FKM masterbatch is a granular product made from fluororubber (FKM) resin as a carrier, with the addition of pigments, dispersants, and other additives. Fluororubber (FKM) is an elastic material made by copolymerizing monomers such as vinylidene fluoride (VDF), chlorotrifluoroethylene (CTFE), and tetrafluoroethylene (TFE), which has excellent chemical resistance, temperature resistance, and mechanical properties. FKM masterbatch is made into granular products by mixing these fluororubber resins with specific proportions of pigments, dispersants, and other additives through processes such as melt extrusion, achieving color customization and functional modification. It is widely used in high-end manufacturing fields.
Characteristic
Chemical resistance
Almost insoluble in any organic solvent, resistant to strong acids, alkalis, oils, and corrosive chemicals, suitable for harsh environments such as chemical, petroleum, aerospace, etc.
Temperature resistance
The long-term temperature range is -20 ℃ to 200 ℃, and the short-term temperature resistance can reach 250 ℃, meeting the requirements of extreme temperature scenarios.
Mechanical properties
It has high strength, high toughness, good resistance to compression deformation and wear resistance, and is suitable for dynamic sealing and wear-resistant components.
Weather resistance
Resistant to ozone and ultraviolet radiation, suitable for long-term outdoor use.
Electrical performance
Has excellent insulation performance and arc resistance, suitable for high voltage and high frequency electric field environments.
Processability
Excellent fluidity, capable of forming complex shapes through processes such as molding, extrusion, injection molding, etc., with minimal performance loss during processing.
Environmental Protection and Safety
Compliant with ROHS standards, free of heavy metals such as cadmium, lead, chromium, etc., it can be used for food contact grade applications (such as medical device components).
Types
FKM masterbatch, also known as fluororubber masterbatch, can be classified into the following types based on their monomer composition and structure:
The binary copolymer of hexafluoropropylene and vinylidene fluoride: commonly known as Type 2 rubber in China, Type 26 fluororubber is of this type and is currently the most commonly used fluororubber variety, accounting for over 80% of the total fluororubber usage.
The ternary copolymer of tetrafluoroethylene, hexafluoropropylene, and vinylidene fluoride: the 246 type fluororubber commonly known as No. 3 rubber in China belongs to this category.
Terpolymer of tetrafluoroethylene, fluorinated vinyl ether, and vinylidene fluoride: with unique properties, it can be used in some special requirements.
Tetrafluoroethylene, propylene, and vinylidene fluoride ternary copolymer: This FKM has increased resistance to alkaline and polar solutions, but its expansion performance has deteriorated, with a fluorine element mass fraction of about 67%.
Pentacopolymer of tetrafluoroethylene, hexafluoropropene, ethylene, fluorinated vinyl ether, and vinylidene fluoride: renowned for its resistance to polar solutions and high-temperature hydrogen sulfide.
نسبة الصيغة
The formula ratio of FKM masterbatch may vary depending on specific application requirements, performance requirements, and production processes. Here is an example of a common FKM masterbatch formula ratio:
Basic formula
Fluororubber (FKM): 60-80 parts
It is the main component of the masterbatch, providing properties such as heat resistance, oil resistance, and chemical corrosion resistance. The selection of different types of fluororubber (such as 26 type, 246 type, etc.) in the formula depends on the specific performance requirements of the product.
Reinforcing filler: 10-30 parts
Commonly used ones include carbon black, white carbon black, etc. Carbon black can improve the strength, wear resistance, and conductivity of rubber; White carbon black can improve the hardness, transparency, and aging resistance of rubber. For example, N330 carbon black is often used in some formulations, with a dosage generally around 15-25 parts.
Plasticizer: 5-15 parts
Examples such as dioctyl phthalate (DOP) and dioctyl sebacate (DOS) can improve the processing performance and flexibility of rubber, reduce its hardness and viscosity, and make rubber easier to form during processing.
Vulcanizing agent: 1-5 parts
Commonly used vulcanizing agents include diisopropylbenzene peroxide (DCP), bisphenol AF, etc. The function of vulcanizing agents is to cause crosslinking reactions of fluororubber molecules, forming a three-dimensional network structure, thereby improving the mechanical and heat resistance properties of rubber. For example, in some formulations, the dosage of DCP is usually controlled at 1-3 parts.
