PA masterbatch is a granular product made from polyamide (PA) as a carrier, by adding various functional additives (such as flame retardants, antistatic agents, antibacterial agents, etc.) and other necessary additives, and through processes such as mixing, extrusion, and granulation. According to different functions, PA masterbatch can be divided into various types such as flame retardant masterbatch, anti-static masterbatch, antibacterial masterbatch, etc.
Types
PA masterbatch, also known as polyamide masterbatch, can be classified into the following types based on their functions and applications:
Enhanced PA masterbatch
Enhanced PA masterbatch is made by adding reinforcing materials such as glass fiber and carbon fiber to PA resin. The addition of glass fiber reinforced PA masterbatch can improve the mechanical strength, rigidity, and dimensional stability of the material, and is widely used in fields such as automotive components and electronic and electrical casings, capable of withstanding significant external forces and impacts. The reinforced PA masterbatch with added carbon fiber not only has high mechanical properties, but also endows the material with good electrical and thermal conductivity. It is commonly used in high-end sports equipment, aerospace and other fields that require extremely high material performance.
Flame retardant PA masterbatch
Prepared by adding flame retardants such as halogen, phosphorus, nitrogen, etc. to PA resin. Halogen flame retardant PA masterbatch has good flame retardant effect, but may produce toxic gases during combustion; Phosphorus based and nitrogen based flame retardant PA masterbatch are relatively environmentally friendly, producing less smoke and toxic gases during combustion. Flame retardant PA masterbatch is mainly used in fields with strict requirements for flame retardancy, such as electronic appliances, wires and cables, which can effectively prevent the occurrence and spread of fires.
Toughened PA masterbatch
Toughened PA masterbatch is generally modified by adding elastomers such as ethylene propylene rubber, nitrile rubber, etc. to PA resin. Toughened PA masterbatch can significantly improve the toughness and impact resistance of PA materials, enabling them to maintain good flexibility even in low temperature environments and be less prone to brittle cracking. Commonly used in the manufacturing of automotive interior parts, sports equipment, packaging materials, and other products that require good impact resistance.
Conductive PA masterbatch
It is usually made by adding conductive fillers such as carbon black, metal fibers, and carbon nanotubes to PA resin. Conductive PA masterbatch has good conductivity and can be used to manufacture anti-static components, electromagnetic shielding materials, etc. in electronic appliances. It can effectively prevent static electricity accumulation and electromagnetic interference, protect the normal operation of electronic equipment and the safety of users.
Weather resistant PA masterbatch
Weather resistant PA masterbatch is made by adding UV absorbers, antioxidants, and other additives to PA resin, which can improve the aging resistance of PA materials in outdoor environments and prevent problems such as fading, cracking, and mechanical performance degradation caused by long-term exposure to natural environments such as sunlight and rain. Weather resistant PA masterbatch is commonly used in outdoor building materials, automotive exterior parts, agricultural films, and other fields, which can extend the service life of products.
Antibacterial PA masterbatch
Prepared by adding antibacterial agents such as silver ion antibacterial agents, organic antibacterial agents, etc. to PA resin. Antibacterial PA masterbatch has the ability to inhibit the growth and reproduction of microorganisms such as bacteria and molds, and can be used to manufacture medical and health products, food packaging materials, kitchen utensils, and other products closely related to human health. It can effectively prevent the growth of bacteria and ensure the hygiene and safety of products.
