PS masterbatch is a granular product made by processing polystyrene (PS) resin as a carrier, adding various pigments, additives, etc.
يكتب
There are various types of PS masterbatch, and the following are some common classifications and specific types:
Classification by function
ماستر باتش التلوين
Colored masterbatch: This is the most common type of colored masterbatch, which can make PS products present various bright colors such as red, yellow, blue, green, etc. by adding pigments or dyes of different colors. Widely used in daily necessities, toys, home appliance shells and other fields to meet the appearance color requirements of different products.
White masterbatch: mainly used for producing white PS products, such as white plastic cups, white household appliance shells, etc. Usually added with white pigments such as titanium dioxide, it has high coverage and good whiteness.
Black masterbatch: used to dye PS resin black, it is widely used in the outer shell of electronic and electrical products, insulation layer of wires and cables, and other aspects. The carbon black in black masterbatch not only provides a black appearance, but also enhances the weather resistance and UV resistance of the product.
ماسترباتش وظيفي
Flame retardant masterbatch: Adding flame retardants to PS masterbatch can improve the flame retardant performance of PS products, making them less prone to combustion or delaying the combustion rate when exposed to open flames. Commonly used in fields with high requirements for fire safety, such as electronic appliances, buildings, etc., such as TV casings, building insulation materials, etc.
Anti static masterbatch: Adding anti-static agents can reduce the surface resistance of PS products, making them less prone to static electricity accumulation. Suitable for fields such as electronic component packaging and optical instrument packaging that are sensitive to static electricity, to prevent damage to products caused by static electricity.
Antibacterial masterbatch: Contains antibacterial agents that can inhibit the growth and reproduction of bacteria, molds, and other microorganisms, maintaining the hygiene and cleanliness of PS products. Commonly used in medical devices, food packaging, daily necessities and other fields, such as medical syringes, food preservation boxes, children’s toys, etc.
Weathering masterbatch: Added with UV absorbers, antioxidants and other additives, it can improve the aging resistance of PS products in outdoor environments, prevent discoloration, brittleness, cracking and other phenomena caused by long-term exposure to natural environments such as sunlight and wind and rain. Commonly used in fields such as building door and window profiles, outdoor billboards, automotive components, etc.
Function
Universal masterbatch: suitable for the production of general PS products, such as ordinary plastic containers, stationery, hangers, etc. This type of masterbatch can meet basic usage requirements in terms of performance, and has good processing performance and physical and mechanical properties.
Specialized masterbatch
Food packaging masterbatch: designed for the special requirements of food packaging, with good hygiene performance, in compliance with relevant food safety standards, and strict restrictions on the use of additives to ensure no contamination of food.
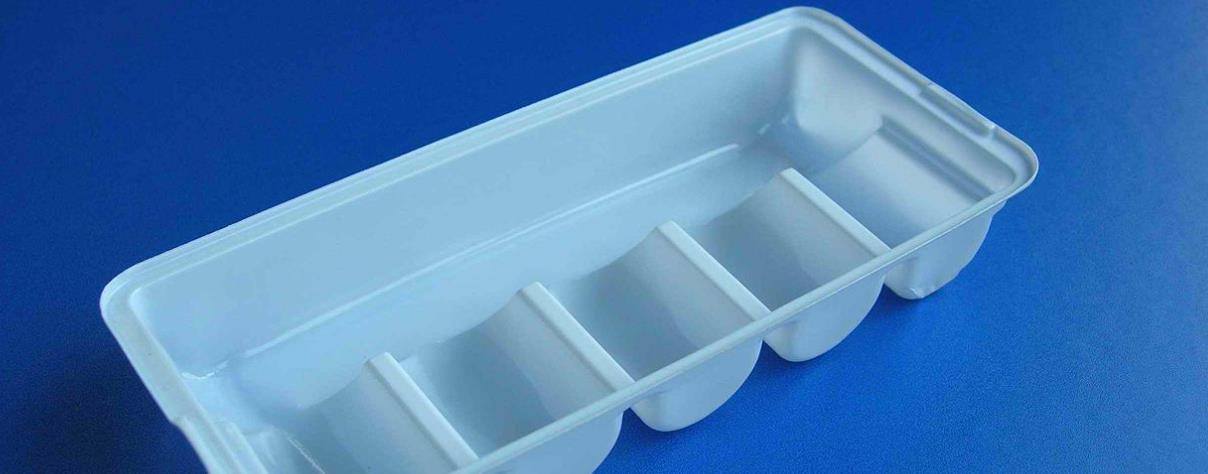
Masterbatch for electronic and electrical appliances: It has high requirements in terms of electrical insulation performance, flame retardancy, impact resistance, etc., to meet the safety and performance requirements of electronic and electrical products, such as used in the production of computer cases, mobile phone charger shells, etc.
