common weight loss feeders can accurately transport PP raw materials, additives, and other materials to the extruder according to the set amount of material added. At the same time, the feeder should have good sealing and stability to prevent material leakage and uneven feeding, ensuring accurate proportioning of materials during the production process.
Screw conveying accuracy: The machining accuracy and assembly quality of screws have a significant impact on the stability of material conveying. The pitch and diameter tolerances of the screw should be controlled within a small range, generally with a pitch tolerance of no more than ± 0.05 millimeters and a diameter tolerance of no more than ± 0.03 millimeters, to ensure that the material can be stably conveyed forward in the screw groove and avoid material retention or fluctuation. In addition, the gap between the screw and the barrel should be uniform and consistent. If the gap is too large, it can easily cause material reflux and affect conveying efficiency; If the gap is too small, it may cause excessive material shearing and screw wear.
Corrosion resistance and wear resistance
Corrosion resistant materials: Although PP itself has good resistance to most chemicals, some corrosive additives may be used in the production process. Therefore, components such as the barrel and screw of the extruder that come into contact with the material need to be made of corrosion-resistant materials. The barrel is usually protected by lining with stainless steel or spraying a corrosion-resistant coating, while the screw can be made of alloy steel with good corrosion resistance and surface treated, such as hard chromium plating or electroless nickel plating, to improve its corrosion resistance and extend the service life of the equipment.
Wear resistant design: In the production process of PP masterbatch, there will be certain friction between the material and the screw and barrel, especially in the case of high-speed extrusion or adding fillers, the wear is more obvious. In order to improve the wear resistance of the equipment, the surface of the screw and barrel should have high hardness and wear resistance. In addition to selecting suitable materials, special heat treatments such as quenching and tempering can also be applied to the screw and barrel to improve their surface hardness. In addition, wear-resistant liners can be installed in the feeding section and easily worn parts of the barrel for regular replacement and to reduce equipment maintenance costs.
Automated Control and Monitoring
Control system: Modern PP masterbatch production extruders are usually equipped with advanced automation control systems, such as PLC (Programmable Logic Controller) or DCS (Distributed Control System). These systems can achieve real-time monitoring and precise control of parameters such as temperature, pressure, screw speed, and material flow rate of the extruder. Operators can easily set and adjust production parameters through the human-machine interface (HMI), monitor and manage the production process, and improve production efficiency and product quality stability.
Fault diagnosis and warning: The automation control system should also have fault diagnosis and warning functions. The system can monitor the operating status of equipment in real time. When abnormal situations occur, such as high temperature, abnormal pressure, motor overload, etc., it can promptly issue alarm signals and automatically take corresponding protective measures, such as stopping the machine or reducing production speed. At the same time, the system can also record fault information to help maintenance personnel quickly locate and troubleshoot faults, reduce equipment downtime, and improve production continuity and reliability.
التطبيقات
PP masterbatch, also known as polypropylene masterbatch, is widely used in plastic products, fiber products, and other industries. The following is a specific introduction:
Plastic products industry
Injection molded products: Adding an appropriate amount of PP masterbatch in the production of injection molded products such as plastic buckets, plastic pots, and plastic toys can improve the processing performance of polypropylene, enhance the surface smoothness, hardness, and strength of the products. For example, adding filler masterbatch to PP plastic buckets not only reduces costs, but also has better rigidity and stability.
Blow molded products: When producing blow molded products such as plastic films, plastic bags, and plastic bottles, PP masterbatch can be used to adjust the melt flow and mechanical properties of polypropylene. Adding anti-aging masterbatch during the production of agricultural film can improve its weather resistance and extend its service life; Adding smooth masterbatch can reduce the friction coefficient of the film surface, making it easier to process and use.
Extrusion products: In the extrusion production of PP pipes and sheets, adding PP masterbatch can improve the extrusion stability of materials and the quality of products. For example, adding anti-static masterbatch can give PP sheets anti-static properties, prevent dust adsorption, improve product cleanliness, and is commonly used in fields such as electronic device packaging.
Fiber products industry
In the field of clothing, when producing PP fibers for clothing fabrics, color masterbatch can be added to give the fibers various colors without the need for post dyeing, reducing environmental pollution and costs during the dyeing process. At the same time, adding antibacterial masterbatch can endow fibers with antibacterial properties, inhibit bacterial growth, maintain clothing hygiene and cleanliness, and are commonly used in sports clothing and underwear fields.
In the field of home textiles, the use of PP masterbatch can improve the performance of fibers in the production of home textile products such as bedding and curtains. For example, adding soft masterbatch can make PP fibers softer and more comfortable, improving the user experience of home textile products; Adding flame-retardant masterbatch can improve the fire safety of home textile products and reduce fire hazards.
Industrial fibers: PP masterbatch also plays an important role in the production of industrial fibers such as geotextiles, ropes, and filter materials. For example, adding reinforcing masterbatch can improve the tensile strength and tear resistance of geotextiles, enabling them to better withstand soil pressure and external forces; Adding anti-aging masterbatch can improve the service life of ropes in outdoor environments, ensuring their safety and reliability.
Other industries
Automotive industry: Many automotive interior parts such as instrument panels, seats, door panels, etc. are made of PP material, which can meet different performance requirements by adding various PP masterbatch. For example, adding toughening masterbatch can improve the impact resistance of PP materials, making automotive interior parts less prone to breakage when impacted; Adding scratch resistant masterbatch can improve the hardness and wear resistance of interior parts, reduce scratches generated during daily use, and maintain aesthetics.
Wire and cable: PP material is commonly used for the insulation layer and sheath of wire and cable, and adding PP masterbatch can improve its performance. For example, adding low smoke halogen-free flame retardant masterbatch can make PP materials have good flame retardant properties, reduce the production of smoke and toxic gases in the event of a fire, and improve the safety of wires and cables; Adding weather resistant masterbatch can improve the aging resistance of PP materials in outdoor environments and extend the service life of wires and cables.
Medical industry: PP masterbatch is also used in the production of medical supplies such as syringes, infusion sets, medical packaging, etc. For example, adding antibacterial masterbatch can give PP products antibacterial function, prevent bacteria from breeding on the surface of the product, and reduce the risk of infection; Adding transparent masterbatch can improve the transparency of PP material, allowing medical supplies to be clearly observed for internal conditions.