Sulfurizing agent: 0.5-2 parts
Examples such as triallyl isocyanurate (TAIC) and N, N-meta phenylene bismaleimide (HVA-2) can improve vulcanization efficiency and enhance the properties of vulcanized rubber.
Other additives (added as needed)
Antioxidant: 0.5-2 parts
Examples such as 2-mercaptobenzimidazole (MB) and 4-methyl-2,6-di-tert-butylphenol (264) can prevent performance degradation of rubber due to oxidation, thermal aging, and other factors during long-term use, thereby extending the service life of rubber products.
Lubricant: 0.5-2 parts
Stearic acid, paraffin, and other lubricants can be used to reduce the friction between rubber and processing equipment during the processing, improve processing efficiency, and enhance the surface quality of products.
Coloring agent: appropriate amount
Add an appropriate amount of pigment or dye according to the appearance requirements of the product to give FKM masterbatch a specific color.
It should be noted that the above formula ratios are for reference only. In actual production, adjustments and optimizations need to be made based on specific product performance requirements, processing techniques, and the characteristics of raw materials. For example, if it is necessary to improve the low-temperature resistance of the masterbatch, the amount of plasticizer can be appropriately increased; If high requirements are placed on the aging resistance of the product, it is necessary to adjust the type and dosage of anti-aging agents. At the same time, there may be differences in the performance of raw materials produced by different manufacturers, which also need to be considered in formula design.
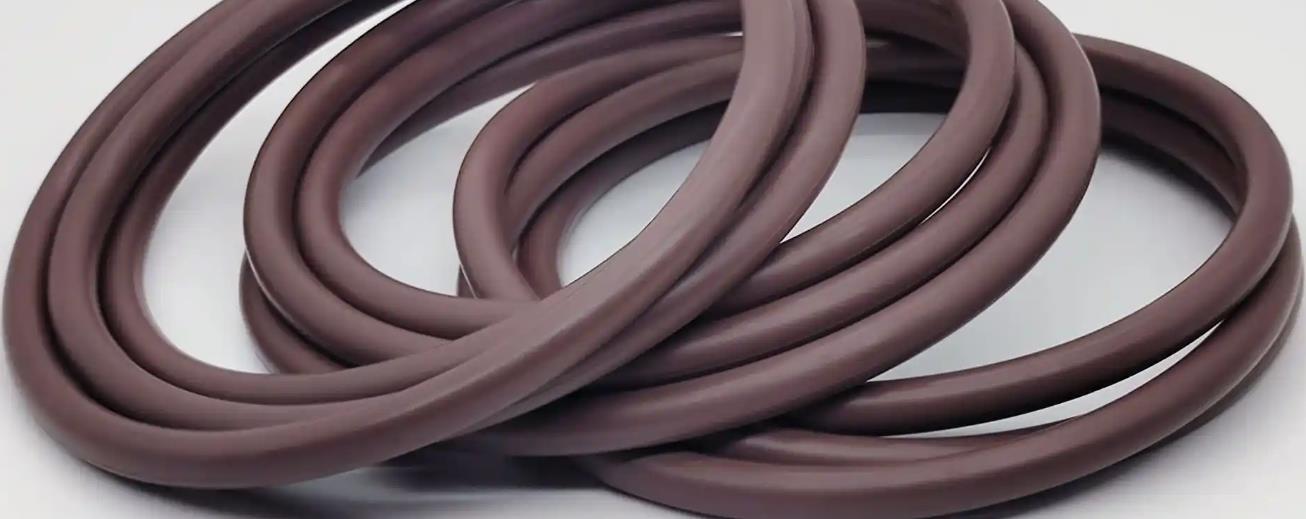
عملية الإنتاج
The production process of FKM masterbatch usually includes multiple steps such as raw material preparation, mixing, processing and molding, vulcanization, etc. The following are its specific production processes:
1. تحضير المواد الخام
Choose the appropriate fluororubber: Select different types of fluororubber based on product performance requirements, such as 26 type, 246 type, etc. Fluororubber should have good purity and performance stability.
Prepare other additives: Accurately weigh reinforcing fillers, plasticizers, vulcanizing agents, vulcanizing aids, anti-aging agents, lubricants, coloring agents, and other additives according to the formula requirements. Ensure that the quality of additives meets the requirements and is free of impurities.
2. الخلط
Initial mixing: Put fluororubber into an open or internal mixer for initial plasticization to achieve a certain degree of plasticity. Then, add plasticizers, lubricants, etc. in the order of the formula to evenly disperse them in the fluororubber.