Optical grade masterbatch: characterized by high transparency, low birefringence, and good optical uniformity, it is mainly used in the manufacturing of optical lenses, optical discs, display screens, and other products that require high optical performance.
Classified by added ingredients
Inorganic additive masterbatch
Filling masterbatch: Inorganic fillers such as calcium carbonate, talc powder, and kaolin are added to reduce the cost of PS products, while also improving their hardness, rigidity, and dimensional stability. However, excessive filling may lead to a decrease in the toughness and transparency of the product.
Enhanced masterbatch: Adding reinforcing materials such as glass fiber and carbon fiber can significantly improve the strength, modulus, and heat resistance of PS products. It is commonly used in the manufacturing of products with high mechanical performance requirements, such as automotive parts and engineering plastic parts.
Organic additive masterbatch
Toughening masterbatch: Organic toughening agents such as elastomers and rubber are added to improve the toughness and impact resistance of PS products, making them less prone to breakage when subjected to external impact. Commonly used for products that require high toughness, such as plastic pipes, plastic films, etc.
Plasticizing masterbatch: Adding plasticizers such as phthalates and aliphatic diesters can reduce the melting temperature and viscosity of PS resin, improve its processing performance and flexibility, and make PS products softer and more elastic. It is commonly used in the production of soft PS plastic products, such as plastic films and synthetic leather.
Common proportioning information for different types of PS masterbatch
ماستر باتش التلوين
Color masterbatch: The general reference ratio is around 1% -5%, depending on the required color depth and product requirements. If used for general plastic products, the ratio of coloring masterbatch to PS resin may be around 1:50; For advanced plastic products, the ratio may be around 1:20.
White masterbatch: The content of titanium dioxide is usually around 40% -80%, with the rest being PS carrier resin and a small amount of additives. The addition ratio in the product is generally 2% -5%.
Black masterbatch: The carbon black content is relatively high, reaching 30% -55%, or even higher, such as some high concentration black masterbatch with a carbon black content of up to 92%. The common addition ratio of PS black masterbatch in PS resin is 2% -5%, and the specific dosage depends on the requirement for blackness.
ماسترباتش وظيفي
Flame retardant masterbatch: The addition ratio is usually between 10% and 30%, depending on the flame retardant grade required for PS products.
Anti static masterbatch: The reference ratio of HIPS specific permanent anti-static masterbatch is 15% -20%, and the reference ratio of ordinary anti-static PS masterbatch is about 3%.
Antibacterial masterbatch: The recommended dosage is generally 2% -4%, which should be directly mixed with PS plastic particles before processing.
Weathering masterbatch: The addition ratio is generally around 5% -15%, mainly determined according to the weather resistance requirements of the product’s usage environment.
Mother granules classified by purpose
Universal masterbatch: The addition ratio is usually between 2% and 10%, adjusted according to the performance requirements and cost control of the product.
Food packaging masterbatch: The general addition amount is around 2% -5%, which not only meets the hygiene requirements of food packaging, but also ensures the performance of the product.
Electronic and electrical masterbatch: For example, conductive masterbatch used in the production of PS carrier tape conductive plastic, with a reference ratio of about 25%.
Optical grade masterbatch: The addition amount is usually low, usually around 1% -3%, to ensure the optical performance of the product.