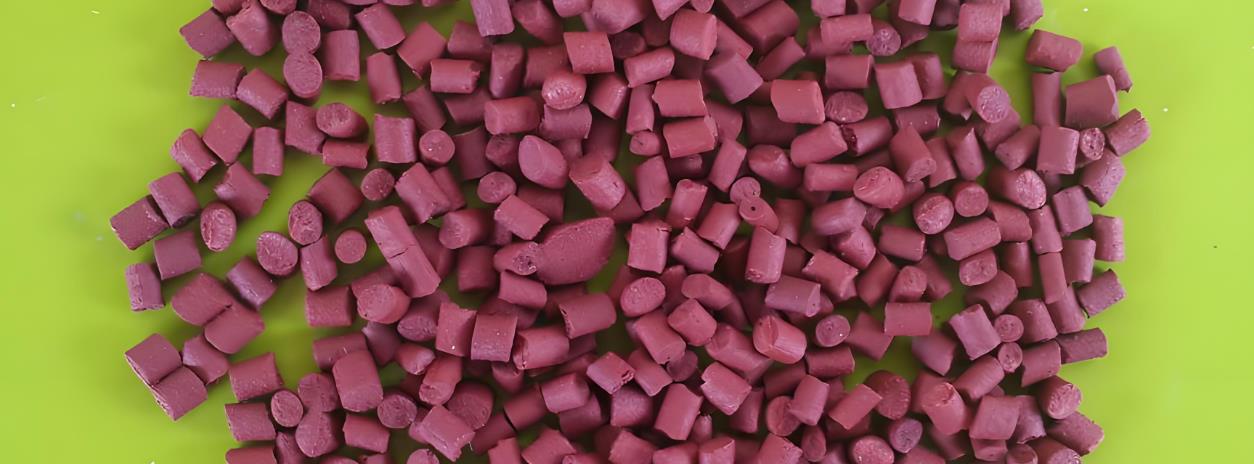
نسبة الصيغة
Different types of PA masterbatch have different functional and performance requirements, and their formula ratios also vary. The following are the approximate ratio ranges of some common types of PA masterbatch, which need to be adjusted according to specific product requirements in actual production:
Enhanced PA masterbatch
PA resin: 60% -80%
Fiberglass: 20% -40%
Other additives (such as coupling agents, lubricants, etc.): 0.5% -5%
Flame retardant PA masterbatch
PA resin: 70% -90%
Flame retardant: 10% -30%
Other additives (such as synergists, antioxidants, etc.): 0.5% -5%
Toughened PA masterbatch
PA resin: 70% -90%
Elastic body: 10% -30%
Other additives (such as compatibilizers, antioxidants, etc.): 0.5% -5%
Conductive PA masterbatch
PA resin: 80% -95%
Conductive fillers (such as carbon black, carbon nanotubes, etc.): 5% -20%
Other additives (such as dispersants, coupling agents, etc.): 0.5% -5%
Weather resistant PA masterbatch
PA resin: 90% -98%
UV absorber: 0.5% -3%
Antioxidant: 0.5% -2%
Other additives (such as light stabilizers, etc.): 0.5% -2%
Antibacterial PA masterbatch
PA resin: 90% -98%
Antibacterial agent: 0.5% -5%
Other additives (such as dispersants, etc.): 0.5% -2%
عملية الإنتاج
The production process of PA masterbatch is similar to that of PBT masterbatch mentioned above, usually including steps such as raw material preparation, ingredient mixing, extrusion granulation, drying treatment, and packaging and storage. However, the specific operations and parameters may vary depending on the type of masterbatch. The following is a detailed introduction to the production process of PA masterbatch:
Raw material preparation
PA resin selection: Select the appropriate PA resin based on the performance requirements of different types of PA masterbatch, such as PA6, PA66, etc. At the same time, attention should be paid to the viscosity, molecular weight distribution, and other indicators of the resin to ensure that it meets production requirements.
Additive preparation: For reinforced PA masterbatch, glass fiber, carbon fiber and other reinforcing materials should be prepared and surface treated to improve its adhesion with PA resin. For flame-retardant PA masterbatch, suitable flame retardants such as bromine based and phosphorus based flame retardants should be selected. Toughened PA masterbatch should be prepared with elastomers such as ethylene propylene rubber and nitrile rubber. Conductive PA masterbatch should be prepared with conductive fillers such as carbon black and carbon nanotubes, and ensure that their particle size and purity meet the requirements. Weather resistant PA masterbatch should be prepared with UV absorbers, antioxidants, etc. Antibacterial PA masterbatch should be prepared with corresponding antibacterial agents, such as silver ion antibacterial agents, organic antibacterial agents, etc.
خلط المكونات
Pre mixing: PA resin and additives are preliminarily mixed in a certain proportion in the feeding section of a high-speed mixer or twin-screw extruder, so that the additives are evenly dispersed in the PA resin. The pre mixing time is generally 5-10 minutes.
High speed mixing: further mixing is carried out using a high-speed mixer, and the material is mixed more evenly in a short period of time through a high-speed rotating stirring blade. The mixing speed is usually between 500-1000 revolutions per minute, and the mixing time is 10-20 minutes. For some difficult to disperse additives, such as carbon nanotubes, glass fibers, etc., it may be necessary to add dispersants or use special mixing processes to improve their dispersion effect.