Add reinforcing fillers and other additives: On the basis of initial mixing, add reinforcing fillers, anti-aging agents, coloring agents, etc., and continue to mix to ensure that various additives are fully and evenly mixed with fluororubber. During the mixing process, it is necessary to control parameters such as temperature, time, and speed. Generally, the mixing temperature is around 100-150 ℃ and the mixing time is 10-30 minutes.
Final mixing: At the end of the mixing process, add sulfurizing agent and sulfurizing aid to achieve uniform mixing. Due to the easy decomposition and failure of sulfurizing agents at high temperatures, the temperature during final mixing should be appropriately lowered, generally controlled at around 60-80 ℃.
3. Processing and molding
Extrusion molding: The mixed rubber material is put into an extruder, and the extruder’s screw rotation and heating device are used to extrude the rubber material from the machine head at a certain temperature and pressure, forming the desired shape and size of masterbatch. The extrusion temperature is generally controlled at around 120-180 ℃, and adjusted according to different fluororubber varieties and formulas.
Injection molding: For some masterbatch products with complex shapes and high precision requirements, injection molding technology can be used. Add the mixed rubber material into the material cylinder of the injection molding machine, heat and plasticize it, and inject it into the mold at a certain pressure and speed. After cooling and forming, the masterbatch product is obtained. The injection temperature is generally around 150-200 ℃, and parameters such as injection pressure and holding time are adjusted according to the specific requirements of the product.
4. Sulfurization
One stage vulcanization: Place the processed masterbatch into a vulcanization tank or flat vulcanizing machine, and perform a stage of vulcanization at a certain temperature and pressure. The vulcanization temperature is generally around 150-180 ℃, the vulcanization pressure is 10-20MPa, and the vulcanization time varies depending on the thickness of the masterbatch and the formula, usually 10-60 minutes.
Secondary vulcanization: The masterbatch after primary vulcanization usually needs to undergo secondary vulcanization to further improve its performance. Secondary vulcanization is generally carried out in an oven, with a temperature controlled at around 200-250 ℃ and a vulcanization time of 2-24 hours. Secondary vulcanization can improve the cross-linking structure of fluororubber, enhance its heat resistance, aging resistance, and mechanical properties.
5. Quality inspection
Appearance inspection: Check whether the appearance of the masterbatch is smooth, free of bubbles, impurities, cracks, and other defects, and whether the color is uniform and consistent.
Size measurement: Use measuring tools to measure the size of the masterbatch to ensure that it meets the product specifications.
Performance testing: Conduct mechanical performance tests on the masterbatch, such as tensile strength, elongation at break, hardness, etc; Heat resistance testing, such as thermal aging test, high temperature tensile test, etc; Oil resistance testing, such as immersion tests in different oil media; And electrical performance testing, etc., to evaluate whether the quality and performance of the masterbatch meet the requirements for use.
6. Packaging and storage
Packaging FKM masterbatch that has passed the inspection according to certain specifications and quantities, usually using plastic film bags or aluminum foil bags to prevent moisture, oxidation, and contamination of the masterbatch. The packaged masterbatch should be stored in a dry, ventilated, and cool environment in the warehouse, avoiding direct sunlight and high temperatures.
معدات الإنتاج
The FKM masterbatch production equipment is mainly used for raw material processing, mixing, molding, vulcanization and other processes. The following are the main equipment required for each process:
1. معدات معالجة المواد الخام
Rubber cutting machine: used to cut large pieces of fluororubber raw materials into small pieces suitable for processing, facilitating subsequent plasticizing and mixing operations. It usually consists of a frame, a rubber cutter, a transmission device, and a control system. The cutting edge of the rubber cutter is sharp and can quickly and accurately cut rubber.
Powder measuring equipment: such as electronic scales, measuring buckets, etc., used for accurately weighing powdered additives such as reinforcing fillers, vulcanizing agents, anti-aging agents, etc. Electronic scales have functions such as high precision, fast weighing, and digital display, while measuring buckets can quantitatively mix ingredients according to different formula requirements to ensure accurate addition of additives.