Mother granules classified by added ingredients
Inorganic additive masterbatch
Filling masterbatch: The content of inorganic fillers such as calcium carbonate and talc powder can range from 30% to 80%, with PS carrier resin accounting for 20% to 70%. The addition ratio in PS products can be adjusted between 10% and 50% according to the performance requirements of the product.
Reinforced masterbatch: The content of glass fiber and other reinforcing materials is generally around 20% -50%, with PS carrier resin accounting for 50% -80%. The proportion added to PS resin is usually 10% -30%.
Organic additive masterbatch
Toughening masterbatch: The content of toughening agents such as elastomers is generally around 10% -30%, and PS carrier resin accounts for 70% -90%. The addition amount in PS products is usually 2% -10%.
Plasticizing masterbatch: The plasticizer content can be between 20% -50%, and the PS carrier resin accounts for 50% -80%. The proportion added to PS resin is generally 5% -20%.
The above ratios are for reference only. In actual production, adjustments and optimizations need to be made based on specific product requirements, production processes, raw material properties, and other factors.
عملية الإنتاج
The production process of PS masterbatch usually includes the following key steps:
إعداد المواد الخام
Resin selection: Select suitable polystyrene (PS) resin based on product performance requirements, such as general-purpose PS, high impact PS, etc.
Additive preparation: Prepare corresponding additives according to the type and formula of the masterbatch, such as pigments, flame retardants, antistatic agents, antibacterial agents, plasticizers, etc. Ensure that the quality and purity of additives meet production requirements.
خلط المكونات
Accurate measurement: Use high-precision measuring equipment to accurately weigh PS resin and various additives according to the formula. For some masterbatch with strict requirements for addition amount, such as functional masterbatch, the measurement accuracy may be required to reach ± 0.1% or even higher.
Pre mixing: Add the weighed raw materials into a high-speed mixer for pre mixing. The speed and mixing time of the mixer need to be adjusted according to the characteristics of the raw materials and the formula. Generally, the speed is between 500-1500 revolutions per minute, and the mixing time is 5-15 minutes to ensure that the additives are evenly dispersed in the PS resin.
البثق المنصهر
Extruder setting: Add the mixed material into the twin-screw extruder. Based on the characteristics of PS resin and additives, set parameters such as temperature, screw speed, and feeding speed for each section of the extruder. Generally speaking, the temperature of the extruder is set between 160-220 ℃, the screw speed is 100-500 revolutions per minute, and the feeding speed is adjusted according to the extruder’s production capacity and formula requirements.
Melt mixing: The material is gradually melted and thoroughly mixed through heating, pressure, and screw shearing in the extruder. The additive is further uniformly dispersed in the melted PS resin to form masterbatch with specific properties. In this process, it is necessary to ensure that the material stays uniformly in the extruder to ensure the stability of the quality of the masterbatch.
Filtering and impurity removal: In order to improve the quality of the masterbatch, filtering devices such as filters and screen changers are usually installed during the extrusion process to filter out impurities and undissolved additive particles in the material, ensuring high purity of the extruded masterbatch.
التحبيب المبرد
Water cooling or air cooling: The extruded masterbatch is extruded into strips or filaments through a die, and then enters a cooling water tank or air cooling device for cooling. The water cooling method has a fast cooling speed and can quickly shape the masterbatch, but it may result in a higher surface moisture content of the masterbatch; The air cooling method has a relatively slow cooling speed, but the surface of the masterbatch is dry and the subsequent treatment is relatively simple.
Granulation: The cooled mother granules are cut into granules of a certain length by a granulator. The tool speed and cutting method of the granulator will affect the particle shape and size uniformity of the masterbatch. Generally speaking, the particle size of the masterbatch is controlled at around 2-5 millimeters to meet the requirements for subsequent processing and use.
التعبئة والتغليف والتخزين
Drying treatment: If the masterbatch absorbs a lot of moisture during the cooling process, it needs to be dried to prevent moisture from affecting the performance of the masterbatch. The drying temperature is generally between 60-80 ℃, and the drying time is 2-4 hours.