Extrusion granulation
Melt extrusion: Add the mixed material into a twin-screw extruder and heat it to the melting temperature of PA resin. The melting temperature of PA6 is generally between 220-230 ℃, while the melting temperature of PA66 is between 250-260 ℃. The rotation of the screw causes the material to be subjected to shear and pressure forces inside the barrel, further mixing and plasticizing evenly. The screw speed is adjusted according to the material characteristics and production efficiency, generally between 100-600 revolutions per minute. For reinforced PA masterbatch, attention should be paid to the addition and dispersion of glass fibers or carbon fibers during the extrusion process to avoid fiber aggregation or uneven distribution. For conductive PA masterbatch, it is necessary to ensure that the conductive filler is evenly dispersed in the PA resin to obtain stable conductivity.
Filtration: During the extrusion process, impurities and unmelted particles in the material are removed through a filter or filtering device. The number of filter mesh is selected according to product quality requirements, generally between 80-200 mesh.
Granulation: The filtered molten material is extruded from the extruder die to form continuous strips or filaments, and then cooled and shaped by air or water cooling. After cooling, the strip-shaped or filamentous material is then cut into particles of the desired size by a granulator, namely PA masterbatch. The speed of the granulator and the choice of cutting tools will affect the particle size and shape of the masterbatch, which is generally between 2-5 millimeters in size.
Drying process
PA masterbatch is prone to absorbing moisture during the production process, and in order to ensure its performance and quality, it needs to be dried. The drying temperature is generally between 80-120 ℃, and the drying time is 2-6 hours to reduce the moisture content of the masterbatch to below 0.1%. For some moisture sensitive PA masterbatch, such as PA66 masterbatch, drying requirements may be more stringent.
التعبئة والتغليف والتخزين
Packaging: Pack the dried PA masterbatch in plastic or paper bags, and then pack it in a sealed outer packaging box to prevent the masterbatch from absorbing moisture and being contaminated during storage and transportation. The packaging specifications are determined according to customer needs, commonly including 25kg/bag or ton bag packaging.
Storage: PA masterbatch should be stored in a dry, ventilated environment, away from direct sunlight and moisture. It is best to control the storage temperature between 10-30 ℃ to prevent changes in the properties of the masterbatch. For some special types of PA masterbatch, such as antibacterial PA masterbatch, attention should be paid to the hygiene of the storage environment to prevent the antibacterial agent from becoming ineffective.
معدات الإنتاج
The production equipment for PA masterbatch mainly includes batching equipment, mixing equipment, extrusion granulation equipment, drying equipment, and packaging equipment. The following is a specific introduction:
1. Ingredient equipment
Electronic scale: used for accurately weighing various raw materials such as PA resin and additives. According to the production scale and accuracy requirements, electronic scales with different ranges and accuracies can be selected, such as electronic scales with a range of 0.1-500 kilograms and an accuracy of ± 0.1 grams, to ensure the accuracy of ingredient ratios.
Automatic batching system: composed of storage tanks, measuring devices, conveying devices, and control systems, it can achieve automatic batching and conveying of various raw materials, improve batching efficiency and accuracy, and is suitable for large-scale production.
2. المعدات الهجينة
High speed mixer: using high-speed rotating mixing blades to achieve uniform mixing of materials in a short period of time. It has the advantages of fast mixing speed and good mixing effect, and is commonly used in the pre mixing of PA masterbatch production and the preliminary mixing of additives and resins.
Double planetary mixer: The mixing blade rotates while revolving, causing strong shear and mixing effects on the material during the mixing process. It can achieve uniform mixing of high viscosity materials and difficult to disperse additives, and is suitable for the production of PA masterbatch with high mixing requirements.
3. Extrusion granulation equipment
Twin screw extruder: It is one of the key equipment for the production of PA masterbatch. Two interlocking screws rotate inside the barrel, subjecting the material to shear, compression, and mixing during transportation, achieving melting, plasticization, and uniform mixing of the material. The twin-screw extruder has the advantages of large conveying capacity, good mixing effect, short and uniform material residence time, and can be selected according to different PA masterbatch formulations and production process requirements, with different aspect ratios, screw structures, and driving powers.
Extruder auxiliary equipment: including die head, cooling device, and pellet cutter, etc. The die head is used to extrude molten material into the desired shape, such as strip or filament; Cooling devices generally use air or water cooling methods to quickly cool and shape extruded materials; The granulator cuts the cooled material into particles of a specified size. Depending on the cutting method, it can be divided into hot cutting granulator and cold cutting granulator. Hot cutting granulator is suitable for materials with high viscosity, while cold cutting granulator is suitable for various materials with good cutting quality.