2. المعدات الهجينة
Internal mixer: It is a commonly used mixing equipment in FKM masterbatch production, which consists of an internal mixing chamber, rotor, pressure weight, discharge device, and other parts. In the mixing chamber, the rotor rotates relative to each other at different speeds, allowing the fluororubber and various additives to mix evenly under high temperature, high pressure, and strong shear force. The internal mixer has the advantages of high mixing efficiency, good mixing quality, and automatic control, which can effectively improve production efficiency and product quality.
Open mill: It mainly consists of two parallel rollers, and the gap between the rollers can be adjusted. By rotating the roller, fluororubber and additives are mixed and plasticized on the surface of the roller. The open mill is flexible in operation, easy to observe and control the mixing process, and is commonly used for small-scale production or preliminary processing of rubber materials.
3. Processing and molding equipment
Extruder: composed of screw, barrel, head, transmission device, heating and cooling system, etc. The screw rotates inside the barrel, pushing the mixed rubber material forward. At the same time, the rubber material is plasticized at a certain temperature through a heating device, and then extruded from the machine head to form masterbatch of the desired shape and size. The extruder has the advantages of high production efficiency, high product size accuracy, and continuous production, and is a commonly used molding equipment in FKM masterbatch production.
Injection molding machine: mainly composed of injection device, mold clamping device, hydraulic system, and electrical control system. After the injection device heats and plasticizes the rubber material, it is injected into the mold cavity through the injection cylinder. The mold closing device provides sufficient locking force to keep the mold closed during the injection process. Injection molding machines are suitable for producing FKM masterbatch products with complex shapes and high precision requirements.
4. Sulfurization equipment
Flat vulcanizing machine: composed of heated flat plate, mold, hydraulic system, and control system. Place the formed masterbatch into the mold, heat the mold with a heating plate, and apply pressure using a hydraulic system to allow the masterbatch to undergo vulcanization reaction at a certain temperature and pressure. The flat vulcanizing machine has the advantages of high vulcanization pressure, uniform temperature, and good product quality, and is commonly used to produce FKM masterbatch products with large thickness and small area.
Vulcanization tank: It is a large vulcanization equipment, usually a cylindrical tank body, equipped with heating devices and ventilation systems inside. Place the formed masterbatch into a vulcanization tank and heat and sulfurize it by introducing steam or other heating media. The vulcanization tank is suitable for mass production of FKM masterbatch products of various shapes and sizes, with advantages such as high production efficiency and good vulcanization uniformity.
5. Quality inspection equipment
Tensile testing machine: used to test the mechanical performance indicators such as tensile strength and elongation at break of FKM masterbatch. It applies tensile force to the specimen and measures the stress-strain curve of the specimen during the tensile process, thereby obtaining the mechanical property data of the material.
Hardness tester: used to measure the hardness of FKM masterbatch. Common hardness testers include Shore hardness tester, Rockwell hardness tester, etc. Choose the appropriate hardness tester based on the hardness range of FKM masterbatch for measurement.
Thermal aging test chamber: used to simulate the aging process of FKM masterbatch under high temperature environment and evaluate its heat resistance performance. Place the sample in the test chamber, conduct aging tests under certain temperature and time conditions, and then observe and test the performance changes of the sample.
Oil bath test device: used to test the oil resistance of FKM masterbatch. Soak the sample in different oil media and observe the weight, volume, and mechanical properties changes of the sample under certain temperature and time conditions to evaluate its oil resistance performance.
6. Packaging equipment
Automatic packaging machine: used for packaging the produced FKM masterbatch. It can automatically complete packaging processes such as measurement, filling, and sealing, improving packaging efficiency and quality. Automatic packaging machines usually use electronic measuring devices, which can accurately control the weight of packaging, and have multiple packaging forms to choose from, such as bagged, boxed, etc.
Sealing machine: For some situations that require manual bagging, the sealing machine is used to seal the packaging bag. Common sealing machines include heat sealing machines, pulse sealing machines, etc. Choose the appropriate sealing machine according to the different packaging materials for sealing operations to ensure good sealing of the packaging bag.
FKM masterbatch extruder
Kerke’s masterbatch extruder can be used to produce FKM masterbatch. Our FKM masterbatch extruder has multiple models to choose from, which can meet different production requirements.
-
آلة البثق اللولبية المزدوجة للمختبر
متى ستحتاج إلى آلة بثق ثنائية اللولب للمختبر؟ إذا كنت ترغب في إجراء تجارب واختبارات...