Packaging: Pack the dried masterbatch in plastic film bags or paper bags, and then pack it into cardboard boxes or woven bags. During the packaging process, attention should be paid to preventing moisture and impurities from entering the masterbatch. For some masterbatch with special requirements, such as anti-static masterbatch, it may be necessary to use anti-static packaging materials for packaging.
Storage in warehouse: Store the packaged masterbatch in a dry and ventilated warehouse, avoiding direct sunlight and high temperature environments. At the same time, the mother granules should be classified and stored, and labeled for easy management and traceability.
Throughout the entire production process, it is necessary to strictly control the process parameters of each link and regularly maintain and upkeep the equipment to ensure the production of PS masterbatch products with stable quality and reliable performance. In addition, it is necessary to conduct quality testing on the produced masterbatch, including appearance, particle size, melt flow rate, additive content, performance indicators, etc. Only masterbatch that passes the testing can enter the market for sale and use.
معدات الإنتاج
The equipment for producing PS masterbatch mainly includes the following types:
معدات الدفعات
Electronic scale: used for precise weighing of raw materials such as PS resin and additives. Its high weighing accuracy can meet the precise requirements of different formulas for raw material dosage, ensuring the stability of product quality.
High speed mixer: Mix the weighed raw materials thoroughly to ensure that the additives are initially evenly dispersed in the PS resin. By using high-speed rotating stirring blades, sufficient mixing of materials can be achieved in a short period of time, preparing for subsequent melt extrusion.
معدات البثق
Twin screw extruder: It is the core equipment for the production of PS masterbatch. It has good mixing, plasticizing, and conveying capabilities, which can fully melt and mix materials under high temperature, high pressure, and screw shear, allowing additives to be uniformly combined with PS resin. By adjusting parameters such as screw speed, temperature, and feeding speed, it is possible to adapt to different formulations and product requirements.
Single screw extruder: It is also used in the production of PS masterbatch with low mixing requirements. Its structure is relatively simple and the cost is low, but the mixing effect is not as good as that of twin-screw extruders, and it is usually used to produce simpler PS masterbatch products.
Extrusion mold: Installed at the outlet of the extruder, it determines the shape and size of the extruded masterbatch. Common molds include mouth molds with different shapes such as circular and square, which can be selected and replaced according to product requirements.
معدات التبريد
Cooling water tank: used for water-cooled cooling. When the extruded masterbatch passes through the water tank, it comes into direct contact with cooling water and quickly cools and solidifies. The length, water temperature, and water flow rate of the sink can be adjusted according to the characteristics of the masterbatch and production speed to ensure cooling effect.
Air cooling device: uses air cooling to cool the masterbatch. Blow cold air towards the extruded masterbatch through a fan, allowing it to cool naturally in the air. The air cooling device has a simple structure and is easy to operate, which can avoid the problem of residual water caused by water cooling. However, the cooling speed is relatively slow, making it suitable for the production of masterbatch with low cooling speed requirements.
معدات التحبيب
Granulator: Cut the cooled mother granules into particles of a specified length. According to the different cutting methods, it can be divided into hot cutting granulators and cold cutting granulators. The hot cutting machine is used to cut the mother granules while they are in a hot state, with fast cutting speed and regular particle shape, but the equipment is relatively complex; The cold granulator cuts after the mother granules have cooled down. The equipment is simple, but the cutting speed is slow, and the uniformity of particle size may be slightly poor.
المعدات المساعدة
Drying machine: used for drying the masterbatch to remove the moisture absorbed during the production process. Common drying machines include hot air circulation drying machines, dehumidification drying machines, etc. Suitable drying equipment can be selected according to the characteristics and drying requirements of the masterbatch.
Packaging machine: Packaging the produced masterbatch. There are automatic packaging machines and semi-automatic packaging machines, which can complete packaging processes such as measurement, filling, and sealing, improve packaging efficiency and quality, and ensure that the masterbatch is not affected by moisture or pollution during storage and transportation.