4. Drying equipment
Hot air circulating oven: Drying PA masterbatch through circulating hot air has the advantages of uniform drying and accurate temperature control. There are multiple shelves inside the oven, which can hold trays containing masterbatch. Hot air circulates in the oven to remove moisture from the masterbatch. Suitable for small and medium-sized production.
Boiling dryer: uses hot air to make materials boil in the drying chamber, achieving rapid drying of materials. It has the advantages of fast drying speed, good drying effect, and less clumping of materials, and is suitable for drying PA masterbatch in large-scale production.
5. Packaging equipment
Automatic packaging machine: capable of automatically measuring, filling, and sealing PA masterbatch for packaging processes. According to packaging specifications and material characteristics, different types of automatic packaging machines can be selected, such as granule packaging machines, ton bag packaging machines, etc. The granule packaging machine is suitable for small packaging specifications, such as 25kg/bag packaging; The ton bag packaging machine is used for large packaging specifications, such as packaging of 1 ton per bag.
Sealing machine: used to seal the packaged PA masterbatch bags, ensuring the sealing of the packaging bags and preventing moisture and contamination of the masterbatch during storage and transportation. Common sealing machines include hot melt sealing machines, pulse sealing machines, etc. The appropriate sealing machine can be selected according to the material and thickness of the packaging bag.
In addition, some auxiliary equipment may be used in the production process of PA masterbatch, such as raw material conveying equipment, material storage tanks, dehumidifiers, etc., to ensure the smooth progress of the production process and stable product quality.
PA masterbatch extruder
Kerke’s masterbatch extruder can be used to produce PA masterbatch. Our PA masterbatch extruder has multiple models to choose from, which can meet different production requirements.
-
آلة البثق اللولبية المزدوجة للمختبر
متى ستحتاج إلى آلة بثق ثنائية اللولب للمختبر؟ إذا كنت ترغب في إجراء تجارب واختبارات...
-
آلة البثق ذات اللولب المزدوج المتوازي
تم تصميم آلة البثق ذات المسمار المزدوج ذات الدوران المتوازي لدينا لتصنيع المركبات والدفعات الرئيسية مع سعة إنتاج تتراوح من...
-
طارد ثلاثي (3 براغي)
آلة البثق ثلاثية البراغي هي تقنية جديدة ذات مزايا عديدة. تُستخدم آلة البثق ثلاثية البراغي بشكل رئيسي...
-
نظام البثق ثنائي المرحلة
تم تصميم نظام بثق الأم والطفل للمواد الخاصة التي لا يمكن معالجتها على مرحلة واحدة من البثق، المرحلة الأولى...
-
خط تصنيع العجنات في بانبوري
تم تصميم آلة العجن والبثق الخاصة بنا لصنع تطبيقات خاصة بسعة إنتاج تتراوح من 30 كجم / ساعة إلى 1000 كجم / ساعة.
-
نظام القطع / نظام التكوير
تحتاج المواد المختلفة إلى نظام قطع مختلف، توفر شركة Kerke جميع أنواع أنظمة القطع، فيما يلي شرح لها…
Related requirements
The production of PA masterbatch (polyamide masterbatch) has high requirements for the extruder in plasticization, mixing, temperature control, etc., as follows:
Plasticizing capacity
Screw design: PA resin has a high melting point and requires the screw to provide sufficient shear and friction forces to achieve plasticization. Typically, a mutation type screw is used, which has a shorter compression section and can subject PA resin to strong shear and compression in a shorter period of time, rapidly heating and melting. Meanwhile, the aspect ratio of the screw is generally between 25-32 to ensure sufficient length for the PA resin to fully plasticize.
Drive power: Due to the high energy consumption required for PA resin melting, the extruder needs to be equipped with a high-power drive motor to ensure stable rotation of the screw during production, overcome material resistance, and achieve good plasticizing effect. Generally speaking, for extruders producing PA masterbatch, their driving power needs to be reasonably configured according to the specifications and production capacity of the extruder. Typically, extruders with an extrusion capacity of 100-500 kilograms per hour have a driving power of around 30-100 kilowatts.
Mixed dispersion performance
Efficient mixing element: In order to evenly mix various additives (such as toughening agents, flame retardants, colorants, etc.) in PA masterbatch with PA resin, efficient mixing elements should be installed on the extruder screw. For example, using pin screws, barrier screws, etc., these screw structures can increase the turbulence level of materials and improve the mixing effect. At the same time, multiple kneading blocks can be set on the screw, and by combining kneading blocks at different angles and arrangements, multiple shearing and mixing of the material can be achieved, so that the additive can be uniformly dispersed in the PA resin.