-
آلة البثق ذات اللولب المزدوج المتوازي
تم تصميم آلة البثق ذات المسمار المزدوج ذات الدوران المتوازي لدينا لتصنيع المركبات والدفعات الرئيسية مع سعة إنتاج تتراوح من...
-
طارد ثلاثي (3 براغي)
آلة البثق ثلاثية البراغي هي تقنية جديدة ذات مزايا عديدة. تُستخدم آلة البثق ثلاثية البراغي بشكل رئيسي...
-
نظام البثق ثنائي المرحلة
تم تصميم نظام بثق الأم والطفل للمواد الخاصة التي لا يمكن معالجتها على مرحلة واحدة من البثق، المرحلة الأولى...
-
خط تصنيع العجنات في بانبوري
تم تصميم آلة العجن والبثق الخاصة بنا لصنع تطبيقات خاصة بسعة إنتاج تتراوح من 30 كجم / ساعة إلى 1000 كجم / ساعة.
-
نظام القطع / نظام التكوير
تحتاج المواد المختلفة إلى نظام قطع مختلف، توفر شركة Kerke جميع أنواع أنظمة القطع، فيما يلي شرح لها…
Related requirements
The extruder plays a key role in the production of FKM masterbatch, and the following are some requirements for the extruder:
1. Screw design
High shear capacity: FKM (fluororubber) has high viscosity and strength, requiring the screw to provide sufficient shear force to fully mix and plasticize it. Therefore, screws are usually designed with a large aspect ratio, typically between 20-30, to increase the residence time and shear action of materials in the screw.
Special thread structure: In order to better adapt to the production of FKM masterbatch, the thread structure of the screw also has special requirements. For example, using a gradient screw, the depth of the screw groove gradually becomes shallower from the feeding section to the homogenization section, which can gradually compress and shear the material during the extrusion process, facilitating the plasticization and mixing of the material. At the same time, a mixing section is set at the head of the screw, which usually uses structures such as pins and barriers to further enhance the mixing effect of the material and make the performance of FKM masterbatch more uniform and stable.
2. Drive power
Due to the high viscosity of FKM material, the extruder requires a high-power drive motor. Generally speaking, the driving power of the extruder for producing FKM masterbatch varies depending on the specifications and production capacity of the extruder, usually ranging from tens of kilowatts to hundreds of kilowatts. Sufficient driving power can ensure that the screw can overcome the resistance of the material during high-speed rotation, achieve a stable extrusion process, and avoid situations where the screw speed decreases or the material extrusion is not smooth due to insufficient power.
3. Heating and cooling system
Accurate temperature control: The production of FKM masterbatch has strict temperature requirements and requires precise control of the material temperature during the extrusion process. The heating system of extruders usually adopts electric heating or thermal oil heating methods. The heating elements are evenly distributed on the barrel, which can quickly heat the materials inside the barrel to the desired temperature. At the same time, it is equipped with an efficient cooling system, such as circulating water cooling or air cooling devices, to provide timely cooling when the temperature is too high, ensuring the stability of the material temperature. Generally speaking, the temperature control accuracy during FKM masterbatch extrusion process is required to be within ± 2 ℃.
Multi stage temperature control: In order to better adapt to the characteristics of materials in different extrusion stages, extruders usually adopt a multi-stage temperature control method. For example, in the feeding section, the temperature is relatively low, generally controlled at 50-80 ℃, to prevent premature softening of the material and affect the feeding effect; In the compression and homogenization sections, the temperature gradually increases, usually controlled at around 150-200 ℃, to fully plasticize and mix the material; At the head of the machine, the temperature can be appropriately reduced and controlled at 130-160 ℃ to ensure that the extruded masterbatch has a good molding effect.
4. Head design
Reasonable channel design: The channel design of the machine head should ensure that the material can be evenly extruded, avoiding uneven flow velocity or material retention. Usually, a streamlined flow channel design is adopted to reduce dead corners and sudden changes in the channel, allowing materials to flow smoothly in the channel, thereby ensuring the dimensional accuracy and appearance quality of the extruded FKM masterbatch. For example, for masterbatch with a circular cross-section, the outlet of the head flow channel will be designed as a gradually changing circle, allowing the material to naturally form a circular cross-section during extrusion and controlling the size deviation within a small range.