Screening equipment: Screen the mother granules after granulation to remove particles and impurities that do not meet the required size. The commonly used screening equipment includes vibrating screens, rotating screens, etc., which classify and screen the mother particles through different aperture screens to ensure the uniformity of product particle size.
PS masterbatch extruder
Kerke’s masterbatch extruder can be used to produce PS masterbatch. Our PS masterbatch extruders has multiple models to choose from, which can meet different production requirements.
-
آلة البثق اللولبية المزدوجة للمختبر
متى ستحتاج إلى آلة بثق ثنائية اللولب للمختبر؟ إذا كنت ترغب في إجراء تجارب واختبارات...
-
آلة البثق ذات اللولب المزدوج المتوازي
تم تصميم آلة البثق ذات المسمار المزدوج ذات الدوران المتوازي لدينا لتصنيع المركبات والدفعات الرئيسية مع سعة إنتاج تتراوح من...
-
طارد ثلاثي (3 براغي)
آلة البثق ثلاثية البراغي هي تقنية جديدة ذات مزايا عديدة. تُستخدم آلة البثق ثلاثية البراغي بشكل رئيسي...
-
نظام البثق ثنائي المرحلة
تم تصميم نظام بثق الأم والطفل للمواد الخاصة التي لا يمكن معالجتها على مرحلة واحدة من البثق، المرحلة الأولى...
-
خط تصنيع العجنات في بانبوري
تم تصميم آلة العجن والبثق الخاصة بنا لصنع تطبيقات خاصة بسعة إنتاج تتراوح من 30 كجم / ساعة إلى 1000 كجم / ساعة.
-
نظام القطع / نظام التكوير
تحتاج المواد المختلفة إلى نظام قطع مختلف، توفر شركة Kerke جميع أنواع أنظمة القطع، فيما يلي شرح لها…
طلب
PS masterbatch has a wide range of applications, mainly including the following aspects:
Plastic Modification
Improving mechanical properties: By adding reinforced PS masterbatch, such as glass fiber reinforced PS masterbatch, the strength, rigidity, and tensile properties of plastic products can be significantly improved. In the fields of electronic and electrical casings, automotive components, etc., this enhanced PS masterbatch is widely used to meet the structural strength requirements of products.
Improving processing performance: Some PS masterbatch can improve the processing flowability of PS resin, reduce its melt viscosity, and make it easier to form in molds. For example, when producing complex shaped plastic products, adding PS masterbatch with good processing performance can improve production efficiency and product quality, and reduce waste rates.
color
Accurate color matching: PS coloring masterbatch can achieve precise color matching, meeting the diverse color needs of different users for plastic products. Whether it is bright colors or soft solid colors, they can be achieved by selecting suitable coloring masterbatch. PS coloring masterbatch is widely used in industries such as toys, stationery, and packaging to enhance the visual appeal of products.
Color stability: PS coloring masterbatch has good color stability in plastic products and is not easily affected by environmental factors such as light, temperature, and humidity, which can cause fading or discoloration. This enables plastic products to maintain bright colors during long-term use, improving the product’s lifespan and appearance quality.
Functional addition
Flame retardant: In some fields that require fire resistance, such as electronic appliances, building materials, etc., flame retardant PS masterbatch is used. This type of masterbatch contains efficient flame retardants, which can give PS plastic products good flame retardant properties, reduce the risk of fire, and protect people’s lives and property safety.
Anti static: PS anti-static masterbatch can endow plastic products with anti-static properties, preventing the accumulation of dust and electric shock on their surfaces due to static electricity. The application of anti-static PS masterbatch can improve the quality and safety of products in fields such as electronic component packaging and medical and health products.
Antibacterial: Antibacterial PS masterbatch contains antibacterial agents that can inhibit the growth and reproduction of microorganisms such as bacteria and mold, giving plastic products antibacterial properties. In the fields of food packaging, daily necessities, medical devices, etc., the application of antibacterial PS masterbatch can improve the hygiene performance of products and ensure people’s health.