Strengthening dispersion measures: For some difficult to disperse additives, such as nanoscale fillers or functional additives, extruders can be equipped with specialized dispersion devices, such as static mixers. The static mixer is installed inside the barrel or in front of the head of the extruder, which can further enhance the mixing and dispersion effect during the material flow process, ensuring that the additive forms a stable and uniform system in the PA masterbatch.
Temperature control accuracy
Accurate temperature control system: During the production process of PA masterbatch, temperature has a significant impact on product quality. The extruder needs to be equipped with a high-precision temperature control system, generally using electric heating or thermal oil heating methods, and monitoring the temperature of each heating section in real time through temperature sensors such as thermocouples or thermal resistors. The temperature control accuracy should be within ± 1 ℃ to ensure that the PA resin is in a suitable temperature range during melting, mixing, and extrusion processes, and to avoid product performance degradation caused by temperature fluctuations, such as molecular weight reduction, color changes, and other issues.
Cooling system: In addition to heating control, the cooling system is also crucial. After PA masterbatch extrusion, it is necessary to quickly reduce the temperature through a cooling device to prevent masterbatch adhesion and deformation. Extruders are usually equipped with air or water cooling systems to cool the head and extruded masterbatch. The air-cooled system uses a fan to force air flow to remove heat, while the water-cooled system uses circulating water for cooling. The cooling rate can be adjusted according to production speed and masterbatch specifications.
Pressure stability
Stable extrusion pressure: Stable extrusion pressure is a key factor in ensuring the uniformity of PA masterbatch size and appearance quality. The hydraulic system or mechanical transmission system of the extruder should be able to provide stable pressure output, with pressure fluctuations generally controlled within ± 3%. Stable pressure can maintain a uniform flow rate of the material during extrusion, thereby producing PA masterbatch with high precision in diameter and length.
Pressure regulating device: In order to adapt to different production processes and product requirements, extruders should have flexible pressure regulating devices. Operators can accurately adjust the extrusion pressure by adjusting the back pressure of the screw, changing the pressure parameters of the hydraulic system, or adjusting the throttle device of the machine head. For example, in the production of PA masterbatch with different specifications or formulas, by adjusting the extrusion pressure reasonably, the flowability and molding effect of the material can be optimized, and the quality and performance of the product can be improved.
Material conveying stability
Accurate feeding: The production of PA masterbatch requires precise control of the amount of various materials added, so the feeding device of the extruder should use high-precision feeding equipment. Common weight loss feeders can accurately deliver PA resin, additives, and other materials to the extruder according to the set amount of material added. At the same time, the feeder should have good sealing and stability to prevent material leakage and uneven feeding, ensuring accurate proportioning of materials during the production process.
Screw conveying accuracy: The machining accuracy and assembly quality of screws have a significant impact on the stability of material conveying. The pitch and diameter tolerances of the screw should be controlled within a small range, generally with a pitch tolerance of no more than ± 0.05 millimeters and a diameter tolerance of no more than ± 0.03 millimeters, to ensure that the material can be stably conveyed forward in the screw groove and avoid material retention or fluctuation. In addition, the gap between the screw and the barrel should be uniform and consistent. If the gap is too large, it can easily cause material reflux and affect conveying efficiency; If the gap is too small, it may cause excessive material shearing and screw wear.
Corrosion resistance and wear resistance
Corrosion resistant materials: PA resin may have some corrosive additives added during processing, such as certain antioxidants and lubricants. Therefore, components such as the barrel and screw of the extruder that come into contact with the material need to be made of corrosion-resistant materials. The barrel is usually protected by lining with stainless steel or spraying a corrosion-resistant coating, while the screw can be made of alloy steel with good corrosion resistance and surface treated, such as hard chromium plating or electroless nickel plating, to improve its corrosion resistance and extend the service life of the equipment.
Wear resistant design: Due to the hardness of PA resin, it will cause significant wear on the screw and barrel during the extrusion process. In order to improve the wear resistance of the equipment, the surface of the screw and barrel should have high hardness and wear resistance. In addition to selecting suitable materials, special heat treatments such as quenching and tempering can also be applied to the screw and barrel to improve their surface hardness. In addition, wear-resistant liners can be installed in the feeding section and easily worn parts of the barrel for regular replacement and to reduce equipment maintenance costs.