Easy to replace mold head: In order to meet the production needs of FKM masterbatch with different specifications and shapes, the machine head should be designed with a structure that is easy to replace the mold head. This allows for quick replacement of different molds according to production requirements, achieving diversified product production. At the same time, the installation and disassembly of the die head should be convenient and fast, and ensure the accuracy of the fit with the die head during the installation process, ensuring stable quality of the extruded masterbatch.
5. Measurement accuracy
High precision measurement: In the production of FKM masterbatch, precise control of material extrusion is required to ensure product quality and stable performance. Extruders are usually equipped with high-precision measuring devices, such as gear pump measuring systems or screw measuring systems. These measuring devices can accurately measure and control the flow rate of materials, with a measurement accuracy of within ± 1%. By precisely controlling the extrusion amount of materials, it can be ensured that each batch of FKM masterbatch has good consistency in quality and performance.
6. Automation control
Advanced control system: Modern extruders typically use advanced automation control systems, such as PLC (Programmable Logic Controller) or DCS (Distributed Control System). These control systems can achieve real-time monitoring and control of parameters such as temperature, pressure, speed, and material flow of the extruder. Operators can set and adjust various parameters through touch screens or computer interfaces, and the system has fault alarm and automatic protection functions, which can timely detect and handle abnormal situations in the production process, ensuring the safe and stable operation of the extruder. Meanwhile, the automation control system can also record production data, facilitating production management and quality traceability.
طلب
FKM masterbatch, also known as fluororubber masterbatch, has excellent properties such as high temperature resistance, oil resistance, and chemical corrosion resistance. Therefore, it has a wide range of applications in multiple fields. The following are some of the main application aspects:
Automotive industry
Seals: The temperature inside the engine compartment of a car is high and there are various lubricants, fuels, and other media present. Seals made of FKM masterbatch, such as oil seals, O-rings, gaskets, etc., can maintain good sealing performance in high temperature and oil environment, prevent oil leakage, and ensure the normal operation of engine and other components.
Rubber hose: used for fuel pipes, cooling water pipes, etc. in automobiles. FKM masterbatch endows rubber hoses with good oil resistance and high temperature resistance, which can withstand the erosion of fuel and the high temperature environment inside the engine compartment, ensuring that rubber hoses will not age or crack during long-term use, and improving the safety and reliability of automobiles.
Aerospace field
Sealing materials: Aircraft engines, hydraulic systems, and other parts need to withstand extreme high temperature and pressure environments. Sealing materials made of FKM masterbatch have excellent resistance to high temperature, high pressure, and chemical corrosion, which can meet the high reliability requirements of seals in the aerospace industry and ensure the safe operation of critical systems in aircraft.
Fuel system components: FKM masterbatch can be used to manufacture seals and gaskets for fuel pumps, fuel filters, and other components in aircraft fuel systems. It can withstand the erosion of aviation fuel, ensure the sealing and stability of the fuel system, and prevent safety accidents such as fuel leaks.
Petrochemical industry
Pipeline sealing: In the petrochemical production process, pipelines transporting various oils and chemical raw materials require reliable sealing. FKM masterbatch made seals can maintain good sealing performance in harsh chemical environments and high temperature conditions, prevent pipeline leakage, and ensure the safety and stability of the production process.
Reactor lining: FKM masterbatch can be used to make lining materials in chemical reactors, which can resist corrosion from various chemicals, protect the inner wall of the reactor, extend the service life of the reactor, and ensure the safety of the reaction process and product quality.
Electronic enterprises
Wire and cable: FKM masterbatch can be used to manufacture the insulation layer and sheath of wire and cable, with good high temperature resistance, aging resistance, and chemical corrosion resistance, which can protect the normal operation of wire and cable under harsh environmental conditions, improve the service life and safety of wire and cable.
Electronic component sealing: In the packaging of some electronic components, such as semiconductor devices, sensors, etc., FKM masterbatch made seals can provide good sealing protection, prevent external moisture, dust, and chemical substances from corroding electronic components, and ensure the stable and reliable performance of electronic components.
مناطق أخرى
Medical devices: In some medical device components that require contact with human blood, body fluids, or chemical drugs, such as infusion tubes, syringe seals, etc., FKM masterbatch has good biocompatibility and chemical corrosion resistance, which can ensure the safety and reliability of medical devices.
Construction industry: FKM masterbatch can improve the weather resistance, water resistance, and chemical corrosion resistance of materials such as building sealants and waterproofing membranes, prolong the service life of building materials, and enhance the waterproof and sealing performance of buildings.