Automated Control and Monitoring
Advanced control system: Modern PA masterbatch production extruders are typically equipped with advanced automation control systems, such as PLC (Programmable Logic Controller) or DCS (Distributed Control System). These systems can achieve real-time monitoring and precise control of parameters such as temperature, pressure, screw speed, and material flow rate of the extruder. Operators can easily set and adjust production parameters through the human-machine interface (HMI), monitor and manage the production process, and improve production efficiency and product quality stability.
Fault diagnosis and warning: The automation control system should also have fault diagnosis and warning functions. The system can monitor the operating status of equipment in real time. When abnormal situations occur, such as high temperature, abnormal pressure, motor overload, etc., it can promptly issue alarm signals and automatically take corresponding protective measures, such as stopping the machine or reducing production speed. At the same time, the system can also record fault information to help maintenance personnel quickly locate and troubleshoot faults, reduce equipment downtime, and improve production continuity and reliability.
طلب
PA masterbatch, also known as polyamide masterbatch, has good wear resistance, chemical resistance, high mechanical strength, and excellent processing performance. It is widely used in various fields such as textiles, injection molding, and films. The following is a specific introduction:
Textile industry
Improving fiber performance: In synthetic fiber production, adding PA masterbatch can improve the dyeing performance, anti-static performance, and softness of fibers. For example, by adding PA masterbatch containing special dye receiving groups, fibers can be made easier to color, with brighter and more uniform colors, while reducing energy consumption and environmental pollution during the dyeing process. Adding anti-static PA masterbatch can effectively prevent fibers from generating static electricity during processing and use, improving the processability and wearing comfort of fibers.
Manufacturing functional fibers: PA masterbatch can be used to produce fibers with special functions, such as antibacterial fibers, moisture wicking fibers, etc. By blending PA masterbatch containing antibacterial agents with conventional fiber materials, fibers with antibacterial properties can be produced, which can be used in the production of medical and health products, sportswear, and home textiles. This can effectively inhibit bacterial growth and maintain the cleanliness and hygiene of the products. The fibers produced by adding PA masterbatch with moisture wicking function can quickly absorb and dissipate sweat excreted by the human body, keeping the skin dry and improving the comfort of wearing. They are commonly used in the manufacturing of sportswear and outdoor equipment.
Injection molding industry
Enhancing Plastic Performance: PA masterbatch is often used to enhance the performance of plastics. By adding reinforced PA masterbatch such as glass fiber and carbon fiber, the mechanical strength, rigidity, and heat resistance of plastic products can be significantly improved. In the manufacturing of automotive components, such as engine hoods, seat frames, door interior panels, etc., the use of reinforced PA masterbatch in plastic parts can reduce weight while maintaining good structural strength and stability, meeting the automotive industry’s requirements for high-performance and lightweight components. In the field of electronic appliances, it is used to manufacture components such as casings and brackets, which can improve the durability and reliability of products, while also better adapting to high temperature environments.
Improving processing performance: During injection molding, PA masterbatch can improve the flowability and formability of plastics. Some PA masterbatch containing lubricants or flow modifiers can reduce the viscosity of plastic melt, making it easier to flow in the mold, thereby improving the efficiency and product quality of injection molding, and reducing product defects such as short shots and bubbles. This is particularly important for manufacturing plastic products with complex shapes and high-precision requirements, such as precision electronic component casings, optical lenses, etc.
Thin film industry
Improving film performance: PA masterbatch can be used to produce high-performance packaging films. Adding PA masterbatch to ordinary plastic film can improve the barrier performance of the film, making it more effective in blocking oxygen, water vapor, etc., thereby extending the shelf life of packaged products. For example, in food packaging, the use of composite films containing PA masterbatch can effectively prevent food oxidation, deterioration, and moisture, maintaining the freshness and quality of the food. At the same time, PA masterbatch can also improve the mechanical strength and toughness of the film, making it more durable, less prone to breakage, and easier to package and transport.
Manufacturing special films: PA masterbatch can be used to manufacture films with special functions, such as heat shrinkable films, conductive films, etc. The film made of heat shrinkable PA masterbatch can produce uniform shrinkage when heated, and can be used for product packaging to fix and protect the product. It is widely used in packaging industries such as beverages and daily necessities. Conductive PA masterbatch can be used to manufacture thin films with conductive properties for electromagnetic shielding and anti-static packaging of electronic devices. It can effectively prevent electromagnetic interference to electronic devices and protect sensitive electronic components from electrostatic damage.